Die Leistungsfähigkeit der Supply Chain steigern
Von Prof. Dr. Götz-Andreas Kemmner
Die Wirtschaftlichkeit der Supply Chain zu steigern und gleichzeitig die Planungs- und Dispositionsabläufe möglichst stark zu automatisieren stellt eine Herausforderung für jedes Supply Chain Management dar. Mit Hilfe der COLT-Analyse kann dieses Ziel konsequent und kontinuierlich angesteuert und zum ERP-Performance-Management ausgebaut werden.
Unter dem COLT-Wert versteht man die kostenoptimale standortbezogene Umschlagshäufigkeit (engl. Cost Optimal Location Turn Rate). In diese Kenngröße fließen die drei wichtigsten Parameter jeder Supply Chain, nämlich der (Durchschnitts-)Bestand, die Lagerkosten und die Lieferbereitschaft ein.
Ein COLT für alle Fälle
Der COLT-Wert ist eine Leistungskennzahl (engl. KPI oder Key Performance Indicator) und gibt nicht einen Ist-Wert, sondern einen Ziel- oder Richtwert an, der in einer Wertschöpfungskette erreichbar sein sollte, wenn alle ERP-Parameter wirtschaftlich optimal eingestellt sind und „intelligent“ geplant wird. „Intelligente Planung“ bedeutet in diesem Zusammenhang, dass seitens der Anwender an den Dispositionsvorschlägen des ERP- oder Dispositionssystems so viel wie nötig und so wenig wie möglich verändert wird. In der Praxis kann es immer wieder erforderlich werden, dass Anwender die Dispositionsvorschläge des ERP-Systems trotz optimal eingestellter Parameter übersteuern müssen, da sie über Informationen verfügen, die dem System nicht vorliegen. Die Gefahr ist allerdings groß, dass Anwender aus jahrelanger Erfahrung und Gewohnheit auch dann in die Dispositionsvorschläge eingreifen, wenn dies eigentlich nicht notwendig wäre. Den notwendigen vom unnötigen Eingriff zu unterscheiden, macht hier die „Intelligenz“ der manuellen Eingreifens aus. Anwendereingriffe können allerdings auch notwendig werden, weil ein ERP-System nicht ausreichend fein eingestellt werden kann. Im diesem Fall muss gegebenenfalls ein ERP-Optimierungstool , wie z. B. DISKOVER SCO der SCT GmbH, die Dispositionsaufgabe übernehmen.
Von ALT zu COLT
Wir werden später noch feststellen, dass es gewisser Voraussetzungen bedarf, einen COLT-Wert für eine Bestandsstufe, ein Werk oder einen Werksverbund zu ermittelt. Ehe man den COLT-Wert und damit die eigene Zielvorgabe ermittelt, stellt sich die Frage, wo ein Unternehmen, ein Standort oder eine Fertigungsstufe heute stehen. Dazu lässt sich auf recht einfache Weise ein ALT-Wert ermitteln. ALT steht für Actual Location Turn Rate oder in Deutsch tatsächliche standortbezogene Umschlagshäufigkeit. Dieser Wert errechnet sich als Quotient aus den Verbrauchswerten und dem mittleren Bestandswert der betrachteten Einheit. Er bewertet die Qualität des Zusammenspiels aus ERP-System und Disponenten bzw. Fertigungssteuerern.
Letztlich kann und muss man für eine existierende Wertschöpfungskette einen weiteren Kennwert ermitteln, die Technical Turn Rate (TTR). Der TTR-Wert beschreibt, zu welchen Umschlagshäufigkeiten man gelangen würde, wenn man sich strikt an die Dispositionsvorschläge des ERP-Systems, so wie sie heute eingestellt sind, halten würde.
Zwischen COLT-Wert, TTR-Wert und ALT-Wert liegen oft Welten und das aus zwei Gründen:
Zum einen wird, wie bereits angesprochen, häufig auch unnötigerweise in die vom ERP-System automatisch generierten Bestellvorschläge manuell durch die Disponenten eingegriffen. Zum anderen sind die Dispositions-Parameter allzu häufig völlig unterpflegt und somit veraltet. Was dann natürlich nicht gerade positive Effekte auf die Zuverlässigkeit der automatisch generierten Bestellvorschläge hat und ein gewisses Misstrauen der Disponenten rechtfertigt. Letzten Endes beißt sich die Katze hier in den Schwanz: Die Parameter im ERP-System sind nicht richtig gesetzt oder veraltet, die Bestellvorschläge entsprechend unzureichend und durch das ewige „Nachbessern“ in den Vorschlägen nimmt sich niemand die Zeit, die Parameter zu pflegen.
