Neue Methoden zur Beschaffungs- und Bestandsoptimierung von Ersatzteilen
Entnahmen aus Ersatzteillagern folgen selten den bekannten Wahrscheinlichkeitsverteilungen. Das bei einem Automobilzulieferer jetzt neu implementierte Dispositionssystem berücksichtigt diesen Umstand.
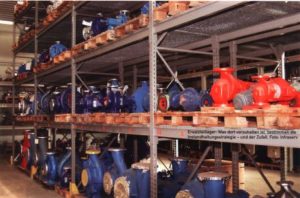
Strategien der Lagerhaltung von Ersatzteilen und Instandhaltungsmaterialien hängen von zwei wichtigen Faktoren ab: der gewählten Instandhaltungsstrategie – und dem Zufall.
Nun scheint gerade der Zufall auf den ersten Blick nicht gerade eine Größe zu sein, mit der sich besonders gut planen lässt. Aber Zufallsverteilungen bestimmen nun einmal die Entnahmeabfolgen von Materialien und Ersatzteilen – und wenn Experten mit mathematischen Methoden diese Abläufe analysieren, wird aus dem “flüchtigen Gesellen Zufall” ein zuverlässiger Helfer. Und genau diese Aufgabe lösten die Logistiker der Stabilus GmbH in Koblenz, gemeinsam mit den Entwicklern einer speziellen Planungssoftware.
Für die Logistiker von Stabilus stand am Anfang dieser Arbeit ein gewisser Umdenkprozess. Denn Stabilus ist ein Hersteller von Systemen für hydraulische Dämpfung und Verstellung von Klappen, Türen, Sitzen in zahlreichen industriellen Produkten, besonders aber in der Automobilindustrie. Und die hier üblichen Abwicklungsprozesse im Bereich Beschaffung und Produktion von Serienmaterialien haben das Denken im Unternehmen wesentlich mitgeprägt.
Der Bereich der Nichtserienmaterialien wie Ersatzteile und Instandsetzungsmaterialien ist jedoch völlig anders strukturiert und anderen Regeln unterworfen als die Verwaltung von Serienmaterialien. Und diese Bedingungen gilt es bei der Disposition des Instandhaltungsbedarfs zu berücksichtigen.
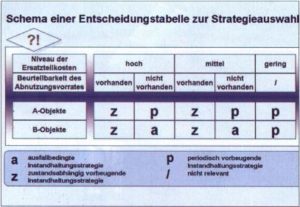
Die Objekte werden nach ihrer Wichtigkeit unterteilt
Zur richtigen Disponierung dieser Materialien muss zuerst einmal klargestellt werden, für welche Instandhaltungsobjekte sie benötigt werden. Dabei ist es üblich, Instandhaltungsobjekte nach A-, B- und C-Objekten zu klassifizieren:
“A”-Objekte sind ganz besonders wichtig für die Realisierung der Fertigungsziele. Für A-Anlagen ist typisch, dass ihr Ausfall direkt zur Verringerung des Outputs an Endprodukten führt. Ersatzteilen, die zu diesen Anlagen gehören, ist deshalb höchste Aufmerksamkeit bei der Disposition zu widmen.
“B”-Objekte besitzen ebenfalls hohe Bedeutung für die Umsetzung der Fertigungsziele. Allerdings sind sie entweder redundant ausgelegt oder in der Prozesskette mehrfach vorhanden, und ihr Auslastungsgrad erlaubt es, einen Teil der Instandhaltungsobjekte für bestimmte Zeit außer Betrieb zu nehmen.
“C”-Objekte sind Instandhaltungsobjekte von untergeordneter Bedeutung, die entweder im engeren Sinne gar nicht ausfallen können, oder deren Ausfall keinen Einfluss auf die Realisierung der Fertigungsziele besitzt.
Wenn nun eine Dispositions-Grundstrategie für A- und B-Objekte festzulegen ist, dann sind insbesondere zwei Kriterien von überragender Bedeutung:
- die Höhe der Ersatzteilkosten und
- die Beurteilbarkeit des Abnutzungsvorrates.
Je höher die Ersatzteilkosten für ein Instandhaltungs-Objekt ausfallen, als desto vorteilhafter erweist sich eine zustandsabhängige Instandhaltungsstrategie, welche die Nutzungsdauer eines Teiles weitgehend ausschöpft.
Zustandsabhängig vorbeugende Instandhaltung ist jedoch nur dann möglich, wenn der Abnutzungsvorrat an einem Instandhaltungs-Objekt beurteilt werden kann.
Dazu müssen in der Regel jedoch aufwändige Inspektionstechnologien eingesetzt werden, so dass eine Abwägung zwischen Ersatzteilkosten und Inspektionskosten erforderlich wird.
Ausgehend von diesen Überlegungen lassen sich dann den einzelnen Anlagen Instandhaltungsgrundstrategien zuordnen, die in einer Entscheidungstabelle darstellbar sind.
