Teil 3 der Best-Practice-Regeln für eine leistungsfähige Disposition
In den ersten beiden Teilen des Best-Practice-Artikels haben Sie erfahren, mit welchen elf Bausteinen und Regeln Sie Lieferbereitschaft und Sicherheitsbestände festlegen können. Sie wissen nun, dass Sie Sicherheitsbestände aufbauen müssen, bevor Sie sie brauchen und daher regelmäßig ermitteln müssen. Die Architektur Ihrer Wertschöpfungskette bestimmt nun Ihren Grundbedarf und aus der Prozessstabilität können Sie Ihren Sicherheitsbestand ableiten.Nun geht es darum, Ihre Disposition fit genug zum Abheben in neue Welten zu machen! Sie lesen im Folgenden, wann Pull- und wann Push-Steuerung sinnvoll ist, warum das Bauchgefühl der Disponenten leider unzuverlässig ist und Regelwerke für eine leistungsfähige Disposition unerlässlich sind. Die letzten Schritte in eine neue Dispositionswelt:
Klassische Push-Steuerungen, wie plangesteuerte Disposition bzw. MRP II sind heute nicht mehr „cool“, sondern ziemlich „out“. Alles strebt nach Lean Production und „Pull-Steuerung“: Meldebestandssteuerung und vor allem Kanban (Pendelkarten) sind „in“. Beides sind sehr alte Verfahren, die bereits vor dem Zeitalter der Computer im Einsatz waren, Pendelkarten zumindest bereits im Mittelalter. Viele Gründe sprechen für die Renaissance der Pull-Steuerung, dabei wird allerdings gerne übersehen, dass die Push-Steuerung einmal entwickelt worden ist, um bestimmte Nachteile der Meldebestandsteuerung zu überwinden und dass es eine reine Pull-Steuerung praktisch gar nicht gibt.
Pull-Steuerung in der klassischen Form eignet sich primär für gleichmäßige Durchschnittsbedarfe wiederkehrender Artikel mit einer Schwankungs-Varianz bis 1. Man kann Pull-Mechanismen so deformieren, dass sie auch bei Einzel- und Kleinserienfertigung funktionieren, aber dann bringen sie keinen Vorteil mehr gegenüber der Push-Steuerung.Meldebestandsteuerung vor 100 Jahren bedeutete, dass man im Lager bei der Bestandshöhe, bei der man neues Material nachbestellen musste, eine Markierung anbrachte. Meldebestandssteuerung heute bedeutet, dass die Bestandshöhe im Lager über die buchmäßigen Bestände verfolgt wird und die Nachbestellung beim Unterschreiten des Buchbestandes ausgelöst wird.
Um Buchungsaufwand zu sparen, wird heute gerne retrograd gebucht. Material wird dabei von einem Lager erst dann abgebucht, wenn der das Material benötigende Fertigungsauftrag abgearbeitet ist und zurückgemeldet wird. Erst mit dem Zubuchen des neuen Materials im Lager wird also das alte Material abgebucht. Die Buchbestände hängen dadurch immer ein Stück hinter den physischen Beständen hinterher: Keine glückliche Ausgangssituation für eine elektronische Meldebestandssteuerung. Retrograde Buchung und Meldebestandssteuerung passen nicht gut zusammen.
Auch eine Kanban-Steuerung stellt nichts anderes dar als eine Meldebestandssteuerung, allerdings eine, die sich am physischen Bestand orientiert. Im Gegensatz zur Meldebestandssteuerung beobachtet man im Kanban-System die anwachsenden leeren Behälter und nicht den abnehmenden Bestand im Lager, um den Nachschub auszulösen. Ein manuelles Kanban-System hat mit retrograder Abbuchung der Buchbestände zum Beispiel keine Probleme. Probleme im Kanban-System treten bei vielen Unternehmen dann auf, wenn es um das Berechnen oder Nachberechnen der erforderlichen Karten- oder Behälterzahl im Regelkreis geht.
