Constraint-Analysen bei GETRAG FORD Transmissions
Von Georg Ingenbleek1 und Andreas Gillessen
Gesteuert oder nicht – Engpässe (Constraints) determinieren die Leistung jedes Systems. Erst recht, wenn es unter Vollast fährt. Abels & Kemmner identifizierte in einem Projekt die Engpässe bei GETRAG FORD Transmissions, um Fehlinvestitionen bei der Expansion zu vermeiden.
Bei Vollauslastung ist die Produktionsleistung eines Produktionssystems nicht “mal eben so” steigerbar. Nur mit zusätzlichen, teuren Schichten an Samstagen kann zur Zeit die im Dreischichtbetrieb fahrende GETRAG FORD Transmissions, Köln, die nachhaltig gestiegene Marktnachfrage bedienen. Das soll nicht auf ewig so bleiben. Bevor Erweiterungsinvestitionen in Planung gehen, wurde Abels & Kemmner mit der Durchführung einer Engpass-Analyse beauftragt. Diese sollte vorab alle die Produktionsleistung begrenzenden Einflussfaktoren systematisch identifizieren, ihre Wirkzusammenhänge offen legen und Potenziale zur Optimierung quantifizieren, um die Kapazitäten und Kostenrelationen weiter zu optimieren. Die effizienteste Methode, Engpässe und Begrenzungen (Constraints) eines Systems zu identifizieren, ist die Constraint-Analyse. Die Constraint-Analyse ist ein Werkzeug um wirtschaftliches Handeln effizient zu steuern. Ihre Vielseitigkeit erlaubt die Anwendung von der strategischen Unternehmensplanung bis hin zu operativen Entscheidungsfindungen. Erster Ausgangspunkt bei jeder Constraint-Analyse ist dabei die Bestimmung des zu betrachtenden Systems.
Bei GETRAG FORD Transmissions wurde hierfür die Fertigung der Getriebeeinzelteile (Wellen und Räder) gewählt. Zweiter Ausgangspunkt der Constraint-Analyse ist die Annahme, dass wirtschaftliche Systeme nur erfolgreich sind, wenn sie wachsen. Deshalb konzentriert sich die Systemanalyse immer auf die Grenzen des betrachteten Systems. Für GETRAG FORD Transmissions bedeutete dies die Identifizierung aller Engpässe im betrachteten Produktionssystem, seien sie durch Produkte, Prozesse oder Ressourcen sowie ihre Wechselwirkungen verursacht. Hierbei wurden nicht nur physische Constraints (Mitarbeiter, Ausrüstung, Anlagen etc.) betrachtet, sondern auch Grenzen wie Qualifikationsniveau, Denken in Gesamtzusammenhängen, IT-Systeme, Instandhaltung, Lieferanten etc. Anhand dieser beiden Ausgangspunkte “Systemdefinition” und “Betrachtung der Grenzen des Systems” machten sich die Berater von Abels & Kemmner zusammen mit einem Projektteam von GETRAG FORD Transmissions an die Arbeit. Binnen kurzer Zeit war der komplexe Fertigungsprozess in all seinen Segmenten und Facetten beschrieben und die wichtigsten Engpässe definiert. Innerhalb der Projektphase kristallisierten sich auch schon die ersten Verbesserungspotenziale heraus. Letztlich zeigte das Projekt, dass in nicht unerheblichem Umfange die gestiegene Marktnachfrage durch Auflösung und Verringerung bestehender Produktionsengpässe befriedigt werden kann. Einige Engpässe konnten dabei durch wenige Umstellungen bereits beseitigt werden. Jetzt arbeiten GETRAG FORD Transmissions und Abels & Kemmner an der weiteren Auflösung der bestehenden Constraints.
