Optimization potential identified after implementation of SAP/R3 PP and MM
by J. Bertels1, Martin Jürgens2
With the introduction of the material management and production planning modules MM and PP from SAP/R3 at the beginning of 2002, EMSA created the IT basis for integrated production, warehousing and supply chain management. Once the system had been activated and was running stably, the search for optimization potential began. Abels & Kemmner was commissioned to do this. The results of the analysis are now available.
EMSA Holding AG produces a wide range of household, home care and garden products at its sites in Emsdetten/Münsterland and Swansea/Wales. The product range comprises around. 1,500 end products, of which approx. 1,150 are household items and approx. 350 are garden items. Customers in Germany and abroad are supplied from Emsdetten. Significant customer groups include specialist retailers, furniture and department stores, supermarkets, DIY stores and garden centers as well as other retailers that include EMSA branded products in their promotional programs. Customers’ delivery requirements result in around 5,500 order items to be delivered every day (550 orders, 10 items on average). 50% of these items have the delivery date “immediately”, which corresponds to delivery within 3 working days. A further 25% of the items are to be delivered within one week. The remaining 25% of the items have a set delivery date of more than one week.
The objective of the recently completed consulting project was to analyze the business processes and the configuration and handling of the SAP modules MM and PP in order processing at the Emsdetten site and to develop a concept to ensure a delivery readiness level of 98% for customers without increasing inventories or even increasing set-up times in production by reducing batch sizes.
The result showed that EMSA can reliably achieve a delivery readiness level of 98% in the garden products area by redistributing stocks between AB/XY articles and C/Z-Z2 articles without having to increase stocks and without the previously necessary hectic pace in production and the associated cost-intensive friction losses.
The studies show promising savings potential in the area of household items, which are easy to plan. In this segment, it was found that the desired delivery readiness level of 98% can even be achieved if around a quarter of this stock, which currently accounts for around half of the total stock value, is reduced. This means that approx. 14% of the total stock can be reduced. A clear liquidity reserve that should now be utilized.
The reason for this previously undiscovered savings potential was the fact that sales planning had so far carried out little differentiation of the articles. All articles were treated similarly. Accordingly, there were no storage and delivery strategies tailored to individual product groups. As a result, there were very large deviations in the planning for individual items, which led to shortfalls. As in the area of garden products, the unproductive hectic pace that was previously necessary to reliably meet customer requirements can now be avoided. In detail, for example, relevant control parameters of the MM and PP modules of the SAP R/3 ERP system, such as safety stocks, minimum lot sizes and replenishment times, were set manually on a blanket basis and “according to the feeling” of the planners or product line managers. This is set to change in the future. Firstly, the employees are to undergo a training project tailored to the specific needs of EMSA. On the other hand, the company is currently investigating the introduction of an add-on tool such as DISKOVER, which employees can use to carry out important strategic analyses even during daily scheduling. Further steps that are being discussed concern the review of processes, batch sizes and the formation of part families (group technology) in order to develop further inventory and productivity potential with additional inventory reduction. A cyclical external check of the relevant actuators would be optional here. Regardless of how these decisions turn out, however: What is clear is that the systematic supply readiness and inventory management system that has been introduced has unlocked significant potential, aligned the supply chain even better with customers and relieved EMSA’s administrative and planning workload, thus contributing to a sustainable increase in profitability.
The procedure
The project was carried out using a combined approach of methodical article structuring and process selection, as well as an initial process analysis. Of course, a lot of information has to be gathered first.
Once the project team had agreed on a common goal with all the key people (functionaries) involved in the project in a kick-off meeting, the first step was to analyze the current situation on the basis of interviews.
In addition to examining the product range with regard to product structure, market and product dependencies as well as expected changes (new/ discontinued products, serious market changes, etc.), the aim was to determine the material and information flows through the entire company from the customer to the supplier and back to the customer, particularly with regard to factors influencing the finished goods inventories at the Emsdetten site. Such influencing factors can be, for example, special customer stocks, influences that determine throughput times, capacity bottlenecks in production, quality and procurement problems, different storage locations, etc.
In practice, the problems range from master data quality (e.g. article data not available at an early stage, especially for new start-ups, blanket orders not recorded with suppliers or overly long replenishment times) to inadequate order information (e.g.: missing price specifications for price overprint) and delivery problems on the part of suppliers to poor form quality with missing information. However, problems or additional work often arise in the processes due to very industry-specific requirements. At Emsa, for example, this was priority control according to customer-specific delivery quotas.