Während Meldebestände regelmäßig angepasst werden, lässt man Kanban-Bestände gerne möglichst lange konstant. Und während zumindest qualifizierte Disponenten wissen, dass sich ein Meldebestand aus Grundbedarf und Sicherheitsbestand zusammensetzt, wird der Sicherheitsbestand im Kanban-Regelkreis gerne vergessen oder „nach Gefühl“ gesetzt. Dass bei der Auslegung eines Kanban-Regelkreises der erforderliche Lieferbereitschaftsgrad in die Berechnung einfließen muss, gehört noch nicht einmal mehr zum Fachwissen vieler Berater.Klassische mehrstufige Meldebestands- und Kanban-Steuerung kommen mit saisonaler Nachfrage und Trends nicht zurecht. In solchen Fällen genügt es nicht, die Regelkreise und Meldebestände regelmäßig nachzudimensionieren.
Man benötigt vielmehr spezielle Mechanismen, wie Parabellum-Steuerung oder Meldebestandssteuerung mit MRP, um sich auf tieferen Dispositionsstufen rechtzeitig auf die anwachsenden oder abnehmenden Bedarfe einzustellen und so das Anwachsen oder Abfallen der Bedarfe der übergeordneten Dispositionsstufe bedienen zu können. Versteht man nicht damit umzugehen, weil Kenntnisse oder die Funktionalitäten im ERP-System fehlen, dann greift man in solchen Fällen besser auf plangesteuerte Disposition zurück.Mehrere Artikel, die bei demselben Lieferanten bestellt oder mit demselben Transportträger beschafft werden, müssen sinnvollerweise im Verbund disponiert werden, um z. B. volle Container zu erreichen, Mindestbestellwerte zu überschreiten oder Bestellbudgets einzuhalten.Die Beispiele ließen sich noch beliebig fortsetzen, doch dürfte bereits klar geworden sein:
Best-Practice-Baustein 12: Eine leistungsfähige Disposition setzt ein breites Repertoire an Dispositionsverfahren in Abhängigkeit verschiedener Randbedingungen und Artikeleigenschaften ein und schert niemals alle Artikel dispositiv über einen Kamm.
In der differenzierten Anwendung unterschiedlicher Dispositionsverfahren für unterschiedliche Artikel zeigt sich jedoch nur die Spitze des Eisberges einer leistungsfähigen und prozessstabilen Disposition, denn zwischen Artikeln und all ihren Stammdaten und Parametern besteht kein statischer, einmal einzustellender Zusammenhang. Vielmehr gilt:
Grundprinzip 13: Die Planungs-, Prognose- und Dispositionsverfahren und Stammdaten eines Artikels müssen laufend an die sich verändernden Erfordernisse angepasst werden.
Auch wenn es in der Praxis selten geschieht: Es herrscht Konsens darüber, dass zentrale logistische Stammdaten, z. B. Losgrößen oder Wiederbeschaffungszeiten, regelmäßig an sich verändernde Situationen angepasst werden müssen. Dass das laufende Nachregeln auch für die sonstigen logistischen Parameter jedes Artikels gilt, ist schon deutlich weniger bekannt. Ein Artikel, der früher mit starken Nachfrageschwankungen zu kämpfen hatte, läuft heute möglicherweise recht gleichmäßig.
Während früher wenige Kunden diesen Artikel oder das Endprodukt, in den dieser Artikel eingeht, nachfragten, wird er heute vielleicht von einer großen Kundenzahl geordert. Bei solchen Veränderungen muss für den Artikel möglicherweise ein anderes Dispositionsverfahren eingestellt werden. Das laufende Nachführen von Dispositionsverfahren, -parametern und Stammdaten stellt keine Ausnahme, sondern ein regelmäßiges Erfordernis dar, das in der Praxis häufig ignoriert wird.
