Götz-Andreas Kemmner
Die Produktion wird immer ein im Detail nicht planbarer Prozess bleiben. Das bedeutet jedoch nicht, dass man Durchlaufzeiten, Bestände, Termintreue und Kapazitätsauslastung in der Produktion nicht beherrschen kann.
Aufgabe der Produktions- beziehungsweise Fertigungsplanung und -steuerung ist es, den Material-, Auftragsfluss durch die Produktion möglichst optimal zu regeln. Die Zielgrössen sind allen klar: Kurze Durchlaufzeiten, hohe Termintreue, geringe Umlaufbestände und gute Ausnutzung der Produktionskapazitäten. Jeder, der schon einmal in der Fertigungsplanung und -steuerung gearbeitet hat, kennt die Problematik:
Da freut man sich über eine höhere Kapazitätsauslastung aufgrund der Auftragssituation und schon steigen die Umlaufbestände, sinkt die Termintreue, und die Durchlaufzeit verlängert sich. Vor allem bei Einzel- und Kleinserienfertigern kommt am Ende der Montage auch noch weniger heraus, da ständig irgendwelche Teile zur Fertigstellung des Auftrages fehlen. In manchen Unternehmen, so hat man das Gefühl, entziehen sich diese Zielgrössen jeder Planung und Steuerung.
Dilemma der Ablaufplanung
Man spricht vom “Dilemma der Ablaufplanung”, obwohl es eigentlich mehr so etwas wie ein “Quadrolemma” darstellt. Stellen Sie sich vor, sie müssten drei Wasserbälle in der Badewanne unter Wasser drücken und gleichzeitig dafür sorgen, dass der Wasserspiegel nicht steigt… Damit die Aufgabe nicht zu einfach wird, dreht jemand ständig den Wasserhahn auf oder lässt Wasser ab und bläst Luft in die Wasserbälle oder lässt welche entweichen. Eine unlösbare Aufgabe, werden Sie sagen, doch genau diese Aufgabe stellen viele Unternehmen täglich kalt lächelnd ihren Fertigungssteuerern.
Die Produktion ist ein im Detail nicht planbarer Prozess. Die Tatsache, dass Durchlaufzeiten, Termintreue, Umlaufbestand und Kapazitätsauslastung folglich “nur” statistisch miteinander verbunden sind, begründet jedoch lediglich, warum man mittels Feinplanungssoftware und Leitstand-Funktionalität keine ordentliche Leistung erbringen kann, sie zeigt jedoch auch, dass man mit dem richtigen Werkzeug und der richtigen Methode eine ordentliche Leistung erbringen könnte!
Manche innovative Unternehmen versuchten und versuchen ihren Fertigungssteuerern zu helfen, indem sie ihnen Feinplanungs-Software und Leitstände zur Verfügung stellen. Jetzt wird teilweise stunden-, ja nächtelang gerechnet, um Fertigungsaufträge und Arbeitsvorgänge möglichst minutengenau optimiert einzuplanen. Schneller als die Ergebnisse dargestellt werden können, haben sich die Randbedingungen jedoch verändert. Die Systeme rennen einer Realität hinterher, die sich immer anders entwickelt, als die Berechnung dies erwartet. Präzise danebengeschossen geht eben auch am Ziel vorbei!
“Die Produktion ist ein im Detail nicht planbarer Prozess”, diese alte Wiendahlsche Feststellung ist genauso unverrückbar wie die Heisenbergsche Unschärferelation in der Quantenphysik. Während letztere aber allgemein akzeptiert ist, – obwohl sie keiner von uns in der Schule so genau verstanden hat -, leben zahlreiche Softwareprodukte und anwendende Unternehmen von der Hoffnung, die Wiendahlsche Unschärferelation in der Produktion überwinden zu können. Nur mit spezifischen, statistischen Ansätzen wird dies möglich, dessen sollten Sie sich bewusst sein!
“Gebt mir die richtigen Werkzeuge und ich steuere die Produktion richtig”
Beide vermeintlich grundverschiedenen Theoreme gründen auf einem gemeinsamen Mechanismus. Viele physikalische Grössen stehen in einem “unscharfen”, gemeint ist damit statistischen, Zusammenhang. Auch der Zusammenhang zwischen den Grössen Durchlaufzeit, Termintreue, Umlaufbestand und Kapazitätsauslastung in einer Produktion mit zahlreichen Fertigungsaufträgen, Arbeitsvorgängen und Kapazitätsstellen ist statistischer Natur. Eine Optimierung dieser Grössen kann deshalb auch nur mit statistischen Methoden erfolgen. Wenn Sie also als Fertigungssteuerer wegen einer schlecht gesteuerten Produktion kritisiert werden, empfehlen Sie Ihrem Gesprächspartner, sich zuerst einmal mit der Heisenbergschen Unschärferelation auseinander zu setzen.
