von Peter Pantscharowitsch1, Dr. Götz-Andreas Kemmner, Andreas Gillessen
Viele Hersteller personalintensiver Branchen verlagern seit Jahren ihre Produktion ins Ausland. Der Pirmasenser Schuhmodenhersteller Peter Kaiser entschied sich jedoch, ein neues Werk in Deutschland zu bauen. Neben dieser Neubaumaßnahme zur Zusammenlegung der deutschen Werke wurden alle Unternehmensbereiche einer straffen Neustrukturierung unterzogen. Mit dieser neuen Organisationsform will Peter Kaiser den Standort Pirmasens auch für die Zukunft international wettbewerbsfähig halten.
Peter Kaiser produziert an den beiden Standorten Pirmasens und Legares, Portugal, jährlich 1,4 Mio Paar Damenschuhe im gehobenen Preissegment. Zum Zeitpunkt des Projektbeginns entfielen auf den Standort Pirmasens mit einem Hauptwerk und zwei Außenwerken 1,2 Mio. Paar Schuhe. In Legares wurden weitere 200.000 Paar gefertigt. Durch umsichtige und vorausschauende Geschäftspolitik gelang es Peter Kaiser, sich im umkämpften Schuhmarkt gut zu behaupten und trotz des produktbedingt hohen Personalkostenanteils profitabel zu arbeiten. Es war jedoch absehbar, dass Kostensteigerungen durch die hochwertigen Materialien, v.a. Leder, und die Lohnkostensteigerungen in wenigen Jahren die am deutschen Standort erarbeiteten Erträge auffressen würden. Vor diesem Hintergrund beauftragte Peter Kaiser Abels & Kemmner im August 2001 mit der Erarbeitung eines mittelfristigen Standortkonzeptes für den Produktionsstandort Pirmasens.
Ziel des “OptiKaiser” genannten Projektes war und ist es, die Schuhproduktion am Standort Pirmasens international wettbewerbsfähig zu halten. Hierzu mussten Möglichkeiten zur organisatorischen, technischen und kapazitiven Weiterentwicklung erarbeitet, bewertet und zu einem Gesamtkonzept zusammengefasst werden und mit der Alternative des Ausbaus der Produktion in Portugal verglichen werden.
Engpassanalyse
Die wichtigsten Handlungsfelder hierfür ergaben sich dabei aus der Engpassanalyse, mit der Abels & Kemmner die Projektarbeit bei Peter Kaiser begann. Innerhalb dieser zügig und detailliert durchgeführten Analyse zeigten sich Verbesserungspotenziale in den Feldern Standortstruktur, Beschaffungsorganisation, Versand, Informationstechnologie, Shopfloor-Produktivität (mit den Arbeitsfeldern Produktionstechnik, Prozessstabilität, Materialfluss & Layout und Arbeitsorganisation) sowie im Anlaufmanagement. Diese Handlungsfelder wurden in Teilprojekte strukturiert und für jedes Teilprojekt wurde ein Projektteam festgelegt, das für die konzeptionelle Ausarbeitung im Rahmen von Workshops unter den verschiedenen Expansionsszenarien verantwortlich war. Um letztlich die Gesamtkonzeption entscheidungsfähig auszuarbeiten, wurden anschließend die Teilkonzepte entsprechend des ausgewählten Expansionsszenarios betriebswirtschaftlich bewertet. Darauf aufbauend wurde das Finanzierungskonzept und ein Umsetzungsplan erarbeitet.
Standortplanung
Im Ergebnis zeigte sich, dass sich die Neubaumaßnahme am Standort Pirmasens gegenüber einer Produktionsverlagerung nach Portugal, verbunden mit dortigen Neuinvestitionen, behauptet. Folgende Faktoren brachten letztlich die Entscheidung zu Gunsten einer Investition am Standort Pirmasens:
- Die Arbeitsproduktivität am Standort Pirmasens ist noch immer höher als im Werk in Legares.
- Hervorragend qualifiziertes und mit den hohen Qualitätsanforderungen vertrautes Personal war in Pirmasens in ausreichender Anzahl vorhanden.
- Die eingespielte flexible Lieferantenstruktur sichert die Materialversorgung am Standort Pirmasens deutlich besser als am Standort Legares.
- Die Engpassanalyse und die anschließenden Teilprojekte brachten beträchtliche Verbesserungspotentiale zu Tage, die in Pirmasens deutlich kurzfristiger als in Portugal realisiert werden konnten.
Aufgrund dieser Schlüsselfaktoren amortisiert sich die Investition in Pirmasens bereits zu einem Zeitpunkt zu dem entsprechende Produktions- und Personalkapazitäten in Portugal noch nicht zur Verfügung stehen können. Im Ergebnis gewann das neue Standortkonzept Pirmasens durch einen besseren EBT und Cash-flow gegenüber der Alternative in Portugal.
