Mit Kanban wird der Lagerbestandswert bei Montblanc halbiert
von Burkard J. Kiesel, Peter Kluge, Andreas Gillessen, Dr. Götz-Andreas-Kemmner
Mit der Einführung der Kanban-Steuerung für die Produktion der Komponenten sowie das JIT-Prinzip für die Montage der Endgeräte der Schreibgerätefamilie Bohème im März 2003 legte Montblanc die Basis für eine verbesserte Lieferbereitschaft, verkürzte Durchlaufzeiten und reduzierte Lagerbestände. Das gesamte Bestandssenkungspotenzial beläuft sich auf 48 % des zu Projektbeginn vorhandenen Bestandswertes. Aufgrund des erfolgreichen Anlaufs dieses Projektes wird ab sofort auch die Schreibgerätefamilie Meisterstück umgestellt. Aus Projektmanagementsicht verlief die “Live-Schaltung” von Kanban besonders reibungslos. Im Betrieb überzeugt die speziell für Montblanc entwickelte Lösung durch ihre Einfachheit und Transparenz für jeden Mitarbeiter.
Nachdem Montblanc mit Unterstützung von Abels & Kemmner im vergangenen Jahr den Absatzplanungsprozess von der Budgetplanung über den Forecast-Prozess bis hin zur rollierenden monatlichen Bedarfsplanung einem Reengineering unterzogen hatte (siehe m+m Ausgabe 6/2002, Seite 32-35), stand die Sicherstellung der Lieferbereitschaft des Zentrallagers Hamburg sowie die Reduzierung der Durchlaufzeiten und der Lagerbestände auf dem Projektplan. Aufgrund der hohen Fertigungstiefe, der langen Wiederbeschaffungszeiten und der großen und ständig wachsenden Variantenvielfalt, sollten durch den Aufbau dezentraler organisatorischer Regelkreise effiziente Wertschöpfungsketten aufgebaut werden, die das Versorgungsrisiko auf allen Produktionsebenen auf ein Minimum reduzieren. Die eingesetzte MRPII-Logik (siehe Grafik), mit ihrem sehr hohen Koordinationsaufwand, lieferte dafür jedoch keine zufriedenstellenden Ergebnisse. Der bisherigen Vorgehensweise mangelte es an Flexibilität, insbesondere bei kurzfristigen Bedarfsschwankungen einzelner Endprodukte. Um die Lieferbereitschaft am Markt sicherzustellen, waren überhöhte Lagerbestände in der gesamten Wertschöpfungskette bis zum Fertigwarenlager notwendig.
Der wesentliche Hebel zur Verbesserung der Lieferbereitschaft bei gleichzeitiger Reduzierung der Lagerbestände lag bei Montblanc im Aufbau einer JIT-Fertigung und damit in einer Verlagerung der Bestände vom variantenreichen Endgerät auf die variantenbildende Komponentenebene. Die Analyse der Durchlauf- und Rüstzeiten hatte ergeben, dass eine JIT-Fertigung ohne größere Kosten möglich war. Die Einrichtung einer JIT-Fertigung setzt jedoch die sichere Versorgung der Endmontage mit Komponenten und Zukaufteilen voraus. Daher wurde ein zentrales Kanban-Lager vor der Endmontage aufgebaut sowie weitere Kanban-Lager vor verschiedenen vorgelagerten Produktionsstufen. Derzeit werden nach und nach auch die Lieferanten in das System eingebunden.
Dank der präzisen Auslegung des Kanban-Systems und durch die intensiven und gründlichen Vorarbeiten konnte die “Live-Schaltung” auf das Kanban-System ohne große Probleme erfolgen. Innerhalb von nur drei Tagen waren alle Vorbereitungen für die Umstellung realisiert. Da Kanban-Systeme selbststeuernde Systeme sind, die vom Grundsatz her kein zusätzliches IT-System für die Produktionssteuerung erfordern, wurde das Kanban-System bei Montblanc so konzipiert, dass die Produktion auch ohne das im Einsatz befindliche SAP-System laufen kann. Gleichzeitig wurden die SAP-Prozesse so umgestaltet, dass sie die Abläufe des Kanban-Systems nicht durch zusätzlichen Verwaltungsaufwand behindern. Die Mitarbeiter eröffnen lediglich zu Beginn der Produktion einer Losgröße einen Fertigungsauftrag und melden diesen nach Beendigung auch wieder zurück. Es sind keine weiteren SAP-Prozesse notwendig. Alle Bestands- und Umlagerungsbuchungen erfolgen bereits automatisiert im Hintergrund. In den nächsten Wochen wird das Kanban-System noch enger mit dem SAP-System verknüpft werden. Zu diesem Zweck wird die SAP-eigene Kanban-Steuerung eingeführt. Die Auftragseröffnung und -schließung erfolgt zukünftig automatisch durch das Scannen der Barcodes auf den Kanban-Karten. Dies alles hört sich sehr leicht an. Es waren jedoch viele Details zu beachten, um das Kanban-System erfolgreich einzuführen.
