Best-Practice-Regeln für das Produktionskanban, Teil 2:
Layout und Handling planen
In Teil 1 des Best-Practice-Artikels zum Produktionskanban haben wir Ihnen eine Einführung in das Thema gegeben:
- Wann macht es Sinn, ein Produktionskanban in die eigenen Produktionsprozesse zu integrieren?
- An welcher Stelle sollte man das tun?
- Welche Grundvoraussetzungen müssen vorab erfüllt sein?
Wir machen nun weiter mit den praktischen Faktoren, die es bei der Kanban-Einführung zu beachten gilt und starten ganz profan mit
Grundprinzip 10: Mehr Kanbankarten ergeben ein besseres Bild der Bedarfssituation
Der Umlaufbestand an Teilen in einem Kanban-System wird bestimmt von:
- durchschnittlichem Verbrauch pro Zeiteinheit,
- der Bedarfsregelmäßigkeit,
- dem geforderten Lieferbereitschaftsgrad und
- der erforderlichen Produktionslosgröße.
Die Anzahl der erforderlichen Kanbanbehälter hängt dann von der Anzahl der Teile ab, die in einen Behälter passen. Von großen Behältern benötigt man weniger, von kleinen Behältern benötigt man mehr.
Jeder Behälter erfordert Handhabungsaufwand. Das scheint dafür zu sprechen, möglichst große Behälter zu verwenden. Mit dem Gewicht eines Behälters steigen jedoch die erforderliche Kraft und die einzusetzende Technik und damit die Handhabungskosten, was letztlich wieder für mehrere kleine als wenige große Behälter spricht.
Ein weiteres Kriterium spricht für den Einsatz kleinerer Behälter, das mindestens so wichtig ist, wie der Aspekt des Behältergewichts und des Handhabungsaufwandes:
Je mehr Behälter in einem Kanban-Regelkreis umlaufen, desto besser der “Vorschaueffekt” für den liefernden Bereich.
Am Anwachsen der Kartenstapel in einem Sammelkanbansystem kann der liefernde Bereich abschätzen, wann der gelbe und der rote Bereich ungefähr erreicht sein werden. Das hilft, die Auftragsreihenfolgen an den Fertigungskapazitäten vorausschauend zu belegen.
Ideal sind um die fünf Kanbanbehälter, die im Sammelkanban zusammengefasst werden, um einen Produktionsauftrag zu starten.
In der Praxis muss man sich allerdings oft an der Realität der vorhandenen Behältergrößen ausrichten. Und wenn durch Rüstoptimierungsmaßnahmen die Fertigungslosgrößen laufend gesenkt werden können, dann kann man nicht laufend die Kanbanbehälter austauschen oder den physischen Füllgrad eines Behälters immer weiter reduzieren. Die Teile pro Behälter müssen diesen auch einigermaßen füllen, sonst wird zu viel Lagervolumen verschwendet.
Viele Unternehmen befürchten, bei kleineren Kanbanbehältern zu viele Kanbankarten in Umlauf bringen zu müssen. Hierüber müssen Sie sich keine Gedanken machen: die Zahl der Kanbankarten in einem Regelkreis ist eher unkritisch. Kritischer kann zuweilen die Anzahl der kanbangesteuerten Artikel sein, die die liefernde Stelle nachproduzieren muss. Bei zu vielen Materialnummern kann die Übersicht in einer physischen Kanbantafel verloren gehen. Ein elektronisches Kanban kann mit einer großen Anzahl an Kanbanteilen besser umgehen als klassische Lösungen.
Best Practice Baustein 10: In einem professionell gestalteten Produktionskanbansystem wird der Umlaufbestand des Kabanregelkreises auf möglichst viele Kanbanbehälter verteilt. Faustformel: Ideal sind fünf gut gefüllte Kanbanbehälter für ein Produktionslos.
