In der letzten Ausgabe unserer POTENZIALE haben wir Ihnen im ersten Teil dieses Artikels erläutert, dass
- Überbestände manchmal wie Süßigkeiten sind. Sie schmeicheln der Seele und beruhigen, sind aber leider schlecht für den Umfang,
- Es in jedem Unternehmen immer wieder Bestandstreiber gibt, die es regelmäßig zu ermitteln gilt,
- Sie Überbestände durch präzise Absatz- und Bedarfsprognosen vermeiden können,
- Exakt definierte Regelwerke und Simulationsmechanismen dem Bauchgefühl auch der erfahrensten Disponenten vorzuziehen sind,
- Manuelles, hektisches Übersteuern in der Supply Chain einen Peitscheneffekt verursacht, der auch die beste Planung vom Kurs abbringt.
Teil zwei unseres Artikels beginnt mit der richtigen dispositiven Entkopplung zwischen Bestands- und Dispositionsstufen.
Auf der Distributionsseite, von den Zentrallägern über mögliche Regionalläger hin zu eventuellen Filialen oder noch dahinter liegenden „points of sale“ arbeiten viele Unternehmen noch immer mit konzeptionell und personell entkoppelten Dispositionsstufen. Jeder Regional- oder Landesfürst fährt seine eigene Strategie, jeder Filialleiter entscheidet über seine Nachbevorratung selbst. Dies stellt jedoch den ersten Schritt in Richtung dispositiver Anarchie dar.
Grundprinzip 6: Entkoppelte Entscheidungen in internen wie in externen Distributionsketten sprengen den Fluss der Waren.
Falls Sie das sogenannte „Beer Game“ nicht kennen, sollten Sie es sich einmal gönnen. In diesem Planspiel wird eine Lieferkette von einer Brauerei über einen Distributor, einen Großhändler und einen Einzelhändler bis zum Kunden abgebildet. In den einzelnen Lagerstufen müssen in jeder Spielrunde Entscheidungen über die nachzubestellenden Mengen an Bierkästen getroffen werden, sodass die Bestände möglichst niedrig und die Lieferbereitschaftgrade möglichst hoch bleiben. Jede Lagerstufe kennt nur die aktuellen Bestellungen der jeweiligen Kundenseite und entscheidet daraus selbständig, welche Mengen beim Lieferanten nachbestellt werden. Es ist spannend und unterhaltsam zu sehen, wie sich die Dispositionsmengen und Bestände aufschaukeln.
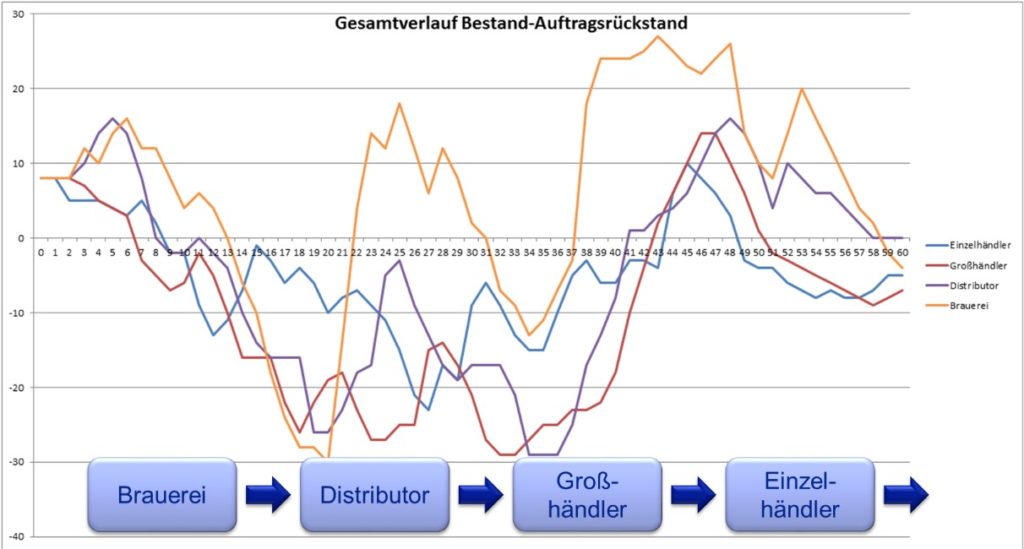
Dieses Beer Game entspricht der typischen Strategie in einer Lieferkette, in der jede Lagerstufe wirtschaftlich selbständig und selbstverantwortlich agiert. Mit Konzepten wie „Forward Sourcing“, Efficient Consumer Response (ECR) oder Collaborative Planning, Forecasting and Replenishment (CPFR) versucht man, solche Planungsketten einzufangen. Das ist nicht einfach, da viele Interessen und Egoismen unabhängiger Parteien, die keinem gemeinsamen Herrn gehorchen, unter einen Hut gebracht werden müssen. In vielen unserer Unternehmen gibt es aber sehr wohl Distributionsketten, die einem gemeinsamen Oberhirten unterstehen und deren Einzelverhalten letztlich zum Gesamtergebnis des Unternehmens konsolidiert werden.
