Advanced Planning & Scheduling bei Leuze electronic
von Michael Schüler, Leuze electronic, und Bernd Reineke
Leuze electronic optimiert seine Einkaufs- und Produktionsentscheidungsgrundlagen nicht mehr wie in der Vergangenheit im ERP-System, sondern auf Basis des Advanced Planning & Scheduling (APS) Tools DISKOVER von SCT. Dieses liefert deutlich präzisere Absatzprognose-Ergebnisse. Überzeugt ist Leuze electronic nicht nur von den ausgeklügelten Regelwerken und Dispositionsalgorithmen – auch die tägliche Arbeit mit dem Tool gestaltet sich sehr praxisnah und ist dadurch äußerst komfortabel. Seine Einführung wurde von der Unternehmensberatung Abels & Kemmner begleitet.
Leuze electronic ist seit über 50 Jahren Experte und Hersteller von messenden und schaltenden Sensoren, von Lösungen für die Bildverarbeitung und Datenübertragung sowie Komponenten und Systemen für die Arbeitssicherheit. Das Unternehmen agiert heute global und bietet seinen Kunden ein ausgedehntes Vertriebs- und Servicenetz. Über 1200 Sensor People sind an 24 Standorten weltweit sind in Entwicklung, Produktion, Vertrieb und Service tätig, unterstützt von mehr als 40 Vertriebspartnern weltweit. Leuze electronic erzielte 2018 einen Rekordumsatz von 214 Millionen Euro.
Lagerbestand und Liefertreue planerisch verzahnen
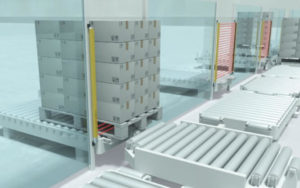
Um die hohe Lieferbereitschaft des Unternehmens weiter zu optimieren, ohne dabei zu viel Kapital in Beständen zu binden, suchte Leuze electronic nach einem Weg, die Lagerbestandsentwicklung im Verhältnis zur geforderten Liefertreue transparenter als bisher darstellen zu können. Nur so können fundiertere Entscheidungen zur Justage des Lieferbereitschaftsgrads auch auf Basis von Kapitalbindungsentscheidungen getroffen werden. Das ist für eine solide Unternehmensplanung unerlässlich. So können auch die Bestände unter Vorgabe entsprechender KPIs gesamtunternehmerisch betrachtet werden und sind damit besser steuerbar.
Dies war mit dem bislang im Einsatz befindlichen ERP-System nicht hinreichend möglich. Die bereitgestellten Prognoseverfahren waren vergleichsweise einfach ausgelegt. Es war zwar möglich, den aktuellen Lieferbereitschaftsgrad zu ermitteln und auf beispielsweise mindestens 95% als Vorgabe auch zu steuern. Es konnte aber niemals transparent dargestellt werden, welche Materialen in welcher Menge als Lagerbestand dafür vorzuhalten sind.
Parallele Einführung des ERP- und APS-Systems
Ziel war, die beiden Key Performance Indikatoren ‚Lagerbestand‘ und ‚Lieferbereitschaftsgrad‘ deutlich besser als in der Vergangenheit in Relation zu bringen sowie diese transparent und nachvollziehbar zu steuern. Mit seiner Entscheidung, in seiner Firmenzentrale auf SAP umzustellen hätte Leuze electronic durchaus auch das Planungstool von SAP einsetzen können. Da es aber teurer war und man fest davon überzeugt war, dass APS-Tools generell genauer auf den Bedarf zugeschnitten sind, entschied man sich für das Tool DISKOVER von SCT. Dieses stellte sich als bestens geeignet heraus, die beiden KPIs exakt in Relation zu setzen sowie unterschiedliche Szenarien auf Basis zahlreicher Prognose- und Sicherheitsbestandsverfahren zu simulieren. In der Regel führt dies zu sinkenden Beständen bei gleichbleibender oder sogar noch gesteigerter Lieferbereitschaft.