Diese Entscheidungstabelle bildet die Grundlage der Dispositionsstrategie für die verschiedenen Instandhaltungsmaterialien. Eine Reihe von für die Disposition relevanten Kriterien wie beispielsweise Lieferbereitschaftsgrade und Sicherheitsbestände lassen sich dann aus diesen Vorgaben ableiten.
Da viele Instandhaltungsmaterialien sowohl in A-, B- als auch in C-Objekten benötigt werden und teilweise längere Lieferzeiten haben, erfordert eine wirkungsvolle Disposition von Instandhaltungsmaterialen zudem eine Bedarfsprognose auf Basis von Vergangenheitsdaten. Und hier kommt nun der “gebändigte Zufall” ins Spiel.
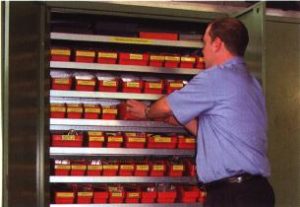
Die Normalverteilung ist in der Lagerwirtschaft nicht der Normalfall
Denn um aus Vergangenheitsdaten die richtigen Prognosen für zukünftige Bedarfsstrukturen abzuleiten, spielt die Verteilung der Nachfragemengen eine entscheidende Rolle. Die Standard-Dispositionsverfahren, die in ERP- oder IPS-Systemen benutzt werden, gehen in der Regel von einem normalverteilten Lagerabgang aus.
Das ist in der Praxis jedoch nur sehr selten wirklich zutreffend – in Wirklichkeit liegt der Anteil der Normalverteilungen im Lagerabgang nämlich nur bei etwa 5%. Ein relativ großer Anteil der Verteilungen, etwa 25%, kann sogar überhaupt keinem der theoretischen Verteilungstypen zugeordnet werden.
Für die Disposition von Nichtserienartikeln, die keinem der theoretischen Verteilungstypen zuordenbar sind suchte Stabilus nun eine Lösung unter SAP, mit der sich auch dieser Bedarfsumfang möglichst einfach disponieren lässt.
Eine solche Lösung bot das Programm “Diskover” – denn diese Software berücksichtigt die tatsächliche Verteilung des Lagerabganges. Im Zusammenspiel mit dem führenden SAP-System ermittelt diese Software nun die optimalen Verfahren und Parameter der Disposition, und zwar in zwei aufeinander aufbauenden Stufen.
Zunächst werden die Teile in einer Artikelstrukturierung je nach Bedarf und Verbrauchsverhalten geordnet.
Anschließend ermittelt das Programm dann für jede Artikelklasse die im Hinblick auf Bestandshöhe und geforderte Lieferbereitschaft optimalen Dispositionsverfahren und -parameter. Diese Parameter werden dann abschließend an das führende Host-System, in diesem Falle also SAP, oder an DISKOVER selbst übergeben, um daraus die Bestellvorschläge für die Teilebeschaffung zu generieren.
Die Ermittlung der artikelspezifischen Grundbedarfe und Sicherheitsbestände erfolgt so, dass ein jeweils vorzugebender Soll-Lieferbereitschaftsgrad ebenso berücksichtigt wird wie die im Unternehmen real auftretenden Verteilungen sowohl der Lagerabgänge als auch der Wiederbeschaffungsschwankungen.
Uwe Mollenhauer, Leiter Internationale Logistik, Fertigungssteuerung und Materialdisposition (SILS) bei Stabilus, ist mit dieser “Bändigung des Zufalls” jedenfalls zufrieden. “DISKOVER ermöglicht es uns recht elegant, bei der großen Anzahl unserer Nichtserienmaterialien die Bestände auf dem Niveau vereinbarter Lieferbereitschaft zu optimieren”, so seine Einschätzung.
Diskover 4.1: Anwendungsbereiche, Struktur und Merkmale
Das Dispositionssystem Diskover 4.1 ist ein operatives Managementsystem für die Optimierung der Supply Chain vom Einkauf bis zur Auslieferung.
Es bietet sowohl umfangreiche Auswahlmechanismen für die tägliche Disposition als auch Portfolioanalyse- und Simulationsfunktionen sowie verteilungsfreie Dispositionsverfahren an.
DISKOVER (DISposition mit Hilfe von Konfidenzbereichen unter Berücksichtigung der tatsächlichen LagerabgangsVERteiLung). ist als Add-On-Tool unter SAP und allen gängigen ERP-, PP- und WW-Systemen lauffähig.
Die Software ist in C++ programmiert und läuft als Client auf allen Windowsplattformen.
Der zentrale, Datenbank-Server, beispielsweise Qraclde oder MS-SQL, kommuniziert über eine standardisierte Schnittstelle mit dem führenden ERP-System. Client und Server sind je nach Datenvolumen auszulegen.