Welche Regeln auf welche Artikel wie angewandt werden sollen, hängt dabei nicht von den logistisch relevanten Eigenschaften der Artikel ab. Notwendige, in jedem Fall zu beachtende, aber noch lange nicht hinreichende Kriterien sind die Bedeutung eines Artikels für den Umsatz (ABC), die Schwankungen in der Nachfrage nach einem Artikel (XYZ), die Zahl der Bedarfsverursacher, die hinter einem Artikel stehen (STU) oder der Lebenszyklus, in dem sich ein Artikel befindet (ELA).
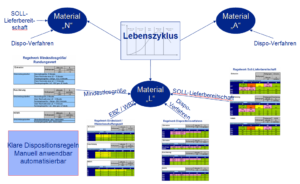
Die Erkenntnis, dass Artikel zu pflegen sind, führt in vielen Unternehmen nur erstaunlich langsam zu entsprechenden Aktivitäten. Die Anweisung an die Disponenten lautet häufig, die Stammdaten ihrer Artikel regelmäßiger zu überprüfen und anzupassen. Jeder mache also, was er für richtig hält – der eine dies, der andere jenes! Eine eigenartige Großzügigkeit, die dieselben Unternehmen ihrer Produktion nicht zubilligen. Für die Fertigungsprozesse ist klar definiert, mit welchen technischen Verfahren, welchen Prozessparametern und in welchen Arbeitsschritten die Teile zu bearbeiten sind. Alles andere würde auch kaum zu reproduzierbaren, verlässlichen Fertigungsprozessen führen. Um zu einer leistungsfähigen Best-Practice-Disposition zu gelangen, gilt selbstverständlich:
Best-Practice-Baustein 13: Unter welchen Randbedingungen welche Parameter, Planungs-, Prognose- und Dispositionsverfahren wie gesetzt werden, muss in klaren Geschäftsregeln einheitlich festgelegt und nicht individuellen Auffassungen der einzelnen Disponenten überlassen werden. Die Parametereinstellungen werden dabei in Abhängigkeit von logistisch relevanten Artikeleigenschaften definiert.
Wie gelangen Sie zu einheitlichen Geschäftsregeln? Bitte nicht, indem Sie die gesamte Disposition zusammentrommeln und gemeinsam über die richtigen Einstellungsregelwerke diskutieren! Hier gilt es, ein weiteres Grundprinzip zu beachten:
Grundprinzip 14: Das Bauchgefühl der Disponenten ist einer der größten Bestandstreiber im Unternehmen.
Unter dem Fachbegriff der „Behavioral Economics“ finden sich in den Wirtschaftswissenschaften zahlreiche Abhandlungen über den Einfluss von Bauchgefühl und vermeintlicher Erfahrung auf betriebswirtschaftliche Entscheidungen. Es würde zu weit führen, Details hier zu diskutieren. Das Fazit der Untersuchungen ist aber auf einen einfachen Nenner zu bringen: Weder professionelle noch private Anleger schlagen den Markt. Erfolge durch „gute“, besser formuliert „glückliche“ Entscheidungen an einer Stelle werden an anderer Stelle wieder zunichte gemacht.
Die Ursachen hierfür sind bei der Disposition dieselben wie bei Aktien und anderen Wertpapieren und führen dazu, dass die Disponenten ihre eigenen Erfahrungen und ihr Bauchgefühl überschätzen. Dispositive Entscheidungen und damit dispositive Regelwerke wirken darüber hinaus weiter in das Geschehen der gesamten Wertschöpfungskette hinein, als es ein Mensch überblicken kann, sei er noch so erfahren und intelligent.
Von Hand eingestellte oder auf der vermeintlichen Erfahrung von Disponenten oder Beratern alleine aufgestellte Regelwerke mögen zwar zu reproduzierbaren Dispositionsergebnissen führen, zementieren aber auch die „Underperformance“ der gesamten Wertschöpfungskette. Schlechte Disposition in klare Regeln gegossen bleibt immer noch schlechte Disposition. Für Top-Unternehmen gilt deshalb:
Best-Practice-Baustein 14: Die richtigen dispositiven Geschäftsregeln für eine High-End-Disposition sind mittels Simulation auf maximale logistische Performance und minimale Kosten der Wertschöpfungskette optimiert und nicht nach Erfahrung und Bauchgefühl eingestellt.
