Clean&Prim KG* optimiert ihre Materialeffizienz
von Armin Klüttgen
Schonenderer Umgang mit Ressourcen, mit dem Ziel Materialverluste zu verringern und handfeste wirtschaftliche Potenziale zu heben, sind drei gute Gründe, aus denen sich in den letzten beiden Jahren immer mehr Unternehmen mit dem Thema „Materialeffizienz“ auseinandergesetzt haben. Das sind auch die Gründe, warum die Clean&Prim KG* zusammen mit der Abels & Kemmner GmbH in einem Materialeffizienzprojekt für einen Teil ihres Artikelsortimentes untersucht hat, welche Kostensenkungspotenziale durch eine weitere Steigerung der Materialeffizienz zu realisieren sind und wie man das Bewusstsein der Mitarbeiter für den schonenden und effizienten Umgang mit den eingesetzten Materialien noch steigern kann. Die Ergebnisse des Projekts bestätigen den Weitblick der Geschäftsleitung. Nun gilt es, die identifizierten Potenziale durch Umsetzung der definierten Maßnahmen zu realisieren.
In seinem Endbericht an das Bundesministerium für Wirtschaft und Technologie (BMWi) im Dezember 2011 zeigte das Fraunhofer-Institut für System- und Innovationsforschung ISI auf, wie groß das Potenzial im verarbeitenden Gewerbe oftmals ist, welches eine Steigerung der Materialeffizienz offenbart. Basis des Berichtes sind die Zahlen einer Erhebung zur Modernisierung der Produktion aus dem Jahr 2009, die das ISI seit 1993 regelmäßig durchführt.
Die Befragung ergab, dass branchenübergreifend im Mittel bei optimaler Ausnutzung der heute verfügbaren technischen Möglichkeiten sieben Prozent des Materialverbrauchs in der Produktion eingespart werden können. Dies hat beeindruckende Auswirkungen auf die Umsatzrendite, wie der Vergleich mit der erforderlichen Umsatzsteigerung zeigt. Welche Umsatzsteigerung notwendig wäre, um in verschiedenen Branchen denselben Ertragseffekt zu erreichen, wie mit der Verbesserung der Materialeffizienz, zeigt die nachfolgende Tabelle exemplarisch für einige ausgewählte Branchen:
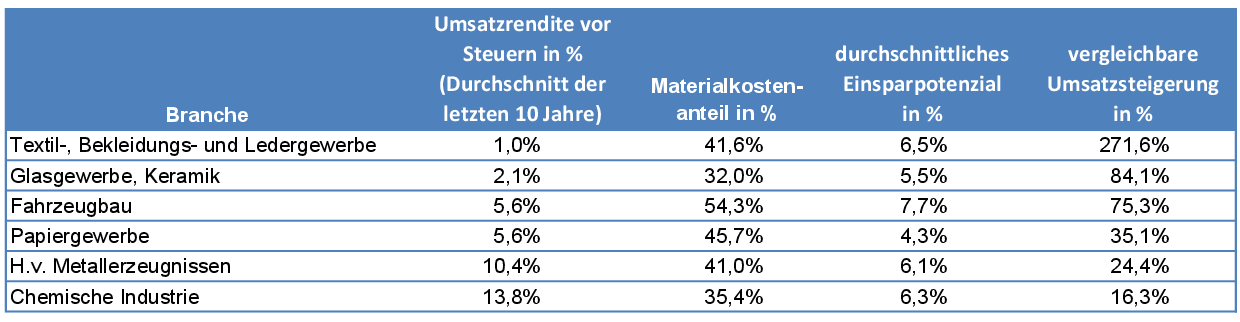
Die dargestellten Beispiele belegen zum einen eindrucksvoll die große Hebelwirkung von Maßnahmen zur Steigerung der Materialeffizienz. Zum anderen vermitteln sie einen Eindruck davon, wie hoch der Anteil der Materialkosten an den Gesamtkosten im verarbeitenden Gewerbe liegt: über alle Branchen hinweg bei ca. 43 %. Davon ausgehend, dass die Ressourcenpreise weiter steigen, viele Materialien am Beschaffungsmarkt knapp werden und eine Vielzahl von politischen Maßnahmen mit der Zielsetzung der Ressourcenschonung versehen sind, ist es für viele Unternehmen unumgänglich, sich dieses Themas ernsthaft und nachhaltig anzunehmen.