Realitätsbaum und identifizierte Handlungsfelder
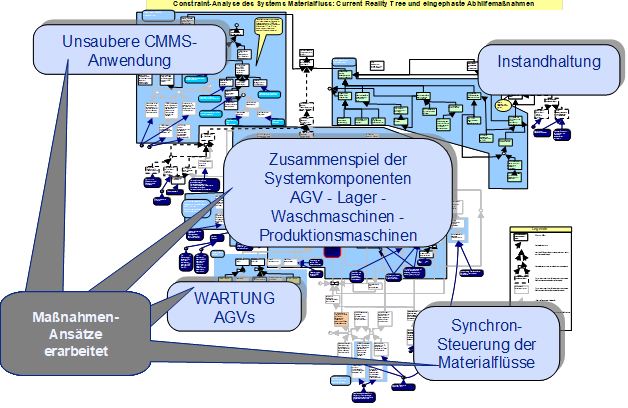
Die Grundannahmen der Constraint-Analyse:
- Jedes System nimmt den ihm nur durch Randbedingungen begrenzten Platz vollständig ein.
- Ein System kann nur wachsen, indem man seine einengenden Randbedingungen beseitigt.
- Wenn eine Randbedingung wegfällt, expandiert das System solange, bis es an eine neue Grenze stößt.
- Unmittelbar auf die Engpässe (Constraints) konzentriert, ist der aus fünf Schritten bestehende Grundprozess der Constraint-Analyse:
- Identifizierung des Engpasses – physisch oder organisatorisch
- Engpass maximal nutzen
- Alles auf den Engpass ausrichten – Synchronisation aller Elemente auf den Engpass
- Engpass verbreitern / Engpassressource erhöhen – Abstellung begrenzender Faktoren
- Den nächsten Engpass identifizieren: Wieder mit Schritt 1 beginnen
Aufbau eines „Realitäts-Baumes“ für die Produktion von GETRAG FORD Transmissions:
Das Ziel der Constraint-Analyse bei GETRAG FORD Transmissions war die Identifikation der Wirkungs-Zusammenhänge zwischen den verschiedenen Effekten, die zur Limitierung des Produktionsdurchsatzes beitragen sowie die Identifikation der notwendigen Abhilfeansätze und deren Priorisierung. Die Vorgehensweise erfolgte gemäß den oben angegebenen Schritten:
1. Was muss geändert werden? Identifizierung der Engpässe Als erster Projektschritt wurde ein “Realitäts-Baum” aufgebaut, der den derzeitigen Ablauf der Prozesse sowie den Zustand der Produktion abbildete. Dazu wurden u. a. Stammdaten analysiert, Mitarbeiter und Führungskräfte interviewt, statistische Bewegungsdaten ausgewertet etc. Aus den Ergebnissen ließen sich die Engpässe und systembegrenzenden Faktoren bereits ableiten (Abb.1):
- Synchronsteuerung der Materialflüsse nicht ausreichend – dies ist der zentrale Ansatzpunkt zur Gesamtsystemverbesserung, d. h. zur Verbesserung des Zusammenspiels der Systemkomponenten, zur Bestandsreduzierung und zur Durchsatzverbesserung.
- Zusammenspiel der Systemressourcen – AGV-Transportsystem, Lager, Wasch- und Produktionsmaschinen – nicht synchronisiert. Dieses Themenfeld besteht aus einem Bündel von Einzelmaßnahmen, die nach und nach umgesetzt werden müssen. Zum Teil erfolgte die Realisierung bereits während der Constraint-Analyse.
- MRP1-System (CMMS) und Produktionsanforderungen nicht sauber abgestimmt – Diese Maßnahmen werden erst einen Effekt auf die Leistung der Produktion haben, wenn der Komplex “Synchronsteuerung der Materialflüsse” als Engpass eliminiert wurde.
- etc.
2. Wie sollen die Veränderungen nun aussehen? Engpass maximal nutzen – Alles auf den Engpass ausrichten – Engpass verbreitern
1. Neben der systematischen Aufarbeitung aller systembegrenzenden Faktoren und der Generierung und Überprüfung geeigneter Lösungen ergaben sich im Projekt sogenannte “Sofortmaßnahmen”, die während des Projektes bereits umgesetzt wurden und direkt engpassentlastende Effekte hervorriefen. Dies waren Maßnahmen wie z. B.:
- Engpassbezogene Personalbedarfsplanung: Bei Personalmangel immer zuerst Engpassarbeitsplätze bereichsübergreifend besetzen
- Vor- und Nach-Operationen direkt per Transport-AGV oder manuell verbinden, sofern die höhere Kapazität nicht anderweitig genutzt wird
- Umprogrammierung AGV-Transportsteuerung:
- Falls keine Voroperationen aktiv à Teile direkt aus Lager abrufen
- Falls keine Nachoperation auf den Teiletyp eingestellt ist à Teile direkt ins Lager fahren
2. Die erarbeiteten Maßnahmen zur Überwindung der drei identifizierten Hauptengpässe bei GETRAG FORD Transmissions sind:
- Fehlende Synchronsteuerung der Materialflüsse – die heutige Produktionssteuerung erfolgt im Push-System. Um eine verbrauchs-/ bedarfsgesteuerte Synchronisation der Materialflüsse zu erreichen, wird die Produktionssteuerung in den nächsten Monaten auf ein Pull-System umgestellt. Zu diesem Thema wurde bereits ein eigenes Projekt initiiert, bei dem Abels & Kemmner beratend zur Seite steht.
