PROZESSE – Bestandsmanagement
SCM Mit dem Projekt „Logistics 2010″ poliert Hansgrohe seine Supply Chain. Maßnahmen wie Lieferantenkanban und bedarfsgesteuerte Beschaffung bescheren dem Sanitärspezialisten erste Erfolge.
Logistik ist eines unserer Kernthemen der nächsten Jahre. Das Projekt „Logistics 2010″ hat für Hansgrohe eine außerordentlich strategische Bedeutung”, erklärt Siegfried Gänßlen, Finanzvorstand der Hansgrohe AG, Schiltach. Der weltweit tätige Sanitär- und Badspezialist war in den letzten Jahren stark gewachsen: Der Umsatz kletterte im Zeitraum 1996 bis 2005 von 224 Mio. auf 476 Mio. Euro. Mit dem Wachstum kamen aber auch Probleme: So hatte Hansgrohe mit steigenden Beständen zu kämpfen. Auch der Anteil der Logistikkosten nahm zu.
Bereits im Januar 2005 startete Hansgrohe daher das Projekt „Logistics 2010“ und wagte sich zuerst an seine Produktion und Beschaffung. Zwar agierte Hansgrohe hier bereits auf hohem Niveau. Die Beschaffungsvorgänge wurden durchgehend vom SAP-System abgebildet und unterstützt und mit vielen Lieferanten bestanden bereits Rahmenverträge mit Lieferabrufen. Zudem hatte das Unternehmen ein leistungsfähiges Lieferanteninfo-Tool „Lextra“. Hierbei handelt es sich um eine Internetplattform, auf der sich die Lieferanten alle nötigen und ergänzenden Informationen abrufen können. „Aber wir hatten viel zu viel Bestände von Lieferanten bei uns im Werk. Das mussten wir ändern“, sagt Ulrich Jaeckle, Leiter Einkauf/Logistik bei Hansgrohe. Das Ziel: Ein Pull-System zu implementieren, das sich vom Kunden bis zum Lieferanten widerspiegelt. Unterstützung erhielt der Sanitärspezialist dabei von den Beratungsunternehmen Abels & Kemmner Gesellschaft für Unternehmensberatung mbH, Herzogenrath bei Aachen, und Leonardo Group GmbH, München.
Hansgrohe entschied sich in der Beschaffungslogistik für ein zweistufiges Vorgehen. Zunächst sollte in einem ersten Schritt die Beschaffungsdisposition analysiert und auf eine verbrauchsgesteuerte Disposition umgestellt werden. Jaeckle: „Durch Optimierung der Dispositionsparameter und Logistikgrößen lassen sich in vielen Fällen bereits mit geringem Aufwand Bestandssenkungen erreichen.“
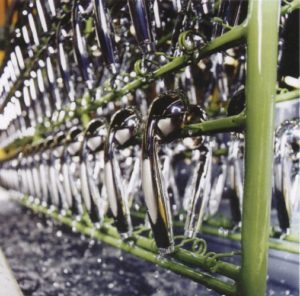
Beschaffung auf dem Prüfstand
In einer ABC/XYZ-Analyse nahm das Unternehmen zuerst die Einkaufsmaterialien des Werkes Schiltach unter die Lupe: Welche Artikel waren hier für die Produktion wichtig (ABC) und wie war deren Vorhersagegenauigkeit bzw. Planbarkeit (XYZ)?
Die dazu notwendigen Daten lieferten speziell entwickelte Reports aus dem SAP-System, die Hansgrohe mit externen Tools auswertete. Der Betrachtungszeitraum betrug dabei zwölf Monate. Die XYZ-Analyse wurde auf Wochenbasis durchgeführt. Während X- und Y-Artikel einen relativ gleichmäßigen Verbrauch in der Vergangenheit aufweisen, haben Z-Artikel einen unregelmäßigen bis sporadischen Lagerabgangscharakter. Zusätzlich wurden bei der XYZ-Analyse die Artikel besonders gekennzeichnet, die mehr als die Hälfte der 52 Wochen nicht nachgefragt wurden. Bei diesen Z2-Artikeln handelt es sich vornehmlich um neue oder auslaufende Einkaufsmaterialien, die dispositiv gesondert zu behandeln sind.
