Unternehmen haben oft mehrere Tausend bzw. Zehntausende Artikel zu disponieren und entsprechend viele Dispo Stammdaten zu optimieren, jedoch fehlen meist u.a. Möglichkeiten zur Simulation und Regelwerke. Hier gibt es je nach ERP System 20 – 100 Dispoparameter pro Artikel, die gesetzt werden müssen und regelmäßig auf ihre Richtigkeit und Konsistenz überprüft werden müss(t)en. Dies manuell zu tun ist eine Sisyphusarbeit. Dennoch müssen die Parameter gesetzt werden, um die Lieferbereitschaft hoch zu halten und die Bestände nicht explodieren zu lassen. Wie macht man das am besten und vor allem auch nachhaltig?
Als ich Ende der Neunziger Jahre als Unternehmensberater meine berufliche Tätigkeit begann, waren Firmen gerade dabei sich vorzubereiten auf das Jahr 2000 sowie auf die Einführung des Euros. Und in viele Firmen waren dies entscheidende Argumente, ein neues ERP-System einzuführen. Ein wesentlicher Punkt dabei war die Übernahme der alten Stammdaten in das neue System: ein Schritt, der damals oftmals noch mittels Migrationsdatenbanken durchgeführt wurde. Die Prüfungen der aus dem Altsystem übernommenen Daten erfolgte oftmals über Regeln. Und ich kann mich noch gut erinnern an die sog. Ausnahmeberichte, in denen Stammdateninkonsistenzen aufgelistet wurden, die es zu prüfen und zu lösen galt. Da die ERP-Einführungsprojekte in diesen Zeiten oftmals ein Jahr oder länger dauerten, hatte mal viel Zeit die Stammdatenberichte immer wieder laufen zu lassen und die Daten zu korrigieren. Und viele Firmen schafften es, dank der großen Anstrengungen im Projekt, live zu gehen mit relativ sauberen Stammdaten.
Aber nach dem Go-Live entstanden und entstehen oftmals Probleme. Die Migrationsdatenbank mit Ihren Berichten war bzw. ist auf einmal nicht mehr da um auf Probleme, Lücken oder Inkonsistenzen in den Stammdaten hinzuweisen. Und das Thema Berichtswesen wird in vielen ERP-Projekten erst ganz am Schluss oder sogar erst nach Go-Live richtig angegangen. Oder war es in Ihren Unternehmen etwa anders, und hatten Sie zum Go-Live alle Berichte bereits fertig? Und auf einmal müssen viele Abteilungen jeweils einen Teil der Stammdaten pflegen. Bei spezialisierten Abteilungen, deren Hauptaufgabe das Datenmanagement ist, sollte über validierte Prozesse und Systeme abgedeckt sein, dass die Daten konsistent gepflegt werden, egal ob es ein Materialänderung oder eine Neueinführung betrifft.
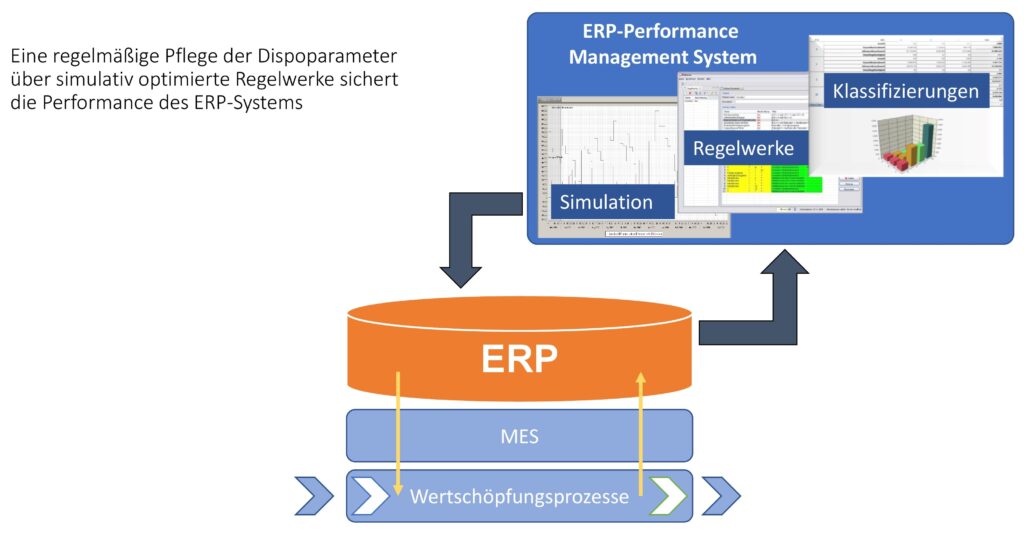
Doch was ist in der Vielzahl der anderen Fälle? In Abteilungen, in denen Stammdatenmanagement eher eine Nebentätigkeit ist, bleibt im Alltagsgeschäft oftmals keine Zeit oder Priorität für eine regelmäßige Überprüfung der Stammdaten. Bei Neueinführungen von ERP-Systemen werden Stammdaten häufig nur aus dem Altsystem kopiert. Und selbst dann, wenn Stammdaten gepflegt werden, ist es schwierig, die resultierenden wirtschaftlichen Konsequenzen von vermeintlich richtig eingestellten oder von inkonsistenten Stammdaten zu übersehen. Infolge schleichen sich dann sukzessive Fehler und Inkonsistenzen in die Stammdaten ein.