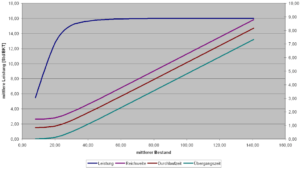
Heisenbergsche Unschärferelation
Die heisenbergsche Unschärferelation oder Unbestimmtheitsrelation ist die Aussage der Quantenphysik, dass jeweils zwei Messgrössen eines Teilchens (etwa ein Ort und Impuls) nicht gleichzeitig beliebig genau bestimmt sind. Sie ist nicht die Folge von Unzulänglichkeiten eines entsprechenden Messvorgangs, sondern prinzipieller Natur. Die Unschärferelation wurde 1927 von Werner Heisenberg im Rahmen der Quantenmechanik formuliert. Unter dem Begriff der Unschärfe ist mathematisch gesehen die sogenannte Standardabweichung gemeint. Der Begriff “Unbestimmtheitsrelation” beschreibt daher die Aussage besser, da es nicht um die Messung geht, sondern um die prinzipielle Unmöglichkeit (Quelle: Wikipedia.de).
Sie werden Ihren Gesprächspartner auf diese Weise wohl nicht dauerhaft los, schon gar nicht, wenn er Ihrer Empfehlung folgt und sich tatsächlich etwas genauer in die Materie einarbeitet. Sie haben jedoch Zeit gewonnen, um die Zusammenhänge genauer zu durchdringen, ehe er zurückkommt.
Die Tatsache, dass Durchlaufzeiten, Termintreue, Umlaufbestand und Kapazitätsauslastung “nur” statistisch miteinander verbunden sind, begründet lediglich, warum Sie mittels Feinplanungssoftware und Leitstand-Funktionalität keine ordentliche Leistung erbringen, sie zeigt jedoch auch, dass Sie mit dem richtigen Werkzeug und der richtigen Methode eine ordentliche Leistung erbringen könnten!
Aber, wie gesagt, Sie haben Zeit gewonnen und diese wollen wir nutzen; allerdings nicht, indem wir uns tief in die statistischen Zusammenhänge eingraben (dafür werden an den Universitäten genug Professoren beschäftigt), sondern indem wir direkt an das Ende der Überlegungen springen und uns mit den praktischen Erkenntnissen der statistischen Überlegungen beschäftigen.
Die dargestellte Grafik gibt eine Produktionskennlinie wieder, Techniker mag sie an Motorenkennlinien erinnern und so weit entfernt ist diese Analogie gar nicht. Eine solche Produktionskennlinie lässt sich für eine einzelne Kapazitätsstelle (Arbeitsplatz, Maschine), für eine Gruppe von Kapazitäten, für eine Produktionsabteilung oder auch die die gesamte Produktion erstellen. In der linken Kurve der Kennliniengrafik ist die Leistung über dem mittleren Bestand abgetragen. Unter dem mittleren Bestand versteht man den Arbeitsvorrat in Stunden, der durchschnittlich, über einen längeren Betrachtungszeitraum, vor der betrachteten Kapazitätsstelle liegt. Die Leistung beschreibt, wie viel Stunden Arbeitsinhalt pro Betriebskalendertag von der Kapazitätsstelle abgearbeitet werden. Deutlich zu erkennen ist, dass die Leitung zuerst proportional zum mittleren Bestand ansteigt. Die Leistungskurve wird dann zunehmend flacher. Wenn man im vorliegenden Beispiel soviel an Aufträgen vor die Maschinengruppe “schaufelt”, dass der mittlere Bestand von 300 auf 600 Stunden ansteigt, so gewinnt man damit noch sagenhafte zwei Stunden pro Betriebskalendertag an Leistung. Dummerweise hat man nicht nur einen Berg an Beständen angehäuft, sondern auch, wie die unteren drei parallelen Kurven zeigen, die Durchlaufzeit von ca. 1,5 auf ca. 3,5 Tage verlängert (an der rechten senkrechten Achse im Diagramm abzulesen). Kommen Ihnen solche Zusammenhänge bekannt vor?
Die Termintreu, statistisch besonders schwer zu greifen und in der Grafik deshalb gestrichelt eingetragen, war bei 300 Stunden Auftragsbestand schlecht und fällt bei 600 Stunden wieder auf einen ähnlich schlechten Wert zurück. Bei 300 Stunden Auftragsbestand war sie schlecht, weil noch eine ganze Reihe von Aufträgen zu früh fertig wurde; bei 600 Stunden ist sie schlecht, weil nun die meisten Aufträge zu spät fertig werden.
Ehe Ihr Gesprächspartner vom Studium der Heisenbergschen Unschärferelation zurückkommt, müssen wir aus der betrachteten Produktionskennlinie praktischen Nutzen ziehen: Jede Produktion, jede Kapazitätsgruppe, jede Kapazitätsstelle besitzt eine solche Produktionskennlinie. Die grundsätzlichen Kurvenformen sind immer dieselben; in ihren Zahlenwerten und ihrer Krümmung unterscheiden sie sich. Ohne, dass Sie durch organisatorische oder technische Massnahmen eingreifen, bleiben die Kurvenverläufe mittelfristig konstant, da können Sie drücken, schieben, zerren oder Termine jagen, wie Sie wollen. Durchlaufzeit, Bestand, Termintreue und Leistung (Kapazitätsauslastung) stehen eisern in den durch die Kurven beschriebenen statistischen Verhältnissen zueinander.
