Um Kapazitätsengpässe in der Produktion aufzulösen, hat der Schaltgerätebauer Fritz Driescher eine marktsynchrone Wertschöpfungskette von der Komponentenfertigung bis zur Endmontage aufgebaut.
Mittel- oder Niederspannungsschaltanlagen, Transformatorstationen sowie Hoch- und Niederspannungs-Sicherungseinsätze gehören zum Produktspektrum der Fritz Driescher GmbH & Co. KG in Wegberg. Nach eigenen Angaben ist das Familienunternehmen inzwischen der einzige Mittelständler seiner Branche. Das erfordert eine hohe Produktqualität, eine hohe Flexibilität bei den Kundenwünschen, kurze Lieferzeiten und eine hohe Termintreue.
Die Komponenten für die auftragsbezogene Endmontage der Schaltanlagen stellt das Driescher-Zentrallager bereit. Das bisherige logistische Geschäftsmodell sah eine auftragsbezogene Komponentenfertigung und Materialbereitstellung für die Endmontage vor. Angesichts zunehmender Marktschwankungen, einer wach-senden Variantenvielfalt sowie kürzerer Lieferfristen stieß es jedoch zunehmend an seine Grenze.
Die bislang fehlende Kapazitätsplanung musste das Auftragszentrum durch manuelle Priorisierungen kompensieren. Teilweise terminierten die Disponenten die Fertigungstermine dabei in die Vergangenheit. Laufend gab es Abstimmungsbedarf zwischen Komponentenfertigung, Zentrallager, Endmontage und Auftragszentrum. In der Endmontage fehlten dennoch häufig Komponenten. Die Mitarbeiter konnten teilmontierte Schaltanlagen nicht zu Ende bauen und begannen, Komponenten zwischenzulagern, was zu Platzproblemen und häufiger Materialsuche führte.
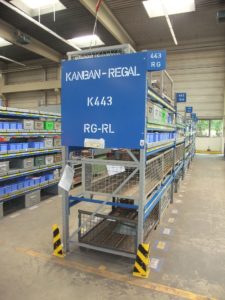
Zu lange Durchlaufzeiten
Die Komponentenfertigung kämpfte gleichzeitig mit hohen Auftragsrückständen und langen Durchlaufzeiten. „Nur mit hohem Kostenaufwand, großen Beständen, großer Flexibilität der Arbeitszeitkonten und einem relativ hohen Anteil an Standardteilen konnten die Liefertermine gerettet werden”, erinnert sich Manfred Bürger, Leiter des Driescher-Auftragszentrums.
Schließlich entschloss sich Driescher vor Kurzem, eine marktsynchrone Wertschöpfungskette aufzubauen. Die Unternehmensberatung Abels & Kemmner GmbH, Herzogenrath bei Aachen, führte mithilfe einer „Advanced Planning and Scheduling”-Software (APS) zunächst eine Ist-Analyse durch. Sie ergab, dass die Fertigung zu 69 Prozent durch nur zehn Prozent der Teile ausgelastet war. Die restlichen etwa 90 Prozent belegten ein Drittel der Fertigungskapazität. In der Komponentenfertigung betrug der Arbeitsvorrat im Durchschnitt 21 Arbeitstage. Das führte zu langen Durchlaufzeiten und Problemen bei der Termintreue.
Um die Fertigungskapazitäten zu erhöhen, wurden Aufträge vorübergehend nach außen verlagert. Eine Personalkapazitätssteuerung wurde installiert, um kurzfristig die Mitarbeiterkapazitäten dem aktuellen Fertigungsbedarf anzupassen. Aufträge wurden nicht mehr in die Vergangenheit gelegt oder verfrüht eingelastet, sondern nur noch zeitgerecht. Im Verlauf von sechs Monaten gelang es mit diesen Maßnahmen, die Durchlaufzeiten auf im Schnitt vier Tage zu senken.
Heute arbeitet Driescher nach der „Hase und Igel”-Strategie. Sie basiert auf einer 80/20-Nivellierung der Fertigungs-kapazitäten – differenziert nach Standard (XY)- und auftragsspezifischen (Z) Teilen. „Hasen”-Artikel (Z-Teile) werden weiterhin bei einem Fertigungsauftrag priorisiert mit kurzen Durchlaufzeiten und schneller Verfügbarkeit gefertigt (Push-Fertigung). „Igel”-Artikel – das sind AB/XY-Artikel und einige Z-Teile – lagern dagegen über eine Pull-Steuerung (via Kanban) bestandsgeführt im Zentrallager oder in einem ZweiBehälter-Kanban-System in sogenannten Supermarktregalen der Endmontage. Sie wurde so umgebaut, dass für jeden der acht Montagebereiche eigene Kanban-Regale und Palettenstellplätze entstehen konnten. Ist ein Behälter leer, wird per Barcodescan ein Umlagerungsauftrag im Zentrallager generiert. Innerhalb von zwei Arbeitstagen muss die Box dann wieder aufgefüllt werden. Während dieser Umlagerungszeit bedienen sich die Mitarbeiter aus dem zweiten Kanban-Behälter.
Dieses System ermöglicht es, die Endmontage mit einer Lieferbereitschaft von zum Teil über 98 Prozent mit Standardkomponenten zu versorgen. Bisher wurden für die acht Montagebereiche 3.176 Artikel auf das Zwei-Behälter-Kanban-System umgestellt. Interessantes Detail: Trotz der zusätzlichen Lagerstufe sanken die Lagerbestände.
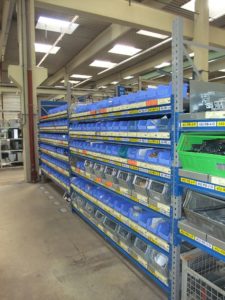
Für die Pull-Steuerung via Kanban wurde im ERP-System „Baan 5″ der Infor GmbH, Friedrichsthal bei Aachen, eine Erweiterung programmiert. Eine einfache Excel-Access-Applikation hilft zusätzlich, eine Kapazitätsplanung auf Basis der Baan-5-Daten für alle Fertigungskapazitäten aufzubauen.
Selbstläufer Kanban-Artikel
Die Kapazitätsbedarfe für Maschinen und Personal werden jetzt ausgehend von den Bedarfsterminen für jede Fertigungsstufe überwacht. Darüber hinaus wurde im Baan-5-System die Materialbereitstellung (Kommissionier-Reports) für die auftragsbezogen gefertigten Artikel so reorganisiert, dass jetzt Umlagerungsaufträge in die Endmontage nur noch dann erfolgen, wenn eine 100-prozentige Materialverfügbarkeit aller Komponenten für einen Auftrag gegeben ist. Regelmäßig justieren die Planer die Planungs-, Steuerungs- und Dispositionseinstellungen im Baan-5-System mithilfe der APS-Software artikelspezifisch nach.
Ergebnis: Durch das neue logistische Geschäftsmodell stieg der Durchsatz in der Komponentenfertigung ohne Kapazitätserweiterung. „Die Kanban-gesteuerten Artikel sind zu Selbstläufern geworden, die lediglich in regelmäßigen Abständen überprüft und nachjustiert werden müssen”, resümiert Bürger.
Fritz Driescher
Die Fritz Driescher GmbH & Co. KG mit Sitz in Wegbergis ist spezialisiert auf die Entwicklung und den Bau von Schaltanlagen und Schaltgeräten für die Energieversorgung. 2008 erwirtschaftete der familiengeführte Mittelständler einen Umsatz von 40 Mio. Euro und beschäftigte 384 Mitarbeiter.