Nun sollte man in diesem Zusammenhang fairerweise nicht behaupten, dass die Stammdaten aller Unternehmen gleich schlecht sind. In manchen Branchen – wie z.B. Pharma, Chemie oder der Nahrungsmittelbranche – sind die für die Produktion benötigten Stammdaten normalerweise von extrem hoher Qualität. Man möchte sich auch nicht ausdenken was passieren würde, wenn dort in einer Stückliste ein Komma an der falschen Stelle stehen würde. Gut ausgebildete QA/QC-Abteilungen, Engineering Change Prozesse und ausgereifte Qualitätssysteme tun Ihr Übriges. Bis zu einem gewissen Punkt kann man damit sogar eine gewisse Stammdatenkonsistenz erzwingen.
Aber sobald wir nicht mehr über GMP-kritische Stammdaten reden oder sobald die Qualität bestimmter Stammdatenfelder nicht mehr über QA/QC-Systeme oder Stammdatentools geprüft bzw. sichergestellt werden, ist es um die Qualität der Stammdaten oftmals wesentlich weniger gut bestellt.
Von Problemen mit Stammdaten verursachte Kosten werden oftmals unterschätzt
Einzelne Stammdatenprobleme müssen nicht direkt zu einem großen (Produktions-)Problem oder einem erheblichen wirtschaftlichen Schaden führen. Und oftmals werden Dispo Stammdaten, die nicht mehr der aktuellen Realität entsprechen, nur als lästige Inkonsistenz wahrgenommen. Leider gilt auch hier das Gesetz der großen Zahl: Viele kleinere Inkonsistenzen können in Summe erhebliche Probleme und Kosten verursachen.
In unserer Beratungspraxis bedienen wir uns oftmals der Daten aus ERP-Systemen, um sie als Basis für unsere Analysen zu nutzen. Eine der ersten Fragen, die wir unseren Kunden deshalb stellen lautet: „Wie gut, glauben Sie, sind Ihre Stammdaten?“ Und nur in den seltensten Fällen trauen sich unsere Kunden dann, für Ihre Stammdaten die Hand ins Feuer zu legen. Und das, obwohl kein Kunde daran zweifelt, dass diese Daten wichtig sind.
Systemtechnisch korrekte Werte sind nicht immer wirtschaftlich sinnvoll
Nehmen wir zum Beispiel Stammdaten in den Bereichen Planung und Disposition. Denken Sie an Felder wie Lieferzeit, Mindestlosgröße, Rundungswert oder Sicherheitsbestand.
Im wahren Leben ist es nicht damit getan, diese Datenfelder einmalig bei der Artikelanlage richtig auszufüllen. Der sinnvolle Wert ist vielmehr zumeist abhängig von der aktuellen wirtschaftlichen Situation oder der aktuellen Phase des Lebenszyklus eines Materials. Eine Mindestbestellmenge von 1000 Stück sowie ein gleichgroßer Rundungswert klingen erst mal als korrekte und konsistente Werte. Aber machen diese Werte immer noch Sinn, wenn der Jahresbedarf sich von 10.000 Stück vor 3 Jahren auf jetzt 500 reduziert hat?
Noch schwieriger ist es, die Konsistenz von Stammdaten über Stücklistenebenen hinweg zu erreichen. Nehmen wir ein einfaches Beispiel: Um 1 Stück eines Endprodukts herzustellen, benötigt man von einer gewissen Komponente auch 1 Stück. Würde es dann wirtschaftlich Sinn ergeben, wenn die Losgröße des Endprodukts 1000 wäre und die Losgröße der Komponente 900 betragen würde? Unabhängig voneinander betrachtet, können beide Losgroßen Sinn ergeben, in der Kombination sind sie aber suboptimal, da die Bestellungen/Produktionen der Komponente asynchron verlaufen von den Bestellungen/Produktionen des Endprodukts. Und stellen Sie sich jetzt vor, wie komplex derartige Betrachtungen werden, wenn es Mehrfachbeziehungen gibt zwischen Komponenten und Endgeräten.
