Materialeffizienz bei Anita Dr. Helbig GmbH um 29% erhöht
Von Felicitas Heid-Davignon1 und Armin Klüttgen2
Die Steigerung der Materialeffizienz findet immer mehr Beachtung. Schließlich schlummert hier großes Optimierungs-Potenzial. Die Anita Dr. Helbig GmbH hat mit Unterstützung von Abels & Kemmner im Rahmen eines Materialeffizienzprojektes erhebliche Kostensenkungspotenziale identifiziert und erste Maßnahmen zur Umsetzung eingeleitet. Das gestiegene Bewusstsein für die wertschöpfende Wirkung von Ausschussreduktion wird sogar noch weitere positive Effekte nach sich ziehen: Bereits während des Projektes hat die neue Transparenz über die Materialeffizienz das Denken aller beteiligten Mitarbeiter spürbar verändert.
Während die Personalkosten schon seit vielen Jahren im Zentrum von Verbesserungsmaßnahmen stehen, wurden die Materialkosten bislang meist vernachlässigt. Eine Umfrage des BDI aus dem Herbst 2008 zeigte, dass ca. die Hälfte aller deutschen Unternehmen im produzierenden Gewerbe noch keine Maßnahmen zur Verbesserung der Materialeffizienz durchgeführt hat. Was ziemlich unverständlich ist, immerhin machen die Ausgaben für Material ca. 46% der Kosten im produzierenden Gewerbe aus. Zudem haben Analysen von Abels & Kemmner ergeben, dass zwischen 19% und satten 53% der Verluste bei der Materialeffizienz geborgen werden können.
Materialeffizienzprojekte amortisieren sich schnell
Damit amortisieren sich Materialeffizienzprojekte sehr schnell und schaffen zum Teil erhebliche Liquiditätsreserven. Auch dies sollte ein guter Grund für jedes Unternehmen sein, seine Materialeffizienz zu kennen und zu optimieren. Warum also nutzen viele Unternehmen diese verborgenen Potenziale nicht?
Die Gründe dafür sind z.B. mangelndes Bewusstsein für das große Potenzial einer genauen Betrachtung der Materialeffizienz. Oder, wenn das Wissen vorhanden ist, steht oft fehlende personelle Kapazität der Durchführung eines solchen Projektes im Wege.
Ein Unternehmen, das bereits davon überzeugt war, durch eine Untersuchung der Materialeffizienz ein deutliches Potenzial zur Kostenreduzierung aufdecken zu können, ist die Anita Dr. Helbig GmbH. Erste intern eruierte Einschätzungen hatten schon Hinweise darauf gegeben. Deshalb ist man gemeinsam mit Abels&Kemmner den unterschiedlichen Ausschussursachen im Rahmen einer Potenzialanalyse auf den Grund gegangen. Das Projekt beinhaltete eine detaillierte Analyse der Ursachen sowie eine exakte quantitative Bewertung der unterschiedlichen Ausschussarten und der darin verborgenen Verbesserungspotenziale. Das Ergebnis war ein Handlungsplan, der im Rahmen der identifizierten Handlungsfelder detaillierte Maßnahmen zur Realisierung der Potenziale aufzeigte.
Ein bisschen Stoff, Bänder, Haken und Ösen, vielleicht noch ein wenig Spitze, eine gute Nähmaschine – und fertig ist der formschöne und luxuriöse BH. So vereinfacht stellen sich viele wohl die Herstellung eines BHs vor. In der Realität aber ist dieses Produkt sowohl in der Planung als auch in der Fertigung die Königsdisziplin in der Textilindustrie. Hier kann man in Bezug auf die Materialeffizienz vieles falsch machen – oder aber, durch die richtigen Optimierungsmaßnahmen – in erheblichem Umfang Kosten reduzieren.
Ausschuss hat viele Ursachen
Die Planung von Vormaterialien und Fertigerzeugnissen sieht sich einer Vielfalt von Problemen gegenüber, die es mit wenig Bestand bei hoher Lieferfähigkeit zu bewältigen gilt. Ein Beispiel hierfür: Da das zu planende Produkt in höchstem Maße modischen Einflüssen unterworfen ist, entstehen bei nicht optimaler Planung erhebliche Mengen an inkurantem Material (insbesondere Stoffe als Breitware bzw. Ballen), das als Überhang aus der Planung übrig bleibt. Dieses Material ist zu wirtschaftlich vertretbaren Konditionen nicht mehr zu verkaufen. Gibt es in der eigenen Produktion keine Möglichkeit der alternativen Verwendung, kann dieses Material nur noch vernichtet werden.
