Materialeffizienz steigern und so durchschnittlich 9,6% Materialkosten sparen
Von Dr. Götz-Andreas Kemmner und Armin Klüttgen
In Bestandsoptimierungsprojekten müssen Fragen der Materialeffizienz oft außen vor bleiben, da sie deutlich weitere Kreise ziehen, als das Projekt vorsieht. Dennoch ist es wichtig, sich auch der Materialeffizienz zu widmen, denn so kann man das Richtige noch besser tun.
Die Potenziale von Materialeffizienzmaßnahmen sind zwar branchenabhängig sehr unterschiedlich, über alle Branchen hinweg beträgt das Potenzial zur jährlichen Materialeinsparung jedoch im Schnitt 9,6%. Je nach Branche kann das jährliche Materialeinsparpotenzial sogar bis zu 20% des Bruttoproduktionswertes betragen, wie eine Studie aus 20051 ermittelte! Die Branchen mit den größten Potenzialen sind demnach die chemische Industrie (20,1%), das Baugewerbe (13,3%), die Herstellung von Kunststoffwaren (11,9%) und Geräten der Elektrizitätserzeugung (8,6%). Aber auch die Herstellung von Metallerzeugnissen, die Be- und Verarbeitung von Holz, die Medizintechnik, die Mess-, Steuer- und Regelungstechnik sowie die Optik weisen Potenziale zwischen 6,4 und 6,9% auf. Die Studie basiert auf 284 Potenzialanalysen in KMU. Im Mittel ergaben sich Einsparpotenziale von 220.000 Euro pro Jahr, 3.300 Euro pro Mitarbeiter bzw. 2,5% bezogen auf den Jahresumsatz. Die Amortisationsdauer der Investitionen zur Bergung dieser Potenziale lag in der Mehrzahl der Fälle unter 6 Monaten. Folgeeffekte der Effizienzmaßnahmen, wie beispielsweise Skaleneffekte im Vertrieb aufgrund von möglichen Preissenkungen, sind hier noch nicht einkalkuliert.
Obwohl diese Studien bekannt sein sollten, verwundert es, dass ca. die Hälfte aller deu tschen Unternehmen im produzierenden Gewerbe noch keine Maßnahmen zur Verbesserung der Materialeffizienz durchgeführt hat, wie eine Umfrage aus dem Jahr 20082 belegt. Dies ist umso mehr verwunderlich, da die Materialkosten im produzierenden Gewerbe mit einem Anteil von etwa 46% an den Gesamtkosten den größten Kostenblock überhaupt darstellen. Die Gründe hierfür sind vielschichtig: Mangelnde personelle Kapazität sowie der mit dem Projekt verbundene Investitionsbedarf stehen ganz oben auf der Liste der Hinderungsgründe.
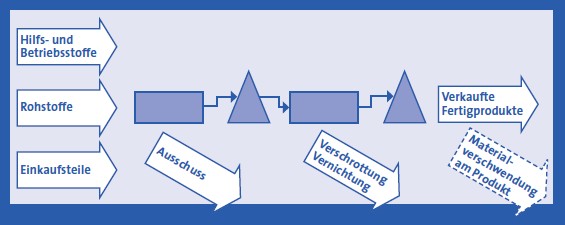
Personelle Engpässe können jedoch durch die Inanspruchnahme externer Berater aufgelöst werden. Zusätzliche Attraktivität gewinnt ein Projekt zur Materialeffizienzsteigerung aber auch dadurch, dass es derzeit ein Förderprogramm des Bundeswirtschaftsministeriums gibt, das bis Ende 2010 auch für Unternehmen bis 1000 Mitarbeiter geöffnet ist. In Abhängigkeit vom Gesamtvolumen der Finanzierung werden solche Projekte mit bis zu 67% über nicht rückzahlbare Zuschüsse gefördert. Damit würden sich solche Projekte im Schnitt in deutlich weniger als sechs Monaten amortisieren und danach jedes Quartal durchschnittlich satte 55.000 Euro Mehrertrag einspielen. Zudem ist es (nicht nur für KMU) an der Zeit, sich intensiv mit diesen bisher eher vernachlässigten Potenzialen auseinander zu setzen, denn die Materialpreise werden langfristig wieder steigen. Zu erwarten ist auch, dass Klimaschutzbestimmungen die Materialkosten zusätzlich steigen lassen.
