Marktsynchrone Produktion in der Uhrenindustrie
Von Gervaise Voisard, Olaf Rellecke und Götz-Andreas Kemmner
Synchron mit den Marktbedarfen zu produzieren und zu beschaffen ist heute in Produktionsunternehmen übliche Praxis. Wie aber baut man marktsynchrone Prozessketten auf, wenn beschaffungsseitig sehr lange Lieferzeiten bestehen? In einem Projekt beim Schweizer Uhrenproduzenten Montblanc-Montre S.A. wurden im Durchschnitt 19 Prozent der Bestände reduziert – trotz langer Lieferzeiten.
Die Montblanc-Montre S.A. aus dem Uhrenmekka Le Locle im Schweizer Jura ist ein Tochterunternehmen der Montblanc-Gruppe in Hamburg und gehört zum Schweizer Luxusgüterkonzern Richemont in Genf. MontblancMontre fertigt hochwertige Uhren der Marke Montblanc, die in den Montblanc-Boutiquen und über ausgewählte Händler weltweit angeboten werden. Gegründet 1997 hat das Unternehmen in den letzten Jahren ein rasantes Wachstum durchlaufen und produziert inzwischen über 100 000 klassische mechanische Uhren im Jahr (Bild 1).
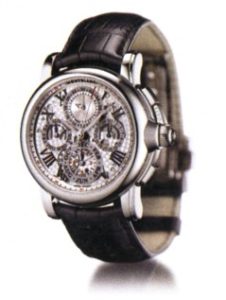
Die Uhrenindustrie – eine besondere Branche
Die Uhrenindustrie weist einen hohen Anteil an Zukaufteilen auf, die von spezialisierten mittelständischen Zulieferunternehmen produziert werden. Nicht nur Uhrwerk-Komponenten, auch Ziffernblätter, Gehäuse oder Zeiger sind hochkomplexe feinmechanische Teile, die in vielen aufwändigen Produktionsschritten, häufig aus speziellen Metalllegierungen und ausgefallenen Sondermaterialien hergestellt werden. Lieferzeiten von drei Monaten gelten hierbei bereits als schnell, und es ist nicht ungewöhnlich, dass von der Bestellung beim Lieferanten bis zur Auslieferung der Teile neun bis über zwölf Monate vergehen.
Hohe Qualitätsanforderungen an die beschafften Komponenten und sorgfältige Qualitätsprüfungen führen weiterhin dazu, dass ein deutlicher, aber schwankender Anteil der Liefermengen vom Qualitätsmanagement zurückgewiesen werden und damit nicht zu dringend benötigten Uhren verbaut werden können.
Weiterhin charakteristisch für die Uhrenbranche ist der hohe jährliche Anteil an Produktneuheiten, der typischerweise 25 bis 35 Prozent einer Uhrenkollektion ausmacht.
All dies sind Randbedingungen, die zu hohen Fertigwarenbeständen führen und trotzdem die Lieferfähigkeit von Fertiguhren negativ beeinflussen. Eine Ausgangssituation, in der man üblicherweise nicht über eine marktsynchrone Wertschöpfungskette diskutiert.
Voraussetzung: Bedarfsprognose
Wenn die Teile, die das Unternehmen heute verbauen muss, bereits vor einem halben Jahr bestellt werden mussten, geht ohne eine sorgfältige Absatzprognose nichts, egal ob man marktsynchron produzieren will oder nicht.
Als Tochterunternehmen von Montblanc in Hamburg setzt Montblanc-Montre ebenfalls SAP ein und ist in den weltweiten Absatzplanungsprozess der Montblanc-Gruppe eingebunden, der bereits vor einigen Jahren gemeinsam mit dem Beratungshaus Abels & Kemmner konzipiert und umgesetzt wurde.
Damit lag eine notwendige, wenn auch nicht hinreichende Bedingung vor, um überhaupt über eine marktsynchrone Produktion nachzudenken. Doch eine noch so gute Absatzplanung kann es nicht vollends vermeiden, dass der tatsächliche Marktbedarf von der Prognose abweicht, Lieferungen verzögert eintreffen oder Teillieferungen der geforderten Qualität nicht gerecht werden. Letztlich sind regelmäßig nicht alle Komponenten verfügbar, die gerade für einen Fertigungsbedarf benötigt werden, oder sie wurden in die falschen Fertiguhren verbaut, die gegenwärtig nicht nachgefragt werden und somit den Lagerbestand erhöhen und die Lieferfähigkeit verschlechtern.