Zumindest in diesen Distributionsketten kann man der Willkür entgegenarbeiten und Top-Performer im Bestandsmanagement tun dies auch. Der Weg dorthin führt über ein zentral gesteuertes Replenishment der verschiedenen Distributionsstufen, auf Basis eines entsprechend ausgeklügelten und laufend optimierten Regelwerks.
Häufig stellen einzelne Lager in der Distributionskette rechtlich selbständige Einheiten dar, die auch eigenständige Ergebnisverantwortung tragen. Von diesen wird die Disposition der eigenen Lagerbestände meist als Hoheitsrecht und Wettbewerbsfaktor verstanden: „Wenn ich für das Ergebnis dieser Landesgesellschaft zuständig bin, dann muss ich auch mein Lager disponieren können, wie ich es für richtig halte“, ist eine typische Reaktion auf den Vorschlag eines zentralen Replenishments. In der Praxis zeigt sich aber immer wieder, dass man mit weniger Bestand in Summe, aber auf die richtigen Artikel verteilt, mehr erreichen kann. Die Materialverfügbarkeit auf den einzelnen Lagerstufen kann man mittels Lieferservicevereinbarungen zwischen diesen und der zentralen Disposition absichern. Unterstützt werden muss dies durch eine disziplinierte Ausnahmenplanung für Projekte, Aktionen oder sonstige Sonderbedarfe.
Best-Practice-Baustein 6:
Ein nachhaltiges Bestandsmanagement lässt sich in einer Distributionskette meist nur durch ein zentral gesteuertes Replenishment erreichen. An die Stelle der dezentralen Bestandsverantwortung für die fremddisponierten Lagerstufen tritt die Verantwortung für Ausnahmeplanungen und Lieferservice-Vereinbarungen.
Eine Supply Chain besteht nicht nur aus Distributionsbeziehungen, in denen verschiedene Lagerstufen über Transportprozesse miteinander verkoppelt sind, sondern auch aus langlaufenden Beschaffungsbeziehungen zwischen einem Kunden und einem produzierenden Lieferanten. In diesen Fällen besteht der logistische Prozess nicht nur aus einer Umlagerungsbeziehung zwischen dem Fertigwarenlager des Lieferanten und den Eingangslager des Kunden. Möglicherweise lagert der Lieferant das zu liefernde Teil gar nicht als Fertigprodukt; auf jeden Fall wird das Lager, aus dem der Artikel an den Kunden geliefert wird, durch einen Produktionsprozess wieder aufgefüllt.
Im Lean Management wird in solchen Fällen gerne empfohlen, im Takt des Kunden zu fertigen, also beide Produktionsstufen zeitlich und mengenmäßig miteinander zu koppeln.
Sofern die richtigen Voraussetzungen hierfür bestehen, funktioniert dies auch sehr gut, wie wir noch sehen werden. In vielen Fällen jedoch vergeben Sie damit Möglichkeiten für Bestandssenkung und Wirtschaftlichkeit, denn Sie beachten besser
Grundprinzip 7: Das Logistische System eines Unternehmens arbeitet nach seinem eigenen unverkennbaren Rhythmus.
Aus Sicht des Bestandsmanagements liegt in der kooperativen Zusammenarbeit zwischen Kunden und Lieferanten noch immer beträchtliches Potenzial zur Reduzierung von Beständen und zur Verbesserung der Versorgungssicherheit. Die Möglichkeiten beginnen bei Zeichnungsteilen und der Produktspezifikation und reichen über das Vermeiden von Lagerstufen bis zur administrativen Integration.