Wenn Sie klare Regeln definiert und mittels eines differenzierten Simulation die Regelwerke so eingestellt haben, dass Sie die geforderte logistische Positionierung mit den geringstmöglichen Kosten erreichen, dann haben Sie einen großen Sprung nach vorne unternommen. Machen Sie jetzt nicht den Fehler, die Einstellungen der Artikel entsprechend dem Regelwerk von Hand regelmäßig nachpflegen zu wollen, denn:
Grundprinzip 15: Datenpflege ist zeitlich zu aufwändig, um manuell durchgeführt werden zu können.
Um die Datenqualität à jour zu halten, müssen die Parametereinstellungen entsprechend der Regelwerke monatlich gepflegt werden. Dies kann aus zwei Gründen nicht von Hand erfolgen:
Erstens wäre bereits das reine artikelspezifische monatliche Eintragen veränderter Stammdaten entsprechend den Regelwerken zu arbeits- und zeitaufwändig und somit manuell nicht zu bewältigen. Zweiter Grund ist die Klassifizierung von Artikeln: Regelwerke basieren zu großen Teilen auf Klassifizierungseigenschaften von Artikeln. Gehört ein Artikel beispielsweise der Klasse der anlaufenden Artikel an, wird er anders gehandhabt als ein Artikel, der zur Klasse der auslaufenden Artikel gehört. Der Klassifizierung eines Artikels liegen teilweise umfangreiche Berechnungen zugrunde. Das wird schon an den „Standardklassifizierungen „ABC“ und „XYZ“ klar. Diese Berechnungen müssen mit jedem Pflegelauf aktualisiert werden, was nicht von Hand geschehen kann.
Software-Systeme, die solche Regelwerke verarbeiten können, schlagen dem Anwender die erforderlichen Einstellungsänderungen je Artikel vor. Die Vorschläge können vom Anwender noch überarbeitet und müssen von ihm für den Upload in das ERP-System freigegeben werden. Nur über diesen halbautomatischen Weg kann sichergestellt werden, dass die faktisch erforderliche „Massen“-Datenpflege auch tatsächlich regelmäßig durchgeführt wird. Deshalb gilt:
Best-Practice-Baustein 15: Regelwerke müssen monatlich auf das gesamte Artikelspektrum halbautomatisch angewendet werden. Dazu müssen die Artikel vorbereitend entsprechend ihrer logistischen Eigenschaften nach- bzw. umklassifiziert werden.
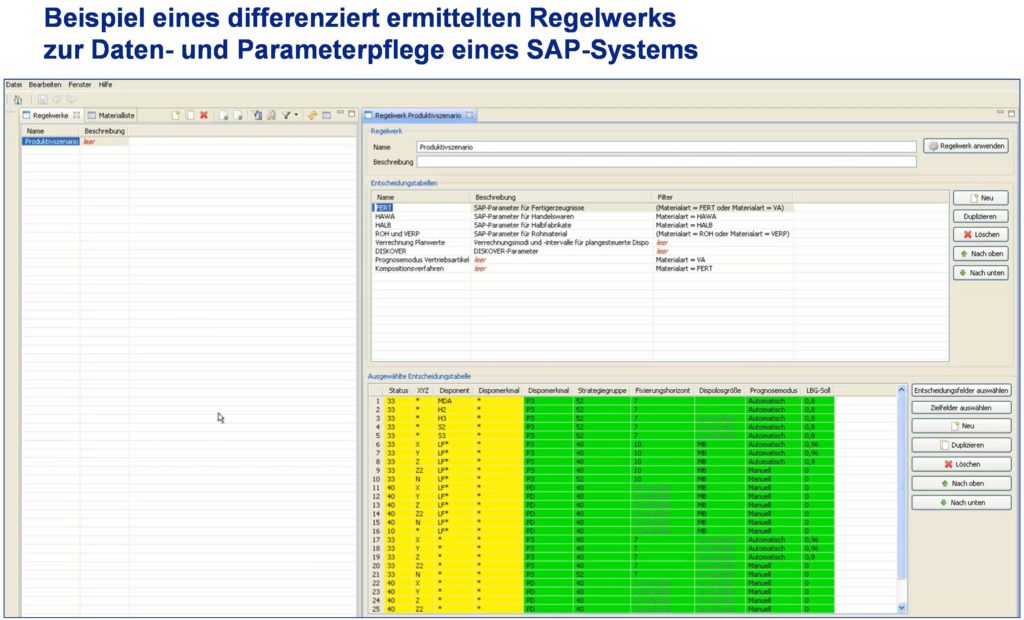
So langsam haben Sie sich durch das Unterholz gekämpft und den Wald der Disposition wieder gepflegt. Zuverlässige Dispositionsparameter waren hierzu ein wesentlicher Schritt, aber noch gilt:
Grundprinzip 16: Ein ERP-System mit den Informationen von gestern kann keine Entscheidungen für morgen treffen.