Materialeffizienz gesamtwirtschaftlich betrachtet
Das in der Materialeffizient schlummernde gesamtwirtschaftliche Potenzial ist enorm, wie die absoluten Zahlen zeigen:
- Im Jahr 2007 betrugen die gesamten Kosten des verarbeitenden Gewerbes 1.723 Mrd. Euro.
- 792 Mrd. Euro (46%) entfielen auf den Posten Materialverbrauch.
- Im Gegensatz dazu entfielen nur 310 Mrd. Euro (18%) auf Personalkosten.
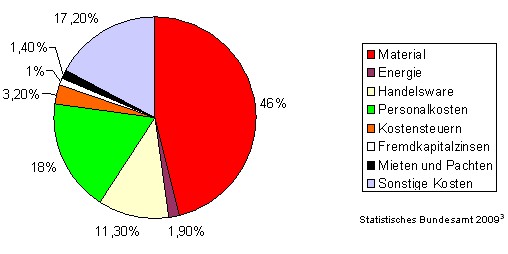
Innovationspotenzial verpasst?
Die Arbeitsproduktivität hat in den letzten 50 Jahren eine Steigerung um den Faktor 3,5 erfahren, die Materialproduktivität hinkt mit dem Faktor 2 deutlich hinterher und zeigt damit in gewisser Weise auch verpasstes Innovationspotenzial bei den Produkten auf.
Dies deutet sich auch beim Vergleich der beiden Kostenblöcke in unseren Unternehmen, Personal und Material an. Während man in den letzten Jahren große Anstrengungen unternahm, die Personalkosten zu senken, sind im gleichen Zeitraum die Materialkosten anteilig am Gesamtkostensatz deutlich gestiegen. So nahmen die Materialkosten von 1995 bis 2007 um ca. 8% zu, während gleichzeitig die Kosten für Personal um 7% zurückgingen.
Deshalb gilt es, das Bewusstsein für die große Chance, die Materialeffizienzprojekte in sich tragen, zu schärfen und Hemmnisse bei der Durchführung von Maßnahmen zu hinterfragen und auszuräumen.
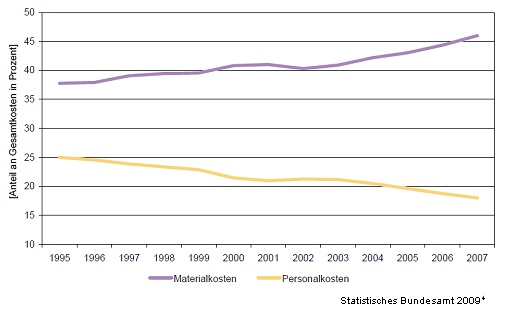
Wie kann die Materialeffizienz gesteigert werden?
