Konsequente Marktorientierung mit Pull-System bei Hansgrohe
Ulrich Jaeckle
Die Hansgrohe AG, einer der wenigen Global Player der Sanitärbranche, optimiert derzeit ihre Supply-Chain-Prozesse. Das Projekt “Logistics 2010” hat für das Unternehmen eine außerordentlich strategische Bedeutung. Dabei steht die Optimierung der gesamten Wertschöpfungskette im Vordergrund. In einem ersten Teilprojekt sollten Produktion und Beschaffung optimiert und konsequent noch den Marktbedürfnissen ausgerichtet werden. Erste Ergebnisse liegen jetzt vor: Durch die konsequente Umsetzung des Pull-Systems wird ab sofort keine Bestellung mehr ohne Nachfragebedarf ausgelöst, was Bestandssicherheit schafft. Das Bestandsreduzierungspotenzial bei den Rohmaterialien ist darüber hinaus mit über 30 Prozent enorm liquiditätssteigernd.
Summary
Stock reduction by over 30 %
– consistent market orientation with the aid the Pull System at Hansgrohe
Hansgrohe AG, one of the few global players in the sonitary branch, is currently optimising its supplychain processes. The project “Logistics 2010” has an extraordinary strategic meaning for the company Priority is given to optimising the entire value added choin. In the first part of the project the areas of production and procurement have been optimised and consistently been adopted to morket requirements. First results are evailable: to consistently opply the Pull System, no order has been launched without a specific demand which has lead to stock security. Furthermore the potential to reduce the stock of row material by over 30% has increased liquidity tremendousty.
Projektziele
Die Zielsetzung des Projektes war von Anfang an klar umrissen: Mit kurzen Reaktionszeiten will man auf die sich verschärfenden Anforderungen im Markt flexibel reagieren. Dabei sollen die Bestände so gering wie möglich gehalten werden, ohne dass der Lieferservice darunter leidet oder die Prozesskosten steigen.
Die konsequente Ausrichtung auf das Marktgeschehen heißt im Klartext, dass nachgefragte Produkte kurzfristig verfügbar sein müssen und dass ohne Nachfrage keine Beschaffung oder Wertschöpfung erfolgen darf. Dies bedingt fein abgestimmte Prozesssehritte innerhalb des Unternehmens, aber auch unternehmensübergreifend bis hin zu den Lieferanten.
In mehreren Teams wurden die anstehenden Aufgaben parallel angegangen: Das Prozessteam war verantwortlich für die Gestaltung der prozessorientierten Produktionslinien. Das Produktteam sollte den untemehmensinternen Materialfluss auf Verbrauchssteuerung umstellen. Das Beschaffungsteam hatte die Aufgabe, die Beschaffungsdisposition zu optimieren und die Lieferanten in den Beschaffungsprozess zu integrieren.
Bestandsanalysen
Mit dem Ziel, kurzfristig positive Effekte zu erreichen, entschied man sich im Bereich Beschaffungslogistik für ein zweistufiges Vorgehen. Zunächst sollte die Beschaffungsdisposition analysiert und umgestellt werden. Durch Optimlerung der Dispositionsparameter und Logistikgrößen lassen sich in vielen Fällen bereits mit geringem Aufwand Bestandssenkungen ereichen.
In einem zweiten Schritt galt es dann, die Lieferanten in den Beschaffungsprozess zu integrieren und so den Gesamtprozess effizienter und flexibler zu gestalten. Zu den Lieferanten zählen zum einen kleine und mittlere Betriebe in der Nähe des Hansgrohe Stammsitzes in Schiltach sowie zahlreiche in Deutschland verteilte Unternehmen. Weitere Lieferanten finden sich in Europa und Asien.
Bei der Vorgehensweise wendeten die Akteure vielfach bewährte Methoden und Verfahren an. Dazu gehörten.
- ABC/XYZ-Analysen,
- Bestandsreichweiten- und Bestandssumpfanalysen,
- Aufnahme der derzeitigen Beschaffungsprozesse und Lieferantenintegration,
- Simulation verschiedener Dispositions- und Planungsverfahren mit Variation bestimmter Parameter (z.B. Prognoseparameter) und logistischer Stellgrößen (z.B. Mindestbestellmengen, Lieferzeiten).
Eine erste Bestandsaufnahme der aktuellen Beschaffungsprozesse und der bestehenden Lieferantenbeziehungen zeigte, dass die Hansgrohe AG bereits auf hohem Niveau agiert. Die Beschaffungsvorgänge wurden durchgehend vom SAP-System abgebildet und unterstützt. Mit vielen Lieferanten bestanden bereits Rahmenverträge (Mengenkontrakte) mit Lieferabrufen. Auch dies war schon fester Bestandteil der SAP-Prozesse.