Die Clean&Prim KG lebt es vor
Die Clean&Prim-Group hat das bei den Mitarbeitern vorhandene Bewusstsein für die Sinnhaftigkeit der Materialeffizienz genutzt, um mit Unterstützung von Abels & Kemmner für einen ausgewählten Teil des Sortiments eine Untersuchung der vorhandenen Potenziale durchzuführen und die dafür erforderliche personelle Kapazität bereitwillig zur Verfügung gestellt. Dies klingt zunächst nicht nach einer besonders erwähnenswerten Leistung, jedoch sind die Nicht-Verfügbarkeit der personellen Kapazität ebenso wie der erforderliche organisatorische Aufwand häufige Ursachen für das Scheitern oder das Unterlassen solcher Projekte.
Dem vielfach bewährten Vorgehensmodell von Abels & Kemmner zur Materialeffizienzanalyse folgend, wurden Handlungsfelder und detaillierte Maßnahmen zur Realisierung der identifizierten Potenziale entwickelt. Basis dieser Ergebnisse waren:
- eine umfassende Ursachenanalyse (Constraint-Analyse),
- eine Stoffstromanalyse zur vollständigen Abbildung aller relevanten Materialströme,
- eine Bewertung der unterschiedlichen Ausschussarten und -mengen sowie
- eine Quantifizierung der Verbesserungspotenziale bezogen auf die unterschiedlichen Ausschussarten.
Materialverluste in Produktion und aus dem Lager heraus
Das untersuchte Sortiment umfasste Produkte, wie z. B. Haushaltsreiniger und Kosmetik sowie Haar- und Körperpflegeprodukte, mit denen u. a. viele deutsche Handelsketten beliefert werden. Bei der Herstellung der Produkte kommen hochwertige Grundstoffe zum Einsatz, die einen hohen Anteil an den Gesamtkosten des Unternehmens ausmachen.
Der Gesamtausschuss setzt sich aus wertvollen Rohstoffen wie Chemikalien, Kunststoffen (Plastikflaschen und Verschlüsse) und Kartonagen (Papier, Pappe) zusammen.
Bei der Analyse wurden diverse Ursachen für Materialeffizienzverluste deutlich: Insbesondere Verluste durch Reinigungsvorgänge bei Aggregaten und Rohrleitungen machen einen signifikanten Teil davon aus. Ein weiterer Teil der Verschrottung entsteht durch planerische Aspekte aus dem Bestand heraus.
Der Produktionsprozess
Für die im untersuchten Produktspektrum produzierten Fertigerzeugnisse verwendet Clean&Prim Rohmaterialien wie Chemikalien, Kunststoffe, Packmittel in Form von Primärpackmitteln (z. B. Dosen und Flaschen) und Umverpackungen wie Kartonagen. Außerdem kommen noch diverse andere Roh-, Hilfs- und Betriebsstoffe zum Einsatz.
Die Rohmaterialien (Chemikalien) werden gemischt und dann über Rohrleitungssysteme in einen Puffer transportiert. Von dort aus werden sie, je nach Produkt oder Anwendung, in unterschiedliche Abfüllbereiche überführt. Auch dies geschieht wieder über entsprechende Rohrleitungssysteme. Beim Abfüllen wird das Material in seine Primärpackmittel (Kunststoffflaschen, Tuben, …) gefüllt. Nach der Primärverpackung und dem anschließenden Palettieren und Umverpacken werden die fertigen Erzeugnisse dem Fertigwarenlager zugebucht, von wo aus sie ausgeliefert werden.
Im Verlauf dieses Herstellungsprozesses gibt es verschiedene Quellen für Materialausschuss. Qualitätsbedingte Ausschüsse fallen in dem detailliert und akribisch überwachten Prozess praktisch keine an. Hier kommt es allenfalls in geringem Ausmaß z. B. zu Beschädigungen der Verpackung. Den weitaus größten Anteil an den Materialverlusten haben die sogenannten geplanten Ausschüsse. Diese entstehen bei Reinigungsvorgängen. Reinigungsverluste treten bei Produktwechsel an den Mischaggregaten, in den betroffenen Rohrleitungssystemen und den Abfüllmaschinen auf.
