Von Steffen Schwippl, Serag-Wiessner KG, und Dr. Bernd Reineke
Serag-Wiessner ist ein Hersteller von chirurgischem Nahtmaterial und sterilen flüssigen Arzneiformen. Das traditionsreiche oberfränkische Unternehmen ist ständig bestrebt, höchste Qualitätsanforderungen zu erfüllen und optimiert kontinuierlich die Prozesse in Produktion und Logistik. Der Bereich Lösungen fertigt sowohl Standardinfusionslösungen, flüssige und sterile Produkte für die Wundbehandlung, zahlreiche Sonderlösungen als auch individuelle Rezepturen speziell auf Kundenwunsch. Ein Großteil der Produkte wird ab Lager innerhalb kurzer Zeit geliefert. Diese Anforderungen möglichst kostenarm zu realisieren, ist einfacher gesagt als getan. Ein im Detail sehr komplexer Fertigungsprozess mit ganz spezifischen Restriktionen muss dafür geplant und gesteuert werden. Eine aufgrund der Vielzahl an Einflussgrößen kaum von Hand zu bewältigende Aufgabe.
Daher sollten in dem Segment ‚Lösungen‘ die Prozesse weiter optimiert werden, mit der Zielsetzung, die Durchlaufzeiten zu reduzieren, Bestände auf das notwendige Maß zu senken und gleichzeitig die Lieferbereitschaft auf einem hohen Niveau von 93 % zu halten. Die Absatzplanung bzw. Bedarfsplanung der Enderzeugnisse unterstützte das ERP-System mit Hilfe einfacher Prognosen. Gekoppelt mit ihrem Erfahrungswissen, erarbeiteten die verantwortlichen Disponenten die Plan- und Fertigungsaufträge. Da die Lieferbereitschaft von großer Bedeutung ist, fanden sich Sicherheiten in den Beständen, Sicherheitsbeständen und Durchlaufzeiten.
Die Umsetzung der Planungsergebnisse in der Produktion unterlag dann wiederum den Einschätzungen der Fertigungssteuerer, die nach Möglichkeit versuchten, die Fertigung möglichst effizient nach bestem Wissen und Gewissen zu planen und zu steuern.
Dabei sind gerade im Produktionsbereich viele Einflussgrößen zu berücksichtigen, die in der Summe zu einer sehr hohen und nicht mehr überschaubaren Komplexität führen. Hinzu kamen aufgrund nicht ausreichender Bevorratung zahlreiche Adhoc-Aufträge, die kurzfristige Umplanungsvorgänge zur Folge hatten und die Effizienz der Prozesse stark beeinflussten.
Ziel des Projektes war es daher, ausgehend von einer systemgestützten Absatzplanung, eine optimierte Produktionsplanung und -steuerung zu ermöglichen. Optimal bedeutet dabei ein Ergebnis, das mit Berücksichtigung relevanter Kriterien nach abgestimmten Regeln eine ressourcenschonende Produktionsreihenfolge darstellt.
Der Wertstrom des Fertigungsprozesses ist in der nachfolgenden Abbildung dargestellt:
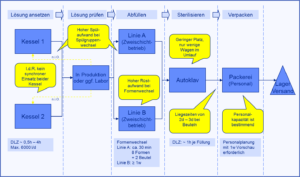
Der Abfüllprozess startet beim Ansetzen der Lösungen in zwei verschiedenen Kesseln. Nach einer Überprüfung der Spezifikation und Erfüllung der Produktanforderungen erfolgt der Abfüllprozess aus den Kesseln in Beutel oder Flaschen. Dafür stehen zwei Abfülllinien zur Verfügung: eine für die Beutel-Produkte und eine für die Flaschenprodukte. Nach dem Abfüllen erfolgt der Sterilisierungsvorgang im Autoklav. Dieser Vorgang erfolgt diskontinuierlich, d.h. der Autoklav wird bis zu seinem Fassungsvermögen aufgefüllt und anschließend erfolgt der temperaturgeführte Sterilisierungsprozess über mehrere Stunden. Nach diesem Vorgang werden die Produkte der Verpackung zugeführt.
Bei der Planung und Steuerung dieses Prozesses sind folgende Restriktionen zu berücksichtigenden:
- Die zum Teil sehr hohen Rüst- und Reinigungszeiten sind bei der Kapazitätsplanung und Terminierung zu berücksichtigen. Die Rüstzeiten für das Abfüllen der Flaschen über die Anlage B beträgt ca. eine Woche, sodass bis dato die Anlage nur zweimal im Jahr umgerüstet wurde.
- Die Räumlichkeiten zwischen Abfüllung und Autoklav sind beengt, so dass nur ein begrenztes Volumen abgefüllter Produkte aufgenommen werden kann. Das führt bei großvolumigen Produkten (große Flaschen oder Beutel) dazu, dass ein Stau vor dem Autoklav entstehen kann.
- Bei kleinvolumigen Produkten ist das Abfüllen der Engpass, Autoklav und Verpackung sind nicht ausgelastet.
- Der Abfüllprozess ist bis zum Sterilisieren im Autoklav noch am selben Tag abzuschließen. Ein neuer Abfüllvorgang kann also nur mit entsprechendem Vorlauf begonnen werden, sodass die abgefüllte Ware bis zum Schichtende sterilisiert werden kann.