Die eigene Produktion in einen Takt zu bringen, kann ein sehr wirkungsvoller Ansatz sein, Materialströme zum gleichmäßigen Fließen zu bringen und damit auch das Bestandsmanagement zu vereinfachen. Dabei den Takt des Kunden zu übernehmen, ist häufig ein zu einfaches Leitmodell, da in vielen Fällen die Produktionskette des Lieferanten nicht speziell und ausschließlich für die Produktionskette des Kunden arbeitet. Aus der Sportmedizin wissen wir, dass zusammen joggen nicht immer von Vorteil ist: Jeder Läufer muss seiner eigenen Kondition entsprechend seinen Rhythmus finden.
Eine Kopplung zwischen Kunde und Lieferant liegt nicht nur vor, wenn der Lieferant im Takt des Kunden arbeitet, sondern in schwächerer Form auch, wenn der Lieferant auf die Bestellung oder den Abruf des Kunden sofort zu reagieren hat, um eine vereinbarte Lieferfrist einzuhalten.
Bei langfristigen Geschäftsbeziehungen und regelmäßigen Lieferungen liegt in der Entkopplung von Lieferant und Kunde oft ein großes wirtschaftliches Potenzial verborgen. Es kann wirtschaftlich und bestandsseitig geschickter sein, im eigenen Takt zu fertigen oder sich durch einen Bestandspuffer vom Kunden zu emanzipieren. Auch ein klassischer Fertigwarenbestand dient zur Entkopplung, dann aber ggfs. auf Kosten höherer Bestände. Ein geschickteres und sehr wirkungsvolles Instrument zur Entkopplung stellt ein VMI (Vendor Managed Inventory)-Konzept dar.
Im typischen VMI-Modus erfolgt die Nachbevorratung des Kundenlagers durch den Lieferanten selbständig. Der Kunde erspart sich die Dispositionsarbeit, der Lieferant gewinnt dispositive Freiheitsgrade, da er über seine Nachlieferung bezügliche Liefertermin und Liefermenge selbständiger entscheiden kann. Der Lieferant übernimmt die Kapitalbindung der beim Kunden liegenden Bestände, der Kunde deren Lagerung und Bewirtschaftung und typischerweise auch das wirtschaftliche Risiko. VMI-Konzepte stellen keinen schlechten Deal für Lieferanten dar. Erstaunlich, dass sich noch immer viele dagegen wehren.
Anders liegt der Fall, bei dem die Produktionskette des Lieferanten wirklich speziell auf die Produktionskette des Kunden ausgerichtet ist, wie es in der Serienfertigung und speziell in der Automobilindustrie sehr häufig vorkommt. In diesem Fall ist die Strategie einer sehr engen Zusammenarbeit vorteilhaft, zumal sie ja schon in die Produktionskette hineinkonstruiert wurde. Wenn die Fertigungsprozesse von Kunde und Lieferant sehr genau aufeinander abgestimmt sind und beide sehr stabil laufen, kann man durch Just in Time (JIT) oder Just in Sequence (JIS) Prozesse sehr geringe Bestände bei hoher Lieferbereitschaft erreichen. Man verzichtet dabei aber auf der Seite des Lieferanten auf das im Lean Management geheiligte Prinzip der Pull-Steuerung zugunsten einer gezielten Push-Steuerung, damit die Materialien genau im richtigen Moment zufließen.
Best-Practice-Baustein 7:
In einer Produktionskette wirtschaftlich selbständiger Unternehmen lassen sich Bestände, Lieferbereitschaft und Wirtschaftlichkeit der beteiligten Parteien meist durch entkoppelte Prozesse am besten optimieren. Im Sonderfall exakt aufeinander abgestimmter Produktionslinien gelten hingegen wieder die Verkopplungsprinzipien einer internen Produktionskette.
Wie besprochen, bietet die Fertigung im Takt bei internen Produktionsketten und bei speziell aufeinander abgestimmten externen Produktionsketten große Vorteile für die Wirtschaftlichkeit der Fertigung und für das Bestandsmanagement. Leider stehen diesem Idealbild allzu oft Artikel mit großen Losen und mit langen Durchlaufzeiten im Weg…
Grundprinzip 8: Artikel mit großen Losen und langen Durchlauf- und Lieferzeiten sind Junk Food für die Wertschöpfungskette – billig zu haben, aber schwer zu verdauen.