Der zweitgrößte Posten der Materialverluste entsteht durch Altware (zu verschrottende Überstände im Lager), die durch Effekte in der Planung entsteht und dann aber aus diversen Gründen verschrottet werden muss. Die Gründe, warum durch Planung Altware entsteht, sind sehr vielfältig. Dalli stellt sich hier einer höchst komplexen Planungsaufgabe, die durch eine Reihe von Besonderheiten zu Unschärfen im Planungsergebnis führen kann. Exemplarisch seien hier genannt:
- Schwierig planbare Aktionen im Umfeld einer großen Variantenvielfalt
- zum Teil starke saisonale Schwankungen
- teilweise Spotgeschäft bei Packmitteln
- Auslaufsteuerung mit der Anforderung, den punktgenauen Auslauf (alle Bestände termingerecht auf null fahren) bei Fertigerzeugnis (Inhalt), Vormaterial und Verpackung zu synchronisieren
- Produktänderungen, die aufgrund von Kundenwünschen vorgenommen werden, z. B. in Form von Rezepturänderungen oder Verpackungsänderungen.
Materialverluste lassen sich deutlich reduzieren
Die von Abels & Kemmner ermittelten Potenziale sind zum Teil erheblich: Sowohl geplante Ausschüsse in der Fertigung (Reinigungsverluste und Überpackung) als auch Ausschüsse aus dem Lager (Überbestand aus Planung, der zu verschrotten ist) weisen rein technisch deutliche Reduzierungspotenziale auf.
Die Maßnahmen, mit denen diese Potenziale gehoben werden können, zeichnen sich jedoch zum Teil durch unternehmensspezifische starke Abhängigkeiten und Wechselwirkungen aus und sind deshalb nur eingeschränkt nutzbar. Besonders die hohe Kundenorientierung darf nicht unter den Optimierungsprozessen leiden. Alle möglichen ermittelten Maßnahmen lassen sich dabei im Sinne einer Handlungsfeld-Landkarte vier Hauptstoßrichtungen zuordnen:
- Untersuchung von Verbesserungsmöglichkeiten in der Fertigung,
- Ausbau der durchgängigen Planung zur Vermeidung von Altware,
- Optimierung einzelner Geschäftsprozesse, wie z. B. Produktentstehungsprozess etc.,
- Gestaltung einer noch effizienteren Systemunterstützung.
Im Folgenden stellen wir Ihnen einige ausgewählte Maßnahmen exemplarisch dar:
Reinigungsverluste bei Produktwechsel transparent machen
Die Reinigungsverluste in der Fertigung machen absolut betrachtet den größten Anteil aller Materialverluste aus. Entsprechend führt eine Reduzierung dieser Verluste zu weniger Kosten. Der erste Schritt dazu ist, die Transparenz darüber, wo und wie viele Reinigungsverluste anfallen, weiter zu steigern. Je nachdem, welcher Produktmix über welche Linie gesteuert wird, kann es hier zu stärkeren Schwankungen kommen. An der Fertigung beteiligte technische Einheiten wie Mischer, Puffer, Filter, Pumpen, Rohrleitungen, Homogenisatoren und Abfüllmaschinen weisen je nach Produktmix und Fertigungsreihenfolgen schwankende Verlustraten auf. Daher gilt es, die bisher eingesetzten Methoden zur Verlustermittlung sowie das entsprechende Controlling zu verfeinern.
Gesamtkonzept einer durchgängigen Planung
Die Überführung der heutigen, bereits ausgefeilten Planungsprozesse in ein umfassendes Gesamtkonzept der vollständig durchgängigen Planung und Disposition bietet absolut betrachtet den eindeutig größten Hebel zur Vermeidung von Materialeffizienzverlusten. Dieses Gesamtkonzept beinhaltet als Eckpfeiler die Optimierung von Bedarfsplanung und Disposition und wird flankiert von einer noch besseren Kommunikation mit den Kunden. Dies trägt dem Supply-Chain-Gedanken „Planung vom Kunden des Kunden bis zum Lieferanten des Lieferanten“ noch mehr Rechnung, als er in der Clean&Prim KG bereits vorherrscht.
Bei der Optimierung der Bedarfsplanung steht vor allem die bestmögliche Integration sämtlicher verfügbaren planungsrelevanten Informationen für jeden einzelnen Artikel im Fokus, z. B. durch eine integrierte oder eine zusammenfassende Prognose. Dazu sind Vertriebsinformationen, Kundeninformationen, die aktuelle Auftragssituation und statistische Vorhersagen erforderlich, die artikelspezifisch zur bestmöglichen Prognose, auch im Hinblick auf Saisongeschäft, Aktionen und sonstige Ausnahmen, miteinander verbunden werden. Unterstützend müssen dabei auch diverse Klassifizierungen der Artikel eingesetzt werden, wie:
- eine ABC-Klassifizierung (wirtschaftliche Bedeutung),
- eine XYZ-Klassifizierung (Verbrauchsregelmäßigkeit),
- eine ELA- Klassifizierung (Lebenszyklus) oder
- eine STU- Klassifizierung (Anzahl Kunden).
Je nach seiner Klassifizierung, muss ein Artikel in der Bedarfsplanung genau passend eingestellt werden. Dazu bedarf es eines entsprechende Regelwerks, das durch seine Automatisierung ermöglicht, rollierend und aufwandsarm die materialspezifische Dispo-Strategie und alle erforderlichen Dispo-Parameter festzulegen sowie diese regelmäßig für alle Artikel zu überprüfen und neu einzustellen. Wichtig dabei ist jedoch, dass die bereits sehr hohe Flexibilität gegenüber dem Kunden unter allen Umständen erhalten bleibt und weiter verbessert wird. Dies haben die Spezialisten von Abels & Kemmner mit in Betracht gezogen und so gewährleistet das automatisierte Regelwerk dabei eine jederzeit optimale Disposition für jedes Fertigerzeugnis und jedes Vormaterial. Es ist daher gemeinsam mit der verbesserten Bedarfsplanung der Schlüssel zur Vermeidung von Altware und damit von Materialverlusten.
Geschäftsprozesse, die die durchgängige Planung stützen
Der Produktentstehungsprozess bzw. die Produkteinsteuerung, der Produktänderungs- und der Produktauslaufprozess nehmen erheblichen Einfluss auf Planung und Disposition. Wichtig bei allen genannten Prozessen ist eine möglichst enge Zusammenarbeit mit dem Kunden, der bei dem Geschäftsmodell der Clean&Prim KG erheblichen Einfluss auf die Planungsprozesse hat. Das Geschäftsmodell ist geprägt von häufigen Produktänderungen gepaart mit großer Variantenvielfalt sowie Änderungswünschen der Kunden bzgl. Produkt und Verpackung. Hier ist die Kenntnis des „True Demand Signal“ sehr hilfreich, also im Sinne der Supply Chain die möglichst frühe, echte Marktbedarfsinformation. Dies untermauert planerische Annahmen durch Hinzunahme realer Markt- bzw. Kundeninformationen frühzeitig und erhöht die Planungssicherheit. So können planerische Materialverluste deutlich reduziert werden.
Gerade bei Produktänderungen ist das Risiko hoch, dass obsoletes Material entsteht, da teilweise bereits schon initiierte Planungsvorgänge betroffen sind, wie z. B. Druck, Lieferung und Lagerung von Verpackungsmaterial. Für den Produktänderungsprozess muss daher klar festgelegt werden:
- die Art der möglichen Änderungstypen (Kundenanforderungen, Produktverbesserung, …),
- die Rollen und Zuständigkeiten je Änderungstyp,
- eindeutige Geschäftsregeln je Änderungstyp,
- ein Workflow zum Steuern und Überwachen der Abarbeitung des Änderungsprozesses,
- eine klare Dokumentation und Kommunikation des Prozesses sowie die Einbettung in die durchgängige Planung.
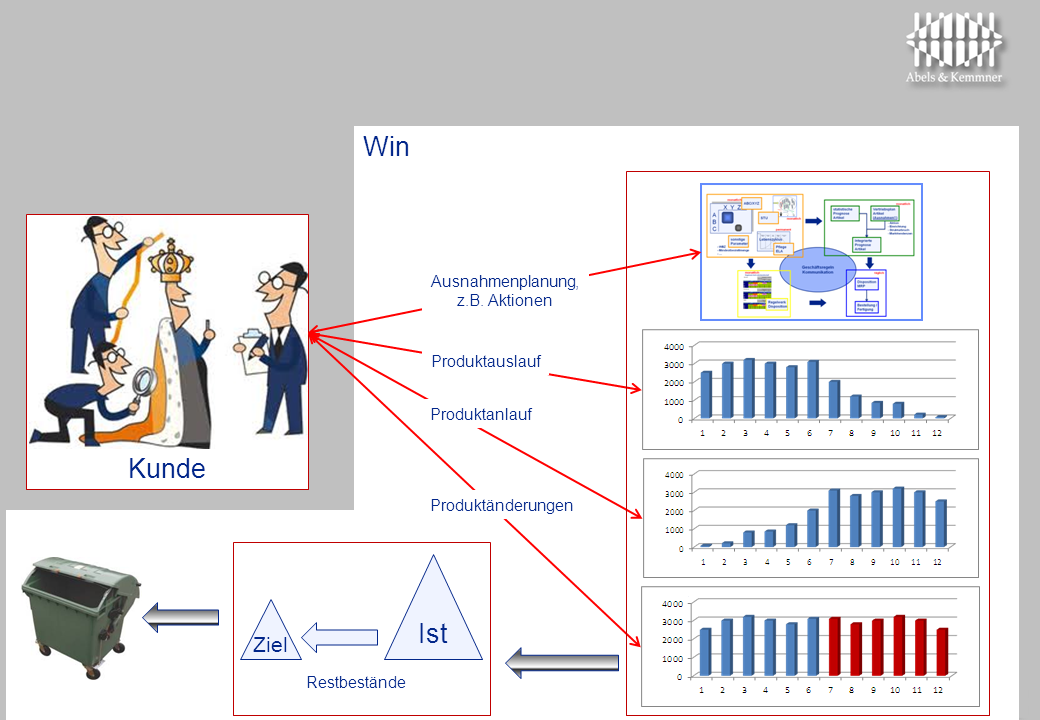
Auch der Produktauslauf führt häufig zu Materialverlusten, da ein bestimmtes Produkt zu einem festgegebenen Termin unter Aufrechterhaltung höchster Lieferbereitschaft auf Bestand null reduziert werden muss. Dies alleine ist sicher schon eine schwierige planerische Aufgabe. Erschwerend kommt hinzu, dass eine enge Synchronisierung des Auslaufs von Produkt und Primärpackmittel notwendig ist, was sich z. B. aufgrund der vorgegebenen Mindestbestellmengen bei den Packmitteln als sehr schwierig erweist.
Zusätzlich kann es vorkommen, dass ein angekündigter Auslauftermin kundenseitig verschoben wird. Auch in diesem Falle muss die Planung zur Aufrechterhaltung der geforderten Lieferbereitschaft handeln und sowohl Vormaterial als auch Fertigerzeugnisse nachbevorraten. Das führt in der Folge immer wieder zu Restbeständen.
Hier ist es besonders hilfreich, die bereits bestehende enge Partnerschaft mit den Kunden weiter auszubauen und auf der anderen Seite im Rahmen der Lieferantenintegration eine möglichst enge Einbindung insbesondere der Packmittellieferanten zu realisieren – denn so lässt sich die Entstehung von Altware verhindern und damit die Materialeffizienz weiter steigern.
Systemunterstützung forcieren
Das Projekt hat gezeigt, dass für eine höhere Materialeffizienz auch die Möglichkeiten der Systemunterstützung besser genutzt werden müssen. Daher werden die vorhandenen Systeme zukünftig im Hinblick auf einen durchgängigen Gesamtplanungsprozess weiterhin hochgradig integriert und für ein Maximum an Transparenz sorgen. Der manuelle Aufwand in Planung und Disposition wird sich deutlich reduzieren. Gerade in der Disposition werden so die Freiräume geschaffen, um sich intensiv mit den wirklichen „Problemfällen“ befassen zu können.
Fazit
Die Clean&Prim KG hat nicht nur eine sehr materialintensive Fertigung, sondern sie geht mit den eingesetzten zum Teil sehr hochwertigen Grundstoffen auch äußerst bewusst um. Ein effizienter Umgang mit immer knapper werdenden Rohstoffen gehört einerseits zur Unternehmensphilosophie und bietet andererseits wirtschaftliche Vorteile. Im Rahmen des Materialeffizienzprojektes mit der Abels & Kemmner GmbH konnte die Clean&Prim KG ihre bereits gute Materialeffizienz verbessern und wird diese Strategie anhand der Projektergebnisse auch weiter fortsetzen.