Wenn das Kaliber nicht stimmt
Wie errechnet man nun den COLT-Wert für die bestehende Supply Chain Konfiguration? Die Grundvoraussetzung dafür sind dynamische, zeitbasierte Werte, da nur diese ein realistisches Bild der Situation spiegeln. Die häufig verwendeten statischen Berechnungen, zum Beispiel ausgehend von Wertstromanalysen, gehen leider an der Realität vorbei, da die wenigsten produzierenden Unternehmen oder Großhändler mit statischen Zu- und Abflüssen in ihrer Wertschöpfungskette zu tun haben (s. Abb. 1).
.
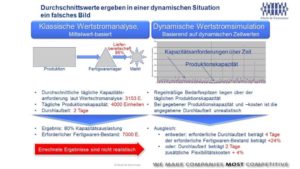
Das Beispiel aus Abb. 1 zeigt, dass eine klassische statische Wertstromberechnung zu völlig falschen Kennwerten führen würde.
Eine einfache Wertstromberechnung ist auch deswegen falsch, will die Zahl der Parameter, die Einfluss auf die Dispositionsentscheidung und damit letztlich den Bestand, die Lieferbereitschaft und die Kosten einer Wertschöpfungskette nehmen, sehr groß ist und weit über die Parameter hinausgeht, die der Anwender „an der Oberfläche“ seines ERP-Systems überhaupt einstellen könnte.
Die folgende Liste von Parametern, die in unterschiedlichen ERP-Systemen unterschiedlich bezeichnet werden, vermittelt davon vielleicht einen kleinen Eindruck:
- Rundungswerte
- Prognosegewichtung
- Sicherheitsbestand
- Prognoseverfahren
- Prognosezeitraum
- Sicherheitsbestandsverfahren
- Abweichungsverfahren
- Prognoseverteilung
- Verbrauchs- und Anpassungsverfahren
- Rückwirkende/vorausgreifende Verbrauchsverfahren
- Periodenübergreifende Verbräuche
- Berechnungsverfahren der Grundverbräuche
- Sicherheitsbestandsfaktor
- Mindestbestand
- Externer MRP Typ
- MRP Verfahren
- Losgrößenverfahren
- Fixe Bestellkosten
- Lagerkosten
- Vorkaufszeitraum
- Gesamt-Durchlaufzeit
- Auftragseröffnungs-Zeitraum
- Auftrags-Durchlaufzeit
- Lieferzeit
- Wareneingangsbezogene Bearbeitungszeit
- Mindestlosgröße
- Losgrößeninkrement
- Maximale Losgröße
Wenn die einfache Arithmetik der Wertstromberechnung schon nicht ausreicht, so könnte man meinen, dass man wenigstens aus dem ERP-System selbst die Zielwerte für den Lagerumschlag ableiten kann. Schließlich können ERP-Systeme die Bestandsentwicklung eines jeden einzelnen Artikels oder Materials in die Zukunft hochrechnen und berücksichtigen dabei alle eingestellten Dispositions- und Logistik-Parameter. Bei dieser Hochrechnung im ERP-System wird allerdings unterstellt, dass Bedarfe so wie vorhergesagt eintreffen und es keinerlei Störungen gibt.
Unter diesen fiktiven Randbedingungen kann man aus den in die Zukunft hochgerechneten Dispositionsvorschlägen des ERP-Systems tatsächlich einen Lagerumschlagswert zu ermitteln. Dieser Wert ist aber wegen der bereits genannten Gründe nur rein theoretischer Natur und in der Praxis allenfalls zufällig erreichbar. Die sich ergebende „Fictional Turn Rate (FTR-Wert), wird in der Praxis gerne als Zielwert für die Anwender herangezogen, hat aber überhaupt keinen Bezug zur Realität!
Es gibt leider nur einen Ansatz, wie man zu realistischen und belastbaren Kennwerten und Zielwerten gelangen kann: durch eine dynamische Wertstromsimulation unter Beachtung von Vergangenheitsdaten.
Das richtige Kaliber ermitteln
Mittels einer dynamische Wertstromsimulation, basierend auf den realen historischen Bedarfsverläufen, kann man das Verhalten eines jeden Einkaufsteils und jedes Fertigteils individuell simulieren. Dazu nimmt man klassischerweise die täglichen Kundenauftrags- oder ersatzweise die Verbrauchswerte der letzten zwölf Monate, simuliert dagegen das Prognose- und Dispositionsgeschehen und prüft, welche Kennwerte sich hinsichtlich Durchschnittsbestand, Kosten und Lieferbereitschaft hätten erreichen lassen.
