Die Notwendigkeit der Integration einer hierarchischen Planung
Im täglichen Supply Chain Management wird permanent eine Vielzahl von einzelnen Planungsentscheidungen getroffen -bisweilen mit weitreichenden Folgen. Bildet man diese Entscheidungen in einem hierarchischen Planungsmodell ab, so ist zu erkennen, dass sie auf unterschiedlichen Ebenen getroffen werden. Je nach Ebene unterscheiden sich die Reichweite der Betrachtung und ihr Detaillierungsgrad erheblich. Um ein planerisches Gesamtoptimum zu erzielen ist jedoch die Integration der unterschiedlichen Planungsebenen bzw. deren Planungsprozesse ein entscheidender Faktor zur Steigerung der Qualität der gesamten Supply Chain.
Die richtige Planung und Steuerung des Materialflusses in der Supply Chain ist die unabdingbare Grundlage für ein erfolgreiches Supply Chain Management. Eine solche Planung ist kein einstufiger Prozess, sondern erfolgt in mehreren Schritten, die von der Absatzplanung über die Programm- und Produktplanung zur Feinplanung voranschreiten und sich in ihrer Zeitdimension unterscheiden: Die langfristigste und zugleich auch gröbste Planungsebene ist dabei die strategische Absatzplanung eines Unternehmens. Zu diesen strategischen Entscheidungen gehören insbesondere alle diejenigen, die definieren, welche Märkte man mit welchen Produkten bedienen möchte.
Die feinste und kurzfristigste Ebene ist die unmittelbare Durchführungsebene. Hier werden im Rahmen der Feinplanung z. B. Entscheidungen über Maschinensteuerung und Anlagenbedienung gefällt und Messwerte im Zuge der Betriebsdatenerfassung (BDE) erfasst, die zur Anpassung von Prozessmodellen in der Fertigung und weiteren Controllingzwecken genutzt werden können. Ebenso sind dieser Ebene die ‚Echtzeit- Entscheidungen‘ zuzurechnen, die z. B. im Rahmen der Bestellfreigabe, des Werkstatt- und Transportmanagements oder auch des Kundenauftragsmanagements gefällt werden. Das eine – die strategische Absatzplanung – hat offensichtlich wenig mit dem anderen – der Maschinensteuerung – zu tun. Und dennoch hängt alles zusammen. Deshalb brauchen wir integrierte Planungsprozesse. Fangen wir bei der Absatzplanung an.
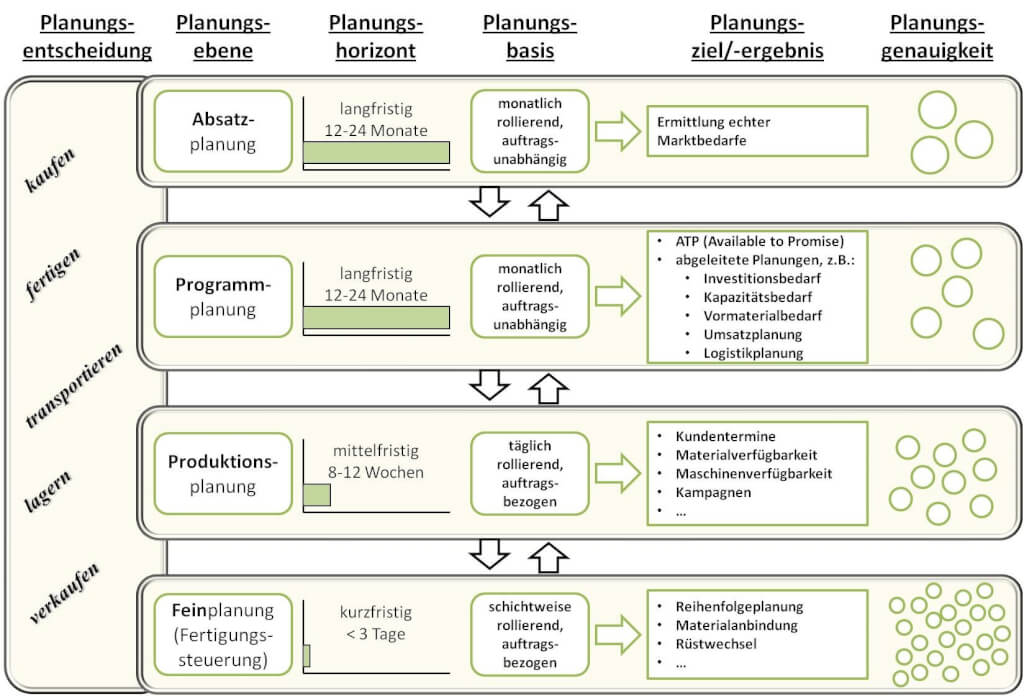
Absatzplanung
Ziel der Absatzplanung ist es, einen ‚unbeschränkten‘ Marktbedarfsplan (mit ‚echten Marktbedarfen‘) zu erstellen. Ein solcher Forecast unterliegt noch keinen Restriktionen. Er beantwortet lediglich die Frage, auf welche Mengen und Bedarfszeitpunkte eines Produktes oder einer Produktgruppe ein Anbieter sich einstellen sollte, damit die voraussichtlichen Marktbedarfe bedient werden können.