Grundprinzip: Zweistufige Regelkreise
Um diese Situation grundlegend und nachhaltig zu verbessern, wurde von Abels & Kemmner gemeinsam mit einem Projektteam von Montblanc-Montre und Montblanc-Simplo in Hamburg ein sogenanntes „Postponed Manufacturing Concept” (postponed = aufgeschoben) mit zweistufigem Regelkreis entwickelt, dessen betriebsinterne Stufen inzwischen umgesetzt sind. Die Lieferanteneinbindung folgt in weiteren Stufen.
Alleine durch die internen Umstrukturierungen konnten die Bestände trotz gegebener Problematik um durchschnittlich 19 Prozent gesenkt werden.
Der gesamte Herstellungsprozess wurde in zwei Nachbevorratungsregelkreise aufgeteilt (Bild 2): Das Fertigwarenlager wird nun über eine Justin-time-Endmontage mit den Fertiguhren beliefert. Diese Endmontage greift auf vormontierte Uhren zurück, an denen lediglich noch die Armbänder angebracht werden.
Da sich eine große Zahl an Fertiguhren nur durch die unterschiedlichen Leder-, Textilund Metallarmbänder unterscheidet, konnte auf diese Weise die Variantenbildung wertstromabwärts in Richtung Kundendelta gelegt werden, wodurch deutlich geringere Bestände an Fertiguhren im Fertigwarenlager bevorratet werden müssen.
Der Idealzustand wäre, die Montage sogar direkt an den Point-of-Sale zu verlagern. Eine Reihe von Qualitätsrestriktionen verbieten es gegenwärtig jedoch noch, auf diesen Montageschritt zu verzichten.
Ausgehend von der Positionierung der Fertiguhren in einen ABC/XYZ-Portfolio* wurden Kriterien definiert, welche Uhren überhaupt auf dem Fertigwarenlager bereitgehalten und welche Uhren bei Bedarf kurzfristig über die JIT-Endmontage nachproduziert werden.
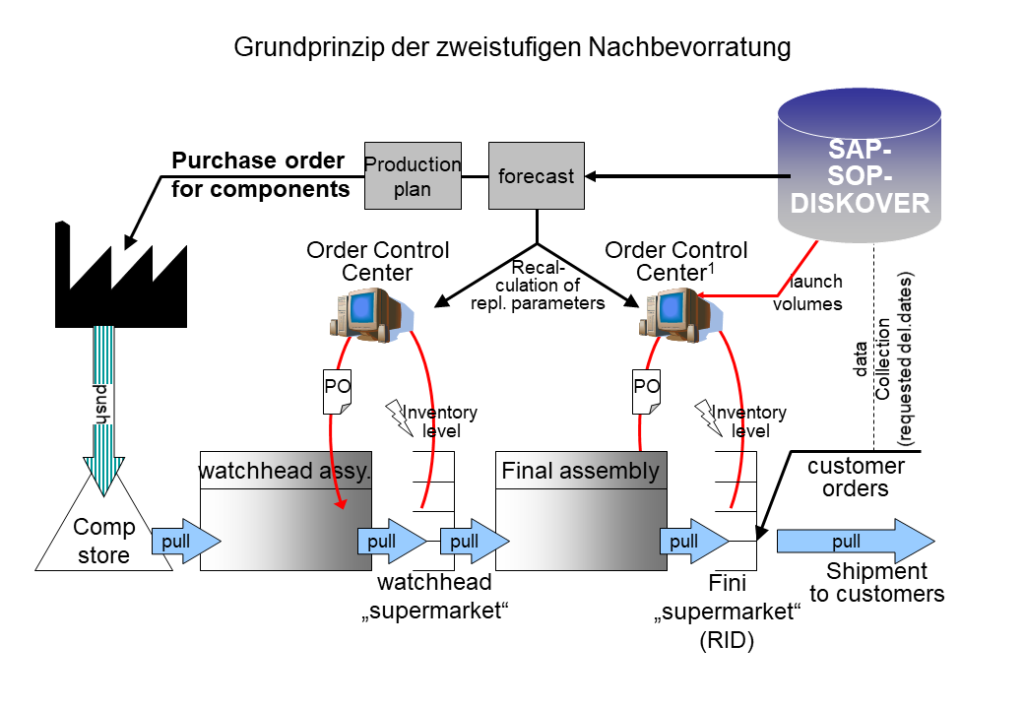
Statt klassischem Kanban: Order Control Center
Von vornherein war klar, dass ein klassisches Kanban-System zur Steuerung der beiden Nachbevorratungsregelkreise nicht in Frage kam. Ein klassisches Kanban-System setzt voraus, dass die Komponenten in den Supermärkten, aus denen sich ein Regelkreis bedient – zumindest größtenteils – vorhanden sind. Vor der Durchführung eines anstehenden Kanbans müsste geprüft werden, ob die benötigten Komponenten in dem Supermarkt in ausreichender Anzahl vorhanden sind.