Als sehr leistungsfähig zeigte sich das von Hansgrohe entwickelte Liefernanteninfo-Tool “Lextra”. Hierbei handelt es sich um eine Internetplattform, auf der sich Lieferanten alle nötigen und ergänzenden Informationen abrufen können. Zu den Informationen gehören unter anderem die langfristige Bedarfsplanung der Materialien, Rahmenverträge und kurzfristige Lieferabrufe. Ohne Papier und ohne Faxe erhalten die Lieferanten auf diesem Wegen also ihre Aufträge.
Einige Lieferanten nutzen diese Informationsquelle auch zur automatischen Datenübernahme ihn ihr eigenes Warenwirtschaftssystem und können auf diesem Wege Zeit, Aufwand und Fehlerkosten sparen.
Im zweiten Schritt stand für die Einkaufsmaterialien des Werkes West (Schiltach) eine ABC/XYZ-Analyse auf dem Plan. Die dazu notwendigen Daten lieferten speziell entwickelte Reports aus dem SAP-System; sie wurden mit externen Tools ausgewertet. Der Betrachtungszeitraum betrug dabei zwölf Monate.
Die XYZ-Analyse wurde auf Wochenbasis durchgeführt. Während X- und Y-Artikel einen relativ gleichmäßigen Verbrauch in der Vergangenheit aufweisen, haben Z-Artikel einen unregelmäßigen bis sporadischen Lagerabgangscharakter. Zusätzlich wurden bei der XYZ-Analyse die Artikel besonders gekennzeichnet, die über mehr als ein halbes Jahr nicht nachgefragt wurden. Bei diesen Z2-Artikeln handelt es sich vornehmlich um neue oder auslaufende Einkaufsmaterialien, die dispositiv gesondert zu behandeln sind.
Die Ergenisse der ABC/XYZ-Analyse zeigen ein klassisches Bild: Während es gelingt, im AB/XY-Bereich die Bestände im Verhältnis zum Umsatz gering zu halten, sind die Bestände bei den sporadisch benötigten Artikeln (Z2-Artikel) sowie bei den geringwertigen C-Artikeln zu hoch, was durch einen geringen Lagerumschlag zum Ausdruck kommt. (Bild 1).
Die Reichweitenanalyse verdeutlicht die Arbeitsweise der Disponenten (Bild 2): Hochwertige A- und B-Teile werden geringer bevorratet und weisen kleinere Reichweiten auf, während man sich mit C-Teilen höher eindeckt und damit administrativen Aufwand einspart.
Simulation und Optimierung
Basierend auf diesen Erkenntnissen wurden im nächsten Schritt die Parameter für die Simulationsläufe mit dem Optimierungstool Diskover festgelegt¹.Bei den hochwertigen A-und B-Artikeln sollte nach Möglichkeit ein hoher Lagerumschlag erzielt werden. Dazu wurde eine Eindeckzeitraum von fünf Arbeitstagen gewählt, d.h. dass bei der Bestellmengenrechnung die Bedarf von fünf Arbeitstagen zusammengefasst werden.
Bei den geringwertigen C-Artikeln wurde ein Eindeckzeitraum von 20 Arbeitstagen gewählt, was sich nur gering auf die Bestände auswirkt, aber sowohl im Einkauf als auch in der Logistik den administrativen und physischen Aufwand in Grenzen halten sollte. Die sporadisch verbrauchten Z2Artikel wurden bei der Simulation ebenfalls berücksichtigt, allerdings sollten diese Artikel wegen des höheren Bestandsrisikos zukünftig auftragsbezogen beschafft werden. Alle Artikel wurden mit drei verschiedenen Lieferbereitschaftsgraden (90, 95 und 98 Prozent) simuliert, um zum einen die erzielbaren Lieferbereitschaftsgrade beurteilen zu können und zum anderen die Auswirkungen des Lieferbereitschaftsgrades auf die Bestände zu ermitteln (Bild 3). Die Simulationen wurden sowohl mit den in Diskover verfügbaren Prognoseverfahren durchgeführt als auch eingeschränkt nur mit den in SAP verfügbaren Verfahren, was einen Ausschluss der verteilungsfreien Verfahren bedeutete.
Die Ergebnisse der verschiedenen Simulationsläufe ergaben Bestandsreduzierungspotenziale von bis zu 47 Prozent. Dabei betrugen die Lieferbereitschaftsgrade der zukünftig lagerhaltigen Artikel zwischen 91 und knapp 96 Prozent. Die hohen Lieferbereitschaftsgrade konnten mit den verteilungsfreien Verfahren in Diskover erreicht werden, aber auch die SAP-Verfahren kamen zu zufrieden stellenden Ergebnissen.
Als zu favorisierende Variante entschied man sich daher für die SAP-Verfahren mit einem Soll-Lieferbereitschaftsgrad von 95 Prozent, was immer noch eine Bestandsreduzierung um ca. 34 Prozent bedeutete.