Wer von uns arbeitet nicht mit asiatischen Lieferanten zusammen? Viele Produkte sind überhaupt nur noch in Asien zu beschaffen, bei anderen lassen einem die Preisvorteile der asiatischen Lieferanten keine Wahl. Doch das Asian Sourcing bringt auch beträchtliche Nachteile mit sich. Vergessen wir einmal die gar nicht so seltenen Fälle, in denen die Preisvorteile der asiatischen Lieferanten bereits durch die Reisekosten der Einkäufer aufgefressen werden. Aus logistischer Sicht gravierender wirkt der Effekt, der zumeist langen Wiederbeschaffungszeiten verbunden mit großen Beschaffungs-Losgrößen geschuldet ist: egal ob diese Folgen von Mindestbestellmengen, Frachtkostenoptimierung oder dem Zwang zur Containerfüllung sind.
Artikel mit großen Losgrößen und langen Wiederbeschaffungszeiten verursachen immer hohe Bestandsschwankungen mit hohen Durchschnittsbeständen. Im Schnitt wirken die großen Lose noch deutlich dramatischer als die langen Wiederbeschaffungszeiten. Bei einer Verdopplung der Wiederbeschaffungszeit müssen die Eindeckzeiten nicht zwangsläufig mit ansteigen. Der erforderliche Sicherheitsbestand erhöht sich aber um ca. 40 %. Eine Verdoppelung der Losgröße führt hingegen zu einer Verdopplung des Grundbestandes. Je unregelmäßiger die Artikelnachfrage, desto stärker wirkt sich der Sicherheitsbestandseffekt aus, je gleichmäßiger die Nachfrage, desto stärker fällt die Grundbestandsveränderung ins Gewicht.
Arbeitet man nicht nur in der Beschaffung, sondern auch in der Produktion mit großen Losen, fließt das Material in großen Stößen durch die Fertigung. Dies ist verbunden mit der Gefahr vorübergehender Kapazitätsengpässe, die sich langsam durch die Wertschöpfungskette schieben wie ein Ferkel, das von einer Schlange verschluckt wird. Derartige Verstopfungen führen direkt zu höheren Umlaufbeständen in der Produktion.
Natürlich kann man Fertigungs- und Beschaffungslose nicht beliebig klein machen, sondern muss die Gesamtkosten im Blick haben, aber dann bitte wirklich die Gesamtkosten und nicht nur die Einkaufspreise. Es macht einen gewaltigen Unterschied, ob Bestandsmanagement und Logistikstrategie darauf ausgerichtet sind, kontinuierlich an der Verringerung von Losgrößen und Wiederbeschaffungszeiten zu arbeiten oder ob Sie beide Parameter als mehr oder weniger gegeben hinnehmen. Hinter diesen beiden „Bestandsmanagementkulturen“ öffnet sich die Schere zwischen den absoluten Top-Performern und den restlichen Unternehmen; erstere arbeiten kontinuierlich daran, den Materialstrom zu zermahlen und damit den Flussgrad ihrer Produktion (Verhältnis von Bearbeitungszeiten zu Durchlaufzeiten) zu erhöhen. Je höher der Flussgrad, desto gleichmäßiger der Warenstrom und desto geringer die Lager- und Umlaufbestände.
Abbildung 2: Innerhalb wirtschaftlich verbundener Unternehmen und in der Distributionskette sollten Dispositionsstufen immer über ein zentrales Regelwerk synchronisiert werden.
Best-Practice-Baustein 8:
Ein nachhaltiges Bestandsmanagement benötigt einen gut verdaulichen Materialbrei aus kleinen Fertigungs- und Beschaffungslosen und möglichst kurzen Wiederbeschaffungszeiten.
In jeder Lieferbeziehung, egal ob dispositiv entkoppelt oder über ein zentrales Dispositionsregelwerk gearbeitet wird, kann es einmal zu Lieferengpässen kommen. Bei dispositiv entkoppelten Lieferketten trifft man in solchen Fällen auf…
Abbildung 3: Je kleiner Beschaffungs- und Fertigungslose, desto gleichmäßiger fließt der Warenstrom. Je geringer die Wiederbeschaffungszeiten, desto geringer der Sicherheitsbestand.
