Eine falsche Bestandsplanung führt nicht nur zu hohen Lagerhaltungskosten, sondern durch Fehlbestände auch zu Mangelerscheinungen in der Lieferbereitschaft. Der Armaturenhersteller Hansa hat seine Prozesse erfolgreich umgestaltet und nachhaltige Verbesserungseffekte erzielt.
Ein erster Scan hinsichtlich der planerischen und dispositiven Prozesse bei der Hansa Metallwerke AG zeigte, dass ein deutliches Optimierungspotenzial in den Bereichen Bedarfsprognose, Materialdisposition, Beschattung und Produktion/Auftragsabwicklung vorlag. Grundlage für den Scan war die intensive Arbeit mit Checklisten der Abels & Kemmner GmbH, Herzogenrath, die modular auf das jeweils zu untersuchende Unternehmen angepasst werden können. Der nicht optimale Entwicklungsstand der Supply-Chain-Prozesse, gemessen an den heutigen Best-Practice-Möglichkeiten, war ein erster Indikator dafür, dass durch geeignete Maßnahmen im Bereich der Systemunterstützung, der Prozesse in Planung und Disposition sowie der eingesetzten Verfahren signifikante logistische Verbesserungen zu erwarten waren
Darüber hinaus wurde im Rahmen einer Potenzialstudie eine erste Überbestandsanalyse für Fertigwaren, Handelswaren und Einkaufsteile durchgeführt. Die Bestandsreduzierungspotenziale lagen zwischen 18 und 40 Prozent und waren in den ersten sechs Monaten realisierbar. Das gesamte Bestandsreduzierungspotenzial für Fertigwaren und Halbfertigerzeugnisse lag teilweise über 50 Prozent.
Die erste Hauptprojektphase
In der ersten Hauptprojektphase wurden für die unterschiedlichen Materialarten die Planungs- und Dispositionsabläufe detailliert aufgenommen, die dabei vorhandene IT-Unterstützung untersucht sowie Werks- und Lagerstrukturen im vorhandenen System erfasst. Parallel wurden Bestandstreiber-Workshops mit den verschiedenen Fachbereichen durchgeführt, die zu weiteren Erkenntnissen führten.
Der Einkauf tendierte zur Preisoptimierung über Menge. Neue Produkte unterlagen einem langen Designprozess. Meilensteine zur Übergabe an die Produktionsphase wurden jedoch nicht gesetzt, was zum Ende oft zeitkritische Entscheidungsfindung bei fixem Endtermin zur Folge hatte. Die Folge war dann unter anderem, dass die Initialbefüllung der Lager bei neuen Produkten zu hoch angesetzt wurde, weil keine Zeit blieb, passende Analysen durchzuführen.
Die Innovationsfreude der Entwickler führte zu häufigen technischen Änderungen, was die Variantenvielfalt unnötig in die Höhe trieb und insbesondere für das Ersatzteilgeschäft zu hohen Lagerbeständen führte.
Beim Auslauf-Prozess fanden sich Restmengen aus Rahmenverträgen, die durch fehlende Kommunikation von Restabnahmeverpflichtungen den Warenbestand unnötig hoch hielten. Durch die fehlende aktive Steuerung kam es bisweilen auch zur Unterschreitung von Mindestbeständen und damit zu neuen Bestellvorgängen. Die vergleichsweise schlechte Liefertreue der Lieferanten wurde aufgrund fehlender Ressourcen nicht aktiv angegangen. Alternativ war es leichter, die Sicherheitsbestände nach oben zu setzen.
Sortimentszwänge beim Zubehör wurden grundsätzlich befürwortet und als fertiges Montagekit lieferfertig bevorratet, ohne jedoch alternative Supply-Chain-Modelle auf vorherigen Wertschöpfungsstufen zu prüfen, um hier teure Bestände inklusive eigener Wertschöpfung zu vermeiden.
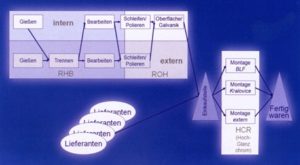
Die zweite Phase
In der zweiten Hauptprojektphase wurde eine Konzeption zur nachhaltigen Reduzierung der Fertigwaren- und Einkaufsbestände entwickelt. Dazu wurden neben Artikelstrukturierungen nach ABC- und XYZ-Kennzeichen verschiedenste Sensitivitätsanalysen in Form von Simulationen durchgeführt.
Diese Analysen zeigten auf, welche logistischen Größen wie Soll-Lieferbereitschaft, Wiederbeschaffungszeiten oder Losgrößen in welchem Ausmaß die Bestandssituation beeinflussen. Darauf basierend wurden sämtliche Parameter zur Optimierung der Wertströme durch dynamische Simulation ermittelt. Die detaillierte Analyse der vorhandenen IT-Unterstützung sowie der Planungsmethoden und -prozesse zeigten in einigen Bereichen Schwächen auf, die von dem umzusetzenden Konzept nachhaltig aufgelöst werden konnten.