In der Produktion fallen darüber hinaus noch weitere geplante sowie qualitätsbedingte Ausschüsse an. Die geplanten ergeben sich zum Beispiel beim Zuschneiden von einzelnen Teilen aus einem Lagenbild, wobei Verschnitt im Lagenbild selber sowie an den Lagenrändern und -überständen entsteht. Die Qualitätsausschüsse ergeben sich daraus, dass das Arbeitsergebnis nicht den geforderten Kriterien entspricht. Hierbei ist eine Nacharbeit oftmals nicht möglich, wodurch auch hier eine Vernichtung notwendig wird. Die Ausschüsse in der Produktion können dabei erheblich sein. All diese Ausschüsse, die offensichtlich unterschiedlichste Ursachen haben, gilt es möglichst zu vermeiden.
Bevor wir aber in die Details der Maßnahmen einsteigen, die zur Beseitigung der Ausschüsse führen sollen, ist es erforderlich zu verstehen, wie vielschichtig der Produktionsprozess ist und welche Herausforderung sich dadurch für die Planung der BH-Fertigung ergeben.
Neben Arbeitsvorgängen wie Kommissionieren und Verpacken für den Materialfluss zur Näherei besteht die Fertigung im Wesentlichen aus Vorfertigung, Kaschieren, Zuschneiden, Molden und Nähen. In der Vorfertigung werden sog. Zutaten wie z.B. Haken, Ösen, Bänder, etc. verarbeitet. So werden z.B. Verschlüsse hergestellt, Träger konfektioniert oder aber Bänder geschnitten, die unmittelbar für die Näherei zur Verfügung gestellt werden. Vor dem Zuschnitt wird Breitware gefärbter und bedruckter wie unbedruckter elastischer Stoffe vom Ballen abgewickelt und durch verschiedene Verfahren entspannt, da der Stoff auf dem gelieferten Ballen unterschiedliche Spannungen aufweisen kann. Im nächsten Schritt werden die entspannten Materialien mit Legewagen auf vorgegebene Lagenhöhe und -länge gelegt, z.B. mit dreißig Stück, und gemäß Lagenbild zugeschnitten. Beim Kaschieren werden verschiedene Stoffe flächig miteinander verbunden (verklebt), wodurch das Material stabiler (verstärkt) wird und auf den beiden Seiten unterschiedliche Optik und / oder Haptik entstehen. Auch die Vormaterialien für das Kaschieren sind Breitwaren. Beim Molden werden unter Einsatz von hohen Temperaturen und Druck rechteckige Stoffplatten in die richtige Größe und Form des gewünschten Cups gebracht. Die endgültige Form entsteht durch Stanzen, wobei die überstehenden und nicht genutzten, aber verfahrenstechnisch erforderlichen Ränder entfernt werden. Das Vormaterial des Moldens sind im Zuschnitt entstandene rechteckige Platten. Beim Nähen entsteht aus den zuvor beschriebenen Materialien bzw. den daraus gefertigten Schnitt teilen und weiteren Komponenten, wie Einfassbändern, elastischen Bändern, Bügeln, usw. der fertige BH. Dieser kann aus bis zu vierzig verschiedenen Bestandteilen und bis zu fünf verschiedenen Breitwaren bestehen.
Stoffstromanalyse – Identifikation der Materialverluste
Diese Beschreibung der Produktion zeigt bereits, dass der Stoff viele einzelne Arbeitsschritte durchlaufen muss, bis aus ihm ein fertiger BH geworden ist. Die bei Anita im ersten Schritt durchgeführte Stoffstromanalyse war deshalb ein wesentlicher und unerlässlicher Bestandteil des Materialeffizienzprojektes. Sie schlüsselte die Materialströme zwischen den Fertigungsabteilungen auf und dokumentierte bei jeder Fertigungsabteilung, wie viel geplanter und qualitätsbedingter Ausschuss in diesem Bereich angefallen ist und wie viel inkurante Mengen vernichtet wurden.
