Steigerung der Materialeffizienz erfordert ganzheitliche Betrachtung
Eine hohe Materialeffizienz ist einer der wichtigsten Wettbewerbsfaktoren. Aus diesem Grund unterstützt das Bundesministerium für Wirtschaft und Technologie Unternehmen finanziell beim Auffinden entsprechender Effizienzsteigerungspotenziale.
Oft wird dabei zuerst auf die rein technischen Aspekte der Produktentwicklung und Fertigung geschaut. Dabei schlummert im ganzheitlichen Design des gesamten Wertstroms deutlich mehr Potenzial, als in der reinen Technik.
Die Steigerung der Materialeffizienz ist für deutsche Unternehmen eines der wichtigsten Themen der kommenden Jahre. Auch das Bundesministerium für Wirtschaft und Technologie (BMWi) hat die ökonomische Bedeutung einer verbesserten Materialeffizienz erkannt und bietet kleinen und mittleren Unternehmen dazu finanzielle Unterstützung an. Zu diesem Zweck können die vom BMWi ausgegebenen Innovationsgutscheine auch für eine qualifizierte Beratung zur Steigerung der Rohstoff- und Materialeffizienz eingesetzt werden. Das BMWi übernimmt 50% der Kosten für die Beratung durch ein vom BMWi autorisiertes Beratungsunternehmen. Nach Vorstellung des BMWi sollen die externen Fachleute dann Materialverluste bei Produkten und in der Produktion aufspüren und konkrete Verbesserungsvorschläge machen.
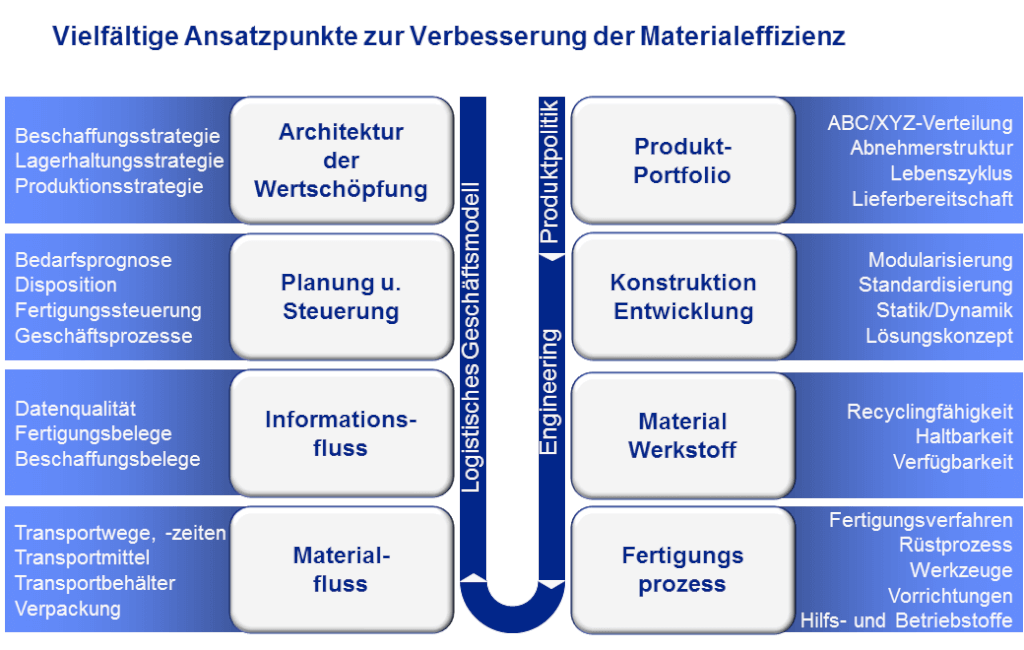
Was sich in der Praxis immer wieder zeigt: In den meisten Unternehmen beschränken sich Maßnahmen zum Thema Materialeffizienzsteigerung lediglich auf einzelne Teilbereiche des Wertstroms, nämlich die technischen oder sehr materialbezogenen Aspekte der Produktion. Also z.B. die Verringerung von Ausschuss (Qualitätsschrotte) oder die Optimierung von Verschnitt (Planschrotte) durch effizientere Zuschnitte oder Stanzungen. Auch materialsparendere Konstruktionsformen – Stichwort: Leichtbau in Automobilbranche – werden oft berücksichtigt. Der Fokus liegt also zumeist auf den Prozessen in den Maschinen bzw. auf dem Umgang mit den eingesetzten Materialien selbst. Doch damit ist das Potenzial für eine Steigerung der Materialeffizienz noch lange nicht ausgereizt. In den dispositorischen Aspekten des Wertstroms – also all das, was um die Maschine herum passiert – schlummert noch viel mehr ungenutztes Potenzial zur Steigerung der Materialeffizienz. Einige Beispiele nur:
Interne vs. externe Vielfalt