„Die Ergebnisse der ABC/XYZ-Analyse zeigten ein klassisches Bild: Während es uns gelang, im AB/XY-Bereich die Bestände im Verhältnis zum Umsatz gering zu halten, war der Bestand bei den sporadisch benötigten Artikeln (Z2-Artikel) sowie bei den geringwertigen C-Artikeln zu hoch. Das drückte sich durch einen geringen Wert des Lagerumschlags aus”, erklärt Jaeckle. Eine Reichweitenanalyse verdeutlichte die Arbeitsweise der Disponenten: Hochwertige A- und B-Teile wurden geringer bevorratet und wiesen kleinere Reichweiten auf, während man sich mit C-Teilen höher eindeckte und damit administrativen Aufwand einsparte. Eine Ausgangssituation, in der jede Menge Optimierungspotenzial steckte. Mit einer Simulation mittels dem Optimierungstool „DISKOVER” der Abels & Kemmner GmbH sollten diese freigelegt werden. Jäckle nennt die notwendigen Parameter: „Bei den hochwertigen A- und B-Artikeln sollte nach Möglichkeit ein hoher Lagerumschlag erzielt werden. Dazu wurde ein Eindeckzeitraum von fünf Arbeitstagen gewählt, d.h. dass bei der Bestellmengenrechnung die Bedarfe von fünf Arbeitstagen zusammengefasst werden.”
Bei den geringwertigen C-Artikeln wählte Hansgrohe einen Eindeckzeitraum von 20 Arbeitstagen. Dies wirkt sich nur gering auf die Bestände aus, sollte aber sowohl im Einkauf als auch in der Logistik den administrativen und physischen Aufwand in Grenzen halten. Die sporadisch verbrauchten Z2-Artikel wurden bei der Simulation ebenfalls berücksichtigt, allerdings sollten diese Artikel wegen des höheren Bestandsrisikos zukünftig auftragsbezogen beschafft werden.
Alle Artikel wurden mit drei verschiedenen Lieferbereitschaftsgraden (90, 95 und 98 Prozent) simuliert, uni zum einen die erzielbaren Lieferbereitschaftsgrade beurteilen zu können und zum anderen die Auswirkungen des Lieferbereitschaftsgrades auf die Bestände zu ermitteln. Die Ergebnisse der verschiedenen Simulationsläufe ergaben Bestandsreduzierungspotenziale von bis zu 47 Prozent. Dabei lagen die Lieferbereitschaftsgrade der zukünftig lagerhaltigen Artikel zwischen 91 Prozent und knapp 96 Prozent.
Umsetzung erfolgreich
„Im Anschluss an die Analysen und Simulationen ging das Team umgehend die Umsetzung der Ergebnisse an. Dazu wurden die Dispositionsverfahren für ausgewählte lagerhaltige Artikel im SAP-System aufprognosegestützte Bestellpunktverfahren umgestellt und die erforderlichen Planungsparameter, wie sie von DISKOVER kalkuliert wurden, eingegeben”, schildert Jaeckle die weitere Vorgehensweise.
Die Standardeinstellungen der Bestellpunktverfahren in SAP wurden im Customizing dahingehend modifiziert, dass das System die aktuellen Bedarfe bei der Beschaffungsrechnung ebenfalls berücksichtigt und sich nach Abzug dieser Bedarfe immer noch ein Bestandsniveau über dem Meldebestand ergibt. Durch die Umstellung deckt sich die Hansgrohe AG nicht mehr so hoch mit Material ein. Mit der Reduzierung der Mindestbestellmengen und Wiederbeschaffungszeiten, die der Einkauf mit den Lieferanten neu vereinbaren konnte, nimmt die Zahl der Lieferabrufe gegenüber der Vergangenheit zu.
