Methodenchaos bei der Prozessoptimierung in den Griff bekommen
von Prof. Dr. Helmut Abels
Viele Produktionsunternehmen sind ständig bemüht, ihre Produktionsprozesse zu optimieren. Hierzu existiert eine Vielzahl von Optimierungsmethoden. Erfahrungen zeigen allerdings, dass immer noch überwiegend die Optimierung einzelner Bereiche bzw. Teilprozesse im Vordergrund steht. Die erzielten Optimierungserfolge “verpuffen” so leicht im Gesamtprozess oder wirken mitunter sogar kontraproduktiv, wenn sie nicht in eine durchgängige Gesamtlösung eingebettet sind.
Um den Methodeneinsatz besser zu organisieren, etabliert eine zunehmende Anzahl von Unternehmen so genannte “ganzheitliche Produktionssysteme” (GPS). GPS bilden einen Ordnungsrahmen für die Methoden, die in allen Teilen und Prozessen eines Unternehmens zum Einsatz gebracht werden sollen. Vorreiter dieser Entwicklung ist die Automobilindustrie, allen voran Toyota mit dem bekannten Toyota Produktionssystem (TPS). Heute verfügen auch alle anderen Automobilanbieter sowie viele Zulieferfirmen und in zunehmendem Maße auch Produktionsunternehmen anderer Branchen über solche Systeme. Im Daimler Chrysler Produktionssystem (DCPS) werden beispielsweise 92 Optimierungsmethoden beschrieben, von denen ca. 60 Methoden flächendeckend in allen Werken eingeführt werden sollen.
Der Erfolg dieser Systeme wird bisweilen in Frage gestellt. Kritiker hinterfragen, ob es ein standardisiertes System für alle Werke geben kann, wenn die Rahmenbedingungen (Produktstruktur, Zielmärkte, Fertigungsorganisation, etc.) deutlich voneinander abweichen (vgl. z.B. Weber/Wegge 2003). Ebenso lässt sich über die Übertragbarkeit dieses Ansatzes auf Einzel- und Kleinserienfertiger diskutieren. Dennoch: bei den bereits etablierten Produktionssystemen fallen immer wieder zwei Aspekte auf:
- Die Entwicklung synchroner (durchgängig optimierter) Produktionsprozesse ist Chefsache. Hier sind entsprechende Visionen und Vorgaben der Unternehmens- bzw. Werksleitung erforderlich, deren Entwicklung nicht delegiert werden können.
- Die angebotene Methodenvielzahl in Produktionssystemen ist immer noch erheblich. Damit bleibt auch die Frage offen, welches die notwendigen Methoden für die Umsetzung synchroner Produktionsprozesse sind und in welcher Reihenfolge diese Methoden dann eingeführt werden müssen.
Bei der Beantwortung dieser Fragestellung kann das Wertstrommanagement wichtige Hilfestellung leisten. Das Wertstrommanagement ist ein Management-Werkzeug, bei dem es von vorneherein nicht um die Betrachtung partieller Prozessschritte, sondern um den Herstellungsprozess als Ganzes geht, d.h. also mindestens “von Rampe zu Rampe”, aber auch werks- bzw. unternehmensübergreifende Betrachtungen sind möglich. Dabei bietet es der Führungskraft Hilfestellung in dreifacher Hinsicht an:
- Mit einfachen Hilfsmitteln wird zunächst und recht schnell eine transparente Diskussionsbasis durch Aufnahme des Ist-Zustandes geschaffen.
- Anschließend erfolgt die Entwicklung der zukünftigen Wertstromvision für den synchronen Prozessablauf.
- Aufgrund der Einfachheit der Darstellungen eignet sich das Wertstrommanagement auch hervorragend zur Kommunikation der Vision an die Mitarbeiter sowie zur Ableitung der erforderlichen Einzelmaßnahmen, die dann abgestimmt mit dem Gesamtentwurf in Projektteams umgesetzt werden.
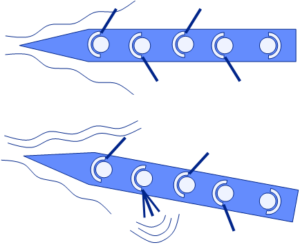