KANBAN. Für erhöhte Flexibilität und reduzierte Lagerbestände sorgt bei Chiron nun die Just-in-time-Montage. Kanban macht dabei Abläufe transparent.
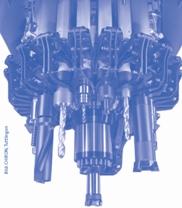
Bei der Einführung der Just-in-time-Montage (JIT) von Werkzeugarmen zum Werkstückwechsel in CNC-Fertigungszentren sowie für die Beschaffung und Produktion der dafür benötigten Baugruppen und Komponenten hat Chiron kürzlich ein Kanban-System unter SAP eingeführt. Ziel dieser Umstellung auf JIT war zum einen die Verbesserung der Lieferbereitschaft und zum anderen eine Reduzierung der Lagerbestände. Bei der Umsetzung mit SAP galt es einiges zu beachten, um verkürzte Durchlaufzeiten, reduzierte Lagerbestände sowie hohe Flexibilität und Lieferbereitschaft optimal zu justieren. Angestrebt wurde die Realisierung eines Karten-Kanban-Systems mit Anbindung an das SAP-Kanban-System. Dies sollte ohne Anpassungsprogrammierung sichergestellt werden. Hierzu waren viele Details zu beachten, um eine erfolgreiche Kanban-Einführung zu gewährleisten, denn das Konzept wurde grundsätzlich nicht SAP-“normiert”, sondern funktionsoptimiert entwickelt. Insbesondere die Anforderung, ein Sammel-Kanban mit Ampelsteuerung in SAP umzusetzen, war schwierig, da der SAP-Standard Sammel-Kanban als eigenständige Funktion nicht anbietet. Im SAP-Standard wird stattdessen für jeden Kanban-Behälter ein Fertigungsauftrag ausgelöst, auf den jeweils auch die hinterlegten Rüstzeiten gebucht werden. Die Kanban-Behälter so lange zu sammeln, bis die erforderliche Losgröße erreicht ist, und nur über diese Losgröße einen Kanban-Fertigungsauftrag mit einer Rüstzeit zu generieren, war ohne Anpassungsprogrammierung erst durch die Kombination von zwei SAP-Regelkreisen – bestehend aus Losfertigungs-Kanban und Umlagerungskanban – möglich.
Regelkreis-Dimensionierung.
Eine weitere Anforderung an ein optimiertes Kanban-System ist mit SAP jedoch nicht hinreichend umsetzbar: Die Regelkreis-Dimensionierung. Sie ist regelmäßig vorzunehmen, denn Schwankungen in der Kundennachfrage, Veränderungen der Produktionsabläufe und der Produktionsparameter sind immer gegeben. Normalerweise erfolgt die Regelkreis-Dimensionierung jedoch nur über die „klassische” Kanban-Formel, die auch im SAP-Modul PP zur Anwendung kommt. Optimale Kanban-Regelkreise werden allerdings nur dann erzielt, wenn weitere Stellgrößen mit einfließen, etwa die Losgröße des Lieferanten beziehungsweise Kunden, das Verbrauchsverhalten des Artikels (XYZ-Verhalten) oder die Liefertreue. Aus diesem Grund wird bei Chiron die Kanban-Dimensionierung von Abels & Kemmner eingesetzt. Aus den SAP-Verbrauchs- oder SAP-SOP-Daten entnimmt sich diese den Bedarf der Werkzeugarme und ermittelt daraus die Stücklistenauflösung für alle kanban-gesteuerten Komponenten. Diese Werte bilden die Grundlage für die Dimensionierung, weil aus ihnen für jede Komponente der Grund- und Sicherheitsbestand in Abhängigkeit vom Verbrauchsverhalten ermittelt wird. Über die definierten Parameter jeder einzelnen Komponente und einen Simulationszeitraum von fünf Jahren wird nun getestet, wie viele Kanbans in das System eingesteuert werden müssen. Dabei wird der Sicherheitsbestand laufend überwacht, ob er ausreicht, damit das System nicht leer läuft, beziehungsweise ob keine überflüssigen Kanban-Behälter im System zirkulieren.
Die Praxis.
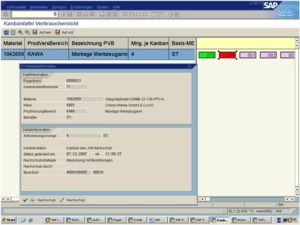
Die Umstellung auf die JIT-Fertigung mit Kanban-Steuerung bedurfte zuerst einer organisatorischen Veränderung in den betroffenen Bereichen: Die Werkzeugarm-Montage erhielt ein neues Montagelayout. Aufgrund geringer Rüstzeiten und kurzer Durchlaufzeiten können die Werkzeugarme mit der Losgröße 1 montiert werden und kurzfristig für die Endmontage der Fertigungszentren bereitgestellt werden. Die Abrufe werden über das so genannte ereignisgesteuerte SAP-Kanban ausgelöst. Das Logistikzentrum löst seinen Bedarf in SAP aus und generiert damit einen Fertigungsauftrag in SAP, der unmittelbar danach in der Werkzeugarm-Montage ausgedruckt wird. Diese muss ihren Bedarf mit einer Durchlaufzeit von maximal zwei Tagen bedienen. Dann müssen die Werkzeugarme fertig zum Versand dem Logistikzentrum zur Verfügung stehen.
Problem Ersatzteil.
Ersatzteilbestellungen von Kunden allerdings müssen teilweise unmittelbar und direkt bedient werden können. Um dies gewährleisten zu können, wurde ein eigener Kanban-Regelkreis für Ersatzteile in SAP angelegt. Die Steuerung erfolgt hier klassisch über Kanban-Karten, die an den Werkzeugarmen befestigt sind. Damit eine immer ausreichende Bestückung mit Komponenten und Baugruppen gewährleistet ist, wurde das Komponentenlager zur Versorgung der Werkzeugarm-Montage als Kanban-Lager vor der Werkzeugarm-Montage ausgelegt. Durch diese Vorgehensweise wurde es möglich, die verstärkte Lagerhaltung weg vom Werkzeugarm und zurück auf eine geringere Wertschöpfungsstufe zu verlegen (Komponenten statt Werkzeugarme).
http://www.chiron-werke.de/
https://www.ak-online.de/
Vom Push- zum Pull-Prinzip
Beim ursprünglich in Japan entwickelten Kanban-System darf nur nachproduziert oder nachgeliefert werden, wenn ein Verbrauch einer bestimmten Menge, eines bestimmten Artikels an einer bestimmten Stelle stattgefunden hat. Als Informationsträger zur Kommunikation zwischen dem produzierenden und dem abnehmenden Bereich dienen hierbei Karten (Kanban) oder die Produktions-/Transportbehälter selbst. Material wird damit nur dem tatsächlichen Verbrauch entsprechend nachgezogen. Kanban ist einfach, es fordert und fördert die eigenverantwortliche Steuerung produzierender Einheiten und schafft Transparenz über Verbrauch und Bestände.