Nachdem also die Entscheidung für sowohl ERP- als auch APS-System gefallen war, führte Leuze electronic am Stammsitz in Owen beide Lösungen parallel ein. „Die Einführung von DISKOVER SCO war allerdings deutlich einfacher als die ERP-Einführung“, erklärt Michael Schüler, Head of Supply Chain Management bei Leuze electronic. Zum einen, da das APS-System nur eine Teilfunktion des gesamten betrieblichen Ablaufs abbilden muss. Zum anderen aufgrund der hohen Flexibilität des DISKOVER-Entwicklungsteams, welches immer schnell und agil auf die Anforderungen von Leuze electronic im Rahmen des Einführungsprojektes reagiert hatte. „Das Einführungsprojekt war pünktlich zur Scharfschaltung des SAP-Systems umgesetzt. Zurückzuführen war dies nicht zuletzt auf die hohe Qualifikation des Einführungsteams sowie die gute Beratung von Abels & Kemmner “, sagt Schüler. Am 1. August 2018 wurden beide Systeme parallel live geschaltet. Rund sechs Monate später war die Einführung von SAP weitestgehend abgeschlossen. Ab sofort ist man in der Lage, die Potenzialermittlung für weitere Bestandsoptimierungen anzugehen. Hierfür wurde die Art und Weise, wie das Potenzial im APS-System ausgewiesen wird, exakt auf den Bedarf von Leuze electronic angepasst.
Standortübergreifende „Inter-Company“ Funktionen
Von großem Nutzen für Leuze electronic sind dabei insbesondere die werksübergreifenden „Inter-Company“-Planungsfunktionen des neuen APS-Tools. Diese nutzt Leuze electronic für Lichtschranken, Barcodeleser und weitere Geräte, die von der Leuze assembly, einem Leuze-Tochterunternehmen in Unterstadion bei Ehingen bezogen werden. Der transparente Datenaustausch lässt sich zwischen verschiedenen ERP-Systemen, die ihre Dispositionsverfahren mittels DISKOVER nahtlos so synchronisieren wollen, so organisieren, als wäre alles eine einzige Fabrik. Voraussetzung hierfür ist der flexible Support von ERP-Systemen unterschiedlichster Auslegung. Diese Flexibilität und Integrationsfähigkeit weist auch das APS-System bei Leuze auf, denn am Standort Unterstadion kommt weiterhin InforLN zum Einsatz.
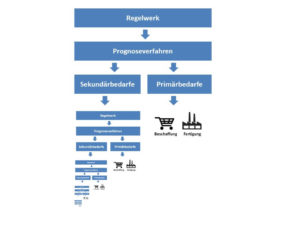
In allen Unternehmen wird heute durchgängig auf Basis der Stückzahlprognose der zukünftig verkauften Produkte als oberste Ebene (Primärbedarfe) geplant. Auf Basis von Stücklisten lösen diese Sekundärbedarfe für beispielsweise Gehäuseteile oder Stecker aus. Da auch bei der Leuze assembly das Tool DISKOVER zum Einsatz kommt, können diese Prognosen nun nahtlos vom Stammhaus übergeben und auf alle zu fertigenden Einzelteile heruntergebrochen werden. Diese werden im gleichen Planungslauf eigenständig disponiert – das heißt, entkoppelt vom Endprodukt, so dass für jedes Teil einzeln die optimale Entscheidung getroffen werden kann. Die über diese „Inter-Company“- Funktionen des APS-Tool virtuell zu einer Fabrik verknüpften Fertigungsstandorte oder auch Distributionshubs müssen demzufolge nicht die gleiche ERP-Struktur haben. Ein werksübergreifendes Dispositionsmanagement für Einkauf und Produktion sind durch den parallelen Betrieb des APS-Tools möglich.
