Unproduktive Peitscheneffekte bei marktsynchroner Produktion vermeiden
von Oswald Kuschel1, Peter Bröcker2, Andreas Gillessen, Dr. Götz-Andreas Kemmner
Das heutige Supply Chain Management hat in der gegenwärtigen Marktsituation nur einen einzigen und unbestrittenen Maßstab: Die Wünsche und Anforderungen der Kunden und des Marktes. Um diesem Maßstab bei anhaltender Explosion der Produktvarianten gerecht zu werden, müssen Unternehmen nahezu aller Branchen schlanke und flexible Wertschöpfungsketten aufbauen, die mit möglichst geringen Beständen und geringer Ressourcenverschwendung gefahren werden können. Durch die Unsicherheit in den Markterwartungen und eine zunehmend stochastischer werdende Kundennachfrage steigen die Anforderungen an das Supply Chain Management und insbesondere an die Flexibilität der Unternehmen weiter. Wie in einer solchen Situation die Produktivität trotz fehlender Economies-of-Scale dennoch gesteigert und die Marktwünsche befriedigt werden können, zeigt das Beispiel der Orthomol GmbH in Langenfeld.
Das Unternehmen Orthomol hat sich zum führenden Spezialisten für ergänzende bilanzierte Diäten entwickelt. Aktuell werden mehr als 100 Produkte und über 50 Probe- und Musterartikel produziert. Als Lieferservice garantiert Orthomol seinen Kunden, dass Aufträge, die bis 13:00 Uhr mittags eingehen, noch am gleichen Tag um 17:00 Uhr verschickt werden. Später eingehende Order am folgenden Tag. Um diesen schnellen Service bei steigender Individualisierung der Produkte und einer zunehmend stochastischeren Nachfrage gewährleisten zu können, muss die gesamte Wertschöpfungskette vom Versand über die Konfektionierung bis zur Produktion bei Orthomol ein sehr hohes Maß an Flexibilität aufweisen (s. Abbildung 1). So können durch optimierte Rüstzeiten relativ häufig Produktwechsel vorgenommen werden. Die Produktion liefert über die Konfektionierung direkt in das Fertigwarenlager, welches über Reichweiten auf Basis der Absatzplanung gesteuert wird. Die Bestände und damit die Reichweiten wurden aufgrund der hohen Flexibilität der Produktion sehr gering gehalten. Entnahmen aus dem Lager führten jedoch nahezu unmittelbar zum Anstoß der Nachproduktion. Damit kurzfristige Reaktionen und eine hohe Flexibilität möglich waren, mussten in allen Bereichen Personalkapazitäten “vorgehalten” werden, um kurze Durchlaufzeiten und geringe Bestände zu gewährleisten. Auf der Ebene der verpackten aber noch unkonfektionierten Mischung gibt es darüber hinaus keine Lagerstufe. Daher hängt die Auslastungssituation des Bereichs Konfektionierung unmittelbar von der Produktionsleistung der parallel laufenden Fertigungslinien ab. Die Produktion gibt somit auch den Takt für die Auslastung der personal-intensiveren Konfektionierung an. In der Konfektionierung werden daher schon seit längerer Zeit Produktionsspitzen über sehr flexible externe Zulieferunternehmen ausgeglichen. Dennoch verursachten die Veränderungen in der Marktnachfrage auch in der Konfektionierung zunehmend größer werdende Verluste in der Bereichsproduktivität.
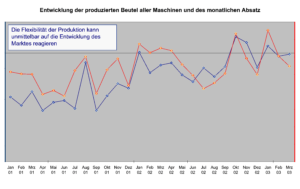
Harmonische Produktion trotz stochastischer Nachfrage
Die Analyse und Strukturierung des Artikelspektrums (ABC-XYZ-Analyse) bot hier gute Ansatzpunkte für eine Verbesserung. Durch Umstrukturierungen in den Lagerbeständen, d. h. Erhöhung der Reichweiten bei den Schnelldrehern mit relativ regelmäßigem Verbrauchsverhalten bei gleichzeitiger Realisierung von Reduzierungspotenzialen in anderen Artikelklassen, konnten ohne größere Lagerbestandsveränderungen große Verbesserungen im Produktionsplanungsprozess erreicht werden. Durch die Veränderung der Lagerbestandsreichweiten je Artikelklasse können jetzt die Marktschwankungen für die Produktion gedämpft werden. Die Produktionsplanung kann hierdurch mit höherer Sicherheit arbeiten. Orthomol ist jetzt in der Lage, die Produktion für 2 Wochen vorzuplanen und sogar eine Produktionsprogrammfixierung für eine Woche vorzunehmen. Dabei werden jedoch immer nur ca. 80 % aller Kapazitäten in Produktion und Konfektionierung verplant und ca. 20 % für so genannte Exoten und unerwartete Bedarfe offen gelassen. Treten diese außerordentlichen Bedarfe nicht auf, wird die Kapazität mit “normalen” Aufträgen aufgefüllt. Durch die Reduzierung der operativen Hektik und durch die verbesserte Planungssicherheit im Planungshorizont, können die starken Kapazitätsschwankungen reduziert und die Kapazitätsauslastung entscheidend verbessert werden. Dies führt zu starken Produktivitätsverbesserungen, wobei der Markt nach wie vor ohne Abstriche und ohne höhere Fertigwarenbestände bedient werden kann.