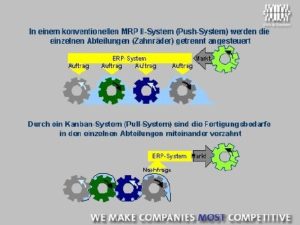
Umsetzung und Einführung
Die Einführung von Kanban begann mit einer Änderung der Arbeitsweise und des Verhaltens der beteiligten Mitarbeiter bei Montblanc. Dies bedingte allein schon die Dezentralisierung der Produktionssteuerung zurück in die einzelnen Produktionsbereiche. Eine wesentliche Ursache für die Probleme vieler Unternehmen bei der Einführung von Kanban-Systemen liegt darin, dass die Mitarbeiter nicht bereit sind, die Kanban-Regeln einzuhalten. Sie fertigen auf Vorrat, bunkern Komponenten, halten Losgrößen oder Durchlaufzeiten nicht ein. Sind die Mitarbeiter vom System nicht überzeugt, halten sie dessen Regeln nicht ein und bringen das System damit zum Scheitern. Ein wesentlicher Erfolgsfaktor der Kanban-Einführung bei Montblanc war daher die Integration der Mitarbeiter in die Systemkonzeption. Alle organisatorischen Abläufe wurden gemeinsam mit den Mitarbeitern der jeweiligen Produktionsbereiche erarbeitet. Auf diese Weise konnte das Vertrauen der Mitarbeiter in das Konzept und das Verständnis bzw. die Identifikation mit den Gesamtabläufen und den Detailabläufen der jeweiligen Produktionsbereiche geschaffen werden.
In der Praxis erleben viele Unternehmen während der Einführungsphase aber auch deshalb ein Desaster, weil das System nicht an die Realität der Produktionsabläufe angepasst wurde. Bei Montblanc wurden deshalb vor der eigentlichen Dimensionierung der Regelkreise, alle relevanten Material-, Informations- und Auftragsabwicklungsprozesse aufgenommen und mit den Mitarbeitern der Produktionsbereiche neu auf die Anforderungen der Kanban-Abläufe zugeschnitten. Dabei wurden die Prozesse jeweils unter folgenden Aspekten betrachtet:
- Ist ein Flussprinzip über die Produktionsbereichsgrenzen möglich, ohne ein Kanban-Lager einzurichten?
- Wenn ein Kanban-Lager unabdingbar ist, kann es auf einer geringeren Wertschöpfungsstufe bzw. vor einer variantenbildenden Produktionsstufe eingerichtet werden?
- Können die Produktions- und die Rüstzeiten sowie die Losgrößen reduziert werden?
- Ist die Prozessstabilität ausreichend um die Produktionszeiten zu garantieren und ist die Prozessqualität beherrschbar?
- Ist die Kapazitätssituation (Mitarbeiter / Maschinen) ausreichend bzw. ausreichend flexibel um die Versorgungssicherheit zu gewährleisten?
- Sind die Disziplin und die Qualifikation der Mitarbeiter hinreichend für die Führung des Kanban-Systems?
Alle identifizierten größeren Reorganisationspotenziale wurden dabei bewusst auf den Zeitpunkt nach Einführung der Kanban-Steuerung verlegt. Dies war zum einen sinnvoll, weil erst nach der Kanban-Einführung erste Erfahrungen mit dem neuen System im Echtbetrieb gemacht werden können und diese entscheidenden Einfluss auf die Fragestellung haben, wie die Abläufe verändert werden können und sollten. Hierdurch wird darüber hinaus auch Doppelarbeit vermieden. Zum anderen sollte die Umstellung auf Kanban nicht durch andere Reorganisationsprojekte verzögert werden.