Zukünftig kann auch die S&OP-Planung auf das im APS-System integrierte Budget- und Absatzplanungsmodul umgestellt werden, indem die Vertriebsmitarbeiter die Daten direkt in der Maske des APS-Tools bearbeiten und damit quasi die Prognosen automatisch um ihre Absatzplanung anreichern. Inwieweit diese Daten im APS-System übernommen werden, entscheidet jedes Unternehmen beziehungsweise die an diesem Prozess beteiligten Entscheider frei. Verändert sich bei größeren Kunden unterjährig die Umsatzprognose stärker, als automatisch prognostiziert, können diese Daten im APS-Tool auch über eine zusätzliche Sonderbedarfsplanung eingepflegt werden. Diese praxisnahe Funktion wurde eigens für spezifische Aktionen, neue Einlistungen oder andere große Veränderungen der Kundenbeziehungen implementiert.
Je nachdem, wie das Zusammenspiel zwischen Absatzprognose, -plan und Sonderbedarf im APS-System eingestellt ist, plant das Tool täglich neu – einschließlich der im ERP-System neu erfassten Bestellungen, gegebenenfalls angepassten Stammdaten und Parameter. Beim Erstabgleich der Ende 2018 noch klassisch umgesetzten vertriebsseitigen 2019er-Jahresabsatzplanung mit der automatischen Prognose des Operations-Teams war die Korrelation der Prognose von DISKOVER mit der vertriebsseitigen Absatzplanung deutlich erkennbar. Es gab von Anfang an nur minimale Abweichungen. Die im APS-System hinterlegten Algorithmen erkennen auf Basis der historisch gesammelten „Big Data“ sehr gut automatisch, wie sich die Absatzverläufe zukünftig voraussichtlich entwickeln werden.
Management by Exception
Planerisch braucht man künftig sowohl im Vertrieb als auch in der Disposition im Grunde nur noch diese Ausnahmefälle näher zu betrachten. Beispielsweise indem der Vertrieb über monatlich automatisch versendete Berichte angetriggert wird, um Besonderheiten mittels der Sonderplanungsmöglichkeiten zu melden. So könnte die gesamte Unternehmensorganisation flexibel auf Veränderungen im Vertrieb reagieren. Durch Konzentration auf diese wenigen Ausnahmen lässt sich der gesamte Planungsaufwand zum Abgleich von Vertriebsabsatzplanung mit der Disposition deutlich reduzieren.
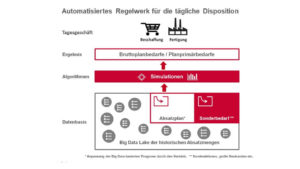
Im nächtlichen MRP-Lauf (Material Requirements Planning) werden vom APS-System – täglich neu und vollständig automatisiert – Bestell- und Fertigungsvorschläge unter Berücksichtigung von Kundenwunschmengen und -terminen sowie Eindeckzeiten und Mindestbestellmengen ermittelt. Fertigungsplaner und Einkaufsdisponenten gleichen dies dann mit ihren Vorschlagslisten, die im aktuellen Planungshorizont liegen, ab. Erscheint der Bestell- und/oder Fertigungsbedarf – der bereits im APS-System auf Material- und Maschinenverfügbarkeit hin geprüft wurde – plausibel, wird er im APS-System als ToDo ‚fixiert‘. So kann dieser mit einem Mausklick ins ERP-System übergeben werden. Von da an wird der Beleg wieder im ERP-System als Einkaufs- oder Fertigungsauftrag verwaltet.
Ideale Unterstützung verschiedenster betrieblicher Abläufe
Können die Vorgaben des Vertriebs lediglich auf Produktgruppenebene abgegeben werden, kann das APS-Tool diese auf Basis prozentualer Verteilungen auf die einzelnen Produkte der jeweiligen Gruppe umrechnen. So kann jede einzelne Komponente eines jeden Produkts auf Basis der jeweils hinterlegten Stücklisten neu berechnet werden. Das erleichtert die Einplanung neuer Vertriebskanäle deutlich, da man die bislang erzielten Absatzverteilungen innerhalb einer Gruppe entsprechend auch beim neuen Vertriebskanal – mitunter justiert – anwenden kann. „An den lösungsorientierten Features von DISKOVER SCO kann man gut erkennen, dass das APS-Tool auf Basis von Praxiserfahrung entstanden ist“, erklärt Schüler.