Einer solchen Simulation kann man darüber hinaus mit auf den Weg geben, welche Planungs- und Dispositionsparameter sie optimieren und was das eigentliche Optimierungsziel sein soll:
- Erreichen des Soll-Lieferbereitschaftsgrads bei geringstmöglichem Bestandsniveau
- Erreichen des Soll-Lieferbereitschaftsgrads bei geringstmöglichen Kosten;
(auf dieses Ziel hin wird bei der Ermittlung des COLT-Wertes optimiert) - Erreichen der niedrigsten Kosten bei gleichzeitigem Kompromiss zwischen Lieferbereitschaftsgrad und Bestandsniveau
Als Ergebnis der dynamischen Wertstromsimulation ergeben sich eine Vielzahl weiterer Leistungskennzahlen sowie artikelbezogene Umschlagsraten in Relation zur gewünschten Lieferbereitschaft. Geht man in eine solche Simulation mit den bestehenden ERP-Einstellungen, erhält man als Ergebnis die oben bereits beschriebene Technical Turn Rate (TTR-Wert). Dreht man an den Parametern, im Bestreben die Einstellungen zu optimieren, kann man die Konsequenzen ermitteln, die sich durch veränderte Parametereinstellungen ergeben würden. Auf diese Weise lassen sich die Performance und Wirtschaftlichkeit der Wertschöpfungskette systematisch verbessern und die zugehörigen COLT-Werte ermitteln.
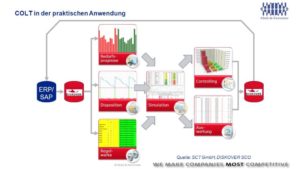
Was hier vielleicht theoretisch klingen mag, wird bereits bei vielen Unternehmen, auch mittelständischen, erfolgreich genutzt (s. Abb. 2). Voraussetzung dafür ist allerdings ein geeignetes System, das seine Daten aus dem ERP-System erhält und damit die entsprechenden Simulationen im Hintergrund durchführen kann.
Richtig zielen mit dem COLT
Wir wissen nun, wie man den COLT-Wert erstellt und was der eigentliche Sinn der Übung ist, nämlich die Optimierung der gesamten Supply Chain. Eigene Berechnungsbeispiele aus der Praxis verschiedener Unternehmen sollten die Anwendung verdeutlichen.
Fangen wir einmal mit der Fragestellung an, wie gut unsere Supply Chain arbeiten könnte, wenn wir nur genau wüssten, was auf uns zukommt. Genau das ist es ja, was die ERP-Systeme den Disponenten vorgaukeln und die Disponenten wissen, dass es genau so nicht kommen wird.
Das Simulationsbeispiel (s. Abb.3) vergleicht den aktuell erreichten Durchschnittsbestand eines Werkes mit dem Durchschnittsbestand, der erreichbar wäre, wenn die Prognosewerte, die das ERP-System erwartet, auch genau kommen und die Fertigungs- und Bestellvorschläge des ERP-Systems exakt umgesetzt würden; sozusagen ein märchenhafter Zustand: die Fictional Turn Rate, der FTR-Wert.
Es zeigte sich in diesem Falle, dass z.B. die Fertigwarenbestände um 73% hätten gesenkt werden können. Auf das gesamte betrachtete Werk bezogen, hätte sich der Lagerumschlag von 23 (ALT-Wert) auf 50 (FTR-Wert) erhöht.
Völlige Phantasie? Richtig, aber die Phantasie des ERP-Systems! Diese Zielwerte für Durchschnittsbestände und Lagerumschläge hätten sich ergeben, wenn man mit den Daten des ERP-Systems in die Zukunft weitergerechnet und hieraus einen Zielwert für das Werk bzw. die Disposition ermittelt hätte.