Erstellt wird der Forecast als integrierte Prognose, die in der Regel aus der bestmöglichen Kombination unterschiedlichster Informationen besteht. Kombiniert werden technische bzw. statistische Prognosen auf Basis der Verbräuche der Vergangenheit, Informationen des Vertriebs z. B. zu Anläufern, Ausläufern, Aktionen, Projekten, neuen / verlorenen Kunden, regionalen Marktänderungen usw. sowie Informationen von Kunden. Der unbeschränkte Marktbedarfsplan aus der Absatzplanung stellt den Input für die Programmplanung dar.
Programmplanung
Hauptziel der Programmplanung ist es, einen Plan zu erzeugen, der die Möglichkeiten der Produktion und den prognostizierten Marktbedarf optimal ausbalanciert. Zu treffende Entscheidungen lassen sich wie folgt umschreiben: Was, wann und wie viel muss produziert werden unter Berücksichtigung von Kundenvereinbarungen, Kapazitäts- und Materialrestriktionen sowie Bestands- und Auslastungsgrundsätzen?
Ergebnis dieser Überlegungen ist sodann ein unternehmensweit abgestimmter und kommunizierter beschränkter Absatzplan, der im Anschluss wieder der Absatzplanungsebene verfügbar gemacht wird. Erst dann können die Umsatz- sowie die Produktions- und Feinplanung als weitere wesentliche abgeleitete Planungsgrößen erstellt werden.
Produktionsplanung
An die Programmplanung schließen sich Produktionsplanung und Feinplanung an. Sie unterscheiden sich extrem in der Länge ihres Planungshorizontes und dem Detaillierungsgrad ihrer Planungsaussage: Die Produktionsplanung betrachtet einen Horizont von 8 bis 12 oder mehr Wochen, während die Feinplanung häufig nur 2 bis 3 Tage vorausblickt.
Die Produktionsplanung bildet ‚Zeittöpfe‘ (Tag, Woche) und füllt diese mit Jobs (Aufträge, Planaufträge). Dabei wird die Auslastung je Zeittopf angegeben. Wenn nötig, kann die Produktionsplanung auch gegen begrenzte Kapazitäten planen. Der Abgleich zwischen Kapazitätsbedarf und Kapazitätsangebot kann dabei im Allgemeinen nach einfachen Mechanismen oder manuell durch den Planer erfolgen.
Feinplanung
In der Feinplanung spalten sich die Lösungsansätze in zwei grundsätzliche Philosophien: die deterministische Feinplanung und die stochastische Fertigungsflussregelung.
Die deterministische Feinplanung soll eine detaillierte Reihenfolge von Fertigungsaufträgen und Arbeitsvorgängen erzeugen, wenn erforderlich, bis zum einzelnen Stück eines Materials. Diese Reihenfolge soll die Effizienz der Ressourcen maximieren. Der resultierende Produktionsplan basiert auf detaillierten Regeln / Vorgaben und Produktionsbedingungen.
Häufig zu treffende Schlüsselentscheidungen fußen dabei auf der aktuellen und geplanten Verfügbarkeit der benötigten Materialien, den vorhandenen Fertigungsrestriktionen und den aus der Zielhierarchie abgeleiteten Einplanungsstrategievorgaben wie z. B. minimierte Rüstzeit, maximierte Lieferbereitschaft je Arbeitsvorgang oder maximierten Durchsatz. Die Schlüsseloutputs der Feinplanung sind terminierte Start- und Endzeiten für jeden Arbeitsvorgang eines Fertigungsauftrags pro Material und die umfassende Sichtbarkeit von Feinplanungsproblemen im Kurzfristhorizont.
Die systemgestützte automatisierte Erstellung von Feinplänen kann je nach Branche sehr aufwendig sein, da die Restriktionen der Fertigung, die die Produktionsreihenfolge beeinflussen, sehr vielfältig sein können.
Die Anzahl der bestimmenden Faktoren bei der Reihenfolgebildung kann sehr groß und die Interdependenzen dieser Faktoren können sehr vielfältig sein. Oftmals scheuen Unternehmen den Aufwand der Systemmodellierung oder stellen aufgrund der Vielschichtigkeit dieser Thematik das Planungsergebnis in Frage. Die deterministische Feinplanung kämpft nicht nur mit der Vielzahl der Einflussgrößen, die nie vollständig erfasst werden können, sondern auch mit deren Veränderungsdynamik. Diese beiden Faktoren führen dazu, dass Feinpläne oft schon veraltet sind, wenn sie fertiggestellt wurden.