Regelwerke und Simulationen sorgen automatisch für wirtschaftlich sinnvolle, konsistente Dispo Stammdaten
Wie kann man derartigen Inkonsistenzen und Schiefständen in den Stammdaten entgegenwirken? Der einzig praktikable Ansatz besteht im Einsatz von Regelwerken. Derartige Regelwerke übernehmen Stammdaten aus dem ERP-System und prüfen die übernommenen Werte systematisch nach bestimmten Regeln, die der Benutzer selbst definieren kann. Derartige Prüfregeln können einfach sein, z.B.: „Wenn das Material zu der Warengruppe X gehört und der Lieferant Y ist, wird die Standardlieferzeit auf Z Tage eingestellt“. Aber es ist auch möglich, wesentlich komplexere Regeln zu definieren. Außerdem können die Regeln ohne großen Aufwand an die aktuellen wirtschaftlichen Gegebenheiten angepasst werden, was z.B. in Zeiten von Corona zu einem konsistenten, adaptiven Verhalten führt. Und der Einsatz von Prüfungen auf aggregierter Ebene wie Produktgruppe, Warengruppe, Kundengruppe oder Lieferant führt dazu, dass man alle Instanzen der entsprechenden Gruppe schnell und konsistent prüfen kann und, falls nötig, Werte verändert. Außerdem werden bei Neuanlage eines Materials bestimmte Stammdaten direkt richtig eingestellt, was sowohl den Aufwand als auch das Risiko von Fehlern bei der Stammdatenerstellung erheblich reduziert.
Beim Prüfen von komplexen Zusammenhängen zwischen Stammdaten, deren Wechselwirkung nicht direkt ersichtlich ist, empfiehlt sich zudem der Einsatz von Simulationssystemen. In derartigen Systemen kann das Zusammenspiel diverser Dispositionsparameter auf Basis von Vergangenheitsdaten simuliert werden. So können die Auswirkungen unterschiedlicher Parametereinstellungen auf das Wertstromverhalten aufgedeckt und die Parametereinstellungen infolge verbessert werden. Im Rahmen solcher Simulationen kann auch überprüft werden, zu welchen Ergebnissen andere Stammdaten geführt hätten, z.B. hinsichtlich Beständen, Lieferbereitschaft, Anzahl der Bestellungen oder Anzahl an Produktionsaufträgen. Außerdem kann man schnell und effizient aufzeigen, was die Umstellung von festen Parameterwerten (wie z.B.: „100 Stück“) auf dynamische Werte (wie z.B.: „eindecken für einen Monat Bedarf, aber runden auf 10 Stück“) bedeuten würde, ohne in die operative ERP-Umgebung einzugreifen und demütig auf die praktischen Ergebnisse oder den sich ergebenden Schaden warten zu müssen. Mittels Simulation lassen sich schnell und kostengünstig grundlegende Einsichten in Zusammenhänge zwischen verschiedenen Stammdatenfeldern gewinnen, die zu gravierenden wirtschaftlichen Verbesserungen, wie z.B. Bestandsreduzierungen um oftmals mehr als 20%, führen. Mit diesem Ansatz wird das Management von Stammdaten aufwandsarm, konsistent, nachhaltig und trotzdem adaptiv gelöst. Werden die Simulationen zudem regelmäßig durchgeführt – beispielsweise monatlich – reduziert sich auch die Gefahr, dass das Stammdatenmanagement im Alltagsgeschäft untergeht, erheblich. Die Pflege der Regelwerke und Simulationen sollte jedoch ein gut ausgebildeter Anwender übernehmen, weshalb Unternehmen nicht nur Tools anschaffen sollten sondern auch ihre Anwender schulen müssen.
Was kann man tun, wenn Regelwerke oder Simulation zum optimieren der Dispo Stammdaten keine Optionen sind?
Auch in Fällen, in denen automatisierte Lösungsansätze wie Regelwerke oder Simulationen nicht möglich oder nicht wirtschaftlich sind, kann man mit einfachen Mitteln die Qualität und Konsistenz der Stammdaten verbessern. Viele Firmen berechnen intelligente Kennzahlen, wie z.B. die Reichweite der kleinstmöglichen Losgröße, die auf wirtschaftliche Schiefstände in den Stammdaten hinweisen. Wenn die kleinste Menge, die Sie laut Ihrer Stammdateneinstellungen bestellen können, z.B. für mehr als 2 Jahre reichen würde, drängt sich schnell die Frage auf, ob diese Losgröße wirtschaftlich noch Sinn ergibt.
Ein weiterer, pragmatischer Schritt besteht darin, Ihren „Lieferanten“ regelmäßig eine Übersicht der Stammdaten in Ihrem System zur Überprüfung zu schicken. Mit dem Terminus Lieferant kann in diesem Zusammenhang natürlich sowohl ein interner Lieferant (wie z.B. die Produktionsabteilung) als auch ein externer Lieferant gemeint sein. Auch viele Lieferanten haben ein starkes Interesse daran, dass ihre Kunden realistische Lieferzeiten in ihren ERP-Systemen interlegt haben und in sinnvollen Mengen – wie z.B. vollen Paletten oder Palettenlagen – bestellen. Selbst in Einzelhandelsumgebungen, mit typischerweise vielen Lieferanten und einem ständig wechselnden Produktangebot, sind regelmäßige Stammdatenprüfungen unabdingbar. Auch dort sollten sich Unternehmen Gedanken darüber machen, wie sich eine regelmäßige Überprüfung aufwandsarm umsetzen und die Anpassungen schnell und effizient verarbeiten lässt. Falls Sie selbst Lieferant sein sollten, wäre es ebenfalls sinnvoll, Stammdatenänderungen Ihren Kunden proaktiv mitzuteilen und regelmäßig Stammdatenübersichten zwecks Überprüfung zu verschicken.