- Da die Anlage B zum Abfüllen der Flaschenprodukte über einen längeren Zeitraum den Rüstzustand nicht wechselt, müssen die Produkte, die den aktuell eingestellten Rüstzustand erfordern, zum Zeitpunkt des Umrüstens so hoch bevorratet sein, dass der Zeitraum bis zu dem Zeitpunkt, an dem dieser Rüstzustand wieder erreicht wird, überbrückt und die Lieferfähigkeit bewahrt werden kann.
Unterstützung des Planers durch spezialisierte Werkzeuge
Zur Bewältigung dieses hochkomplexen Planungsprozesses sollten in Zukunft die Planer und Fertigungssteuerer durch geeignete Werkzeuge unterstützt werden. Neben der Bestimmung der richtigen Fertigungsmengen musste die Unterstützung soweit gehen, dass auch eine optimierte Reihenfolge der Fertigungsaufträge ermittelt wird, so dass durch einen geeigneten Produktmix die Kapazitäten optimal ausgelastet sind und sich ein geringstmöglicher Rüstaufwand ergibt. Gleichzeitig galt es, Bestände für die Produkte der Linie B aufzubauen, um die Dauer des Rüstzyklusses zu überbrücken.
Berechnung des EPEI als Planungsgrundlage
Am Anfang der Konzeption der zukünftigen Lösung stand die Frage, welches die richtigen Losgrößen sind und wie viele Rüstvorgänge machbar sind. Zur Beantwortung dieser Frage wurde das Prinzip des EPEI (Every Part Every Intervall) zugrunde gelegt. Bei dem EPEI handelt es sich um den kleinstmöglichen Zeitabschnitt, in dem jedes der Produkte, die über diese Linie gefertigt werden, in ausreichender Menge hergestellt werden kann. Das EPEI ermöglicht also eine optimale Ausnutzung der verfügbaren Ressourcen durch Bearbeitungs- und Rüstprozesse.
Eine erste Überraschung war es, dass die bisherige Annahme, die Linie B könne maximal zweimal im Jahr gerüstet werden, widerlegt wurde. Mit Berücksichtigung von geringen zeitlichen Puffern konnte die Zahl der Rüstvorgänge quasi verdoppelt und damit die Losgrößen halbiert werden. Ein erster Schritt also zur Bestandsreduzierung.
Wichtige Eingangsgröße: die Prognose
Eine der wichtigsten Eingangsgrößen für den Planungsprozess ist eine belastbare Prognose der zukünftigen Bedarfe. Zur Ermittlung der optimierten Prognosen dient das bereits in einem anderen Produktsegment im Einsatz befindliche Optimierungssystem DISKOVER SCO.
Dieses liefert zum einen Bedarfszahlen zur Erfüllung der gewünschten Lieferfähigkeit und zum anderen die notwendigen Produktionsvorschläge unter Berücksichtigung der aktuellen Bedarfs- und Beschaffungssituation. Diese Produktionsvorschläge werden nun von dem neu geschaffenen Fertigungssteuerungssystem aufgegriffen, in die richtige Reihenfolge gebracht und durchterminiert. Dabei dient eine sogenannte Rüstmatrix als Grundlage zur Reihenfolgeoptimierung, die die Rüstzeiten aller möglichen Produktwechsel im Abfüllprozess enthält. Der Terminierungsalgorithmus setzt auf die aktuelle Fertigungssituation auf, also darauf, in welchem Rüstzustand sich die Abfüllanlage befindet und wie weit der Fertigungsfortschritt ist.
Unter Berücksichtigung der Schicht- und Pausenzeiten werden die Aufträge auf Arbeitsvorgangsebene terminiert und in Form einer tabellarischen Ansicht sowie als Gantt-Diagramm dargestellt (siehe Abbildung 2).
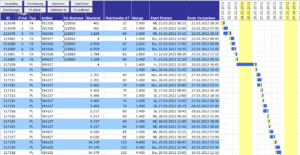
Der Fertigungssteuerer kann jetzt die Planaufträge umsetzen und automatisiert an das ERP-System übergeben. Weiterhin bietet die Lösung die Möglichkeit, mit einfachen Klicks Aufträge zu fixieren, zu splitten oder auch die Reihenfolge zu verändern.
Bereits nach 2 Monaten Einsatz konnten mit Hilfe des Schedulers die Bestände im Produktsegment PL um 23 % gesenkt werden (vgl. Abbildung 3). Gleichzeitig hat sich die Liefersituation deutlich verbessert. Viel wichtiger aber sind die bessere Transparenz und schnelle Erledigung der Planungsaufgabe. Diese kann nun auch von weiteren Mitarbeitern nach kurzer Einweisung in das Tool übernommen werden.
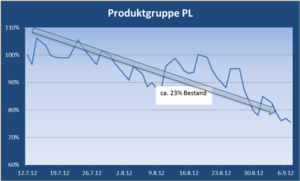
Weitere Informationen zu diesem Themenfeld finden Sie hier:
- Best-Practice-Regeln für eine leistungsfähige Disposition
- Die hierarchische Planung: Auf den richtigen Planungs-Mix kommt es an!
- Hohe Lieferbereitschaft bei schwankender Nachfrage
- Stets präziser Eingriff in die Supply Chain