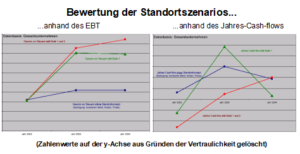
Bei der Standortplanung wurde ein dreistufiges Handlungsszenario mit mehreren Handlungsalternativen auf jeder Stufe erarbeitet. Auf jeder Handlungsstufe wurde anhand strategischer Kriterien sowie detaillierter Cashflow- und Ertragsanalysen die sinnvollste Variante ausgewählt. Eine Reihe grundsätzlich möglicher Handlungsalternativen entfiel dabei, weil sich bei der weiteren Ausarbeitung der Produktivitätsmaßnahmen in den einzelnen Teilprojekten bestätigte, was sich bereits bei der Engpassanalyse abgezeichnet hatte:
- Die Integration der beiden Außenwerke (Werk III und Werk V) war unumgänglich, obwohl beide Werke durch ihre schlanken Strukturen und beschränkten Produktspektren im innerbetrieblichen Vergleich die höchsten Produktivitätszahlen erreichten. Doch diesem Produktivitätsvorteil standen beträchtliche Schnittstellenkosten gegenüber.
- Zahlreiche Produktivitätspotenziale am Standort Pirmasens können nur mittels eines verbesserten Materialflusses und eines stringenteren Layouts der Produktion ausgeschöpft werden.
Entwicklung zukünftiger Standortstrukturen
Als Entscheidungsgrundlage für die Wahl der zukünftigen Standortstrukturen war es unerlässlich, die bestehenden Werke im Rahmen eines internen Benchmarkings miteinander zu vergleichen. Das Benchmarking sollte darüber Aufschluss geben, wie sich die Produktivitätssituationen in den vier Werken unter Berücksichtigung der werksindividuellen Randbedingungen darstellen und welches die spezifischen Erfolgsfaktoren sind. Die Erkenntnis war, dass die beiden kleinen Außenwerke in Pirmasens, auch unter Berücksichtigung der nur durch das Werk 1 möglichen schlanken Strukturen und des geringeren Produktionsspektrums, produktiver arbeiteten. Dies hatte entscheidenden Einfluss auf die Gestaltung des neuen Materialflusses und Produktionslayouts für den Erweiterungsbau.
Der Weg zum Ziel
Um eine für das Management hinreichende Entscheidungsgrundlage auf Basis von Ertrags- und Cashflowanalysen entwickeln zu können, mussten zuvor einige Hausaufgaben gemacht werden. Im Einzelnen umfassten die Teilprojekte, die Abels & Kemmner nach der initialen Engpassanalyse über zwei Monate hinweg begleitete, folgende Bereiche, von denen im Folgenden die wichtigsten detaillierter erläutert werden.
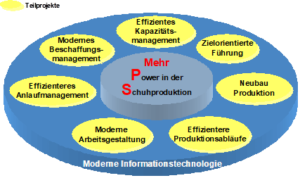
Bei Peter Kaiser werden jährlich sechs Kollektionen dem Markt angeboten. Zur Vorbereitung der Kollektionen werden ca. 1.500 Prototypen angefertigt. Daraus entstehen ca. 600 Modellen, die in bis zu 15 Schuhgrößen angeboten werden. Durch die angebotene Farb- und Materialvielfalt ergeben sich ca. 1.350 unterschiedliche Materialmöglichkeiten. Die Schuhhändler können nun innerhalb der Modelle einer Kollektion individuelle Farb- und Materialvarianten wählen, woraus letztendlich ca. 12.000 Artikelvarianten resultieren. Alle diese Artikel werden auftragsbezogen in bis zu 40 Arbeitsschritten, in einer durchschnittlichen Auftrags-Losgröße von 8 Paaren pro Tag gefertigt – mass customization at its best!.
In mehreren Schüben ca. 600 neue Modelle jährlich hochzufahren, erfordert ausgeklügelte Arbeitsabläufe und einen hohen Abstimmungsaufwand zwischen den Abteilungen. Um den Anlauf neuer Modelle noch reibungsloser zu gestalten wurde ein Anlaufmanagement eingeführt. U.a. treffen sich in einem SE-Team2 Vertreter aus der Kollektionsentwicklung, der Produktion, dem Einkauf und der Planung regelmäßig, um Erfahrungen mit der Fertigung neuer Prototypen auszutauschen sowie Entwicklungs- und Planungsmaßnahmen miteinander abzustimmen. Weiterhin wird eine detaillierte “Planungsmatrix” demnächst einen detaillierten Überblick über den Fertigstellungsgrad jedes Werkzeuges und den Beschaffungszustand jedes Zukaufteils ermöglichen. Eine konsequente Reduzierung der Teilevielfalt verbunden mit Standardisierungsmaßnahmen wird die Beschaffungs- und Produktionsabläufe vereinfachen ohne die Gestaltungsfreiheit der Modelleure einzuengen oder die Modellvielfalt zu reduzieren.