Üblicherweise sollte ein Stoffstrom zwar in Mengeneinheiten (kg, m, m², m³…) aufgeführt werden. Bei Anita war dies nicht möglich, weil zu den Materialnummern (Teilen) die Gewichte nicht durchgängig dokumentiert waren und bei zusammengefügten Teilen (z.B. Meterware und Stückgüter in der Vorfertigung) eine eindeutige Zuordnung zum Einsatzmaterial und damit eine sinnvolle Darstellung nicht mehr möglich war. In einem solchen Fall kann aber die bewertete Menge Abhilfe schaffen, sodass dennoch die Informationen im Stoffstrom im Hinblick auf die Materialeffizienz aussagekräftig sind, da zu jedem Produktionsbereich exakte Werte ermittelt werden konnten. Konkret ermittelt wurden:
- Weitergeleitetes Material
- Ausschussvolumen geplant (absolut und in %),
- Ausschussvolumen Qualität (absolut und in %)
- Ausschuss inkurantes Material (absolut und in %)
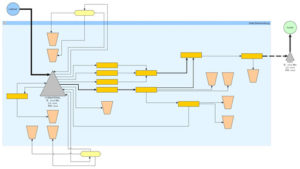
Festgestellt wurde, dass bei Anita sowohl in der Vorfertigung als auch beim Nähen nur geringe qualitätsbedingte Ausschüsse anfallen, geplante Ausschüsse gibt es bei diesen Arbeitsvorgängen nicht. Beim Kaschieren, Zuschneiden und insbesondere beim Molden kommt es jedoch zu deutlichen Ausschussraten, die sich aus den hohen Qualitätsanforderungen von Anita ergeben. Darüber hinaus waren beim Molden und beim Zuschneiden erhebliche geplante Ausschüsse zu verzeichnen. Die Vernichtung inkuranter Materialien (inkl. Faltschachteln) aus dem Lager vervollständigt die Aufstellung der Materialverluste. Auch hierbei fallen beträchtliche Summen pro Jahr an. Insgesamt wurden im Jahr 2009 Materialien im Wert von ca. 20% des Einkaufsvolumens vernichtet. Den größten Anteil daran hatten mit über 73% die geplanten Ausschüsse im Molden und im Zuschnitt. Aber auch die Qualitätsausschüsse im Molden und insbesondere die inkuranten Materialien trugen mit fast 22% beträchtlich zur Höhe der Ausschüsse bei.
Constraintanalyse – Die Kernursachen der Materialverluste identifizieren
Die im Rahmen der Stoffstromanalyse ermittelten Materialeffizienzverluste wurden mit Hilfe einer Constraint-Analyse weiter untersucht. In der Constraint-Analyse wird eine Ursachen-Wirkungskette aufgebaut. Ziel ist es, in einem komplexen Ursache-Wirkungsnetz die „root-causes“, also die Ursachen an der Wurzel des Netzwerkes zu identifizieren. Ein in der Folge der Constraintanalyse zu erstellender Handlungsplan beinhaltet die Maßnahmen, um die gefundenen root-causes zu beseitigen.
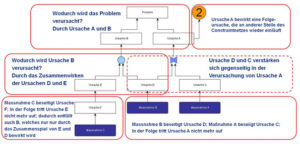
Durch die Beseitigung der Kernursachen fallen in der Folge die Auswirkungen im Constraint-Netz in sich zusammen und die unerwünschten Effekte, in diesem Falle Material-Ineffizienzen, können beseitigt bzw. reduziert werden. Die Constraint-Analyse wurde nur dort durchgeführt, wo im Rahmen der Stoffstromanalyse substanzielle Materialeffizienzverluste identifiziert werden konnten.
Klares Ergebnis der Analyse: die wesentlichen Materialverluste entstehen durch die Komplexität der Planungsaufgabe, deren vielschichtige Probleme in inkurantes Material münden sowie durch besonders anspruchsvolle Fertigungsverfahren, die nicht immer stabil ablaufen und bei denen schwierig zu beherrschende Materialien eingesetzt werden.
Planungsabweichungen generieren inkurantes Material
Die Absatzplanung der Artikel und in der Folge die Planung der zu beschaffenden Materialien wird bei Anita von einer Vielzahl von Faktoren beeinflusst, die das Planungsergebnis teilweise erheblich von der tatsächlich eintretenden Situation abweichen lassen. Die Kundennachfrage richtet sich in einzelnen Kollektionsgruppen stark nach modischen Einflüssen und es besteht eine stete Forderung nach Neuheiten. Der Neuheitencharakter wird dabei nicht nur durch Farben und Drucke erzeugt, sondern vielfach auch durch neuartige Materialien und Verarbeitungen, die eine spezielle Funktion bewirken. Diese müssen höchsten Funktions- und Qualitätsansprüchen genügen, was zwei Auswirkungen zur Folge hat: Anita durchläuft gemeinsam mit dem Lieferanten einen sehr aufwendigen und damit zeitintensiven Entwicklungsprozess, der im Hinblick auf die Anforderungen der Planung schwierig zu integrieren ist. Als zweiten Effekt hat man wegen der sehr hohen Qualitätsanforderungen und dem aufwendigen Entwicklungsprozess nur wenige alternative Lieferanten zur Verfügung. Hier können Beschaffungsprobleme entstehen, die nur über zusätzliche Sicherheitsbestände abgedeckt werden können. Hohe Wiederbeschaffungszeiten bei vielen Stoffen und Vormaterialien und teilweise sehr sporadisch verlaufende Bedarfe machen dem Planer das Leben zusätzlich schwer.