Mächtige Regelwerke und umfassende Simulationsfunktionen
Ein wichtiger Grund für den Einsatz des neuen APS-Systems liegt vor allem in den umfassenden Simulationsfunktionen, mächtigen Regelwerken, den Möglichkeiten zur Artikelklassifizierung sowie der automatisierten Parameterpflege. All diese Funktionen ermöglichen es Unternehmen, jede Komponente ohne großen Aufwand, bis ins Detail exakt zu planen, so dass Bestände nicht mehr nach Bauchgefühl, sondern auf Basis belastbarer Fakten separiert nach Primär- und Sekundärbedarfen geplant werden können. Im Regelwerk des eingesetzten Tools kann man unter anderem gewünschte Eindeckzeiten mit zu fertigenden Mindeststückzahlen in Verbindung bringen, wodurch die Effizienz der Produktion automatisch optimiert wird. Voraussetzung für eine exakte Prognose und optimierte Disposition ist allerdings, dass die Stammdaten und Dispo-Parameter im System alle korrekt eingegeben sind. Deren Überprüfung durch Expertenlogistische Entkopplungspunktanalysen oder Lagerhaltungsstrategien nach ABC/XYZ-Analysen sind unerlässlich und eine wichtige Voraussetzung für eine erfolgreiche APS-Einführung.
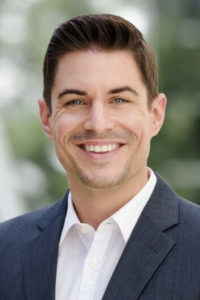
„Im Ergebnis haben wir dank der umfassenden Regelwerke und Simulationsfunktionen von DISKOVER SCO heute eine deutlich genauere Prognose als Dispositionsgrundlage und können genau evaluieren, wie sich Bestände bei sich ändernden Lieferbereitschaftsgraden verändern würden. Dies in einem standardisierten Prozess mit gleichen Werkzeugen über alle Standorte hinweg und unabhängig von den zum Einsatz kommenden ERP-Systemen“, resümiert Schüler. Reduziert wurde auch der operative Aufwand durch die Verwendung automatisierter Triggerfunktionen für spezifische Aufgaben, wie beispielsweise die Aufforderung zur Meldung von Sonderbedarfen oder die regelmäßige Überprüfung teurer Mindestbestände. Durch den Aufbau eines umfangreichen Kennzahlenarchivs können dem Management die wichtigsten logistischen Kennzahlen unter stets einheitlichen Ermittlungswegen regelmäßig übergeben werden. Ergeben sich Abweichungen vom Zielkorridor, können diese ereignisorientiert versandt werden. Das erleichtert das Controlling des Dispositionsmanagements deutlich.
„Auf Basis dieser Kennzahlen können wir bereits erkennen, dass Leuze electronic bis heute bei gleichbleibendem Lieferbereitschaftsgrad rund 14 Prozent der Bestände nachhaltig abbauen konnte. Und dies alleine auf Basis transparenterer Informationen, genauerer Parametereinstellung und differenzierterer Lagerhaltungsstrategien“, kalkuliert Dr. Bernd Reineke, geschäftsführender Gesellschafter bei Abels & Kemmner. Er begleitete die Einführung des APS-Tools bei Leuze electronic aktiv und wird auch in Folgeprojekten weitere nachhaltige Bestandssenkungspotenziale aufdecken und umsetzen. „Wir gehen davon aus, dass wir durch verschiedene weitere Maßnahmen den Bestand um weitere 10 Prozent senken können.“
Vereinfacht auch die Planung neuer Logistik-Hubs
In der Zukunft ist der Aufbau eines Logistik-Hubs in Singapur geplant, von dem aus der asiatische Raum noch besser versorgt werden soll und der für seine Disposition ebenfalls das neue APS-Tool nutzen soll. Aus der Historie von DISKOVER heraus kann dabei der neue Logistik-Hub von Anfang an optimal bestückt werden, da die Regelwerke für passende Mindestbestände quasi automatisch übernommen werden können. APS-Tools können folglich auch sehr einfach alle Entscheidungsgrundlagen liefern, die man benötigt, um verteilte Distributionsstandorte und Lagerstätten auf- oder abzubauen.