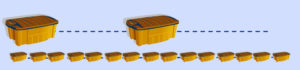
Grundprinzip 11: Kleine Loshäppchen verdaut ein Materialfluß besser
Produktionslosgrößen sind Staustufen im Materialstrom, die konsequent und kontinuierlich geschliffen werden müssen. Mit Losgröße 1 wäre der Materialstrom viel gleichmäßiger und der Peitscheneffekt in der Produktionskette würde deutlich geringer.
Auch wenn die Losgröße 1 aus wirtschaftlichen Gründen bei vielen Fertigungsprozessen nicht machbar ist, sollte der Druck auf die Losgrößenreduzierung aufrechterhalten werden.
Das Produktionskanbansystem kann hierzu einen Beitrag leisten, auf den erfolgreiche Unternehmen nicht verzichten: die Standardfertigungslosgröße sollte immer auf den “roten Bereich” und nicht auf den Beginn des “gelben Bereiches” gesetzt werden. Wird aus Gründen der Reihenfolgeplanung oder des Kapazitätsausgleichs bereits im gelben Bereich mit der Produktion begonnen, so liegt die korrespondierende Losgröße unterhalb der Standardlosgröße. Der Kompromiss, mit der Produktion bereits beginnen zu dürfen, ehe die eigentlich definierte Nachbevorratungsschwelle des roten Bereiches erreicht ist, sollte mit dem Losgrößenkompromiss “bezahlt” werden. Hierdurch wird ein gewisser Druck aufgebaut, die wirtschaftliche Losgröße weiter zu senken.
Wer umgekehrt vorgeht und die Standardlosgröße auf den Beginn des gelben Bereiches setzt, der erlaubt der Produktion, die zukünftigen durchschnittlichen Fertigungslosgröße zu erhöhen.
Best Practice Baustein 11: Bei einem Produktionskanban liegt der rote Bereich bei der wirtschaftlichen Losgröße und der gelbe Bereich darunter.
Das richtige Kanbankonzept
Grundprinzip 12: Ein Bild sagt mehr als tausend Tabellen
Der ursprüngliche Kanban-Mechanismus besteht aus einem rein manuellen Kreislauf ohne Anbindung an ein ERP-System, der mit Karten und Kanbantafeln, in die die Karten mechanisch gesteckt werden, arbeitet. Ein klarer Vorteil dieses Mechanismus ist die einfache und übersichtliche Visualisierung der Bedarfssituation für die liefernde Stelle. Ein rein mechanisches Kanbansystem hat jedoch einen großen Nachteil, es hinterlässt keine “elektronischen Spuren” im ERP-System. Es kann daher weder mit anderen ERP-gesteuerten Dispositionsprozessen synchronisiert werden, noch können die Kanban-Regelkreise zentral überwacht werden.
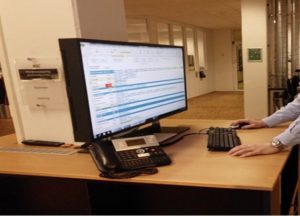
Die digitale Variante einer Kanbanlösung stellt ein elektronisches Kanban dar. Hier werden die gesamten Kanbanregelkreise im Rechner geführt. Entsprechende Lösungen gibt es als Module oder Funktionen verschiedener ERP-Systeme.
Normalerweise arbeiten auch elektronische Kanbansysteme mit physischen Karten, da jeder Kanbanbehälter gekennzeichnet sein muss. Der Behälterzustand, z.B. ob er gerade gefüllt oder gerade leer, wird durch einen Barcode-Scan oder das Lesen einer RFID-Information dem elektronischen Kanbansystem mitgeteilt. Im elektronischen Kanbansystem werden die Karten und ihre “Betriebszustände” im Rechner geführt. Beim Auslösen eines Sammelkanbans erfolgt ein Druck der Karten. Später werden die Karten leerer Behälter wieder gescannt und danach vernichtet, da sie sich jetzt in elektronischer Form in der Kaban-Software wiederfinden. Manche Unternehmen bewahren die leer-gescannten Karten auch auf und holen sie wieder aus der Schublade, wenn der gelbe oder rote Bereich erreicht wurde, statt neue Karten zu drucken.