Um die Istsituation der Supply Chain zunächst richtig beurteilen zu können wurden u.a. folgende Untersuchungen durchgeführt:
- Analyse der Marktnachfrage und der darauf basierenden Absatzplanung, ihrer Prognoseverfahren und ihrer Prognosequalität
- Strukturierung des gesamten Artikelspektrums von den Rohstoffen bis zu den Fertigwaren (ABC / XYZ – Analysen), Analyse der Entwicklung der Lagerbestände, der Reichweiten und ihr Verbrauchsverhalten im Zeitverlauf
- Analyse der Produktivität der Bereiche Versand, Konfektionierung und Produktion im Zeitverlauf
- Ermittlung des Beschäftigungsrisikos der einzelnen Fertigungsbereiche
- Analyse der Produktionsplanung, ihre Planungsparameter, Einflussgrößen und Planungsqualität
- Überprüfung der Lieferzuverlässigkeit und Flexibilität der Lieferanten
Beschäftigungsrisiko definieren und Potenziale erarbeiten
Der erste Berührungspunkt einer wachsenden Marktstochastik ist natürlich die Absatzplanung. Die Analyse des Marktes und die Beurteilung der Absatzplanungsqualität bilden daher den Ausgangspunkt für alle weiteren Betrachtungen.
Die ständige Erhöhung der vom Markt geforderten Varianten führt ohne geeignete Gegenmaßnahmen direkt zu einer Erhöhung der Lagerbestände, weil die Absatzprognosen im längerfristigen Bereich natürlich nicht immer genau zutreffen können und darüber hinaus durch die vielen Produktvarianten auch eine Absatzschwankung im Produkte – Mix vorprogrammiert ist.
Detailanalysen der Absatzplanung bei Orthomol zeigten eine ähnliche Tendenz. Obwohl die Absatzplanung über das gesamte Artikelspektrum hinweg recht genau war, konnte auf der Einzelartikelebene nicht das mögliche Optimum erreicht werden. Durch die Verabschiedung und Einleitung verschiedenster Maßnahmen soll der Absatzplanungsprozess zukünftig das Prognoseoptimum für jeden einzelnen Artikel auf einem schwieriger werdenden Marktumfeld herausholen. Hierzu wurden u.a. folgende Maßnahmen abgestimmt:
- Klassifizierung des Artikelspektrums und Überprüfung / Neuzuordnung der am besten geeigneten Prognoseverfahren für jede Artikelklasse
- Setzen engerer Tracking – Signale des Absatzplanungssystems
- Einführung einer Planungsbesprechung vor Umsetzung der Planung mit Produktion und Einkauf
- Optimierung des Planungsprozesses für Marketingaktionen hinsichtlich notwendiger Vorlaufzeiten
- Fixierung des Planungszeitraums jedes einzelnen Produktes hinsichtlich des Zeitraums seiner “genauen” und verbindlichen Planung
- Einführung und Aufbau von Checklisten für die Produktmanager zur Planungsunterstützung
Veränderungen im Versand
Der Versand war in der Lage jede Marktnachfrage mit seinen vorhandenen Kapazitäten auch bedienen zu können. Die dabei erreichte Flexibilität war jedoch nicht so groß, um auf die täglichen Marktschwankungen in der Kundennachfrage durch kurzfristige Anpassungen der Beschäftigungssituation reagieren zu können (Abb.2). So waren tendenziell zu viele Mitarbeiter notwendig, um eine praktisch “100 %ige” Lieferbereitschaft zu garantieren. Deshalb war in der Diskussion, ob nicht der Arbeitsvorrat im Versand erhöht werden kann. Dies könnte dadurch geschehen, dass man die Auslieferung der Ware auf spätestens den übernächsten Arbeitstag verlängert. Durch das erhöhte Arbeitsvolumen könnte eine verbesserte Einsatzplanung und damit eine höhere Grundbeschäftigung realisiert werden. Diese Änderungen hätten jedoch direkte Auswirkungen auf die Lieferfristen. Getreu der Maxime “Der Markt stellt die Forderungen, wir folgen!” wurde sie deshalb verworfen. Über eine so genannte “Feierabendschicht auf Abruf” in Kombination mit einer Grundbeschäftigung sollen nun auftretende Spitzen flexibler abgefangen werden.