- Zusammenspiel der Systemressourcen – zu diesem Thema wurde ein ganzes Maßnahmenbündel definiert, von dem nur einige hier kurz erwähnt werden sollen: Wasch-Aufwand verringern durch Lagerung der Öl- und Emulsionsteile auf unteren Lagerebenen; Einlagerungsvolumen verringern indem Zunderteile vor Ort gelagert werden; Ressourcenverfügbarkeit sicherstellen durch Neubestellung von Transportkörben; Reaktionszeit zwischen Operationen verkürzen durch gezielte Verlängerung oder Verdoppelung der Auslaufpuffer; AGV-Bedarf verringern; (siehe Abb. 2).
- MRP1-System und Produktionsanforderungen nicht abgestimmt – aufgrund mangelnder Erweiterungsmöglichkeiten des bestehenden CMMS-Systems wird ein neues Produktionssteuerungssystem zur Realisierung einer Pullsteuerung mit Schnittstelle zum CMMS-System geschaffen. Dieses wird einfach, benutzerfreundlich, durch die Produktionsplanung selbst parametrierbar sein, damit kein oder nur geringer IT-Support notwendig wird.
3. Nach Beseitigung der identifizierten Engpässe wird ein erneuter Durchlauf erfolgen, mit dem Ziel die dann neu auftretenden Engpässe zu ermitteln und wieder geeignete Maßnahmen zu deren Beseitigung zu generieren, zu testen, und umzusetzen um die Leistung des Produktionssystems weiter zu steigern.
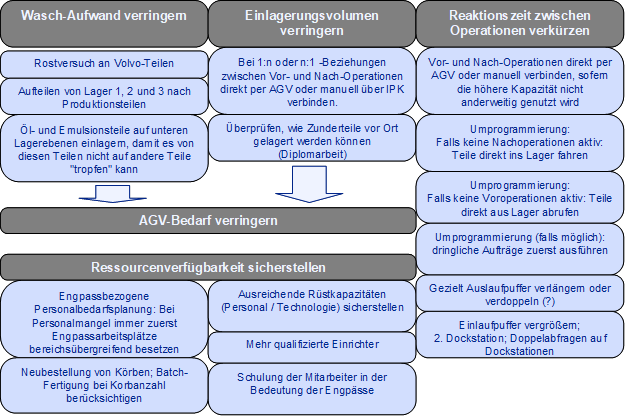
Constraint Management
In jedem Prozess begrenzen nur einige wenige Variablen (möglicherweise nur eine) die Leistung des Systems. Um Systembegrenzungen sichtbar zu machen, kann der Produktionsprozess mit einer Kette verglichen werden, bei dem das schwächste Glied die Grenze für die Leistungsfähigkeit des Gesamtsystems repräsentiert.
Bei GETRAG FORD Transmissions wurde folgendes Problem gelöst: Die Produktion bemüht sich ständig die vom Markt geforderten Liefertermine und damit die Lieferbereitschaft sicherzustellen. Der offensichtliche Konflikt, dem die Produktionsleitung ausgesetzt ist, resultiert aus dem Versuch den notwendigen Durchsatz sicherzustellen (was oft bedeutet, Rüstwechsel vorzunehmen, die die Bereichs-Effizienz reduziert) und die Kosten unter Kontrolle zu halten (was normalerweise bedeutet, in hohen Losgrößen in Teilbereichen der Fertigung zu produzieren). Die Effizienzsteigerung lokaler Produktionsbereiche führt gemäß Constraint Management jedoch nicht zur Optimierung des Gesamtsystems. Das Ergebnis bereichsbezogener Effizienzsteigerungen führt normalerweise einfach nur zu einer Erhöhung des work-in-process oder des Fertigmaterials, ohne das der Absatz gesteigert oder die Kosten reduziert werden konnten. Tatsächlich steigen sogar dadurch die Gesamtkosten für das Unternehmen.
