Produktionslogistik: Prozesskettenoptimierung bei Erhard Armaturen
Die Lagerhaltung von Fertigteilen ist extrem teuer, denn hier wird nahezu die gesamte Wertschöpfung des Unternehmens inklusive Personalkosten bevorratet. Die Firma Erhard Armaturen GmbH & Co. hat deshalb ihren gesamten Beschaffungs- und Produktionsprozess in einem zweijährigen Projekt optimiert, um das Fertigwarenlager abzubauen und trotzdem die Lieferbereitschaft zu erhöhen. Heute ist man bis zu 98 % lieferbereit und Fertigwarenbestände werden nur noch für die Erzeugnisse gehalten, die einen hohen, planbaren Bedarf aufweisen oder die für die Installateurkunden bereitstehen müssen, die sich morgens auf dem Weg zur Arbeit noch eindecken wollen.
Durch die Verminderung der Fertigwaren reduzierte sich auch der Anteil der Erzeugnisse, die aufgrund fehlender Teile wieder demontiert bzw. umgebaut werden mussten. Insgesamt wurde jedoch nicht nur die betriebsinterne Wertschöpfung aus dem Lager genommen, sondern der gesamte Warenbestand im Unternehmen drastisch reduziert. So konnten auch die Bestände in den Eingangs- und Zwischenlägern trotz deutlicher Erhöhung der Lieferbereitschaft um ca. 40% reduziert werden. Dies führte zu einer wesentlich verbesserten Finanzstruktur des Unternehmens, denn mit jeder eingesparten Million Lagerbestandswert können 150 bis 300 Tausend DM Verwaltungskosten gespart werden.
Erhard Armaturen GmbH & Co ist ein traditionsreiches Unternehmen mit derzeit 680 Mitarbeiterinnen und Mitarbeitern an 4 Produktionsstätten in Heidenheim, Oettingen, Bad Köstritz und Daun und einen Umsatz von 160 Mio. DM. Für die Wasser- und Gasversorgung, Abwasserentsorgung, Industrie und Verfahrenstechnik werden im Werk Oettingen acht Erzeugnisgruppen in unterschiedlichen Varianten gefertigt (z.B. metallisch dichtende/weichdichtende Schieber, Rückflusssperren/Rückschlagklappen, Be/Entlüftungsventile, Membranventile, Hydranten). Die Produktion teilt sich aufgrund des reichhaltigen Variantenspektrums in eine Vorfertigung und mehrere Endmontagen (Bild 1), die bis dato an ein Fertigwarenlager lieferten.
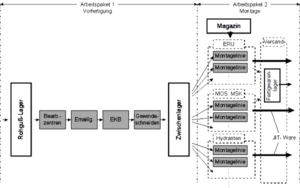
Aufbau der Just-in-Time-Montage
Dieses Fertigwarenlager wurde jedoch als unnötiger Kostenapparat erkannt und sollte reduziert werden. Im Prinzip lässt sich diese Forderung auch leicht erfüllen: Man räumt das Lager mit den eingehenden Bestellungen Zug um Zug bis es auf die richtige Größe reduziert ist und fertigt von da ab nur noch auftragsbezogen. Dies ist natürlich eine einäugige Sichtweise, denn kaum ein Kunde würde die damit verbundene Zeitverzögerung von mehreren Wochen in Kauf nehmen. Demzufolge musste die gesamte Supply Chain vom Einkauf bis hin zur Montage optimiert werden (Bild 2).
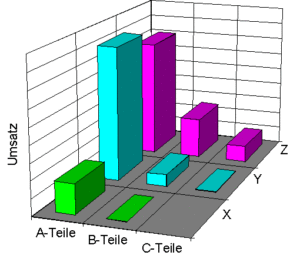
Um stets mindestens den Lieferbereitschaftsgrad halten zu können, begann man zunächst mit der Optimierung der Disposition für die Rohteile- und Halbfabrikateläger und implementierte gleichzeitig eine Fertigungssteuerung zum Aufbau einer montagesynchronen Vorfertigung. Hiermit wurden die Voraussetzungen für den Aufbau einer Just-in-Time Montage und den Abbau des Fertigwarenlagers geschaffen.