Grundprinzip 9: Verknappen Waren des täglichen Bedarfs, und das sind im business-to-business-Bereich praktisch alle Waren, dann übersteuert zuerst die Nachfrage.
Aus dem Lebensmittelbereich kennen wir das alle: Drohende Winterstürme aber auch mehrere Feiertage hintereinander führen gelegentlich zu Hamsterkäufen. Der Spuk ist meist jedoch schnell vorbei.
Das gilt auch für die industrielle Wertschöpfungskette, wenn Engpässe sich als nur vorübergehend erweisen. Anders stellt sich der Sachverhalt dar, wenn die Verknappung über längere Zeit anhält und die Kunden nicht auf Ersatzprodukte ausweichen können.
Viele Lieferanten, die den Marktbedarf an solchen „alternativlosen“ Artikeln nicht mehr bedienen können, fangen ganz natürlich damit an, Teillieferungen an die Kunden zu versenden. Das entspannt die Liefersituation drastisch, vorausgesetzt der Engpass dauert nur vorübergehend an, denn die fehlenden Mengen werden kurzzeitig nachgeliefert. Besteht ein Engpass aber über längere Zeit, typischerweise einige Monate, dann kommt der Lieferant nie hinter seinen Kundenbedarfen her.
Aus Sicht des Kunden stellt sich die Liefersituation dann wie eine Quotierung dar und manche Lieferanten handhaben die Mangelwirtschaft auch tatsächlich so. Der Kunde hat 1000 Stück bestellt und bekommt 200. Eine typische Reaktion der Kunden auf diese Situation ist ein einfacher Dreisatz: Wenn ich bei einer Bestellung über 1000 Stück 200 bekomme, dann erhalte ich bei einer Bestellung über 5000 Stück meine benötigten 1000. Man kann sich leicht vorstellen, dass das Chaos ausbricht, wenn alle Kunden so reagieren…und viele Kunden reagieren so.
Es ist auch nicht ganz einfach für einen Einkäufer, aus höherer Einsicht die Vorteile des eigenen Unternehmens hinter diejenigen der uneinsichtigen Mitkunden zu stellen. In der Folge schwingen sich vermeintliche Marktbedarfe auf, die gar nicht der Realität entsprechen. Aus der Halbleiterindustrie sind solche Zyklen gut bekannt. Im schlimmsten Fall führen sie dazu, dass die Lieferanten drastisch Kapazitäten aufbauen. Sobald aber die reale Nachfrage aufgrund der höheren Fertigungskapazität wieder befriedigt werden kann, fällt die künstliche Nachfragesteigerung wieder in sich zusammen. Zuvor werden aber viele Abnehmer mit hohen Liefermengen überflutet.
Die Lösung solch anhaltender Lieferengpässe liegt eigentlich auf der Hand, aber man muss sie konsequent anwenden: Es ist richtig, die Zuteilungsmengen an die Abnehmer zu quotieren, allerdings auf der Basis der vergangene Bestellungen zu Zeiten ohne relevante Lieferengpässe und nicht auf Basis der aktuellen Kundenbestellungen. Ist diese Verfahrensweise allen Abnehmern klar, besteht auch kein Grund mehr für Bestellmengeninflation und der drohende Schweinezykus wird deutlich gedämpft.
Best-Practice-Baustein 9:
Bei langanhaltenden Kapazitätsengpässen müssen die Lieferungen an die Kunden quotiert werden, und zwar auf Basis der Liefermengen der Vergangenheit.
Was das für das Kunden-Lieferantenverhältnis bedeutet und welche Auswirkungen das Verhalten der Geschäftspartner auf Ihre Supply Chain hat, erfahren Sie in der nächsten Ausgabe der POTENZIALE.
Weitere Informationen zu diesem Themenfeld finden Sie hier:
- 13 Best Practice-Kriterien für ein nachhaltiges und ganzheitliches Bestandsmanagement – Teil 1
- 13 Best Practice-Kriterien für ein nachhaltiges und ganzheitliches Bestandsmanagement – Teil 3
- Sicherheitsbestände: Der Fünf-Punkte-Plan
- Best-Practice-Regeln für eine leistungsfähige Absatzprognose