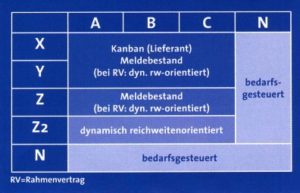
Prozesse optimiert
Die unzureichende Systemunterstützung machte es erforderlich, den Bedarf an externer Prognose- und Dispositionsoptimierung zu untersuchen. Zukünftig setzt Hansa nun die Software „Diskover SCO” aus dem Hause SCT (Supply ChainTechnologies) ein. Über eine Transfertabelle erhält Diskover alle planungsrelevanten Daten aus dem ERP-System, die sodann von der Lösung durch Simulation zur Optimierung der Verfahren und Parameter sowie zur Planung und Disposition bis hin zum Bestellvorschlag oder Fertigungsauftragsvorschlag verarbeitet werden. Die so generierten optimierten Beschaffungselemente werden dann wieder an das ERP-System zur operativen Umsetzung zurückgegeben.
Hinzu kamen ein einheitliches Planungsmodell sowie eine klare Abgrenzung der Planungsebenen und deren Aufgaben (Vertrieb, Produktionsplanung/Disposition, Fertigungssteuerung). Die Absatzplanung inkl. der Berücksichtigung von Trend- und Saisoneffekten wird mittels modernster Planungsverfahren systemgestützt durchgeführt, auch die Behandlung von neuen und auslaufenden Produkten ist dabei klar geregelt. Die Berechnung von optimalen Melde- und Sicherheitsbeständen erfolgt nun durchgängig im System.
Die Disposition wird dann tätig, wenn Handlungsbedarf besteht, also wenn eine Nachbevorratung erforderlich wird. Manuelle Planungsaktivitäten werden durch optimierte automatische Vorgänge ersetzt. Jeder Artikel wird automatisch monatlich rollierend entsprechend seiner Verbrauchscharakteristik und seiner aktuellen Lebenszyklusposition planerisch und dispositiv angepasst. Wie dies zu geschehen hat, ist in der Software im Regelwerk der Disposition hinterlegt. Die Bestands- und Versorgungssituation ist jederzeit transparent und planerische Abweichungen werden dem Disponenten durch Alerts und Reports sofort angezeigt. Der gesamte Planungsprozess ist weniger aufwendig und in seiner Fehleranfälligkeit deutlich reduziert.
Es gibt klare Geschäftsregeln, wie man in der Planung und Disposition/Fertigungssteuerung zu arbeiten hat. Die Vielfalt der Reihenfolge- und Prioritätenlisten hat ein Ende. Unnötige Produktionsvorgriffe finden nicht mehr statt, da sie überflüssige Bestände aufbauen, Vormaterial bei mehrfach verwendeten Teilen verbrauchen, welches unter Umständen anderweitig benötigt wird, und Produktionskapazitäten am Engpass verbrauchen. Die Bestände sind transparent, sodass es nicht mehr zu einer Mehrfachvergabe kommen kann, da sich die verfügbare Menge bei Einsteuerung eines Fertigungsauftrags durch den Planer reduziert.
Fazit
Die Hansa Metallwerke AG hat im Rahmen dieses Projektes konsequent die Umsetzung einer durchgängigen Planung verfolgt und erreicht. Nach rund einem Jahr ist zu konstatieren, dass die deutlich erhöhte Transparenz der Planungs- und Bestandssituation die Handlungsfähigkeit und die Qualität der Planungsentscheidungen steigert. Der Einsatz von Diskover SCO ermöglicht es, jeden einzelnen Artikel bezüglich seiner Planung und Disposition systemgestützt optimal einzustellen. So konnten der dazu erforderliche Bestand seit Projektstart um etwa 30 Prozent reduziert und die Lieferbereitschaft bereits verbessert werden. Das Projekt hat auch eine Entwicklung in Gang gesetzt, die für die Anforderungen der Zukunft hohe Leistungsfähigkeit bei minimalen Kosten verspricht. Damit hat sich das Unternehmen gut aufgestellt, nicht nur die aktuelle Wirtschaftskrise zu meistern,sondern auch bei wieder anziehender Konjunktur anforderungsgerecht und vor allem bestands-beschwerdefrei agieren zu können.
Hansa Metallwerke
Bereits im Jahr 1911 in einer Vorgängergesellschaft in Stuttgart gegründet, produziert die Hansa Metallwerke AG seit 1950 Sanitärarmaturen. Hansa bietet ein variantenreiches Portfolio von innovativen Bad- und Küchenarmaturen sowie Brause- und Duschsystemen an. An seinem Standort Burglengenfeld fertigt das Unternehmen Produkte aus der gesamten Palette. Der Absatz verteilt sich etwa zu gleichen Teilen mit jeweils 50 Prozent auf die In- und Auslandsmärkte. Im Jahr 2008 erreichte der weltweit vertretene Hansa-Konzern einen Umsatz von knapp 220 Mio. Euro. Die Zahl der Mitarbeiter liegt bei 1.150.
Autoren: Steffen Trautwein, Leiter Supply Chain Management, Hansa Metallwerke AG, Stuttgart und Armin Klüttgen, Senior Consultant, Abels & Kemmner GmbH, Herzogenrath.