Simultaneous engineering: virtual company
Shorter product life cycles and time-to-market are forcing suppliers to synchronize cooperation in the vertical supply chain. Supported by VW, six medium-sized companies cooperating in the ‘virtual company’ are using the new Kopl@ Internet platform for this purpose – and are reducing modification costs by up to 50 percent, for example.
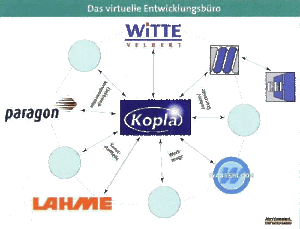
Like many automotive suppliers, locking system manufacturer Witte-Velbert works closely with selected suppliers in a network to develop and manufacture new products. A needs-based group of companies and employees is formed for each order. However, the responsible employees of the companies involved are hundreds of kilometers apart. To avoid losing the advantage of collaboration due to travel times and scheduling problems, they need sophisticated project management that can be centrally controlled across company boundaries. Witte-Velbert practices such cross-company project management with its suppliers C.W. Hanebeck, Gebr. Wasserloos, Lahme, Paragon and Schrimpf & Schöneberg have been successful since 1997.
Since July 1999, the six companies have been working on a web-based central communication system as part of the VIA initiative of the state of North Rhine-Westphalia. The project, code-named Kopl@, is used to exchange and store data and information, structure development processes, distribute project tasks and monitor project progress. In the Kopl@ test phase, which runs until the end of May, the companies are working on the development of a locking system for the VW T5 as a pilot project. Consultants from VW are involved in the Kopl@ project.
The cooperation partners |
|
The call for a tool like Kopl@ was more than loud. The distribution of digital and printed data by email, fax or conventional post did not lead to the desired transparency.
data had to be prepared twice and three times – in one specific case up to six times – which increasingly burdened the project staff with the management of information.
Sales staff and project engineers, often on site with customers for days at a time, could only find out about the current status of individual projects by telephone.
The managers at Witte-Velbert and the supplier companies involved only gained an insight into the current situation of individual projects through project status reports and personal discussions.
Kopl@ is therefore intended to provide relief on the project front. The platform is intended to provide a shared virtual office in which all project employees can work together, regardless of where they are located in the world.
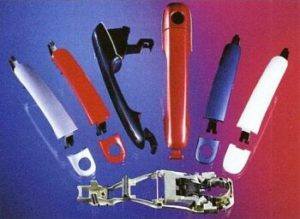
All project documents and other information are stored in this shared office. A search system that generates a running full-text index and can execute complex search queries in dialog supports employees in their search for information. Recurring organizational processes are stored in predefined ‘workflows’ and users automatically receive notifications about new or changed information and documents that affect them. Joint order management and, if necessary, joint schedule coordination promote the handling and transparency of a project. The system structures and channels product development processes with gate reviews and tracking documents. This means that the project activities remain transparent not only for the directly responsible agents and the project manager, but also for an extended project team, the sales department and the management. The advantage: although the parties involved do not have to meet in person as often, they are all on the same level of information. In order to cover this extensive range of services, the management consultancy Abels & Kemmner, which was commissioned with the conception and implementation, chose the e-management tool Livelink from Opentext as the basis. For the specific application, the charterers added specific modules to Livelink and configured the system into a ‘management system for virtual companies’. According to the structure of Livelink, the user of Kopl@ moves in three work areas.
- Information that only the user himself can access can be stored in the personal area.
- The project teams work together in project areas.
- The company workspace is open to all Kopl@ users as a forum and source of information.
As the confidentiality of data and information is extremely important in product development, Kopl@ works with a sophisticated authorization system. Users can be granted different access rights depending on their group membership and their role in projects, and individual access rights can also be defined for each object.
The use of Kopl@ reduces modification and travel costs by up to 50 percent.
The benefits of using Kopl@ can already be quantified: change costs are reduced by 35 to 50 percent, travel costs by 30 to 50 percent and transaction costs by 50 to 80 percent.
In addition, the time required to obtain information is reduced by 40 to 60 percent and the response time for customer requests by 50 to 80 percent.
It is also hoped that Kopl@ will increase the knowledge base that can be accessed within and across companies. The use of a cooperation platform such as Kopl@ is therefore also of strategic importance.
The advantages at a glance
Costs:
- Reduced change effort
- Lower travel costs
- Reduced transaction costs
- Transparent modification costs
Times:
- Faster access to documents
- Rapid induction of new employees
- shorter travel times
- Faster procurement of information
- Shorter time-to-market
Project risk:
- High data security
- Orderly, secure process
- Reliable and efficient handling of standard business processes
- Transparency of project activities
Information level:
- Equal level of information for all parties involved
- Access to the latest documents
- Avoidance of information overload