Soll die deterministische Feinplanung durch ein System derart unterstützt werden, dass automatisch gute und machbare Pläne entstehen, so ist besonders auf zwei Aspekte zu achten:
Erstens sollte das Regelwerk zur Reihenfolgebildung, welches im System hinterlegt wird, so schlank wie möglich sein. Es gilt, die wesentlichen Einflussfaktoren zu bestimmen und deren Zusammenspiel zu definieren. Dabei sollte man nicht vergessen, dass ein Großteil der Regeln ja sowieso schon existiert, nämlich in den Köpfen der Planer. Dieses Wissen gilt es also zu sammeln, zu strukturieren und im System zu hinterlegen.
Der zweite Punkt betrifft die Art der Einführung einer systemgestützten Feinplanung. Bei der Einführung sollten die Planungsschritte, die den Feinplan generieren, quasi halbautomatisch durchgeführt werden. Der Planer stößt dabei jeden Planungsschritt manuell an und kann das Ergebnis seines Tuns beobachten. Dies dient der Verifizierung der hinterlegten Regeln und schafft für den Zeitpunkt, ab dem der Feinplan vollautomatisch generiert wird, beim Anwender das nötige Vertrauen in die Planungsergebnisse und damit die erforderliche Akzeptanz gegenüber dem System.
Die zweite Feinplanungsphilosophie, die stochastische Fertigungsflussregelung, geht von der Erkenntnis aus, dass die Produktion einen im Detail nicht planbaren Prozess darstellt, bei dem Kapazitätsauslastung, Termintreue, Durchlaufzeit und Umlaufbestände nur in einem statistischen Zusammenhang zueinander stehen.
Aufgabe der stochastischen Fertigungsflussregelung ist es, einen definierten Umlaufbestand vor allem an Engpassarbeitsplätzen durch geeignete kurzfristige Regelung des Auftragszulaufs oder des Kapazitätsangebotes möglichst konstant zu halten. Während die Regelung des Auftragszulaufs selten möglich ist, besteht in Produktionsunternehmen mit diskreter Fertigung zumeist die Möglichkeit einer gewissen Kapazitätsflexibilisierung.
Auch bei der stochastischen Fertigungsflussregelung können gewisse Restriktionen, wie Rüstreihenfolgen oder ein Produktmix, berücksichtigt werden. Stichworte hierzu sind Heijunka-Boards, Sequencer und EPEI-Werte. Zahlreiche Untersuchungen und Projekte haben gezeigt, dass sich eine stabile Fertigungssteuerungssituation mittelfristig dann einstellt, wenn als übergeordnetes Prioritätskriterium der einzelnen Fertigungsaufträge die FIFO-Regel (first in, first out) konsequent eingehalten wird. Die stochastische Fertigungsflussregelung ist deutlich weniger aufwendig als die deterministische Feinplanung.
Die Integration der Planungsebenen
Wie man die Integration der unterschiedlichen Planungsebenen ausgestaltet, entscheidet maßgeblich über die Planqualität. Nicht selten findet man in der Praxis den Fall vor, dass die Produktionsplanung vollkommen autark agiert und die Absatzplanung mehr oder weniger ignoriert. Als Grund dafür erkennt man oft, dass die Ergebnisse der Absatzplanung für die Zwecke der Produktionsplanung schlichtweg ungeeignet sind, z. B. wenn sie eine reine Budgetplanung repräsentiert, die nichts mit einer echten „Marktbedarfsplanung“ zu tun hat. In einem solchen Falle gibt es einen harten Schnitt zwischen der Absatzplanung und den darunter liegenden Planungsebenen. Abstimmung zwischen den Ebenen gibt es dann erst wieder im Rahmen des Auftragsbestätigungsprozesses, wenn der Vertrieb die gewünschte Lieferbereitschaft einfordert und die Produktionsplanung erklären muss, warum nun für einen bestimmten Kundenauftrag die geforderte Menge nicht termingerecht verfügbar ist.
In einem über die Ebenen der Planungshierarchie hinweg durchgängigen Basis-Planungslauf gilt es, Informationen in beide Richtungen der Hierarchie zu kommunizieren.
Die Absatzplanung übergibt den Marktbedarfsplan gegen infinite Kapazität an die Programmplanung. Diese wiederum nimmt basierend auf diesen Informationen eine Kapazitätsbetrachtung auf grober Ebene gegen begrenzte Kapazität vor, was dann im nächsten Schritt Einfluss nimmt auf diverse abgeleitete Planungen, z. B. Personal- oder auch Umsatzplanung. Die Ergebnisse dieses Planungsschrittes werden dem Vertrieb als Plan zur Verfügung gestellt.
Fazit
In manchen Branchen ist die vollständig durchgängige hierarchische Planung zur Erzielung des größtmöglichen wirtschaftlichen Erfolgs nicht unbedingt ein „Muss“! Entscheidend ist, dass ein Unternehmen aber den Planungsaufwand identifiziert und betreibt, der nötig und vertretbar ist, um mit ausreichender Planqualität die formulierten unternehmerischen Ziele erreichen zu können. Je höher die Variantenbildung – auch und insbesondere innerhalb einer Serie – und je vernetzter die vorgelagerten Fertigungs- und Supply Chain Prozesse, desto wichtiger ist ein integrierter Planungsprozess.