Leider genügt es nicht, artikelspezifisch richtige Logistikgrößen festgelegt und Dispositionsverfahren abgestimmt zu haben. Wenn dem ERP-System die Informationen über den aktuellen Zustand in Produktion, Beschaffung und Auslieferung fehlt, wird es Ihnen wenig helfen können.
Wie soll das ERP-System richtige Bestandsentscheidungen treffen, wenn die Bestandsinformationen im System falsch sind oder viel zu spät vorliegen? Wie soll es Fertigungsaufträge richtig terminieren, wenn das erforderliche Eingangsmaterial vom Lieferanten nicht rechtzeitig geliefert wird? Wenn die Beschaffung dieses wichtige und kritische Datum nicht regelmäßig abprüft und Terminänderungen im ERP-System zumindest dann einpflegt, wenn sie ihr bekannt werden?
Bei Fertigungsaufträgen mit längeren Durchlaufzeiten durch die Produktion muss ggf. die Fertigstellung einzelner Arbeitsvorgänge zurückgemeldet werden, damit im ERP-System ein ausreichend aktueller Überblick über die Kapazitätsbelastungen auf den einzelnen Fertigungsanlagen vorliegt.
Wie gravierend sich falsche Lieferzeiten auf die Unterstützungseffizienz des ERP-Systems auswirken, haben wir an anderer Stelle schon diskutiert.Diese wenigen Beispiele belegen bereits: Das Pflegen der Dispositionsparameter alleine genügt nicht, um ein brauchbares ERP-System aufzubauen. So wie ein Wagen ohne Benzin nutzlos ist, ist ein ERP-System ohne Datensprit in Form aktueller Bewegungsdaten nutzlos. Zu den Bewegungsdaten gehören hierbei nicht nur Bestandswerte, sondern auch Liefer-, Wiederbeschaffungs- und Durchlaufzeiten, Fertigungsfortschritte und Lieferstatus.
Ein Unternehmen, in dessen ERP-System alle Daten aktuell und akkurat gepflegt sind, steht kurz vor der Pleite – zu aufwändig und kostenintensiv ist es, alle Werte auf dem Laufenden zu halten. Selbst in Einwohnermeldeämtern, die mit großen Abteilungen „Bürger-Datamanagement“ betreiben, liegt die Datenqualität unter 100 %! Die Kunst des Datenqualitäts-Managements im ERP-System besteht darin, zu wissen, unter welchen Randbedingungen an welcher Stelle in den Planungsschritten welche Genauigkeit erforderlich ist und wie stark sich Abweichungen in Aktualität, Qualität und Vollständigkeit der Daten auf die Planungsqualität des ERP-Systems auswirken.Als wesentlichen Best-Practice-Baustein müssen wir deshalb festhalten:
Best-Practice-Baustein 16: Zustandsinformationen über Beschaffungs-, Fertigungsverläufe und Kapazitätsbelastungen müssen ausreichend zeitnah, vollständig und fehlerfrei in das ERP-System zurückgemeldet werden, damit das System verlässliche Entscheidungen treffen kann. Regelmäßige Audits müssen prüfen, ob Rückmeldungen ausreichend aktuell, vollständig und fehlerfrei erfolgen.