Im Anschluss an die Analysen und Simulationen ging das Team umgehend die Umsetzung der Ergebnisse an. Dazu wurden die Dispositionsverfahren für ausgewählte lagerhaltige Artikel im SAP-System auf prognosegestützte Bestellpunktverfahren umgestellt und die erforderlichen Planungsparameter, wie sie von Diskover kalkuliert wurden, eingegeben. Die Standardeinstellungen der Bestellpunktverfahren in SAP wurden im Customizing dahingehend modifiziert, dass das System die aktuellen Bedarfe bei der Beschaffungsrechnung ebenfalls berücksichtigt und sich nach Abzug dieser Bedarfe immer noch ein Bestandsniveau über dem Meldebestand ergibt.
Integration der Lieferanten
Durch die Umstellung deckt sich die Hansgrohe AG nicht mehr so hoch mit Material ein. Mit der Reduzierung der Mindestbestellmengen und Wiederbeschaffungszeiten, die der Einkauf mit den Lieferanten neu vereinbaren konnte, nimmt die Zahl der Lieferabrufe gegenüber der Vergangenheit zu.
Um die betreffenden Lieferanten auf diese Änderungen vorzubereiten, lud das Projektteam sie zu einem Informationsworkshop ein, bei dem die Vorgehensweise im Projekt Logistics 2010 näher erläutert und die Auswirkungen auf das zukünftige Abrufverhalten dargestellt wurden. Jeder Lieferant erhielt eine Aufstellung seiner Artikel mit Angabe der geänderten Einstellungen. Die Lieferanten bestätigten nochmals die in den Rahmenverträgen vereinbarten Lieferfristen und Lieferflexibilitäten, da diese Einstellungen gerade durch die zukünftig geringere Vorratsdecke für Hansgrohe weiter an Bedeutung gewinnen wird und für eine erfolgreiche Umsetzung unabdingbar sind.
Die Reaktion der Lieferanten war durchweg positiv. Ihre Einbindung in die Projektarbeit bei Hansgrohe bot die Möglichkeit, Einfluss auf die zukünftigen Prozesse zu nehmen, und gab das deutliche Signal zur langfristigen Zusammenarbeit. Viele Anregungen konnten in die Ergebnisse der Projektarbeit ein fließen und trugen zum Gesamterfolg bei.
Der Abschluss des Lieferantentermins beinhaltete einen Ausblick auf zukünftige unternehmensübergreifende Materialflusskonzepte, der unter anderem eine Anbindung der Lieferanten über Kanban vorsah. Diese Kanban-Anbindung machte sich das Projektteam als nächsten Schritt zur weiteren Optimierung auch im Sinne einer Reduzierung der internen Administration zur Aufgabe.
Der Erfolg der Umstellungen zeigte sich innerhalb kurzer Zeit. Binnen zehn Wochen ging der Bestand der Pilotartikel bereits uni über 50 Prozent zurück, sodass man schon fast die simulierten Zielbestände erreicht hatte (Bild 4). Der Gesamtbestand reduzierte sich nach weiteren Umstellungen innerhalb kurzer Zeit um über 15 Prozent.
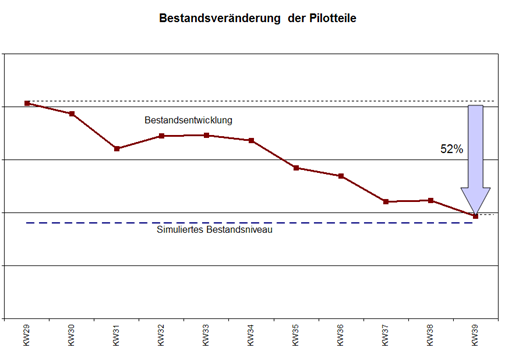
Mit diesen positiven Ergebnissen wird nun die materialflusstechnische Lieferantenintegration weiter vorangetrieben mit dem Ziel, die Bestände weiter zu optimieren und den administrativen Aufwand in Logistik und Einkauf erheblich zu reduzieren.
INFORMATION
Die Hansgrohe AG mit Sitz in Schiltach/Schwarzwald beschäftigt weltweit mehr als 2800 Mitarbeiterinnen und Mitarbeiter, davon ein Drittel im Ausland. Das Unternehmen, das sich in seiner 104-jährigen Geschichte innerhalb der Branche den Ruf als Innovationsführer in Technologie und Design erworben hat, erwirtschaftete 2004 mit seinen Marken Axor, Hansgrohe, Pharo und Pontos einen Umsatz von 428 Mio. Euro (2003: 369 Mio. Euro) -im Vergleich zum Vorjahr ein Plus von 16 Prozent. Die Hansgrohe AG produziert in fünf deutschen Werken, in Frankreich, in den Niederlanden, in den USA und in China. www.hansgrohe.com
Folgende Beratungsunternehmen sind bei dem Projekt beteiligt: Abels & Kemmner Gesellschaft für Unternehmensberatung mbH: Spezialist im Bereich Supply Chain Optimierung, Lieferantenintegration, -kanban und Bestandsmanagement.
ak-online.de
Die Leonardo Group GmbH: Spezialist für Supply Chain Management mit Schwerpunkt auf Lean Production, Kanban und Flexible Fabrik.
www.leonardo-group.com