Bei einigen kritischen Materialien müssen wegen instabiler Produktionsprozesse weitere Puffer vorgehalten werden, damit die Lieferbereitschaft in ausreichendem Maße gewährleistet werden kann. Ein weiteres Problem: Materialmengen und Kontrakte müssen zu einem Zeitpunkt festgelegt werden, zu dem man über die Bedarfsentwicklung eines neuen Produkts inkl. Vorordergeschäft noch nicht wirklich belastbare Aussagen treffen kann. Die Erstdisposition basiert daher meist auf Erfahrungswerten. Wiederkehrende Abweichungen in den Beständen, verursacht durch verschiedenste Defizite in den Prozessen und der Systemunterstützung, ein hoher Anteil von manuell durchgeführten Planungsschritten sowie nicht durchgängig gepflegte Daten behindern die Planungserstellung zusätzlich.
In der Summe entstehen durch die verschiedenen Problemkreise in der Planung, die sich gegenseitig überlagern und zum Teil verstärken, erhebliche Mengen inkuranten Materials, welches schlimmstenfalls vernichtet werden muss. Im Jahr 2009 war dies nach den geplanten Ausschüssen bei den Arbeitsvorgängen Zuschneiden und Molden mit ca.14% am gesamten Ausschuss die drittgrößte Position.
Im geplanten Ausschuss spielt die Musik
Drei Viertel der in 2009 angefallenen Ausschüsse waren geplante Ausschüsse bei den Arbeitsvorgängen Zuschneiden und Molden. Nach dem eigentlichen Molding-Vorgang, der Formgebung für den Cup, werden von den dafür verwendeten Stoffplatten, die zuvor aus der Breitware geschnitten worden sind, die Reststücke im Randbereich (ca. 40%) durch Stanzen entfernt. Die so entstandenen Abschnitte sind nicht mehr verwendbar und zu 100% Ausschuss. Darüber hinaus fallen noch qualitätsbedingte Ausschüsse an, die z.B. entstehen können durch unzureichende Ausfixierbarkeit der Form, Farbumschläge durch Temperatureinwirkung oder auch Veränderung der Oberfläche durch Hitze (Material wird glasig oder kann verhärten).
Im Zuschnitt waren 20% der eingesetzten Mengen geplanter Ausschuss. Dieser setzt sich zusammen aus den Lagenrändern, dem Lagenüberstand sowie den Abschnitten im Lagenbild selber. Verglichen damit waren die Ausschüsse, die beim Zuschneiden auf Qualitätsmängel zurückzuführen sind, z.B. durch nicht erkannten Materialeinsprung, schon fast vernachlässigbar.
Der Handlungsplan
Basierend auf den Erkenntnissen der Stoffstrom- und Constraintanalyse wurden im Rahmen des Projektes Handlungsfelder identifiziert und Maßnahmen formuliert, die die Kernursachen der Material-Ineffizienzen attackieren. Insgesamt wurden in sechs verschiedenen Handlungsfeldern fast fünfzig verschiedene Maßnahmen erarbeitet, die zum Teil ihrerseits wieder mehrere Aktivitäten enthalten. Die Maßnahmen wurden mit ihren Potenzialen zur Verbesserung der Effizienz bewertet und der Größe der Hebelwirkung nach, in einer Projekt-Roadmap aufgelistet. Exemplarisch seien nachfolgend nur einige Handlungsfelder und Auszüge ihrer Maßnahmen dargestellt:
- Handlungsfeld geplante und qualitätsbedingte Ausschüsse in der Fertigung
- Modifikation von Prüfverfahren und Prüfzeitpunkt sowie Schulungsmaßnahmen zur Erhöhung der Qualität beim Arbeitsvorgang Molden
- Machbarkeitsstudien und weitere Maßnahmen zur Reduzierung des geplanten Ausschusses beim Arbeitsvorgang Zuschnitt
- Handlungsfeld Lieferantenanbindung
- Optimierung des Lieferantenportfolios und aktive Lieferantenentwicklung
- Verschiedene Maßnahmen zur besseren Beherrschung sporadischer Bedarfe eingebettet in einen stabilen Abwicklungsprozess
- Verhandeln diverser Einkaufsbedingungen
- Handlungsfeld Materialplanung und -disposition
- Entwurf eines Konzeptes zur Implementierung einer durchgängigen Planung und Disposition
- Optimierung Materialdisposition / Einkauf durch erweiterte Systemunterstützung und verschiedene planerische Erweiterungen
- Handlungsfeld Transparenz der Bestände
- Erhöhung der Bestandssicherheit durch Anpassungen in der Lagerverwaltung
- Etablierung einer vollständig integrierten Bestandsführung in einem System
Die zuvor gelisteten Maßnahmen können nur einen Eindruck vermitteln für die Vielschichtigkeit und die Komplexität des Themas Materialeffizienz sowie die Intensität des mit Anita durchgeführten Projekts. Die Potenziale, die das Projekt offenbart hat, sind durchaus beeindruckend. Und der eingeleitete Bewusstseinsprozess hat schon während der Projektlaufzeit dazu geführt, dass die Motivation zur Steigerung der Materialeffizienz signifikant gestiegen ist und die beteiligten Personen ein großes Interesse an der gesamten Thematik entwickelt haben.