Optimierung der Dispositionsstrategie
Zur Festlegung der Dispositionsstrategie wurde die Artikelstruktur je Erzeugnisgruppe ermittelt und analysiert. Hierzu wurden die Teilebewegungen je Erzeugnisgruppe vom Zwischenlager/Rohgusslager des abgelaufenen Geschäftsjahres herangezogen. Für die Auswahl der geeigneten Prognoseverfahren war es bei der vorliegenden Zielsetzung erforderlich, die Bedarfsschwankungen je Eigenfertigungsteil und Rohgussteil auf Wochenbasis zu kennen. Mittels einer ABC-XYZ-Analyse (Umsatzrelevanz-Verbrauchsverhalten) wurde die Artikelstruktur je Erzeugnisgruppe nach Umsatzwichtigkeit und Vorhersehbarkeit bzw. Gleichmäßigkeit des Bedarfs beurteilt und mittels Simulation die zukünftige Bestandsentwicklung berechnet.
Die Erkenntnisse aus der Analyse der Artikel führten zur Festlegung, welche Halbfabrikate im Zwischenlager, welche Rohgussteile im Rohgusslager gelagert werden müssen und welche Prognoseverfahren für die Vorhersage der zukünftigen Teilebedarfe geeignet sind. Darüber hinaus legte man fest, wie Losgrößen und Mindestbestellmengen zukünftig zu ermitteln sind und wie Grundwert, Sicherheitsbestand und Meldebestand errechnet werden.
Montagesynchrone Fertigungssteuerung
Die Zielsetzung, flexible, reaktionsfähige und kostenoptimierte Fertigungsprozesse mit hoher Lieferbereitschaft zu erreichen, erforderte den Aufbau einer Organisationseinheit “Fertigungssteuerung” mit der erforderlichen Kompetenz und Verantwortung. Von Disposition und Fertigung wurde hierzu ein Belastungsdiagramm je Maschine aus den Lagerzugängen des abgelaufenen Geschäftsjahres erstellt und so bisher existierende Kapazitätsengpässe aufgedeckt. Mit diesen Informationen gelang es, eine Kapazitätsplanung aufzubauen, die von nun an rollierend in Wochen- und Monatsplänen geführt wird. Nach Festlegung des Ablaufs und der Instrumentarien zur Steuerung von Kundenaufträgen wurde die Fertigungsplanung in Kraft gesetzt.
Aufbau der Just-in-time-Montage in drei Schritten
Danach erfolgte der Aufbau der Just-in-time-Montage in drei Arbeitsschritten:
1. Strukturierung des Erzeugnisspektrums
Um zukünftige Montagelinien festlegen zu können, wurde in einer Voruntersuchung zunächst das Enderzeugnisspektrum analysiert. Hierzu wurden die Bewegungen je Erzeugnis/Erzeugnisgruppe des abgelaufenen Geschäftsjahres zu Kundenwunschterminen und -mengen herangezogen und die Bedarfe hinsichtlich Höhe und Gleichmäßigkeit ermittelt. Diese Bedarfe wurden anschließend dem Vertrieb zur Überprüfung hinsichtlich zukünftiger Abweichungen für die nächsten Jahre vorgelegt. Je Erzeugnis und Erzeugnisgruppe wurden dann die Prozessketten der Montagen (inkl. Vormontagen) erhoben und die benötigten Kapazitätsbedarfe je Zeiteinheit ermittelt. Auf Basis dieser Bedarfe wurde das Kapazitätsangebot je Erzeugnisgruppe festgelegt.
2. Materialflussgerechte Anordnung der Montagelinien
Um eine materialflussgerechte Anordnung der Montagelinien bestimmen zu können, wurde ein Arbeitsteam aus Produktionsmitarbeitern und Beratern bestimmt, das in einem Pilotprojekt geeignete Bearbeitungsszenarien sammelte. Besonders geeignet war hierfür die Erzeugnisgruppe “Hydranten”, da sie in einer separaten Halle montiert wurde und neue Montagelinien ohne Restriktionen durch weitere Erzeugnisgruppen erprobt werden konnten.
Zunächst wurden die relevanten Kriterien für die Zuordnung von Erzeugnissen zu Montagelinien definiert. Hierzu zählen z.B. Erzeugnisuntergruppen, Nennweiten, Prüfvorschriften, benötigte Werkzeuge und Prüfeinrichtungen und auch Montage- und Prüfzeiten. Anschließend wurden die Erzeugnisse auf die Montagelinien verteilt. Zwei Faktoren bestimmten dabei die materialflussgerechte Anordnung der Montagelinien:
- das Hallenlayout gab z.B. verfügbare Flächen, Hallentore, die generelle Materialflussrichtung sowie ortsfeste Werkzeuge und Einrichtungen vor
- das bereitzustellende Teilespektrum (Groß-/Kleinteile, Behältergrößen, Lagermöglichkeiten, etc). musste entsprechend dimensioniert und angeordnet werden
Um Zwischenpuffer für Vormontageeinheiten (Baugruppen) zu vermeiden, wurde untersucht, wie diese kapazitiv in den Arbeitsfluss der Montagelinien integriert werden konnten.