Constraint Management versucht die Leistung der Gesamtproduktion zu maximieren statt die jedes einzelnen Bereichs oder jeder Ressource. Hierzu werden die Leistungen der Engpass-Ressourcen maximiert. Engpass-Ressourcen werden auch als “Trommeln” bezeichnet, zu deren Takt die anderen Operationen produzieren. Über Zeit- / Materialpuffer wird ein Abreißen der Produktion / eine Reduzierung der Produktionsleistung an den Engpass-Ressourcen durch Störungen verhindert.
Der Ansatz erscheint sehr einfach. Die vollständige Umsetzung in die Praxis ist für die meisten Organisationen jedoch mit großen Schwierigkeiten verbunden. Produktionsleitung, Meister und Mitarbeiter arbeiten seit jeher nach der Devise “never run out of work”. Kein Material und damit Arbeit an der Maschine zu haben heißt, die Maschine stillstehen zu lassen und wird als große Verschwendung und als nahezu undenkbar angesehen. Wenn das System jedoch richtig arbeitet, können und sollen Ressourcen auch stillstehen bzw. keinen Materialvorrat mehr vor der Maschine haben.
Fazit
Eine Organisation ist ein kompliziertes Netz aus Menschen, Maschinen, Material, Methoden und Massen. Wird noch Detailkomplexität und Dynamik hinzugefügt, die durch Veränderungen bei Kunden, Lieferanten, Mitarbeiter, Regulierungen etc. verursacht werden, ergibt sich ein komplexes Bild der Herausforderungen, dem sich das heutige Management gegenübersieht. In der Vergangenheit wurden Organisationen in kleine, besser zu steuernde Einheiten gesplittet mit dem Ziel die Leistung jeder Einheit zu maximieren. Die Summe der maximalen Leistungen jeder einzelnen Einheit führt aber nicht zur maximalen Leistung des Gesamtsystems. Dieser Konflikt wurde bei GETRAG FORD Transmissions durch gezielte Constraint-Beseitigungen weitestgehend aufgelöst.
Über GETRAG FORD Transmissions
GETRAG FORD Transmissions ist ein 50% – 50% Joint Venture zwischen dem Getriebespezialisten GETRAG und dem Automobilkonzern Ford im Bereich manueller Getriebe. Die Kernkompetenz liegt in der ganzheitlichen Getriebeentwicklung von Schalt- und Automatikgetrieben. Dieses Spektrum umfasst:
Konzeption – Entwicklung – Prototypen – Erprobung – Serieneinsatz
Das international agierende Unternehmen ist an den Standorten Köln, Bordeaux, Halewood und Göteborg vertreten. GETRAG FORD Transmissions ist Teil der GETRAG Corporate Group.
Am 1. Februar 2001 wurde GETRAG FORD Transmissions gegründet als Gemeinschaftsunternehmen des Getriebespezialisten GETRAG mit Sitz in Untergruppenbach (Baden-Württemberg) und des Automobilkonzerns Ford.
Das Ziel des Joint Ventures ist es, die Stärken beider Partner im Bereich manueller und automatisierter Schaltgetriebe miteinander zu verbinden. Die Muttergesellschaften stellten qualifizierte Mitarbeiter, ein hochmodernes Entwicklungszentrum, die Produktionsstätten sowie das entsprechende Know-how und Kapital als Voraussetzung für eine positive Geschäftsentwicklung zur Verfügung.
Seit der Gründung konnten einige Neukunden hinzugewonnen werden, so z.B. Mazda und Volvo
WWW.GETRAG-FORD.DE
1 Dipl.-Ing. Georg Ingenbleek ist Fertigungsbereichsleiter Wellen und Ring Gear – MTX / VXT / M5X / M6X des Werkes Köln der GETRAG FORD Transmissions