OptiKaiser-Projektphasen
Das Projekt “OptiKaiser” gliederte sich in 4 Phasen: 1. Engpassanalyse und Teilprojektplanung, 2. Grobkonzeption, 3. Gesamtkonzeption und 4. Umsetzung. In der ersten Phase wurden die zentralen Handlungsfelder mit ihren Verbesserungsansätzen und die daraus resultierenden Produktivitäts- und Rationalisierungspotenziale erarbeitet. In der zweiten Phase mussten diese Handlungsfelder in ihre einzelnen Teilprojekte strukturiert und deren Produktivitätspotenziale unter verschiedenen Expansionsszenarien überprüft und konzeptionell ausgearbeitet werden. Anschließend diente die dritte Phase dazu, aus den verschiedenen Expansionsszenarien ein Gesamtkonzept auszuarbeiten, betriebswirtschaftlich zu bewerten sowie ein Finanzierungskonzept und einen Umsetzungsplan zu erarbeiten, der in der 4. Phase durchzuziehen war. Entsprechend dem Repowerment-Ansatz von Abels & Kemmner wurden Teile der Produktivitätsmaßnahmen bereits parallel zur 2. und 3. Phase umgesetzt.
Produktivitätscontrolling
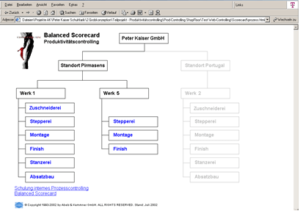
Um alle Werke und deren Produktionsabteilungen zukünftig täglich messen und vergleichen zu können, wurde auf Basis der bereits erarbeiteten internen Benchmarking-Messgrößen ein langfristig angelegtes Produktivitätscontrolling aufgebaut. Ziel ist es, die Werks-, Abteilungsleitung und Meister durch die tägliche Rückkopplung der erreichten Leistung und den Vergleich mit den gemeinsam erarbeiteten Zielwerten in die Lage zu versetzen, ihre Bereiche zielorientiert führen zu können.
Das Produktivitätscontrolling gestaltet sich wie folgt:
- Alle Kennzahlen werden täglich gemessen. Darüber hinaus werden die Kennzahlen zu Monatswerten verdichtet und über die letzten 25 Monate verfolgt. Nach einer Anlaufphase wurden Zielwerte je Abteilung festgelegt
- Zum jetzigen Zeitpunkt werden die Kennzahlen je Abteilung gemessen. Später sollen sie für jeden Meisterbereich gemessen werden
- Die Kennzahlen werden täglich zwischen Meister und Abteilungsleiter besprochen. Als Ergebnis der Besprechungen werden Maßnahmen zur Verbesserung definiert und umgesetzt. Zur Verfolgung der Umsetzung der vereinbarten Maßnahmen wird eine ” Erläuterungs- und Maßnahmenliste” geführt.
- Alle Kennzahlen sowie die ” Erläuterungs- und Maßnahmenliste” werden in der Abteilung ausgehängt. Auf Basis des Kennzahlensystems soll damit ein kontinuierlicher Verbesserungsprozess / Change Management aufgebaut werden.
- Die Kennzahlen werden über die folgenden Stufen nach oben verdichtet:
- Arbeitsgang – Meisterbereich – Abteilung – Werk – Standort – Gesamtunternehmen
- Die Kennzahlen werden auf einem zentralen Informationssystem gehalten. Zugriffsberechtigte können mit Hilfe eines Internetbrowsers über das interne Netzwerk bzw. über das Internet auf die Kennzahlen zugreifen
In einem weiteren Schritt wurde das Produktivitätscontrolling in eine übergeordnete Balanced Scorecard eingebunden, in der später auch Kennzahlen über das reine Produktivitätscontrolling hinaus geführt und dokumentiert werden sollen.
Neben den hier angerissenen Maßnahmen wurde und wird eine ganze Reihe weiterer Maßnahmenkomplexe umgesetzt, die unter dem Motto “Mehr PS” alle das gemeinsame Ziel verfolgen, die langfristige Wirtschaftlichkeit der Schuhproduktion am Standort Pirmasens im internationalen Wettbewerb zu sichern. Die dargestellten Aktivitäten zeigen dabei, dass der optimale Standort bei existierenden Standortstrukturen nicht alleine am Lohnniveau festgemacht werden kann. Es bedarf vielmehr einer Analyse der gesamten unternehmerischen Optionen, um abschließend eine begründete Entscheidung treffen zu können. Diese fällt mitunter anders aus, als es einem der unternehmerische Instinkt vorher geraten hätte. Dies bestätigt zumindest die Entscheidungsgrundlage von Peter Kaiser.
1Herr Peter Pantscharowitsch ist Technischer Leiter der Peter Kaiser GmbH, Pirmasens
2Simultaneous Engineering-Team