3. Dimensionierung der Bereitstellungspuffer an den Montagelinien
Um die Bereitstellpuffer angemessen dimensionieren zu können, wurde mittels Stücklistenauflösung das je Montagelinie erforderliche Teilespektrum ermittelt und nach Höhe und Gleichmäßigkeit des Teilebedarfes klassifiziert. Unter Berücksichtigung der Teileabmessungen konnten nun geeignete Behältnisse und Bereitstellungsformen (Lagerung vor Ort/ bedarfsbezogene Bereitstellung) festgelegt werden. Anschließend wurden die benötigten Pufferflächen ermittelt und die Teileanordnung im Puffer bestimmt. Wegen der begrenzten Platzverhältnisse mussten diese Schritte teilweise mehrmals iterativ durchgeführt und den Gegebenheiten angepasst werden.
Abschließend wurde die Nachbevorratungsstrategie der Teile aus dem Kaufteile- bzw. Eigenfertigungsteilelager festgelegt. Für vor Ort lagernde Teile kommen unterschiedliche Strategien zum Einsatz: Höherwertige Teile mit regelmäßigem Bedarf werden nach einem Kanban-System nachbevorratet, Schüttgut wird in regelmäßigen Zyklen von einem Lagermitarbeiter aufgefüllt und Gitterboxen (überwiegend Eigenfertigungsteile) werden aufgrund der beengten Verhältnisse von den zuständigen Vorarbeitern ständig kontrolliert und nach Aufforderung von einem Staplerfahrer kurzfristig bereitgestellt. Bedarfsbezogen zu kommissionierende Teile werden auftrags- und terminbezogen auf Kommissionierwagen zusammengestellt und zu einer gekennzeichneten Bereitstellfläche gebracht.
Erfolgreiches Pilotprojekt
Die erfolgreiche Umsetzung der Pilotlinien zeigte die erheblichen Potentiale einer flexiblen JIT-Montage auf und konnte die letzte Skepsis der Mitarbeiter weitgehend beseitigen. Nach den guten Erfahrungen aus dem Pilotprojekt wurde die beschriebene Vorgehensweise auf alle weiteren Erzeugnisgruppen übertragen und abschließend ein komplettes Hallenlayout erstellt.
Die Umstellung des gesamten Produktionsprozesses wurde im zweiten Halbjahr 2000 mit Erfolg abgeschlossen:
- Fertigwarenbestände sind zum größten Teil entfallen. Bestände sind nur noch für die Erzeugnisse erforderlich, die von den Installateuren morgens auf dem Weg zur Arbeit mitgenommen werden. Durch die Verminderung der Fertigwaren reduzierte sich auch der Anteil der Erzeugnisse, die aufgrund fehlender Teile wieder demontiert bzw. umgebaut werden müssen. Auch haben sich die Bestände im Zwischenlager trotz deutlicher Erhöhung der Lieferbereitschaft um ca. 40% reduziert. Die Reichweite des Zwischenlagers für beschichtete Halbfabrikate wurde unter Berücksichtigung eines Sicherheitsbestandes kleiner als ein Monat.
- Durch den Einsatz von Bearbeitungszentren in der ersten Bearbeitungsstufe wird der Rohguss zukünftig in wesentlich kleineren Losen bearbeitet. Dies führte zur Verringerung des Rohgusseingangslagerbestands um etwa 30%. Da diese Teile in der Vorfertigung dann direkt komplett bearbeitet werden, kann auf die Zwischenlagerung von angearbeitetem Rohguss ebenfalls verzichtet werden.
- Standarderzeugnisse können aufgrund der hohen Flexibilität der Montage zukünftig in drei bis fünf Tagen bereitgestellt werden. Dies entspricht den regulären Lieferzeitanforderungen vieler Kunden. Der gesamte Fertigungsprozess benötigt zukünftig einen zeitlichen Durchlauf von ca. zwei Wochen bei EKB-Beschichtung bzw. drei bis vier Wochen bei kombinierter EKB- und Email-Beschichtung.
Auch die Mitarbeiter des Arbeitsteams sehen die neue Montageorganisation sehr positiv.