Die Frage der Variantenvielfalt von Produkten hat beispielsweise einen ganz erheblichen Einfluss auf die Materialeffizienz. Dabei gilt es, zwischen der internen und der externen Vielfalt zu unterscheiden. Natürlich sollen Kunden unter einer großen Vielfalt von Produkten auswählen können. Ziel aber muss es sein, intern die Vielfalt durch einen hohen Anteil an Mehrfachverwendungsteilen so gering wie möglich zu halten. Denn eine steigende Variantenvielfalt bei den Komponenten erhöht die Anzahl und Menge der benötigten Rohstoffe, Fertigungs- und Montageteile und Baugruppen. Eine geringere Variantenvielfalt verbessert all diese Faktoren und führt zudem noch zu einer besseren nachfrageorientierten Planbarkeit der Produkte bzw. Produktion.
Komponentenlager vs. Fertigwarenlager
Werden Produktvarianten mit möglichst vielen Standard-Bauteilen umgesetzt, findet zudem die endgültige Variantenausbildung zu einem späteren Zeitpunkt im Wertstrom statt und wird kundenauftragsbezogen montiert (postponed manufacturing), trägt dies doppelt zur Materialeffizienz bei: Die hohe Mehrfachverwendung reduziert direkt das Verschrottungsrisiko, wegen nicht mehr benötigter Bedarfe (Obseleszenzrisiko). Die späte Variantenbildung verstärkt den Effekt, da die aus Gründen der Lieferbereitschaft erforderlichen Bestände und das damit einhergehende Verschrottungsrisiko reduziert werden können.
Maschinenauslastung vs. Nachfrage
Verursacht der eingesetzte Maschinenpark hohe Rüstkosten und evtl. Einfahrausschuss, werden aus Kosten- und Materialeffizienzgründen gerne große Lose produziert. Große Lose können auch bei begrenzter Produktionskapazität erforderlich werden, weil keine Kapazität zum Rüsten verloren werden soll. Große Produktionslose führen aber zu deutlich höheren Beständen und damit zu höherem Verschrottungsrisiko. Hohe Umlaufbestände ergeben sich auch, wenn aus Gründen der Kapazitätsausnutzung mehr als erforderlich produziert wird. Projektanalysen von Abels & Kemmner haben immer wieder ergeben, dass die jährlichen bestandsbedingten Materialeffizienzverluste bei 5,5% bis 9% des Lagerbestandes liegen. So kann über Bestandsaufbau schnell mehr Materialeffizienz verloren gehen, als man an anderer Stelle durch materialverlustreduzierende Maßnahmen gewonnen hat.
In den bislang 11 vom BMWi geförderten und von Abels & Kemmner durchgeführten Materialeffizienz-Projekten konnte eine Reduzierung der Materialverluste um bis 29% erreicht werden, was einer jährlichen Ersparnis von mehreren hunderttausend Euro entspricht.