Fehlt eine Komponente komplett, kann der Auftrag nicht begonnen werden. Fehlt eine Teilmenge einer oder mehrerer Komponenten, kann nur eine Teilmenge des SammelKanbans erfüllt werden. Sofern die unterdeckten Komponenten in mehrere anstehende Sammel-Kanbans eingehen, muss eine Entscheidung über die Priorität der Komponenten-Allokation getroffen werden. Ein klassisches KanbanSystem ist mit einer solchen Situation komplett überfordert.
Um dieses Problem elegant und rationell in den Griff zu bekommen, wurde eine ABAP-Programmierung (Advanced Business Application Programming; Programmiersprache für SAP) am vorhandenen SAP-System vorgenommen.
Das neue SAP-Modul „Order Control Center (OCC)” (Bild 3) hilft heute bei der Steuerung der Nachbevorratungsregelkreise. Die Regelkreise selbst werden durch ein zweites SAP-ABAP, das „Replenishment Parameter Calculation (RPC)-Modul” monatlich nachdimensioniert.
Was in den beiden Nachbevorratungsregelkreisen zu produzieren ist, wird über Meldebestände in den Supermärkten gesteuert, die von den beiden Regelkreisen beliefert werden.
Auf der zentralen Steuerungsmaske des OCC sind alle anstehenden Fertigungsbedarfe für Uhrenköpfe wie für Fertiguhren aufgeführt und nach verschiedenen festgelegten Prioritätskriterien sortiert. Diese Auftragsreihenfolge kann jedoch vom Disponenten übersteuert werden.
Für jeden anstehenden Auftrag weist das OCC aus, welche Menge produziert werden müsste und welche Menge produziert werden kann. Bei der Ermittlung der zu produzierenden Menge eines Teiles berücksichtigt das OCC nicht nur die Unterschreitung eines Meldebestandes, sondern berücksichtigt auch anstehende Kundenaufträge, die über die Nachbevorratungsmenge der Meldebestandssteuerung hinausgehen.
Bei neuen Produkten gibt das OCC genau die vom Marketing als Systemfüllung definierte Erstfertigungsmenge vor. Die tatsächliche Fertigungslosgröße, die gefertigt werden kann, hängt von der am geringsten verfügbaren Komponente ab. Das OCC weist die verfügbaren Komponentenbestände in der Reihenfolge der Auftragsprioritäten den anstehenden Nachbevorratungsaufträgen zu.
Auf diese Weise wird sichergestellt, dass die „wichtigsten” Aufträge zuerst mit benötigten Komponenten versorgt werden. Auch diese Mengenallokation kann vom Bediener übersteuert werden, der auf diese Weise weitere, dem System nicht bekannte Informationen in die Komponentenzuordnung einfließen lassen kann. Die Konsequenzen einer veränderten Zuordnung von Komponentenmengen erhält der Bediener direkt im Dialog angezeigt.
Aus der zentralen Maske des OCC heraus kann der Disponent direkt in die Umsetzung der Bedarfsanforderung (BANF) in einen Fertigungsauftrag oder eine externe Bestellung springen. Die beiden Alternativen sind deswegen notwendig, weil ein Teil der Uhren (ohne Armbänder) von einem externen Lohnfertiger produziert wird. Auf diese Weise wird die Fertigungskapazität der starken Saisonalität angepasst, und es kann auf eine umfangreiche Vorproduktion während der schwachen Saisonzeiten verzichtet werden.
Erst mit dem durch den Bediener angestoßenen automatischen Generieren einer BANF und deren folgender Umsetzung werden Komponentenbestände definitiv den Fertigungsaufträgen zugeordnet. Das OCC nimmt keine Materialreservierungen in die Zukunft vor. Auf diese Weise wird sichergestellt, dass das OCC bei jedem Start die aktuelle Bedarfssituation mit der aktuellen Angebotssituation an Komponenten vergleicht.