Quantifizierung der Ergebnisse
Die Maßnahmen, die im Rahmen der unterschiedlichen Handlungsfelder definiert wurden, haben einen deutlichen Anstieg der Materialeffizienz und damit signifikante jährliche Kosteneinsparungen zur Folge. Bei den Arbeitsvorgängen Nähen, Molden, Zuschnitt und Vorfertigung werden die qualitätsbedingten Ausschüsse um 50% gesenkt, beim Kaschieren um 25%. Die geplanten Ausschüsse beim Molden und im Zuschnitt sollen um 12,5 bzw. 25% gesenkt werden. Zusätzlich sollen die Materialvernichtungen, die auf einem Lagerplatz wegen inkuranter Materialien stattfinden, um ca. 60% reduziert werden.
Insgesamt ergibt sich so eine Reduzierung der Ausschüsse um 29%, was einer jährlichen Ersparnis von mehreren hunderttausend Euro entspricht. Für das durchgeführte Materialeffizienzprojekt bedeutet dies eine Amortisationsdauer von deutlich unterhalb eines Monats. Hinzu kommt noch der in Gang gesetzte Bewusstseinswandel bei allen Projektbeteiligten sowie die eintretenden Multiplikatoreffekte durch die verschiedenen definierten und umzusetzenden Maßnahmen im Unternehmen.
Da das Thema der Materialeffizienz in den letzten Jahren eher etwas vernachlässigt wurde, werden Projekte in diesem Bereich zusätzlich von der demea (deutsche Materialeffizienzagentur), einer Institution des Bundesministeriums für Wirtschaft und Technologie, im Rahmen des Impulsprogramms Materialeffizienz (VerMat), gefördert. Dabei umfasst die Förderung einer Potenzialanalyse (Erstberatung mit förderfähigem Projektvolumen bis 30.000 €) 67% bis zu 15.000 € und 50% von 15.000 – 30.000 €. Eine danach mögliche Vertiefungsberatung wird mit 33% gefördert, wobei die maximale Zuwendung aus durchgeführter Potenzialanalyse und Vertiefungsberatung 100.000 € beträgt.
Über die Anita Dr. Helbig GmbH
1886 gegründet genießt Anita mit über hundert Jahren Erfahrung im globalen Markt einen exzellenten Ruf als Nischenanbieter für hochqualitative Spezialwäsche und darf sich zu den unternehmerisch erfolgreichen Unternehmen der Textilbranche zählen.
Als Spezialanbieter für Miederwaren, Bademoden und spezielle medizinische Produkte für die Nachsorge bei Brustoperationen bildet Anita ein kompetentes, international tätiges Netzwerk aus 20 Einzelgesellschaften mit insgesamt über 1.200 Mitarbeitern und einem jährlichen Umsatz von ca. 80 Millionen Euro.
Produktionsstandorte befinden sich in Deutschland, Österreich, Portugal, der Tschechischen Republik und Fernost. Der Vertrieb erfolgt primär über eigene Tochterunternehmen.
1 Felicitas Heid-Davignon ist Bereichsleitung Produktion und Logistik bei der Anita Dr. Helbig GmbH in Brannenburg.
2 Armin Klüttgen ist Principal bei der Abels & Kemmner GmbH.