Die Ansatzpunkte, um bei der Herstellung von Gütern die Materialeffizienz zu steigern, sind vielfältig. Durch entsprechende Gestaltung von Produkten und durch die Optimierung industrieller Prozesse lassen sich Ressourcen einsparen. Zudem lassen sich Rohstoffe, die als kritisch oder problematisch einzustufen sind, durch weniger problematische ersetzen. Zur Steigerung der Materialeffizienz sind daher alle Maßnahmen geeignet, die den Einsatz von Material (inklusive der eingesetzten Hilfs- und Betriebsstoffe) im Produktionsprozess reduzieren. Dies kann beispielsweise durch Verbesserungen in der Konstruktion von Produkten, durch Verringerung von Ausschuss (Qualitätsschrotte) oder die Optimierung von Verschnitt (Planschrotte) erreicht werden. Die wesentlichen Ansatzpunkte zur Steigerung der Materialeffizienz kann man dabei in folgende Teilbereiche untergliedern:
- Produktkonstruktion und -dimensionierung
- Materialauswahl (Auswahl oder Substitution von eingesetzten Materialien sowie von Reinigungsmitteln und Hilfsstoffen)
- Bestimmung von Geometrien
- Variantenmanagement (Reduzierung interner Komplexität unter Beibehaltung der externen Komplexität)
- …
- Produktionsprozess
- Verfahrenstechniken in der Bearbeitung
- Prozessparameter
- Verschnittoptimierung
- Wiederverwendung von Schrotten / Verwendung von Abfällen
- Zeitpunkt und Art der Reinigung von Zwischenprodukten
- Arbeitsanleitungen Zeitpunkt und Methode der Fehleridentifizierung in den Prozessen
- …
- Umfeld der Produktion
- Disposition und Lagerhaltung
- Verpackung und Transport
- Reinigungsmittel sowie Wasserverbrauch und -aufbereitung
- …
- Planung
- gesamter Prozess in der Supply Chain
- Absatz- bzw. Bedarfs- sowie Bestandsplanung
- Produktionsplanung
- Beschaffungsplanung
- …
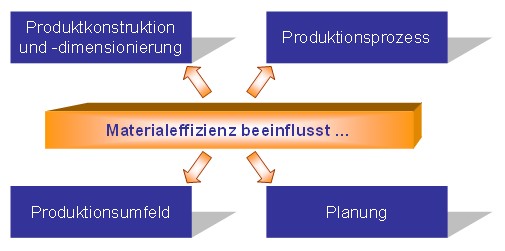
Gerade bei der Entwicklung von neuen Produkten ist das Potenzial zur Verbesserung der Materialeffizienz sehr hoch. Hier ist natürlich gefordert, wie es die Automobilindustrie schon länger praktiziert, grundsätzlich Material einzusparen (z.B. Leichtbau), ohne die Anforderungen an das Gesamtprodukt einzuschränken. Darüber hinaus sollen Produkte reparaturfreundlich und am Ende gut recyclebar sein.
Nicht zu vernachlässigen ist auch in dieser frühen Phase des Produktlebenszyklus die Reduzierung der internen bei Aufrechterhaltung der externen Komplexität. Die Kunden sollen unter einer großen Vielfalt von Produkten auswählen können. Ziel muss es aber sein, intern die Vielfalt durch einen hohen Anteil an Mehrfachverwendungsteilen so gering wie möglich zu gestalten, da eine hohe Variantenvielfalt die Anzahl und Menge der benötigten Rohstoffe, Fertigungs- und Montageteile und Baugruppen beeinflusst und zudem auch Auswirkungen auf die Effizienz der eingesetzten Produktionsmaschinen hat. Durch Reduzierung der Variantenvielfalt im Innern des Unternehmens wird zudem die Planbarkeit der Produkte verbessert und das Risiko von Ausschuss und Verschrottung wegen wegfallender Bedarfe oder Fehlplanungen minimiert. Ganz nebenbei reduziert sich auch der erforderliche Aufwand für Stammdatenerstellung, Disposition, Transport und Handling.
Während diese Aspekte u.a. in der Methode des Design-to-Cost oder in späteren Standardisierungsprojekten ihren Niederschlag finden, setzt die Methode des Zero-Loss-Management besonders wirksam in den Lebenszyklusphasen des Wachstums, der Reife und der Sättigung an. Neben der Betrachtung der gesamten Supply Chain finden hier insbesondere die Produktionsprozesse sowie die Gestaltung der Materialströme Beachtung. Beim Zero-Loss-Management werden alle Kostenelemente, die nicht in Form der Endprodukte beim Kunden eingesetzt und somit vom Kunden auch nicht als Produkt bezahlt werden, als Verlust („Loss“) bezeichnet. Möglichst alle Verluste zu vermeiden, ist Ziel der Optimierung. Zum Fokus eines Materialeffizienzprojektes gehören daher „Losses“, wie Rohmaterialabfall oder -zurückweisungen, Verluste bei Zwischenprodukten, Fertigerzeugnissen und Verpackungsmaterialien sowie Verbrauchsmaterialien, wie beispielsweise Wasser. Beispiele aus der Praxis dafür sind:
- In der Pharma-Industrie die Erhöhung der Zielproduktausbeute durch Optimierung der Prozessparameter, insbesondere der Abweichung vom stöchiometrischem Einsatzverhältnis der Ausgangsstoffe, um eine höhere Gesamtausbeute zu erzielen. Dabei ist eine Kostenverringerung um bis zu 12% durchaus möglich.