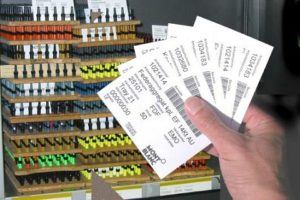
Nicht alles über einen Kamm scheren
Bei Montblanc stellen die Charakteristika des Artikelspektrums ganz unterschiedliche Anforderungen an die Dimensionierung der Kanban-Regelkreise. Es gibt Fertigungsbereiche die prozessbedingt mit hohen Losgrößen arbeiten und andere Bereiche die durch minimale bis gar keine Rüstzeiten gekennzeichnet sind. Diesen unterschiedlichen Bereichen konnte man nur durch eine entsprechend differenzierte Kanban-Dimensionierung gerecht werden. Die eigentliche Dimensionierung der einzelnen Kanban-Regelkreise und damit die Festlegung der Anzahl der umlaufenden Kanbankarten wurde deshalb auf ein breiteres, mathematisch-analytisches Fundament gestellt. Häufig wird bei der Dimensionierung von Kanban-Regelkreisen nur die Wiederbeschaffungszeit pro Kanban, der durchschnittliche Verbrauch des Artikels (vergangenheitsbezogen), die Menge je Kanban-Behälter sowie ein sogenannter Sicherheitsfaktor berücksichtigt. Bei dieser Vorgehensweise hängt die Anzahl der umlaufenden Kanban-Karten und damit die Bestandshöhe im wesentlichen von einem Faktor ab, der nicht mathematisch-analytisch, sondern auf Basis eines “Bauchgefühls” festgelegt wird. Wichtige Bestimmungsgrößen wie
- Losgröße des Lieferanten (Sammelkanban)
- Losgröße / Verbrauch des Kunden
- Verbrauchsverhalten des Artikels (XYZ-Verhalten) und damit der richtige Sicherheitsbestand
- Ausschussfaktoren sowie
- die zukünftigen Verbrauche
werden dabei meist gar nicht erst berücksichtigt. Eine Optimierung der Bestände, Durchlaufzeiten und des Lieferservice kann somit jedoch nicht erreicht werden. Dies ist der zweite wesentliche Grund dafür, dass sich viele Unternehmen mit der Einführung von Kanban schwer tun und nicht die gewünschten Erfolge erzielen.
Eine der großen Schwachstellen bei der Dimensionierung eines Kanban-Regelkreises ist die Kalkulation mit Verbräuchen vergangener Perioden. Bei der Dimensionierung für Montblanc wurde hingegen die “Zukunft” in Form der rollierenden Absatzplanung für die zugrundeliegenden Verbrauchswerte herangezogen. Damit wurde Kanban bei Montblanc zu einem agierenden und nicht zu einem reagierenden Steuerungssystem.
Ein weiterer Schwachpunkt bestehender Kanban-Systeme ist häufig die fehlende regelmäßige Neudimensionierung des Systems. Eine Neudimensionierung muss jedoch in regelmäßigen Abständen bzw. nach Bedarf, sei es aufgrund veränderter Absatzprognosen bzw. veränderter Produktionsparameter, schnell und unkompliziert erfolgen. Bei Montblanc trägt hierfür die Disposition die Verantwortung. Sie wird die Neudimensionierung jedes einzelnen Artikels nach Bedarf bzw. in regelmäßigen Abständen durchführen. Das Ergebnis der Neudimensionierung ist eine veränderte Anzahl umlaufender Kanban-Karten. Bei einer Erhöhung der Kartenzahl müssen die zusätzlichen Karten in das System eingeschleust bzw. bei einer Reduzierung der Kanban-Karten diesem entzogen werden.
Mit der Dimensionierung der Regelkreise wurde gleichzeitig die Kalkulation der gelben und roten Bereiche der Kanban-Tafeln sowie eine Simulation der Kapazitätssituation der einzelnen Produktionsbereiche durchgeführt. Die Simulation kalkuliert die maximale und die minimale Anzahl notwendiger Rüstvorgänge pro Zeiteinheit und gleicht diese mit der bestehenden Kapazitätssituation ab. Zusätzlich wurde die benötigte Lagerfläche für die Kanban-Artikel dimensioniert, indem auch hier im Zeitverlauf die minimal, durchschnittlich und maximal benötigte Lagerfläche je Artikel und Kanban-Lager errechnet wurde. Diese Daten bildeten schließlich die Grundlage für die Beschaffung ausreichend großer Kanban-Tafeln und Regalsysteme.
PPS-Systeme und Kanban
Da Kanban ein selbststeuerndes System ist, benötigt es vom Grundsatz her kein zusätzliches PPS-System. Deshalb darf man bei der Implementierung von Kanban nicht darauf hinarbeiten, bestehende PPS-Systeme zwanghaft in das Kanban-System zu integrieren. Es ist vielmehr erforderlich, dass das PPS-System eine logische Schnittstelle zum Kanban-System hat. Das Kanban-System wurde bei Montblanc deshalb so konzipiert, dass die Produktion grundsätzlich auch ohne das im Einsatz befindliche SAP-System laufen kann. Dennoch benötigt man für die Auftragsabrechnung, die Beschaffung und die planerische Bestandsführung ein Abbild der Produktionsabläufe in einem PPS- bzw. ERP-System.
Warum sollte man nicht direkt auf die Kanban-Funktionalität vieler ERP-Systeme zurückgreifen? Ein wesentliches Merkmal eines Kanban-Systems stellt die Visualisierung aller Abläufe für alle Mitarbeiter dar. Dies wird durch die Abbildung einer Kanban-Tafel rein im ERP-System nicht ermöglicht. Bei Montblanc beispielsweise läuft zukünftig SAP-Kanban parallel zum manuellen Kanban-System, hiervon merken die normalen Anwender jedoch nichts. Sie setzen durch Scannen der Barcodes auf den Kanban-Karten lediglich verschiedene Stati im System. Dadurch wird die Materialbilanz im SAP-System mit den physischen Bestandsveränderungen synchronisiert. Gegen eine reine Kanban-Steuerung über das SAP-System spricht auch, dass das SAP-System gegenwärtig noch große Schwächen in der Kanban-Dimensionierung aufweist und über keine Lösung für die Abwicklung von Sammel-Kanbans verfügt.
Zusammenfassung
Der Erfolg von Kanban liegt in der Selbststeuerung der Produktionsbereiche im Rahmen der definierten Kanban-Regeln sowie der ausschließlichen Orientierung an den Bedarfen der Kunden begründet. Die aufgebauten selbststeuernden Regelkreise reduzieren dabei die Komplexität in der gesamten Logistikplanung. Hierdurch wird der permanente Eingriff der zentralen Steuerung in die Prozesse überflüssig. Es bleibt jedoch eine permanente Aufgabe aller am System beteiligten Mitarbeiter, durch weitere Verbesserungen der Rahmenparameter wie Losgröße, Rüst- und Produktionszeiten, Ausschussquoten, etc. die Wertschöpfungsketten hinsichtlich Durchlaufzeiten, Lieferservice und Bestände weiter zu optimieren.
Über Abels & Kemmner
Die Abels & Kemmner GmbH, die in diesem Jahr ihr 10-jähriges Bestehen feiert, wurde 1993 von den Ingenieur- und Wirtschaftswissenschaftlern Dr. Helmut Abels und Dr. Götz-Andreas Kemmner gegründet. Ein Schwerpunkt des Unternehmens ist die Straffung von Wertschöpfungsketten (Supply-Chain-Optimierung) bei Serien- und Variantenfertigern sowie Großhandelsunternehmen. Abels & Kemmner beschäftigt sich hierbei mit der Auslegung und Optimierung von Auftragsabwicklung und Logistik von den Lieferanten bis zu den Kunden und von der Artikelsortimentierung bis zur IT-Unterstützung. Bereits zweimal gewannen Supply Chain Konzepte, die wir mit unseren Kunden erarbeitet haben, Best Practice Preise. Aufsehen erregte A&K 1997 mit der Gründung des ersten Virtuellen Unternehmens aus sechs mittelständischen Unternehmen der Automobilzulieferbranche.
Den zweiten Schwerpunkt bilden Restrukturierungs- und Ertragssteigerungsprojekte. Hier erarbeiten die Consultants Fortführungsprognosen sowie Restrukturierungs- und Downsizing-Konzepte und setzen diese in den Unternehmen um. Durch erfolgreiche Sanierungen mittelständischer Unternehmen machte sich Abels & Kemmner einen Namen im Krisen- und Turnaround-Management. In den letzten Jahren waren die Berater an der Sanierung eines Großteils der größeren Unternehmensinsolvenzen im Saarland beteiligt.