Erste Erkenntnis
Hieraus resultiert die erste wesentliche Erkenntnis: Wenn Sie die Produktion sinnvoll steuern wollen, dann dürfen Sie nicht täglich zwischen den verschiedenen Zielgrössen Durchlaufzeit, Bestand, Termintreue und Kapazitätsauslastung hin und her eiern, sondern müssen sich, abhängig von der aktuellen wirtschaftlichen und wettbewerblichen Situation richtig strategisch positionieren, indem Sie festlegen, welchen Kompromiss Sie zwischen den verschiedenen Zielwerten eingehen wollen. Sie meinen, Sie tun das schon? Und was ist mit dem Herunterknüppeln der Bestände am Ende des Monats und vor allem des Geschäftsjahres, während ansonsten die Kapazitäten möglichst gut genutzt werden sollen?
Zweite Erkenntnis
Die zweite wesentliche Erkenntnis lautet: Sie verändern Ihre logische Positionierung dadurch, dass Sie den mittleren Bestand an einem Arbeitssystem verändern. Das ist sozusagen Ihr Schieberegler, den Sie allerdings nur bis zu einem gewissen Grad genau bewegen können. Präzise bewegen können Sie diesen Regler nur an den ersten Arbeitsplätzen, an denen ein Fertigungsauftrag bearbeitet wird. Je mehr Arbeitsstationen ein Fertigungsauftrag durchläuft, desto mehr potenzielle Störungen wirken auf ihn ein und desto unsicherer wird es, zu welchem Zeitpunkt er an einem Arbeitssystem zur Bearbeitung anstehen und zum Bestand an diesem Arbeitssystem beitragen wird. Die tiefer in der Produktion liegenden Schieberegler bewegen Sie nicht direkt, sondern – schon wieder – nur über statistische Mechanismen.
“Die Produktion ist ein im Detail nicht planbarer Prozess.”
Durch das Verändern des mittleren Bestandes verschieben sich die anderen logistischen Grössen entlang der Kennlinien, entsprechend dem dargestellten Beispiel. Wenn Ihnen das Ergebnis nicht reicht, weil Sie bei dem angestrebten Bestand beispielsweise kürzere Durchlaufzeiten oder eine bessere Leistung erreichen wollen, müssen Sie durch technische und organisatorische Massnahmen eingreifen, indem Sie zum Beispiel:
- zeitliche Belastungsspitzen abbauen,
- Mindestübergangszeiten reduzieren,
- Auftragszeiten harmonisieren,
- Auftragszeiten reduzieren,
- die Kapazitätsflexibilität erhöhen oder
- eine überlappte Fertigung ermöglichen,
- eine parallele Fertigung ermöglichen.
Dritte Erkenntnis
Sie bewirken dadurch – und dass ist die dritte wichtige Erkenntnis – eine Veränderung der statistischen Zusammenhänge und verschieben somit die Kennlinie. Ihr Ziel haben Sie erreicht, wenn es Ihnen gelungen ist, die Kennlinien so zu verschieben, dass Sie durch den angestrebten Betriebspunkt verlaufen. Wenn Ihnen dies nicht gelingt, werden Sie Ihren Betriebspunkt auch nicht erreichen.
Warum nicht in der Praxis?
Jetzt wissen Sie schon eine ganze Menge, um Ihren Kritikern Paroli bieten zu können. Ihr Chef dürfte von Ihren neuen Kenntnissen beeindruckt sein. Vermutlich wird er Sie jetzt fragen, warum Sie Ihre Erkenntnisse nicht in die Praxis umsetzen. Aber auch hier müssen Sie keine Antwort schuldig bleiben:
Selbstverständlich könnten Sie sich durch einige Kilo statistischer Formeln wühlen und ein Auswerteprogramm schreiben, das einige hunderttausend Arbeitsvorgangstermine und Stammdaten aus dem PPS-System liest und daraus die statistischen Kennlinien ermittelt. Prinzipell wäre es Ihnen auch nicht zu viel, einen Terminierungsalgorithmus zu schreiben, der es ermöglicht, über die Auftragseinsteuerung an den ersten Fertigungskapazitäten die Belastung der “weiter hinten” in der Produktion liegenden Fertigungskapazitäten zu regeln. Sie benötigen hierfür lediglich noch zwei, drei Ihrer Kollegen und vielleicht einige Monate Zeit. Sollte er dies nicht verstehen, können Sie es ihm auch mit einfacheren Worten sagen: Geben Sie mir die richtigen Werkzeuge und stabile Vorgaben und ich steuere Ihnen die Fertigung richtig.
Wenn er Sie dann fragen sollte, wo er ein solches Werkzeug finden kann, verweisen Sie ihn doch einmal auf das neue DISKOVER SCO und für den Methoden- und Wissentransfer an die Berater von Abels & Kemmner, Aachen oder FAST Logistik Consulting Schweiz GmbH, Zug.