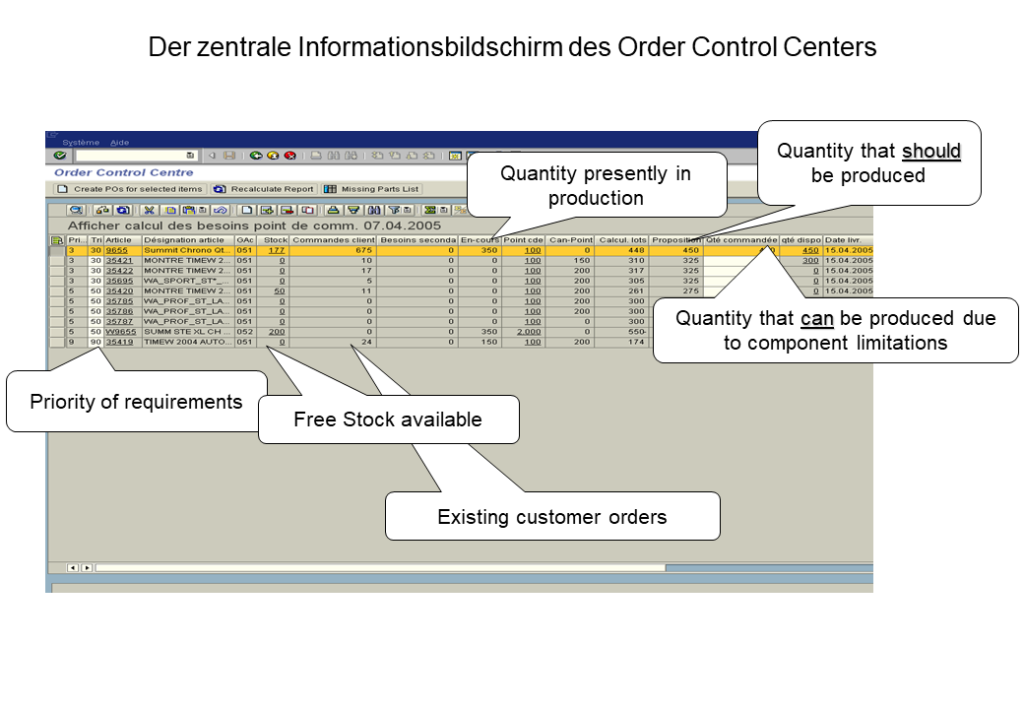
Modul dimensioniert die Regelkreise monatlich
Die saisonal starken Schwankungen in der Marktnachfrage machen es erforderlich, die Meldebestände der Nachbevorratungsregelkreise monatlich artikelspezifisch nachzudimensionieren. Diese Aufgabe erledigt ein zweiter, RPCModul (replenishment parameter calculation) genannter ABAP. Das RPC-Modul greift die im Rahmen der Absatzplanung ermittelten Bedarfsprognosen für die einzelnen Fertiguhren ab und berechnet hieraus vier Steuerungsparameter für jede Fertiguhr: eine Soll-Fertigungslosgröße sowie einen Muss-, Kann- und MaxPunkt.
Der Max-Punkt gibt den maximalen Bestand wieder, bis zu dem der Lagerbestand höchsten aufgefüllt werden darf. Unter dem Muss-Bestand ist der Bestand zu verstehen, bei dem spätestens nachproduziert werden muss. Dieser Muss-Bestand entspricht praktisch dem roten Bereich einer klassischen Ampel-Kanban-Steuerung. So wie man im Ampel-Kanban einen gelben Bereich kennt, bei dessen Erreichen nachgefertigt werden darf, aber nicht nachgefertigt werden muss, berechnet das RPC-Modul einen Kann-Bestand mit derselben Bedeutung.
Hat das OCC alle Fertigungsbedarfe, die durch das Unterschreiten des Muss-Punkts ausgelöst worden sind, rechnerisch mit Komponenten versorgt, so teilt es die weiteren verfügbaren Komponentenbestände den Kann-Fertigungsbedarfen zu.
Ein Fünftel weniger Fertigwarenbestände – das ist erst der Anfang
Das zweistufige Replenishment-Konzept, gesteuert durch das Order Control Center (OCC) und die Replenishment-Parameter-Berechnung (RPC), haben den Steuerungsaufwand im Unternehmen deutlich verringert.
Um die Bestandsentwicklung zu erkennen, muss man einerseits den früheren Fertigwarenbeständen die heutigen Bestände an Fertiguhren sowie an Uhren (ohne Armbänder) gegenüberstellen. Aufgrund der starken Saisonalität ist es darüber hinaus erforderlich, gleitende 12-Monats-Durchschnittsbestände zu vergleichen. Nach einem Jahr im operativen Betrieb ergibt sich hieraus eine Bestandsreduzierung um 19 Prozent.
Konzepte, wie zukünftig Lieferzeiten verkürzt und die Lieferanten in das ziehende System eingebunden werden können, liegen vor und sollen nun in der nächsten Projektstufe umgesetzt werden.