Ein gut gepflegtes und richtig eingestelltes ERP-System legt das Fundament, um auf dem Best-Practice-Weg weiter voranzuschreiten und an der Beseitigung einer weiteren Unzulänglichkeit in vielen Unternehmen zu arbeiten:
Grundprinzip 17: In vielen Unternehmen werden ERP-System nur als teure Schreibmaschinen genutzt.
Stellen Sie sich einmal vor, in der Produktion macht jeder was er will. Arbeitspläne gibt es zwar, aber daran muss man sich ja nicht unbedingt halten, wenn man es besser weiß. Statt nach klaren Vorgaben und Qualitätskriterien zu arbeiten, macht ein Jeder es so, wie er es für richtig hält und für qualitativ ausreichend. Sie meinen, das gibt es in modernen Unternehmen nicht? In der Produktion sicher nicht, wohl aber bei der Handhabung der Planungs- und Dispositionsprozesse. Schlimmer noch, der Anteil von Unternehmen, die auf diese Weise arbeiten, nimmt eher noch zu!
Wesentlichen Anteil daran hat paradoxerweise die verbesserte Benutzerfreundlichkeit und Transparenz vieler ERP-Systeme sowie die Entwicklung sogenannter Cockpits, die alle für eine Anwenderentscheidung erforderlichen Informationen übersichtlich und häufig auch graphisch unterstützt darstellt. Die vermeintliche Informationstransparenz wirkt häufig als Bauchgefühlverstärker des Anwenders und aus dem trügerischen Gefühl falscher Sicherheit heraus wird jetzt erst richtig fehlentschieden. Dieser regelmäßig zu erkennende Effekt spricht nicht gegen die verbesserte Benutzerfreundlichkeit solcher Hilfsmittel. Er zeigt aber, dass Disziplin in der Anwendung gefordert ist. Auch wenn diese häufig nicht eingefordert wird, weil man sich ihrer Notwendigkeit nicht bewusst ist.
Prozessstabile, reproduzierbare und von der schwankenden Erfahrung und Eigenüberschätzung des Menschen unabhängigere Planungs- und Dispositionsprozesse erreichen Sie nur, wenn Sie Ihre Planungs- und Dispositionsprozesse stärker automatisieren und der Mensch nur aus zwei Gründen eingreift: Erstens, um Fehlentscheidungen des Systems zu korrigieren, die daraus resultieren, dass dem System bestimmte entscheidungsrelevante Informationen nicht bekannt sein konnten. Zweitens, um das „Tuning“ des Systems (die Regelwerke) nachzujustieren, wenn das System eine „falsche“ Entscheidung getroffen hat, die es bei richtiger Parametereinstellung hätte richtig treffen können.
Über diese Prinzipien lassen sich natürlich nicht die Präzision und Reproduzierbarkeit des CNC-Programmes einer Werkzeugmaschine erreichen. Ziel muss es aber sein, dass 80 % der Systemvorschläge „durchgewinkt“ werden können. Dies lässt sich bei konsequenter Berücksichtigung der vorausgehend diskutierten Best-Practice-Regeln auch erreichen. Bei den restlichen 20 % zu korrigierender Systemvorschläge – und nur dort – wirkt sich der „Cockpit-Effekt“ eher positiv aus. Es bleibt jedoch immer die Gefahr, falsche Vorschläge durch falsches Bauchgefühl zu ersetzen.
Eine Best-of-Class Disposition muss deshalb auch systemseitig Unterstützung für dispositive Sonderfälle, wie Auslauf- und Einlaufplanung, Ersatzteilmanagement oder gemeinsam Verbunddisposition mehrerer Artikel bieten.