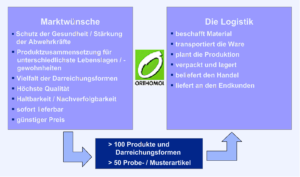
Veränderungen in der Konfektionierung
In der Konfektionierung wird darüber hinaus z. Z. überprüft, ob sich eine Intensivierung der Zusammenarbeit mit den externen Lieferanten bei gleichzeitiger Reduzierung der internen Grundbeschäftigung wirtschaftlich rechnet. Als zentrales Entscheidungskriterium gilt hierfür die Preisobergrenze, die durch die (zusätzlichen) Kosten der Eigenfertigung bestimmt und mit dem Zukaufspreis des Zulieferers verglichen wird.
Die kostenmäßigen Konsequenzen des Fremdbezuges der Dienstleistung ergeben sich dabei durch die Erfassung der Kosten, die bei Fremdbezug entstehen oder durch Fremdbezug eingespart werden können und ihrem anschließendem Vergleich mit der neuen Preisobergrenze für die Eigenfertigung. Die Kosten der Eigenfertigung werden dabei jedoch stark durch die Beschäftigungssituation und die Möglichkeit, die Kapazitäten an wechselnde Beschäftigungssituationen anzupassen, beeinflusst. Durch die neue Produktionsplanungssituation konnte die Kostensituation der internen Konfektionierung jedoch bereits entscheidend verbessert werden.
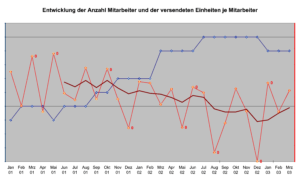
Zusammenfassung
Das Beispiel Orthomol zeigt, dass die allgemeine Tendenz hin zu mehr Flexibilität in einem immer schwieriger werdenden wirtschaftlichen Umfeld differenziert für jedes Unternehmen und für jeden Unternehmensbereich betrachtet werden muss. Entscheidend ist es, die Wünsche und Anforderungen der Kunden und des Marktes mit einer möglichst kostenminimalen Wertschöpfungskette zu bedienen. Diesen Anforderungen muss sich alles unterordnen. Auf dem Weg dorthin muss die Ertrags- und Innovationskraft des Unternehmens als entscheidende Überlebensgröße Maßstab aller Entscheidungen sein. Es kommt somit nicht auf die Produktivität des einzelnen Bereiches an, sondern auf die langfristige Gesamtproduktivität der Wertschöpfungskette. Häufig gilt es hierbei, im Trade-off zwischen Bestandskosten und Flexibilitätskosten den “optimalen “Betriebsbereich” zu finden.
Über Orthomol
Das Unternehmen Orthomol wurde 1991 von Dr. Kristian Glagau und seinem Partner Dr. Hans Dietl gegründet. Entgegen der allgemein wechselhaften Konjunktur wuchs die junge GmbH innerhalb weniger Jahre zu einem der Marktführer im Bereich Mikronährstoffe heran und beschäftigt zur Zeit mehr als 250 Mitarbeiter. Der Produktentwicklung erfolgt durch eine eigene Forschungs- und Entwicklungsabteilung. Mediziner, Pharmazeuten, Oecotrophologen und Biologen bei Orthomol beobachten ständig aktuelle Entwicklungen und Forschungsergebnisse im Bereich der Mikronährstoffe.
Orthomol – Produkte sind ergänzende bilanzierte Diäten und werden auf der Basis des orthomolekularen Prinzips entwickelt, das 1968 von dem amerikanischen Chemie-Nobelpreisträger Linus Pauling begründet wurde. Mikronährstoffe werden dabei im Rahmen einer ernährungsmedizinischen Behandlung eingesetzt, um zum Erfolg einer medizinischen Therapie beizutragen und das Fortschreiten von Erkrankungen zu verzögern. Die Mikronährstoffkombinationen von Orthomol enthalten Vitamine, Mineralstoffe, Spurenelemente, sekundäre Pflanzenstoffe (z.B. Phytoöstrogene, Bioflavonoide), Aminosäuren, Omega-3-Fettsäuren, und Probiotika je nach Indikationsgebiet. Die Besonderheit der Produkte ist ihre komplexe Zusammensetzung und ausgewogene Dosierung. Produkte von Orthomol sind indikativ zusammen gestellte Mikronährstoffkombinationen, die in der Regel auf Empfehlung des Arztes oder des Apothekers eingenommen werden. Sie sind ausschließlich in der Apotheke erhältlich.
1 Oswald Kuschel ist Betriebsleiter bei der Orthomol GmbH und hat das Projekt aus Kundensicht geleitet
2 Peter Bröcker ist Leiter Unternehmenscontrolling bei der Orthomol GmbH