Das elektronische Kanban beseitigt die Nachteile rein manueller Kanbanlösungen. Es vereinfacht die Verwaltung der Regelkreise und ermöglicht eine zentrale Überwachung der Kanbanregelkreise anhand von Kennzahlen. Bei der Nachdimensionierung von Regelkreisen muss niemand in der Fertigung überzählige Karten aus Kanbantafeln entfernen oder neue Karten einstecken.
Ein elektronisches Kanban birgt jedoch auch die Gefahr unzureichender Visualisierung, wenn auf die grafisch aufbereitete Nachbildung einer physischen Kanbantafel verzichtet wird.
Ein wesentliches Erfolgsmerkmal eines Kanbansystems besteht nämlich in der Visualisierung der Bedarfssituation für die liefernde Stelle eines Kanbanregelkreises. Mit Zahlentabellen können Sie diese Visualisierung nicht erreichen. Übersichtlich sind nur grafisch aufbereitete elektronische Kanbantafeln. Der ursprünglichen Idee am nächsten kommen dabei Lösungen, die tatsächlich Karten abbilden und am Bildschirm stapeln.
Wenn Sie auf eine mechanische Kanbantafel verzichten wollen und eine Darstellung am Bildschirm bevorzugen, werden Sie bitte nicht an der falschen Stelle sparsam. Ein 15-Zoll-Bildschirm ermöglicht keine sinnvolle Visualisierung. Für den Preis einer physischen Plantafel können Sie sich mindestens einen 70-Zoll Flat Screen leisten!
Best Practice Baustein 12: Großflächige Visualisierung schlägt Komfort: Erfahrene Kanbanunternehmen legen großen Wert auf die großflächige Visualisierung der Bedarfssituation in einem Kanbansystem. Lieber aufwändig manuell Karten stecken, als komfortabel im Informationsnebel elektronischer Lösungen ohne grafische Kanbanvisualisierung herumzuirren.
Grundprinzip 13: Moderne Führung erfolgt am Tatort.
Im Toyota Produktionssystem spricht man von “Gemba”. Dieser japanische Begriff lässt sich vielleicht am besten mit “Tatort” übersetzen. Am Tatort zu ermitteln, das wissen wir als eifrige Krimileser und -seher, ist für den Kommissar unerlässlich. Die detaillierte Dokumentation des Tatortes durch die Kriminaltechnik kann die Begehung des Tatortes nie ersetzen. Am Tatort werden viele Nebeninformationen aufgenommen, die den Eindruck vervollständigen. Selbst bei sorgfältigster Dokumentation lässt sich nur ein Teil der Informationen festhalten, die den Tatort ausmachen.
Entsprechendes gilt für eine dezentrale Steuerung, wie sie durch ein Kanbansystem aufgebaut wird. Die Leute vor Ort, die Leute am Tatort, kennen und erfassen viele Zusammenhänge, die vom Schreibtisch aus nur schwer auszumachen sind. Das gilt auch – und bereits – für den Schreibtisch des Meisters oder des Fertigungssteuerers. Eine Kanbantafel gehört an den Tatort der liefernden, nachproduzierenden Stelle und nicht ins Meisterbüro; egal, ob es sich um eine physische Kanbantafel oder eine elektronische Variante handelt.
In jedem Fall muss die Tafel so groß und so einsehbar positioniert sein, dass diejenigen, die Sammelkanbans auslösen, in Licht der Öffentlichkeit arbeiten. Geheimwissen des Meisters oder Fertigungssteuerers war gestern – Kanban findet öffentlich statt. Diese Öffentlichkeit ist ein Teil der “Checks and Balances”, die dazu beitragen, dass das System zuverlässig funktioniert und die Regeln eingehalten werden.
Best Practice Baustein 13: Eine Kanbantafel – mechanisch wie elektronisch gestaltet – gehört in die Produktion und nicht ins Meisterbüro.
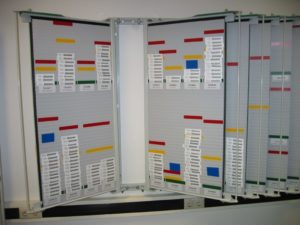
Grundprinzip 14: Kanbanteile und konventionelle Teile produktionstechnisch zu trennen, ist selten wirtschaftlich.
In Unternehmen mit einer typischen Produktstruktur werden 40% bis 80% der Fertigungskapazität mit 10% bis 30% der regelmäßigen Fertigungsteile (AB/XY-Teile) belegt. Die restlichen 70% bis 90% der Materialnummern weisen nur unregelmäßige Bedarfe auf und belegen die restliche Fertigungskapazität. Wenn Sie die AB/XY-Teile auf Kanban umstellen und die restlichen Teile weiterhin konventionell steuern, wird es Ihnen kaum gelingen, den beiden Gruppen von Teilen getrennte Fertigungsbereiche und -anlagen zuzuweisen.
Kanbanteile und konventionelle Teile produktionstechnisch zu trennen, würde in beiden Segmenten Überkapazitäten erfordern und wäre damit nicht wirtschaftlich. Wir stoßen regelmäßig auf Unternehmen, die davon ausgehen, dass Kanbanteile in einer getrennten Kanbanproduktion gefertigt werden müssen. Da dies wirtschaftlich nicht zu machen ist, verzichten sie unnötigerweise auf die Kanbaneinführung.
Der Betrieb eines Kanbansystems erfordert zwar idealerweise Reservekapazität oder alternativ ergänzende Nivellierungsmaßnahmen, er erfordert aber keine physische Trennung von Fertigungsbereichen in Kanban und dem Rest der Welt.
Best Practice Baustein 14: In wirtschaftlich arbeitenden Kanbanlösungen fahren kanbangesteuerte und konventionell gesteuerte Artikel größtenteils über dieselben Kapazitäten
Grundprinzip 15: Wenn nichts zieht, wird nichts geschoben.
Der Zauber eines Kanbansystems liegt in der marktsynchronen Produktion. Es soll eben gerade nichts vorausproduziert werden, wenn kein Bedarf besteht.
Eine absolut konsequente bedarfssynchrone Produktion erfordert allerdings große Flexibilität in der Produktion, um mit den Bedarfsschwankungen zurecht zu kommen. Diese Flexibilität kostet Geld, denn man erreicht sie meist nur durch Reservekapazität oder Zusatzschichten in den Produktionsanlagen und einer höheren Zahl an Stammpersonal und Leiharbeitern.
Was das Personal betrifft, lässt sich ein gewisses Maß an Flexibilität erreichen, indem Mitarbeiter anderen Arbeitsplätzen zugewiesen werden sowie Gleitzeit und Arbeitszeitkonten genutzt werden.
Der gelbe Bereich in einem Produktionskanban sowie die Nivellierung der Produktion durch einen Heijunka-Mechanismus ermöglichen darüber hinaus, die Bedarfsseite etwas zu glätten.
Es kommt jedoch immer wieder einmal vor, dass all diese Abgleichsmechanismen nicht reichen und Leerlauf bei den Mitarbeitern und Unterauslastung in der Produktion droht. Im Betrieb wird dann schnell nach Vorproduktion gerufen. Ein professionell gestaltetes Kanbansystem muss einen vorübergehenden Leerlauf bei Mitarbeitern jedoch aushalten können. Vorproduktion über einen klar definierten Nivellierungsmechanismus hinaus ist keine adäquate Antwort. Sie führt zu Überbeständen, kann Unterauslastung allenfalls zeitlich verschieben, denn irgendwann müssen die Überbestände wieder abgebaut werden, und birgt die Gefahr, dass Auslastungsschwankungen in der Produktion sich weiter steigern. In professionellen Kanbansystemen führt deshalb kein Weg daran vorbei:
Best Practice Baustein 15: Ein konsequentes Kanbansystem muss gelegentlichen Leerlauf bei Mitarbeitern aushalten können.
Richtige Einführung
Grundprinzip 16: Überzeugen geht vor Erzwingen.
Bei der Einführung eines Kanbansystems werden Sie nicht nur auf Begeisterung treffen. Die Vorbehalte gegenüber einem Pull-System sind vielfältig und tief verwurzelt. Wir haben immer wieder die Erfahrung gemacht, dass gerade Meister in der Produktion Kanbansystemen mit Vorsicht begegnen. Dahinter steht der Zweifel, ob ein solches Pull-System tatsächlich funktionieren kann und so viel effektiver ist als ein klassischer Steuerungsmechanismus.
Zuweilen kommt die Unsicherheit hinzu, im Rahmen der dezentralen Steuerung selbst über den nächsten zu fertigenden Auftrag entscheiden “zu müssen” und dies nicht mehr von einem Fertigungssteuerer vorgegeben zu bekommen.
Treffen wir auf solche Vorbehalte in den Vorgesprächen, empfehlen wir zur Vorbereitung auf die Kanbaneinführung ein Planspiel durchzuführen.
Am Markt werden unterschiedliche Planspiele angeboten. Wir greifen gerne auf ein Planspiel zurück, bei dem wir im Laufe von zwei Tagen ausgehend von einer plangesteuerten Produktion nach Vertriebsvorgaben Stück für Stück die Produktionsabläufe vereinfachen und das Steuerungsprinzip umstellen.
Während die Teilnehmer am Anfang den vorgegebenen Produktionsplan trotz großem Stress nicht erfüllen, gelingt ihnen dies am Ende des Planspiels mittels Kanban frappierend schnell und einfach.
Best Practice Baustein 16: Ein Planspiel kann der Beginn einer wunderbaren Freundschaft zwischen Anwendern und einem Kanbansystem sein.

Grundprinzip 17: Der Meister hat immer Recht.
Bei der Auslegung eines Kanbansystems kommt man irgendwann an den Punkt, die errechneten Regelkreise mit den Meistern oder Bereichsleitern der verschiedenen Fertigungsbereiche durchzusprechen. Häufig bezweifeln die Ansprechpartner, dass die Regelkreise ausreichend dimensioniert sind. Was passiert, wenn mehrere Teile, die auf denselben Maschinen gefertigt werden müssen, zum gleichen Zeitpunkt “rot” werden? Der abstrakte Hinweis, dass dies in der Praxis selten vorkommt und durch die definierten gelben Bereiche und die Sicherheitsbestände in den einzelnen Regelkreisen abgefangen werden kann, reicht oft nicht aus, die Vorbehalte zu zerstreuen.
Stimmen Sie mit den Meistern in diesen Fällen eine Vorlaufzeit ab, um die Sie die Wiederbeschaffungszeit des Regelkreises verlängern und die so festgelegt ist, dass die Meister überzeugt sind, damit die Teile rechtzeitig fertigen zu können. Halten Sie diese Vorlaufzeit getrennt von der eigentlichen Wiederbeschaffungszeit fest. Die Vorlaufzeit bedingt zwar, dass Sie etwas mehr Bestand aufbauen, als es Ihr Regelkreis eigentlich erfordert. Sie haben aber den Meister auf Ihre Seite gezogen. Durch die, manchmal wie auf dem Basar, ausgehandelte Vorlaufzeit hat der Meister sich verpflichtet, dass die Kanbanteile im Supermarkt/Kanbanregal rechtzeitig aufgefüllt werden können.
Läuft das Kanbansystem, werden Sie aus der Überwachung der Wiederbeschaffungszeit erkennen können, ob die Vorlaufzeit erforderlich ist. Ist sie nicht erforderlich, können Sie sie in Abstimmung mit den Meistern kontinuierlich verringern. Sollte sie ausnahmsweise einmal tatsächlich erforderlich sein, so haben Sie eben von der Erfahrung des Meisters profitiert. Ziel muss es sein, nicht erforderliche Vorlaufzeiten kontinuierlich zu eliminieren.
Best Practice Baustein 17: Besser “Vorlaufzeiten” als Vorbehalte: Eine erfolgreiche Kanbaneinführung nimmt die Vorbehalte der Meister ernst, die später mit dem Kanbansystem leben müssen. Eine zusätzliche Sicherheit im Regelkreis in Form einer “Vorlaufzeit” kann Vorbehalte zerstreuen. Die Vorlaufzeit muss getrennt dokumentiert und darf nicht in der Wiederbeschaffungszeit versteckt werden, um saubere Regelkreisberechnung und subjektives Sicherheitsempfinden exakt voneinander zu trennen.
Grundprinzip 18: Bestandsreduzierung ist gut, aber Lieferbereitschaft ist besser.
Entscheiden Sie spontan: Woran machen Sie in den ersten vier Wochen seit dem Go-live eines Kanbansystems dessen Erfolg fest: an der Teileverfügbarkeit oder an der Bestandsreduzierung? Wenn Sie wie die meisten entscheiden, dann ist Ihnen anfänglich die Teileverfügbarkeit wichtiger als die Bestandsreduzierung. Dass es eine Zeit dauert, bis Bestände abfließen, wird eher akzeptiert als dass es eine Zeit dauert, bis in einem neuen Kanbanregelkreis ausreichend Bestände aufgebaut sind.
Um überhaupt nicht erst Zweifel an dem möglichen Erfolg eines neuen Kanbansystems aufkommen zu lassen, sollten Sie nie “aus einer Unterversorgung heraus” starten. Stellen Sie ein Teil möglichst erst dann auf Kanban um, wenn Sie die erforderlichen Supermarktbestände aufgebaut haben. Ist ein Kanbanregelkreis nicht lieferfähig wie geplant, kommen schnell Zweifel an der Zuverlässigkeit des gesamten Systems auf.
Kanbanregelkreise mit anfänglichen Überbeständen stellen kein wesentliches Problem dar. Sofern Sie das richtige Teilespektrum für Ihr Kanbansystem ausgewählt haben, werden die Überbestände schnell abfließen.
Best Practice Baustein 18: Vorderwasser gegen Kanbanhasser: Unternehmen, die Erfahrung mit der Einführung von Kanbansystemen haben, starten ihre Regelkreise möglichst immer mit ausreichenden Beständen oder aus Überbeständen heraus.
Trotz Fokus auf der Lieferbereitschaft wird von einem Kanbansystem zu Recht erwartet, dass die Bestände deutlich reduziert werden können. Dies ist fast immer richtig, denn es gilt
Grundprinzip 19: 30% sind meistens drin.
Die Erfahrung zeigt, dass in einem gut eingeführten Kanbansystem durchaus 30% Bestand gespart werden können. Auf den ersten Blick mag dies erstaunen. Eine sauber aufgebaute plangesteuerte Disposition sollte eigentlich in der Lage sein, mit weniger Beständen auszukommen als ein Kanbansystem.
Diese Überlegung ist im Kern richtig. Sofern bei Teilen mit einer regelmäßigen Nachfrage eine plangesteuerte Disposition wirklich sauber ausgelegt ist und alle Störgrößen beseitigt sind, dann lässt sich ein Bestandsniveau realisieren, das man mittels Kanbansystem nicht erreichen wird. Eine just-in-time Produktion stellt eine solche präzise ausgelegte plangesteuerte Disposition dar. Da sich mit vertretbarem Aufwand in der Praxis leider nicht alle Störungen vermeiden lassen, zeigt die Empirie, dass mit Kanbansystemen deutliche Bestandsverringerungen machbar sind.
Zwei weitere Effekte tragen ebenfalls zu den Bestandsvorteilen eines Kanbansystems bei:
- Kanbansysteme sind unempfindlich gegenüber Buchungsfehlern, denn ein Kanbansystem wird nach den physischen Beständen gesteuert. Ist eine Kiste leer, geht die Kanbankarte zurück zum Lieferanten, Inventurdifferenzen zwischen Buchbeständen und physischen Beständen stören ein Kanbansystem nicht.
- Kanbansysteme leiden im Allgemeinen auch nicht so sehr unter dem unseriösen Bestandslimbo, der in vielen Unternehmen zum Ende des Geschäftsjahrs oder gar quartalsweise stattfindet. Einerseits, weil esin Kanbansystemen umständlicher ist, in zahlreichen Regelkreisen die Bestände herunterzufahren, um sie wenig später wieder massiv hochzufahren., Andererseits, weil man bei Kanbanregelkreisen sensibler hinsichtlich ihrer Lieferfähigkeit ist.
Best Practice Baustein 19: Um das Potenzial der Bestandsreduzierung voll auszuschöpfen, legen erfolgreiche Kanban-Unternehmen Wert auf eine sorgfältige und nachhaltige Kanbaneinführung. Ein wesentlicher Erfolgsfaktor ist dabei das konsequente Beseitigen von Störgrößen.
Grundprinzip 20: Zuerst denken, dann handeln.
Als Filippo Brunelleschi 1420 mit dem Bau der Kuppel des Doms von Florenz begann, machte er etwas radikal Neues für seine Zeit und wurde damit zum Wegbereiter moderner Arbeitsorganisation: Er trennte Planung und Ausführung voneinander. Nur so war es ihm möglich, den gewaltigsten Kuppelbau seit der Antike zu realisieren.
Das Prinzip, erst zu Ende zu denken und dann umzusetzen, hat sich seitdem in der Welt – und auch bei guten Handwerkern – durchgesetzt.
Warum nur beginnen viele Projekte zur Kanbaneinführung dann damit, einen ersten Pilotregelkreis auszuwählen und fleißig Karten zu laminieren? Vom Laminieren der Kanbankarten scheint eine große Faszination auszugehen.
Auch wenn eine Kanbaneinführung keine Jahrtausendleistung ist, macht es auch hier Sinn, Planung und Ausführung voneinander zu trennen.
Der erste Schritt bei der Auslegung eines Kanbansystems besteht darin, die erforderlichen Stamm- und Bewegungsdaten zur Berechnung der Regelkreise zu überprüfen und zu korrigieren. Danach gilt es erst einmal, die gesamten Regelkreise zu dimensionieren.
Die Berechnung der Regelkreise ist der Ausgangspunkt für das Auslegen der gesamten Kanban-Infrastruktur: angefangen bei der erforderlichen Größe der Supermärkte, über die benötigte Fläche manueller Kanbantafeln und die Festlegung geeigneter Behältergrößen, bis hin zur Berechnung der erforderlichen Anzahl an Kanbanbehältern sowie die Überprüfung der Kapazitätsauslastung
Best Practice Baustein 20: Studieren geht vor Laminieren: Eine erfolgreiche Kanbaneinführung hat zuerst einmal viel mit Berechnung und Nachdenken und wenig mit dem Laminieren von Karten zu tun.
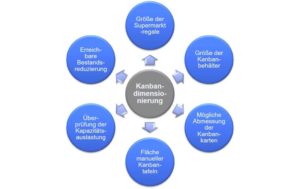