Der Erfolg der Umstellungen zeigte sich innerhalb kurzer Zeit. Binnen zehn Wochen ging der Bestand der Pilotartikel bereits um über 50 Prozent zurück, sodass man schon fast die simulierten Zielbestände erreicht hat. Der Gesamtbestandreduzierte sich nach weiteren Umstellungen innerhalb kurzer Zeit um über 15 Prozent.
Anbindung über Kanban
In einem zweiten Schritt galt es dann, die Lieferanten in den Beschaffungsprozess zu integrieren und so den Gesamtprozess effizienter und flexibler zu gestalten. Seit Jahresbeginn 2006 ging das Unternehmen daher die Lieferantenintegration per Kanban an, zunächst für bestimmte Produkte im Werk Schiltach.
Als Pilotbereich wählte Hansgrohe einen der wichtigsten Bausteine einer modernen Armatur: die Kartusche, das Herzstück eines jeden Einhebelmischers. „Hier haben wir aber einen sehr konstanten Verbrauch an Einzelkomponenten, sodass es sich anbietet, die Lieferanten über Kanban einzubinden”, erklärt Jaeckle. Hansgrohe entschied sich für eine Lösung mit doppeltem Regelkreis zur Versorgung: Einerseits des Montagebereichs aus dem Vorratslager heraus und andererseits zur Nachbevorratung des Vorratslagers direkt durch den Lieferanten.
Der erste Regelkreis zwischen Produktion und Vorratslager besteht aus einer einfachen Pendelkartenlösung. Ist das Material in der Produktion verbraucht, schickt der Werker die Karte über einen mit allen Beteiligten abgestimmten Postweg an das Lager. Im Lager wird diese Karte an die nächste Palette bzw. Verpackungseinheit geheftet und in die Produktion an den vorgesehenen Stellplatz gefahren.
Der zweite Regelkreis zur Anbindung der Lieferanten reicht über die Unternehmensgrenzen hinaus und war daher aufwändiger. Hier setzte Hansgrohe auf die SAP-Funktionalität: Jede Kanban-Karte des zweiten Regelkreises wird in der SAP-Kanban-Tafel mit aktuellem Status geführt. Der Status wird per Scannen des Barcodes auf der Kanban-Karte im Warenaus- und -eingang auf „leer” bzw. „voll” gesetzt. Mit dem Setzen auf den Status „leer” erzeugt SAP automatisch eine Eintragung im Lieferplan. Die Kanban-Karte, die Nachlieferungsbedarf signalisiert, wird über die Nachrichtenfindung in SAP automatisch als PDF-Dokument per E-Mail an den Lieferanten gesendet. Dieser braucht nur noch die Karte auszudrucken, an die Ware zu heften und diese an Hansgrohe zu senden.
Ein weiterer Effekt stellte sich in der Bestandsreduzierung ein: Die Bestände der Materialien, die auf das neue Verfahren umgestellt wurden, sind bereits um rund 40 Prozent zurückgegangen – und dies bei bester Verfügbarkeit.
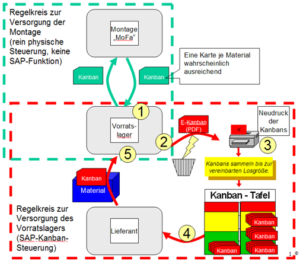
Ausweitung geplant
Die bisher erreichten Ergebnisse haben Hansgrohe überzeugt. Mittlerweile sind neben der Kartuschenproduktion auch rund 95 Prozent der platzintensiven Produkte auf Kanban umgestellt, weitere Bereiche sind in der Umsetzung. Und für das Jahr 2007 steht der internationale Rollout des Projekts „Logistics 2010″ an. Jaeckle: „Wir haben in Deutschland gestartet, um hier erst einmal unsere Hausaufgaben zu machen. Jetzt wo wir sehen, dass es funktioniert, übernehmen wir es.”