- Einsparung bei den Gesamtproduktionskosten um 3,5% durch Vermeidung von Produkt- und Verpackungsverlusten bei einem Hersteller von Tiefkühlkost
- Anpassung von Mess- und Regeltechnik, damit Produktionsparameter enger eingestellt und Qualitätsverluste reduziert werden können -> Reduzierung der Materialverlustkosten um 14%
- Reduzierung der jährlichen Verschrottungen bei einem mittelständischen Handelsunternehmen um 450.000€ pro Jahr
Neben dem oftmals vorhandenen Problem der Verschnittoptimierung bietet das verstärkte Recycling von Werkstoffen zudem ein großes Potenzial zur Materialeffizienzsteigerung. Im Bereich der Schmierstoffe beispielsweise kann ein großer Teil des anfallenden Altöls durch fortschrittliche Recycling-Methoden immer besser wiederverwertet werden.
Konzeption von Materialeffizienzprojekten
Wo auch immer Sie Hauptansatzpunkte wittern: Wichtig ist, dass in Materialeffizienzprojekten alle oben genannten Bereiche in einen umfassenden und ganzheitlichen Gestaltungsansatz eingebettet werden. Einzelaktionen bringen hier wenig, denn sie sind nicht nachhaltig.
Im Rahmen einer Potenzialanalyse gilt es daher im ersten Schritt, eine vollständige Materialbilanz des Unternehmens und seiner Prozesse zu erstellen. Die Materialbilanz stellt in einem produktiven System die Mengen an Materialeinsatz den Mengen an Materialausbringung gegenüber. Der gesamte Stofffluss wird nach Art und Menge identifiziert, Verluste werden offen gelegt. Die zentrale Frage lautet: Wo werden bei der Konstruktion von Produkten, den Produktionsprozessen, dem Produktionsumfeld und der durchgängigen Planung der Supply Chain Materialeffizienzen aufgefressen oder Potenziale zur Materialeffizienzsteigerung nicht genutzt? Die identifizierten Materialeffizienz-Defizite werden dann im nächsten Schritt mit dem Entwurf einer Gesamtkonzeption nicht nur attackiert, sondern sollen nachhaltig aufgelöst werden.
Hier ist die wirkungsvolle Verknüpfung aller Maßnahmen von der Materialbeschaffung bis hin zum Vertrieb der hergestellten Produkte gefordert. Die durchgängige Planung der Supply Chain hinsichtlich Bedarf und Bestand sowie die Festlegung der optimalen Bevorratungsstrategien bildet dabei die unerlässliche Basis, um mit geringem Verschrottungsgrad und damit ressourcenschonend und kostengünstig die Wettbewerbsfähigkeit zu steigern. Fehler in diesen Planungsdomänen führen unweigerlich zu unnötigen Rohstoffverbräuchen, falscher Verwendung von Material (und Energie, die allerdings nicht zur Materialeffizienz gezählt wird) in der Produktion sowie zur Herstellung von nicht benötigten Zwischenprodukten und Enderzeugnissen. Dies wiederum mündet häufig in Verschrottungs- oder rabattierte Verkaufsaktionen, die die Materialbilanz und damit die Materialeffizienz über Gebühr beanspruchen. Der strategische Stellhebel Materialeffizienzsteigerung kann folglich nur dann effizient umgelegt werden, wenn gleichzeitig die Dispositionsprozesse optimiert werden.
1 Studie der Arthur D. Little GmbH, des Wuppertal Instituts für Klima, Umwelt und Energie sowie des Fraunhofer-Instituts für System- und Innovationsforschung.
2 Umfrage des BDI aus dem Herbst 2008
3 Statistisches Bundesamt (2009), Produzierendes Gewerbe – Kostenstruktur der Unternehmen des Verarbeitenden Gewerbes sowie des Bergbaus und der Gewinnung von Erden und Steinen, Fachserie 4 – Reihe 4.3, Wiesbaden.
4 Statistisches Bundesamt (2009), Sachgebiet/Statistik Code 42251