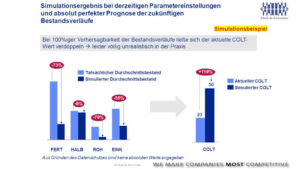
Mit der beschriebenen dynamischen Wertstromsimulation kann man die Dinge realistischer betrachten. Abb. 4 zeigt für dasselbe Werk das Optimierungspotenzial, das unter Verwendung der vorhandenen Dispositionseinstellungen und logistischen Parameter realistischerweise zu erreichen wäre. Hier beträgt das Bestandsreduzierungspotenzial bei Fertigwaren nur noch 2% (statt 73%), allerdings immer noch 33% (statt 55%) bei Einkaufsteilen. Der Lagerumschlag könnte von 23 (ALT-Wert) auf 27 (TTR-Wert) verbessert werden. Diese Simulation zeigt, dass bereits bei bestehender Parametereinstellung im ERP-System sich eine bessere Performance ergeben würde, wenn die Anwender seltener in die Dispositionsvorschläge des Systems eingreifen würden. Der Lagerumschlag von 27 stellt noch lange nicht den kostenoptimalen COLT-Wert dar, sondern erst einmal nur den TTR-Wert, der sich eben aus den aktuellen Parametereinstellungen ergibt.
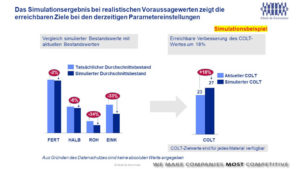
Eine Verbesserung des Lagerumschlags um 18% ist ganz sicher kein zu verachtendes Potenzial, liegt aber deutlich entfernt von den theoretischen Wert 50, der als Zielvorgabe für die Disposition völlig irrwitzig gewesen wäre.
Mit Simulationen der beschriebenen Art lassen sich auch Zielkonflikte zwischen verschiedenen Zielgrößen analysieren, um daraus die richtigen Einstellparameter abzuleiten. Das Beispiel (s. Abb. 5) zeigt, wie sich in einem Produktionsbereich die Zahl der Fertigungsaufträge eines Jahres und der durchschnittliche Fertigwarenbestand hinter der Fertigung veränderten, wenn mit unterschiedlichen Losgrößen gefertigt würde. Hier zeigt sich deutlich, dass es sinnvoll wäre, die Fertigungslosgrößen auf ein Viertel der heutigen Losgröße zu verringern. Dies würde im Jahr nur einen Fertigungsauftrag pro Tag mehr erfordern, aber knapp 600 T€ an Liquidität freisetzen.
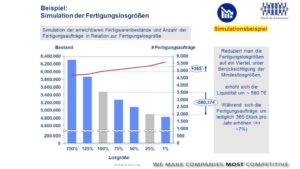
Treffsicher durch regelmäßige Pflege
Die Simulationsbeispiele mögen einen ersten Eindruck davon geben, wie man mittels Simulation von COLT-Werten an der kontinuierlichen wirtschaftlichen Verbesserung der Supply Chain arbeiten kann. Im einfachsten Anwendungsfall lässt sich für einen einzelnen Artikel ermitteln, wie sich Veränderungen von Dispositionsparametern auf die Kennwerte dieses Artikels realistischerweise, und nicht von ERP-System idealisiert hochgerechnet, auswirken würden. Anstatt nur für einen Artikel kann man die COLT-Simulation auch direkt für alle Artikel oder zumindest bestimmte Artikelgruppen durchführen, um die Gesamtauswirkungen unterschiedlicher Dispositionseinstellungen zu ermitteln.
Die COLT-Simulation kann jedoch noch weiterreichen und für Parametereinstellungen direkt den optimalen Einstellwert ermitteln. Die automatische Ermittlung optimaler Einstellwerte ist von großer Bedeutung, um zu nachhaltig wirksamen Verbesserungen und damit zu nachhaltig erreichbaren COLT-Werten zu gelangen. Es genügt nicht, einmalig Parametereinstellung für unterschiedliche Artikel zu optimieren und fest einzustellen. Über Dispositionsregelwerke müssen die Einstellungen immer wieder nachgepflegt werden und bestimmte Parameter, wie z.B. solche, die die Prognose- und Sicherheitsbestandsberechnungen steuern, müssen immer wieder optimiert werden. Deshalb nutzt man in vielen Fällen ein solches Simulationssystem nicht nur einmalig, sondern als laufendes Optimierungsinstrument für ein ERP-System und gelangt so zu einer ERP-Performance-Management-System (vgl. Abb 6).
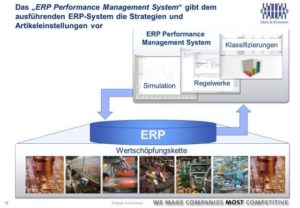
Wie steht es bei Ihnen mit dem ERP-Performance-Management? Wursteln Sie sich noch durch oder optimieren Sie schon?
Bild von THAM YUAN YUAN auf Pixabay