Cross-company collaboration often fails due to information gaps and problems coordinating deadlines. The automotive supplier Witte-Velbert therefore launched project management via the Internet.
Like many suppliers, Witte-Velbert GmbH & Co. KG, a manufacturer of locking systems for the automotive industry, works closely with selected suppliers in the development and manufacture of new products. In the past, a lack of or inconsistent information in the collaboration meant that the need for coordination and travel time as well as the costs for changes threatened to explode.
The distribution of digital and printed data by e-mail, fax or conventional mail did not lead to the desired transparency. There was the problem of maintaining the data promptly, which in this specific case had to be processed up to six times. The exchange of information often only took place over the telephone.
In order to make the project organization more efficient, Witte-Velbert has been working together with the suppliers C.W. Hanebeck GmbH (Iserlohn), Gebr. Wasserloos GmbH (Velbert), Lahme GmbH (Kierspe), Paragon AG (Delbrück) and Schrimpf & Schöneberg KG (Hohenlimburg) are working on a web-based central communication system as part of the Verbundinitiative Automobil (VIA) of the state of North Rhine-Westphalia.
The World Wide Office
The Kopl@ (Kopla) project is intended to be a shared virtual office in which all project employees can work together via the Internet. All project documents and other information are stored in this shared office. Project changes are incorporated into the system and are therefore automatically available to everyone involved.
Recurring organizational processes are stored in predefined “workflows”. Users are immediately informed about new or changed information and documents that affect them. Joint task management and, if required, joint deadline coordination support the handling and transparency of a project.
In the case of product development projects, the product development process is structured and channeled through project phases with gate reviews and tracking documents.
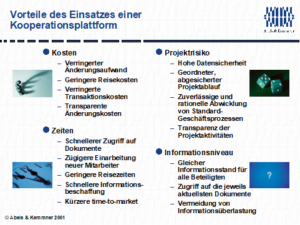
Advantages of a cooperation platform
This means that project activities remain transparent not only for the project team members and the project manager, but also for members of an extended project team, the sales department and the management.
In the Kopla test phase, which ran until the end of May 2002, the companies worked on the development of a locking system for the VW T5 as a pilot project. In order to be able to represent all functions, the entire product creation phase is mapped in Kopla in a task-oriented manner. All necessary information and design drawings are stored in the system. The management consultancy Abels & Kemmner Gesellschaft für Unternehmensberatung mbH, Herzogenrath, which was commissioned with the design and implementation, used the Livelink e-management tool from the Canadian software provider Opentext, expanded it with specific modules and configured the system into a “management system for virtual companies”. According to the structure of Livelink, the user of Kopla moves in three work areas. Information that only the user has access to can be stored in the personal workspace. Project teams work together in project areas, while the company workspace is available as a forum and source of information for all Kopla users. Users can be granted different access rights depending on their group membership and their role in projects.
Significant savings
Following completion of the test phase, the following results can now be quantified:
Change costs fell by 35 to 50%, travel costs by 30 to 50% and transaction costs by 50 to 80%. In addition, the time required to obtain information was reduced by 40 to 60% and the response time for customer requests by 50 to 80%. In addition, it is hoped that the increasing number of users and project management using Kopla will increase the knowledge base that can be accessed within and across companies. “Kopla enables us to handle projects with our business partners quickly and easily without having to store our sensitive data and documents on external systems that are not under our control,” says Edvard Rückert, Managing Director of Witte-Velbert, summarizing the advantages of Kopla.
The book on the subject
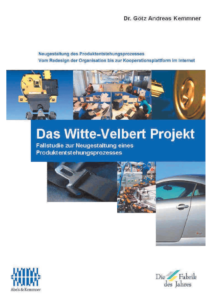
In the “Factory of the Year 2001” competition, Witte-Velbert GmbH won first place in the “Outstanding Product Development Processes” category. The brochure describes the journey from its beginnings in 1994 to the present day. The practical example shows how organizational processes, areas of responsibility and the organizational structure can be improved, how production and suppliers can be integrated into the product development process in the form of a virtual company organization and how customers and suppliers can be integrated using Internet technologies.
Order hotline:
Mrs. Magritsch, Tel. 089/32391-317
You can find more books and other products in our store at www.huss-shop.de