Best-Practice-Baustein 17: Planungs- und Dispositionsprozesse müssen möglichst prozessstabil und deshalb stark regelbasiert automatisiert werden und auch für dispositive Sonderfälle muss systemtechnische Unterstützung verfügbar sein.
Das ERP-System ist richtig eingestellt, Daten werden sauber zurückgemeldet, Dispositionsprozesse laufen so weit wie möglich automatisch ab – was steht dem Erfolg noch im Wege? In vielen Unternehmen zuerst und vor allem die schlechten Prognosedaten, auf denen die Disposition aufsetzen muss. Eine wesentliche Voraussetzung für den Erfolg der Disposition stellt nämlich die Absatz- und Bedarfsprognose dar, denn es gilt:
Grundprinzip 18: Vage Vermutungen über zukünftige Bedarfe sind tödliches Gift für jede Disposition.
Selten kann es sich die Disposition erlauben, auf konkreten Kundenbedarfen aufzusetzen. Für einen Großteil der Artikel werden Sie auf Vermutungen über die zukünftige Bedarfsentwicklung angewiesen sein. Bei schlechter Bedarfsprognose wirkungsvoll zu steuern gleicht dem Versuch, ein leistungsfähiges Schiff erfolgreich zu segeln, ohne zu wissen, woher der Wind weht.Die Best-Practice-Regeln, die zu einer leistungsfähigen Absatz- und Bedarfsprognose erforderlich sind, haben wir an anderer Stelle bereits diskutiert (siehe Best-Practice-Regeln für die Absatzprognose). Hier wollen wir nur festhalten:
Best-Practice-Baustein 18: Eine Best-Practice-Disposition baut auf einer Best-Practice-Prognose und einer leistungsfähigen Planverteilungsrechnung auf.
Wenn Sie die beschriebenen Best-Practice Kriterien erfüllen, dann arbeitet Ihre Disposition wirklich auf Weltklasseniveau. Hinsichtlich der Fertigungssteuerung gilt es jedoch noch einige Lichter zu entzünden, um nach Best-in-Class Kriterien die Fertigung zu regeln.
Eine neue Dispositionswelt
Unternehmen, die die beschriebenen Best-Practice Bausteine realisiert haben, leben in einer neuen Dispositionswelt:Dispositionsentscheidungen werden schneller und zuverlässiger getroffen und sind deutlich weniger von der Erfahrung und dem Bauchgefühl des einzelnen Anwenders abhängig. Personalfluktuation in der Disposition ist weniger kritisch. Das ERP-System leistet nun endlich das was es soll: Es wickelt die Masse der Routineaufgaben ab und lässt den Disponenten die Zeit, sich um die wirklich kniffeligen Fragenstellungen zu kümmern.
Der Planungs- und Steuerungsprozess wird transparenter und effizienter, Stress, Hektik und Reibungsverluste zwischen den Unternehmensbereichen nehmen ab. Die neue Welt bietet jedoch nicht nur ein ruhigeres Arbeitsumfeld, sondern knallharte betriebswirtschaftliche Vorteile: Eine stabilere Lieferbereitschaft am Markt führt zu zufriedeneren Kunden und legt das Fundament für Umsatzsteigerungen und höhere Marktanteile. Sie führt außerdem dazu, dass in der Fertigung weniger umgesteuert werden muss, was sich günstig auf die Produktionskosten auswirkt und wodurch die Gesamtkosten der Wertschöpfungskette sinken.
Hohe Potenziale
Erfahrungswerte aus zahlreichen Projekten zeigen uns, dass eine Bestandsreduzierung von 15 % bis 25 %, verbunden mit einer stabileren und besseren Lieferbereitschaft zu erreichen ist, wenn die Regelwerke ausreichend differenziert optimiert worden sind. Darüber hinaus verringert die weitere Automatisierung der Dispositionsprozesse den erforderlichen Personalaufwand um 25 % bis 45 %.Eine neue Welt, die sich ohne Risiken erreichen und ihre Wohltaten jedem angedeihen lässt, der sich konsequent auf den Weg macht!
Das könnte Sie auch Interessieren: