Die Konjunkturparameter deuten an, dass die Wirtschaft in den kommenden Monaten mehr zu kämpfen haben wird. Da mag es an der Zeit sein, wieder einen Blick auf die Bestände zu werfen. Diese binden nicht nur viel Kapital, das man in schlechteren Zeiten an anderen Stellen im Unternehmen evtl. dringend benötigen würde, sondern verursachen auch hohe laufende Kosten.
Ob Produktions- oder Handelsunternehmen, wir stehen alle vor dem Dilemma, zumindest einen Teil unserer Waren, Produktionsartikel oder Rohstoffe auf Lager zu halten, um kurzfristig die Kunden oder die eigene Fertigung bzw. Montage mit Material versorgen zu können. Einerseits muss man lieferfähig sein und andererseits die Bestände im Griff behalten.
Das Lösen dieses Dilemmas aus Lieferfähigkeit und Bestand überlässt man gerne der Disposition, der Logistik oder dem Supply Chain Management. Es ist jedoch ein großer Fehler von Unternehmern und Geschäftsführern, sich nicht für die Mechanismen des Bestandsmanagements zu interessieren und damit die Zusammenhänge nicht zu verstehen. Denn die richtige Positionierung zwischen Lieferfähigkeit und Bestand ist eine unternehmerische Aufgabe, deren Ausführung sich delegieren lässt, nicht aber die Verantwortung hierfür.
Wer die Grundmechanismen versteht und einige Knackpunkte beachtet, kann die erforderliche Lieferbereitschaft mit geringeren Kosten und Beständen erreichen und weiß andererseits, was zu investieren ist, um lieferfähig zu sein.
Lieferfähigkeit und Bestand: Nicht immer ein Dilemma…
Erfahrung und gesunder Menschenverstand besagen, dass eine höhere Lieferfähigkeit auch einen höheren Bestand erfordert. Dies stimmt aber nur zum Teil. Lassen Sie uns deshalb zuerst einen Blick auf die Kybernetik der Bestände werfen.
Ein Artikelbestand setzt sich grundsätzlich zusammen aus dem erforderlichen Bestand, um den sog. Grundbedarf zu befriedigen, sowie dem sog. Sicherheitsbestand. Der Grundbedarf entspricht dem durchschnittlichen Materialverbrauch während der Wiederbeschaffungszeit. Der Sicherheitsbestand soll dazu dienen, die Nachfrageschwankungen abzufangen, denn in praxi ist der Verbrauch pro Tag ja nicht konstant.
Vier Hauptparameter gibt es, die darüber entscheiden, wie extrem das Trade-off zwischen Lieferbereitschaft und Bestand ausfällt (Abb. 1):
- Die Schwankungsstärke der Bedarfe auf der Lagerabgangsseite,
- die Vorhersagbarkeit dieser Bedarfe,
- die geforderte Lieferbereitschaft,
- die Wiederbeschaffungszeit, um den Artikel nachzubevorraten.
Diese Parameter wirken vor allem auf den Sicherheitsbestand. Nur die Wiederbeschaffungszeit hat auch einen Einfluss auf den Grundbedarf. Dieser verhält ich nämlich proportional zur Wiederbeschaffungszeit: Die doppelte Wiederbeschaffungszeit bewirkt den doppelten Grundbedarf, eine Halbierung der Wiederbeschaffungszeit führt zum halben Grundbedarf.
Unter sonst konstanten Randbedingungen gilt, dass mit wachsender Lieferbereitschaft auch die erforderliche Bestandshöhe anwächst. Leider tut sie dies nicht proportional zur Lieferbereitschaft, sondern zunehmend progressiv. Besonders in Lieferbereitschaftsbereichen jenseits der 93% kann eine geringe Erhöhung der erforderlichen Lieferbereitschaft bereits eine Springflut an zusätzlich erforderlichem Bestand auslösen. Jenseits von 98% muss man mit einer Explosion der Bestände rechnen.
Wenn Sie es mathematisch genauer verstehen wollen:Je höher der geforderte Lieferbereitschaftsgrad ist, desto mehr “Standardabweichungen” an Sicherheitsbestand sind erforderlich. Die Standardabweichung ist eine Messgröße für die Schwankung der Nachfrage; je stärker die Schwankung, desto höher die Standardabweichung. Angegeben wird die Standardabweichung einfach in Form einer Stückzahl oder Tonnage des Artikels.
Das klingt schlimm, muss es aber nicht unbedingt sein. Wie stark die Bestände tatsächlich explodieren, hängt von den anderen oben aufgeführten Einflussparametern ab, der Vorhersagbarkeit der Bedarfe, der Schwankung der Bedarfe und der Wiederbeschaffungszeit.
Starke Bedarfsschwankungen, die Sie nicht vorhersehen können, wirken als Treibmittel für Ihre Bestandsexplosion. Starke Bedarfsschwankungen, die Sie vorhersehen, sind deutlich weniger kritisch. Eigentlich logisch, denn wenn Sie wissen, welche Bedarfe auf Sie zukommen, können Sie sich gut darauf einstellen und müssen keine hohen Sicherheitsbestände vorhalten. Bestimmte Arten von Bedarfsschwankungen kann man gut vorhersehen; Saisonalitäten beispielsweise. Ein großer Teil an Bedarfsschwankungen ergibt sich leider rein chaotisch. Ihnen kann man nur durch entsprechend hohe Sicherheitsbestände begegnen. An dieser Stelle setzt man in Fachkreisen große Hoffnung auf Entwicklungen in der künstlichen Intelligenz. Die bisherigen Ergebnisse sind allerdings noch sehr bescheiden.
Neben Bedarfsschwankungen und Vorhersagbarkeit der Bedarfe spielt auch die Wiederbeschaffungszeit bei der erforderlichen Höhe der Sicherheitsbestände eine Rolle. Der gesunde Menschenverstand sagt einem bereits, dass mit längerer Wiederbeschaffungszeit auch der Sicherheitsbestand größer ausfallen muss. Schließlich ist auch die Unsicherheit, wie die Bedarfe sich entwickeln, umso größer, je länger es dauert, auf wachsende Bedarfe reagieren zu können. Der Zusammenhang zwischen erforderlichem Sicherheitsbestand und der Wiederbeschaffungszeit ist allerdings unterproportional. Eine Verdoppelung der Wiederbeschaffungszeit erfordert nicht doppelt so hohe Sicherheitsbestände. Auch dies ist bei genauerer Betrachtung wieder logisch. Während einer längeren Zeitspanne können sich höhere Bedarfe in einem Zeitraum und niedrigere Bedarfe während eines anderen zum Teil wieder ausgleichen.
Schön, dass eine Verlängerung der Wiederbeschaffungszeit nicht so drastisch auf die Sicherheitsbestände wirkt. Aber Achtung, bei einer Verkürzung der Wiederbeschaffungszeit dreht sich das Spiel um. Wenn Sie es schaffen, die Wiederbeschaffungszeit zu halbieren, dann bedeutet dies eben nicht, dass auch die Sicherheitsbestände halbiert werden. Diese verringern sich in diesem Falle auch nur unterproportional. Je kürzer die Wiederbeschaffungszeit ist, desto geringer sind die Möglichkeiten, dass sich höhere Bedarfe eines Zeitraumes mit geringeren Bedarfen eines anderen Zeitraums ausgleichen.
Wenn Sie es mathematisch genauer wissen wollen:Konkret verändert sich der Sicherheitsbestand entsprechend der Wurzel des Quotienten der beiden betrachteten Wiederbeschaffungszeiten. Bei einer Verdoppelung der Wiederbeschaffungszeit erhöht sich der erforderliche Sicherheitsbestand nur um ca. 140% (Wurzel aus 2). Gelingt es, die Wiederbeschaffungszeit zu halbieren, sinkt der Sicherheitsbestand auf ca. 71% (Wurzel aus 0,5).
Die Risiken guter Lieferfähigkeit für die Wirtschaftlichkeit
Hat man die Kybernetik der Bestände einmal verstanden, dann ist klar, wo die Risiken hoher Lieferbereitschaft (93% oder höher) im Hinblick auf eine effiziente Lagerbestückung und -verwaltung liegen. Bei Artikeln mit starker Nachfrageschwankung führt die hohe Lieferbereitschaft zu hohen Sicherheitsbeständen. Diese binden nicht nur viel Kapital, sondern bedingen auch ein hohes Risiko, dass ein Teil der Bestände seinen Wert verliert:
- Artikel können ihr Mindesthaltbarkeitsdatum überschreiten,
- Artikel können technisch veralten,
- Artikel müssen aus buchhalterischen Gründen abgeschrieben werden.
Eine besondere Situation kann sich ergeben, wenn man gefordert ist, Artikel mit kurzem Shelf-Life und hoher Nachfrageschwankung hoch lieferfähig zu halten. Sie benötigen dann hohe Sicherheitsbestände, die die Bestandsreichweiten nach oben treiben, ggfs. sogar über die erlaubte Lagerhaltungsdauer des Artikels hinaus. Dies kann dazu führen, dass kontinuierlich Bestände vernichtet werden müssen, die ihr Haltbarkeitsdatum überschritten haben. Jenseits ökologischer Kriterien gilt in solchen Fällen: Wenn Sie diese Kosten nicht auf den Verkaufspreis umlegen können, sollten Sie die Lieferbereitschaft reduzieren!
Wenn Sie sich Ihr lagerhaltiges Produktportfolio ansehen, werden Sie vermutlich feststellen, dass Sie sich bei einem Teil Ihrer Artikel mit einer stark schwankenden Nachfrage konfrontiert sehen, während ein anderer, meist geringerer Teil, eine gleichmäßigere Nachfrage aufweist. Mit einer sogenannten XYZ-Analyse können Sie Ihre Artikel transparent nach der Größe der Bedarfsschwankungen in drei Klassen einteilen. X-Artikel weisen geringe und Z-Artikel weisen hohe Bedarfsschwankungen auf. Y-Artikel liegen dazwischen.
Wer es mathematisch genauer wissen will:Alle Artikel mit einem Variationskoeffizienten kleiner als 0,5 werden klassischerweise als X-Artikel, alle mit einem Wert bis 1 als Y-Artikel und alle darüberliegenden als Z-Artikel betrachtet.
Vermutlich haben Sie Ihre Artikel bereits in A-, B- und C-Klassen eingeteilt. Normalerweise klassifiziert man so, dass A-Artikel die ersten 80% des Umsatzes erbringen, B-Artikel weitere 15% erwirtschaften und die letzten 5% von den C-Artikeln erbracht werden. Jeden Ihrer lagerhaltigen Artikel können Sie nun einer ABC- und einer XYZ-Klasse zuordnen. Dieses ABC/XYZ-Portfolio hilft Ihnen bei der wirtschaftlichen Auslegung Ihrer Bestände sehr. Sie können es nutzen, um Bestandshöhen (und -kosten) und Umsatzbedeutung gegeneinander auszubalancieren.
Einerseits sollten Sie versuchen, bei den Artikeln mit stark schwankender Nachfrage (Z-Artikel) den Lieferbereitschaftsgrad zurückzunehmen, um die Lagerbestände auf einem wirtschaftlichen Niveau zu halten. Andererseits sollten Artikel mit hoher Umsatzbedeutung (A-Artikel) lieferfähiger gehalten werden als C-Artikel. Im ABC/XYZ-Portfolio versucht man die Lieferbereitschaft über die neun Portfoliofelder so zu “verteilen”, dass man bei AX-Artikeln eine sehr hohe Lieferbereitschaft anstrebt, die Richtung AY-Feld und AZ-Feld abnimmt. Auch mit dem abnehmenden Beitrag der Artikel zum Gesamtumsatz des Unternehmens reduziert man im allgemeinen die Lieferbereitschaft. Ein BX-Artikel hat also auch bereits weniger Lieferbereitschaft als ein AX-Artikel, aber mehr als ein CX-Artikel.
Für diejenigen, die höher am technologischen Wind segeln möchten:Mit entsprechenden Optimierungsalgorithmen lässt sich diese Lieferbereitschaftsverteilung in Abhängigkeit von dem erlaubten Gesamtbestand automatisch ermitteln. Umgekehrt funktioniert die Optimierung auch: abhängig von einer geforderten Gesamtlieferbereitschaft werden die Bestände in den Portfoliofeldern so ausbalanciert, dass die Gesamtlieferbereitschaft mit möglichst geringem Gesamtbestand erreicht wird.
Sie sehen, man kann viel tun. Die statistischen Wirkmechanismen hinter der Kybernetik der Bestände lassen sich allerdings nicht austricksen. Maximale Lieferbereitschaft bei minimalem Bestand lässt sich leider nicht realisieren. Hohe Lieferbereitschaft tut nicht bei jedem Artikel weh. Bei einer ganzen Reihe von Artikeln muss man sich aber zwischen kommoden Beständen und hoher Lieferbereitschaft entscheiden.
Hohe Lieferfähigkeit ist nicht immer nötig
Der Vertrieb fordert zumeist hohe Lieferbereitschaft bei Fertigartikeln. Daraus spricht die Angst, bei fehlender Lieferbereitschaft Umsatz zu verpassen: Wenn Ihr Vertrieb nicht liefern kann, dann gehen die Kunden zum Wettbewerb. Ganz so konsequent ist der Zusammenhang zwischen Lieferbereitschaft und Umsatzverlust eigentlich nur bei Commodities, die an jeder Straßenecke zu bekommen sind. Machen Sie die Probe aufs Exempel und fragen Ihren Vertrieb (oder sich selbst) einmal, was passiert, wenn ein Artikel einmal nicht verfügbar ist. Im B-to-B-Bereich passiert im Extremfalle nichts, weil sie die fehlende Menge einfach mit der Folgelieferung mitschicken können. Im B-to-C-Bereich dauert eine Lieferung bei einer fehlenden Komponente einmal etwas länger. Langfristig vertreibt unzuverlässige Lieferfähigkeit die Kunden, wenn es für den Kunden aber ein seltenes Erlebnis bleibt, zerbricht daran nicht die Welt. Mit einigen Ansatzwerten lässt sich die Höhe der wirtschaftlichen Lieferbereitschaft eines Artikels sogar abschätzen.
Der Markt ist, wie er ist. Was lässt sich trotzdem tun, um die Bestände zu senken?
Ein nochmaliger Blick auf die Kybernetik der Bestände zeigt uns einige weitere Möglichkeiten jenseits der Differenzierung des Lieferbereitschaftsgrades auf, um die Bestände durch dispositive Maßnahmen zu senken.
Reduzierung der Wiederbeschaffungszeit: Dass die Reduzierung der Wiederbeschaffungszeit sich positiv auf Bestände auswirkt, haben wir bereits angesprochen. Der erforderliche Bestand, um den Grundbedarf zu decken, reduziert sich proportional zur Wiederbeschaffungszeit. Der Sicherheitsbestand sinkt unterproportional, aber er sinkt ebenfalls.
In unseren Beratungsprojekten machen wir regelmäßig die Erfahrung, dass Wiederbeschaffungszeiten bei weitem nicht so unveränderlich sind, wie häufig erwartet. Es macht deshalb Sinn, bei Artikeln, die regelmäßig beschafft oder produziert werden, zu prüfen, ob sich an den Wiederbeschaffungszeiten nicht etwas bewegen lässt.
Manchmal hilft es bereits, einmal anzufragen, ob eine kürzere Lieferzeit nicht machbar wäre, denn die Pflege von Wiederbeschaffungszeiten erfolgt oft nicht so akkurat, wie es sinnvoll wäre. Lieferanten, aber auch die eigene Produktion, beschweren sich selten, wenn der Kunde eine längere Wiederbeschaffungszeit als gegeben hinnimmt.
Die Frist, die für die Nachlieferung eines Artikels benötigt wird, sei es aus der eigenen Produktion, sei es von einem Lieferanten, ist häufig weniger von der eigentlichen Fertigungszeit abhängig, als von den Warte- und Liegezeiten, bis die Fertigung oder der nächste Fertigungsschritt begonnen werden kann. In solchen Fällen hilft es zu überlegen, was man tun kann, um die Warte- und Liegezeiten zu verkürzen. Diskutieren kann man…
- Rohmaterialfreigaben, damit der Lieferant nicht erst bei Bestellung eines Artikels das erforderliche Rohmaterial beschaffen muss,
- Vorproduktion bis zu einer Zwischenlagerstufe, ab der viele unterschiedliche Produktvarianten gefertigt werden,
- Anpassen technischer Spezifikationen.
Erstaunliche Effekte ergeben sich zuweilen, wenn man den Spielraum hat, die geforderte Produktspezifikation mit Lieferanten zu diskutieren. Kleine Änderungen an den technischen Spezifikationen erlauben es manchmal, die Fertigungsprozesse und damit auch die Durchlaufzeiten deutlich zu verkürzen.
Verringerung der Eindeckzeit: Auch die Reduzierung der sogenannten Eindeckzeit ist ein probates Mittel zur Bestandsreduzierung. Es wirkt zwar nur auf den Grundbestand, also den Bestand, der zur Deckung des Grundbedarfes erforderlich ist. Aber auch in den Fällen, in denen die Wiederbeschaffungszeit nicht zu verkürzen ist, kann man noch an der Eindeckzeit drehen. Unter “Eindeckzeit” versteht man den Zeitraum, für dessen voraussichtlichen Bedarf man sich bei einer Bestellung oder einem Fertigungsauftrag mit Material versorgen möchte. Ein Beispiel macht den Sachverhalt deutlich:
Bei einer Wiederbeschaffungszeit von 10 Arbeitstagen und einem durchschnittlichen Verbrauch von 50 Stück pro Tag beträgt der Grundbedarf und damit der Grundbestand 500 Stück. Wenn Sie alle 10 Tage Material nachbeschaffen, dann bestellen Sie jeweils mit einer Losgröße von 500 Stück. Die Eindeckzeit beträgt in diesem Falle, genauso wie die Wiederbeschaffungszeit, 10 Tage. Sie könnten sich auch dazu entscheiden, sich für jeweils nur 5 Tage einzudecken, also alle 5 Tage nachzubevorraten. In diesem Falle würden Sie alle 5 Tage 250 Stück bestellen, die nach 10 Tagen geliefert werden würden. Ehe die erste Bestellung geliefert wird, ist die zweite Bestellung schon platziert.Im beiden Fällen entspricht der durchschnittliche Lagerbestand der halben Bestelllosgröße + dem Sicherheitsbestand. Im ersten Falle wären dies 250 Stück, im zweiten nur 125 Stück, jeweils plus Sicherheitsbestand. Der Gesamtbestand wurde dadurch nicht halbiert, denn der Sockel an Sicherheitsbestand bleibt in beiden Fällen gleich. Ist dieser Sockel sehr hoch, kann der Effekt gering ausfallen. Bei Artikeln mit geringem Sicherheitsbestand wirkt dieser Hebel allerdings drastisch.
Verringerung der Mindestlosgröße: Zuweilen kommt man mit der Verringerung der Eindeckzeit nicht so weit, wie man gerne möchte, weil der Lieferant oder die eigene Produktion auf einer Mindestlosgröße bestehen. Dann nützt es nicht, wenn Sie sich nur für einen kurzen Zeitraum mit Material versorgen wollen, die Mindestlosgröße Sie aber dazu zwingt, Mengen abzunehmen, die Ihre Bedarfe für deutlich längere Zeit decken.
Ein Bestandsreduzierungsinitiative sollte auch hier rütteln und prüfen, ob nicht auch an den Mindestlosgrößen gedreht werden kann. Gründe für Mindestlosgrößen in der Produktion sind zumeist die Rüstzeiten. Wenn das Rüsten einer Anlage aufwändig ist und lange dauert, dann möchte die Produktion aus Effizienzgründen auch länger fertigen dürfen und damit größere Fertigungslose abliefern. Projekte zur Reduzierung von Rüstzeiten können in solchen Fällen helfen, die Bestände in der Wertschöpfungskette zu senken.
Verstetigung des Bedarfes: Gleichmäßigere Bedarfe führen zu geringeren Bedarfsschwankungen und diese automatisch zu geringeren Sicherheitsbeständen bei gleicher Lieferbereitschaft. Aus diesem Grunde lohnt es sich auch, über diesen Hebel nachzudenken. Im B-to-C-Bereich sind die Möglichkeiten eher gering, es sei denn, Sie finden Ansatzpunkte, um den Kunden zu motivieren, gegebenenfalls auf seine Bestellung zu warten. Zuweilen kann es sinnvoll und wirtschaftlich sein, dem Kunden einen Rabatt dafür einzuräumen, dass er sich etwas geduldet. Im B-to-B-Segment lassen sich eher Ansatzpunkte finden, denn Bedarfsschwankungen bei Artikeln resultieren nicht immer aus korrespondierenden Bedarfsschwankungen auf Kundenseite. Teilweise werden durchaus gleichmäßige Bedarfe zu großen Bestelllosen zusammengefasst. Die Überlagerung großer Bestelllose unterschiedlicher Kunden führt letztlich zu starken Bedarfsschwankungen bei einem Artikel.
Bestellen Ihre Kunden bei Ihnen lagerhaltige Artikel, könnte es sinnvoll sein, die eigenen Mindestbestellmengen zu reduzieren, um die Kunden zu motivieren, häufiger kleinere Mengen zu bestellen. Aufsummiert über alle Kunden kann dies die laufenden Kosten für Sicherheitsbestände stärker senken als es die Frachtkosten erhöht. Dies gilt besonders dann, wenn der Kunde bei Ihnen noch mehrere andere Teile bestellt, sodass sich die Zahl der Lieferungen gar nicht unbedingt erhöhen muss, sondern lediglich die Anzahl der Lieferpositionen steigt. Zur Verdeutlichung ein einfaches Beispiel: Anstatt in einer Woche Produkt A in großer Losgröße zu liefern und an der Folgewoche Produkt B, könnten auch jede Woche Produkt A und Produkt B, dann in halbierten Losgrößen, geliefert werden.
Jenseits der angerissenen dispositiven Maßnahmen gibt es auch eine Reihe organisatorischer Maßnehmen in der Zusammenarbeit mit Lieferanten, die Ihnen helfen können, Bestände zu reduzieren. An dieser Stelle seien zwei angesprochen: Konsignationslager und Vendor Managed Inventory.
Unter einem Konsignationslager versteht man ein Lager, das sich typischerweise in der Nähe eines Kunden oder in dessen Räumlichkeiten befindet. Entscheidend dabei ist, dass die Ware Eigentum des Lieferanten bleibt, bis sie entnommen wird. Für Sie als Kunde hat das Konsignationslager den Vorteil, dass die dort enthaltenen Bestände nicht auf Ihre Kapitalbindung gehen. Andererseits fallen im Allgemeinen alle weiteren Lagerhaltungskosten auf Ihrer Seite an. Für die Versicherung der Warenbestände, für das Obsoleszenzrisiko übernehmen Sie die Verantwortung und es sind auch Ihre Lagerkapazität, Ihre Lagertechnik und Ihr Lagerpersonal, die eingesetzt werden.
Unter Kostengesichtspunkten ist eine Konsignationslagerlösung für Sie als Kunden also nicht immer von Vorteil. Wie sieht es aus, wenn Sie als Lieferant von Ihren Kunden gezwungen werden, Konsignationsläger zu unterhalten? Unter Kostengesichtspunkten kann dies durchaus ein Vorteil sein, wenn Sie es schaffen, auf Ihrer Seite im Unternehmen auf weitere Bestände dieser Artikel für diesen Kunden zu verzichten.
Bleibt noch die Kapitalbindung, aber auch an dieser lässt sich evtl. in den Verhandlungen mit Ihren Kunden noch etwas drehen. Genaugenommen ist es ja nicht entscheidend, ob Kapital in der Form von Beständen gebunden ist oder in der Form von Forderungen gegenüber den Kunden. Ein Konsignationslager mit einer Bestandsreichweite und damit einer Kapitalbindung von drei Monaten und sofortiger Zahlung der entnommenen Mengen durch den Kunden stellt sich nicht schlechter dar als Materiallieferungen, die direkt in Rechnung gestellt, vom Kunden aber erst mit einer Frist von 90 Tagen bezahlt werden. Versuchen Sie beim Einrichten eines Konsignationslagers mit Ihrem Kunden deshalb, kurze Zahlungsfristen zu verhandeln.
Ein Vendor Managed Inventory (VMI)-Konzept wird oft als Weiterentwicklung des Konsignationslagerkonzeptes verstanden. Genaugenommen handelt es sich dabei um einen Mechanismus, der in Kombination mit einem Konsignationslager, aber durchaus auch ohne Konsignationslager betrieben werden kann. Grundgedanke des VMI ist, dass der Lieferant die Bestände seiner Artikel im Lager des Kunden selbst nachdisponiert. Dazu werden zumeist ein Minimalbestand und ein Maximalbestand je Artikel festgelegt, zwischen denen sich der Bestand des Artikels bewegen muss. Wann genau der Lieferant nachliefert, bleibt diesem überlassen; entscheidend ist nur, sich mit dem Bestand zwischen den beiden Grenzen zu bewegen.
Ein VMI-Mechanismus bedeutet für den Lieferanten zwar zusätzlichen Aufwand für die Artikeldisposition, kann sich aber positiv auf die Bestände auswirken. VMI erlaubt es Ihnen nämlich, sich von den oft stochastischen Bestellmechanismen Ihrer Kunden zu entkoppeln. Häufig stellen wir fest, dass Lieferanten Artikel, die sie regelmäßig an Kunden liefern, nicht kundenauftragsbezogen fertigen (können) und sie deshalb auf Lager legen, um auf die Bestellungen der Kunden ausreichend schnell reagieren zu können. In solchen Fällen können Sie von einem VMI-Konzept profitieren, weil die Entkopplung von der Bestellauslösung durch den Kunden es ermöglicht, die Nachfertigung zu verstetigen. Damit können Sie nicht nur Ihre Auslieferbestände an die Lieferanten verringern, sondern reduzieren Bedarfsschwankungen evtl. sogar in der gesamten Liefer- und Produktionskette, was in der gesamten Kette zu geringeren Sicherheitsbeständen führen kann.
Endlich auf Technik setzen!
Wie lässt sich ein wirkungsvolles Bestandsmanagement in der Praxis umsetzen? Nicht so, wie es heute noch in vielen Unternehmen geschieht: von Hand!
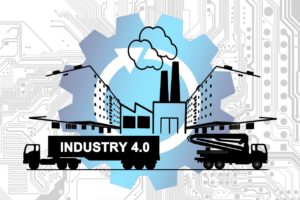
Wir diskutieren über Industrie 4.0 und sprechen davon, dass wir die Arbeitsproduktivität steigern müssen und dass uns überall Personal fehlt. Trotzdem basteln viele Unternehmen ihre Bestände von Hand zusammen. Die meisten Unternehmen nutzen zwar ein ERP-System oder ein Warenwirtschaftssystem, doch diese Systeme werden in der Materialplanung oft nur als teure Schreibmaschinen genutzt. Um zu einem wirkungsvollen Bestandsmanagement zu gelangen, ist es wichtig zu verstehen, dass der Mensch einen der größten Bestandstreiber im Unternehmen darstellt.
Da ist zum einen die Disponentin, die zwar gehalten ist, ihre Bestände gering zu halten, die aber auch sofort Druck erfährt, wenn einige der von ihr disponierten Artikel “trocken fallen”. Fehlende Materialbestände führen meist zu hektischem Bemühen, das erforderliche Material möglichst schnell herbeizuschaffen. Überhöhte Bestände hingegen entspannen die Tagesarbeit und führen weit seltener zu unangenehmen Gesprächen. Man kann es den Disponenten nicht verdenken, dass Sie eher auf “Nummer Sicher” fahren. Der Effekt wird noch verstärkt, wenn sich die Geschäftsführung nicht eindeutig hinter die angestrebte Bestandssenkung stellt und der Disposition den Rücken freihält. In einem Projekt meinte einmal ein Geschäftsführer: “Sagen Sie uns als Experten bitte, welche Lieferbereitschaftsgrade wir bei unseren Artikeln einstellen sollen, für mich ist nur wichtig, dass wir immer lieferfähig sind!” Solches Denken führt zuverlässig zu Bestandserhöhung. Als Geschäftsführer müssen Sie sich klar darüber sein, dass man Nichtlieferfähigkeit aushalten muss. 98% Lieferbereitschaft beispielsweise bedeuten explizit, dass 2% der Bedarfsmenge gezielt nicht fristgerecht geliefert werden sollen; einfach, weil dies zu teuer wäre! Disponenten mache ich deshalb gerne deutlich, dass ich ihre Aufgabe nicht darin sehe, 98% Lieferbereitschaft zu erreichen, sondern sicherzustellen, dass 2% der Bedarfe nicht sofort verfügbar sind.
In letzter Konsequenz kann sich ein Mensch bei seinen Dispositionsentscheidungen nicht vollständig von seinen Emotionen abkoppeln. Zu strategischer Ruhe statt operativer Hektik in der Materialplanung gelangen Sie nur, wenn Sie stärker auf die Planungsalgorithmen Ihrer IT-Systeme setzen. Der Mensch sollte in die Dispositionsvorschläge des Planungssystems nur eingreifen, wenn er über Zusatzinformationen verfügt, die in den Dispositionsvorschlag des Planungssystems nicht eingeflossen sind. Voraussetzung für dieses Handlungsprinzip ist allerdings, dass die Artikelstammdaten und die Parameter der Algorithmen richtig gesetzt sind und dass Ihr Planungssystem über die richtigen Algorithmen verfügt. Es gibt heute bewährte Mechanismen, um Artikelstammdaten kontinuierlich, größtenteils automatisch und mit wenig Aufwand nachzupflegen. An dieser Stelle sei als Stichwort nur “Dispositionsregelwerk” genannt.
Etwas ausführlicher möchte ich auf die Herausforderungen bei den Algorithmen zur Prognose- und Sicherheitsbestandsermittlung eingehen, denn diese werden in den meisten ERP- oder Warenwirtschaftssystemen nicht beachtet, was gravierende negative Auswirkungen auf Bestände und Lieferbereitschaft haben kann. Um diese Herausforderungen zu verstehen, müssen wir nochmals einen kurzen Ausflug in die Statistik unternehmen.
Warum Ihr ERP-System zu falschen Prognosen und Sicherheitsbeständen führt
Vermutlich haben Sie schon einmal von der Gaußschen Normalverteilung gehört. Diese beschreibt, sehr vereinfacht ausgedrückt, auf welche Weise sich Messwerte wiederkehrender Ereignisse symmetrisch um ihren Mittelwert herum verteilen. In der Natur sind praktisch alle gemessenen Werte normalverteilt. Misst man die Körpergrößen der erwachsenen Bevölkerung so kann man daraus eine durchschnittliche Körpergröße ermitteln. Um diesen Mittelwert herum schwankt die Größe der individuellen Personen, und zwar so, dass ein Großteil der Personen eng um den Mittelwert herum liegt, während es nur eine geringe Anzahl extrem großer und extrem kleiner Menschen gibt. Dieses Normalverteilungsprinzip gilt für viele Werte in der Natur.
Leider gilt diese Gesetzmäßigkeit der Normalverteilung bei den Marktbedarfen eines Artikels nur begrenzt. Die meisten Artikel weisen bedauerlicherweise keine normalverteilte Nachfrage auf. Alle klassischen Prognoseverfahren und Verfahren zur Ermittlung von Sicherheitsbeständen unterstellen aber, dass die Nachfrage „normalverteilt“ ist. Wendet man die entsprechenden Formeln an, um aus den Abverkäufen oder Lagerabgängen der Vergangenheit auf die zukünftigen voraussichtlichen Marktbedarfe zu schließen, entstehen Berechnungsfehler. Prognosewerte und Sicherheitsbestände werden entweder zu hoch oder zu niedrig ausgewiesen. In der Folge halten Sie entweder mehr Bestand, als erforderlich und kommen damit zu einer Lieferbereitschaft, die höher ist, als gewünscht, oder Sie verfügen über zu wenig Bestand und erreichen damit die geforderte Lieferbereitschaft nicht. In der Konsequenz kämpfen Sie bei einigen Artikeln mit Überbeständen und sind bei anderen nicht ausreichend lieferfähig. Kommt Ihnen das bekannt vor?
Ob die Nachfrage nach Ihren Artikeln normalverteilt ist oder nicht, können Sie einfach selbst überprüfen: Ermitteln Sie für die Artikel aus den monatlichen Verbrauchsmengen der letzten 12 oder 24 Monate den Mittelwert und den Median und vergleichen Sie die beiden Kennwerte je Artikel miteinander. Sofern Mittelwert und Median auseinanderfallen, liegt keine normalverteilte Nachfrage vor. Wenn Median und Mittelwert zusammenfallen, kann eine normalverteilte Nachfrage vorliegen, muss aber nicht.
Wie kann man mit dem Problem der fehlenden Normalverteilung bei Prognose und Sicherheitsbestandsermittlung umgehen? Bei bestimmten Artikeln sind die Fehler gering, hier reichen die klassischen Verfahren aus. Beim vorgeschlagenen Nachrechnen werden Sie evtl. festgestellt haben, dass bei den regelmäßigen Artikeln (X-Artikel) keine großen Abweichungen zwischen Median und Mittelwert auftreten, bei den Y- und Z-Artikeln aber schon. Bei X-Artikeln reichen die klassischen Verfahren deshalb eher.
Bei den unregelmäßigeren Artikeln sollte man jedoch sogenannte „verteilungsfreie Verfahren“ einsetzen. Diese Verfahren sind vor allem bei der so kritischen Sicherheitsbestandsermittlung wichtig. Leider werden sie in den mir bekannten ERP-Systemen nicht angeboten, sondern nur in ausgewählten Spezialsystemen für Absatzprognose. Für die Prognosewelt in Excel sind sie zu kompliziert.
Zuweilen kann Ihnen ein Provisorium weiterhelfen, das von den meisten ERP-Systemen auch nicht bereitgestellt wird, aber per Tabellenkalkulation bewältigt werden kann, der „Forecast-Bias“. Der Forecast Bias beschreibt, ob eine Prognose regelmäßig zu große oder zu kleine Prognosewerte liefert. Wenn Ihre Prognose immer etwas zu niedrig ausfällt, müssen Sie die Prognosewerte um einen Korrekturwert erhöhen oder andersherum senken. Der Forecast-Bias hilft Ihnen nur bei den Prognosewerten weiter, nicht bei den so wichtigen Sicherheitsbeständen.
Noch einen Schritt weiter als verteilungsfreie Verfahren geht der Mechanismus der simulativen Prognoseermittlung. Auch dieser Mechanismus bleibt Spezialsystemen vorbehalten. Lassen Sie uns deshalb abschließend einen Blick auf solche Spezialsysteme werfen.
Zusatzsoftware für Absatzprognose, Sicherheitsbestandsermittlung und Bestandsmanagement kann sich schnell rechnen
ERP-Systeme sind generalistische Systeme. Sie müssen für ein breites Spektrum von Aufgaben Unterstützung bieten. Da verwundert es nicht, dass nur die größeren Anbieter die Ressourcen haben, sich auch um Spezialthemen zu kümmern und Speziallösungen für bestimmte Aufgabenstellungen zur Verfügung zu stellen. Oft sind diese Lösungen dann auch sehr teuer. So gibt es eine breite Palette spezieller Zusatzprogramme der Bedarfsprognose, Materialdisposition und Bestandsmanagement.
Generell lassen sich vier Gruppen von Zusatzsystemen unterscheiden: Die erste Gruppe besteht aus Systemen, die nur auf ein spezielles ERP-System ausgelegt sind. Diese Systeme laufen meist “im” entsprechenden ERP-System. Sie bieten damit eine enge Integration, die aber auf Kosten der Flexibilität und Lösungstiefe gehen.
Die zweite Gruppe umfasst Low-End-Systeme. Sie sind kostengünstig, bieten aber nur eine sehr beschränkte Funktionalität. Die Zielgruppe dieser Systeme sind kleine Unternehmen, die gezwungen sind, bei der Funktionalität Kompromisse zu machen, da sie meinen, sich teurere, leistungsfähigere Systeme nicht leisten zu können. Diese Gruppe von Add-On-Systemen macht nur bei sehr einfachen ERP- oder Warenwirtschaftssystemen Sinn, da ihre Leistungsfähigkeit kaum über das hinaus geht, was leistungsfähigere ERP-Systeme selbst mitbringen. Allerdings ist die Benutzeroberfläche bei diesen Add-On-Systemen anwenderfreundlicher, als bei vielen ERP-Systemen.
In eine dritte Gruppe von Zusatzsystemen für die Materialplanung fallen High-End-Systeme, die oft für Großkonzerne in spezielle Branchen gedacht sind und preislich extrem hoch liegen.
Letztlich gibt es eine Gruppe von Systemen, die auf mittelständische Betriebe ausgerichtet sind. In dieser Gruppe von Systemen finden die meisten Unternehmen das beste Preis-/Leistungsverhältnis für ihre Problemstellung. Leistungsumfang und Leistungstiefe der etablierten Systeme in diesem Markt sind hoch, allerdings gibt es auch hier deutliche Preis- und Leistungsunterschiede. Der Funktionsumfang dieser Systeme genügt zumeist auch den Anforderungen der Großindustrie. Die Anbieter sind aber selbst mittelständisch und verfügen nicht über Vertriebsstrukturen, wie man sie für Konzern-Kunden benötigt. Mit diesen Systemanbietern können mittelständische Anwenderunternehmen auf Augenhöhe kommunizieren; ein nicht zu unterschätzender Vorteil bei der Systemeinführung und laufenden Betreuung.
Noch ein Software-Programm neben dem ERP-System? Aus meiner Perspektive eine klare Empfehlung auf Grund wirtschaftlicher Überlegungen: Leistungsfähige Zusatzsysteme, die den vorausgehend beschriebenen Anforderungen entsprechen, können sich bereits ab einer Bestandshöhe von durchschnittlich einer Million Euro rechnen. Ab 5 Mio Bestand ist es eigentlich nicht entschuldbar, auf den Effekt dieser Systeme zu verzichten, weil Sie ansonsten laufend Geld verlieren und unnötiges Kapital binden. Denn jede Million an unnötigem Bestand kostet Sie schnell 190.000 bis 300.000€ Ertragsverlust pro Jahr!
Foto: Manu Dias/AGECOM