The weak point analysis of the planning and fulfillment processes along the order processing chain is a basic prerequisite for designing a consistently coordinated order processing chain.
After the exact definition of the data structure, incl. the relevant SAP posting indicators were determined, the data was pulled from the SAP system. This meant that both master data and transaction data had to be made available for analysis with DISKOVER on a large scale. Such a targeted and extensive data transfer must of course be checked with appropriate plausibility checks.
To improve planning figures and optimize inventory management in the finished goods warehouse, a systematic approach was developed for structuring the range of articles and for selecting and optimizing planning procedures and parameters. The two product ranges “Household” and “Garden” were each examined separately. Analysis results were regularly presented to EMSA’s internal project team and article specifics and possible process variants were discussed. The direct involvement of dispatchers is always very important for sustainable success.
Methodical structuring of the article range makes the mass of articles clear and creates planning security.
First, the economic importance and consumption behavior of all products was determined by means of an ABC / XYZ analysis. While the ABC analysis provides information on the extent to which an item has contributed to economic success, the XYZ analysis evaluates how regularly it was consumed and in what quantities. In this context, influences such as trends, seasonal factors, promotions, structural breaks and the item-specific life cycle stages (new and discontinued products) must also be taken into account.
AX, BX, AY and BY articles (A and B: high-turnover, X and Y: regular consumption, easy to forecast) accounted for around 79% of sales in the higher-turnover “Household” segment. In relation to the number of articles, this corresponds to a share of approx. 32%. These easily plannable items account for 55% of the total current stock value, resulting in a high stock range of 1.87 months. This inventory reduction potential needs to be leveraged.
In the more seasonal “Garden” segment (flower boxes, planters, etc.), AX, BX, AY and BY articles account for around 61% of sales. This includes around 33% of the items in this area, which represent 42% of the total inventory value at the end of the season as at the reporting date. This corresponds to an inventory range of 1.1 months.
Due to the extensive availability of data, the XYZ analysis could be carried out on both a monthly and weekly basis. This has the advantage that consumption/demand within the month can also be recognized as regular or sporadic. As a result, it can be determined whether the average monthly requirement must be fully available at the beginning of the month or whether it can be spread evenly over the month. The internal project team and the dispatchers were thus able to determine the stock items to be planned in the future and specify stocking times for the subsequent simulation.
Determination of suitable disposition procedures
This was followed by the definition of suitable disposition procedures for each article class and the simulative calculation of the optimum stock levels for the different delivery readiness levels of 98%, 95% and 90%. The optimum process is the one that achieves the specified target delivery readiness level, e.g. 98%, with the lowest stock levels. In a second project step, the EMSA project team will work directly with the dispatchers to fine-tune the scheduling, including customizing the SAP system.
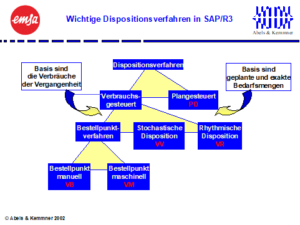
Optimize scheduling under SAP R/3 with DISKOVER 4.0
ERP systems were created to network complex company processes with each other using modules. In this respect, the strengths lie in integration. However, there is still room for optimization within the individual modules. For example, MRP under SAP is fuzzy in two respects and therefore leads to suboptimal results: Firstly, SAP lacks distribution-free procedures for determining the base value and safety stock, which are relevant in practice in many applications, and secondly, SAP’s own parameter optimization in the context of exponential smoothing cannot ensure the desired degree of readiness for delivery under certain framework conditions. For this reason, the efficiency of scheduling can be significantly increased by using the DISKOVER 4.0 add-on tool in addition to SAP R/3. If you consider that for every euro of inventory reduction, up to 30 cents in warehousing costs can be saved, the tool pays for itself from just a few million in inventory value and at the same time leads to an increase in delivery readiness.
In the age of just-in-time philosophies, the actual fulfillment of a planned high degree of delivery readiness in scheduling is becoming increasingly important and is being exacerbated by the new economy. Online shoppers demand supply-by-click. Nobody can afford a delay in the future. However, SAP’s own adjustment module for parameter optimization optimizes the parameters alpha and delta (SAP default: alpha = 0.2; delta = 0.1) only with regard to stock (minimization of MAD (Medium Absolute Deviation)) as part of first-order exponential smoothing. However, no further consideration is given to the target delivery readiness level to be achieved. This means that the alpha-delta parameter combination is not optimally coordinated in terms of achieving the target delivery readiness level. This is where DISKOVER (DISposition with the help of confidence intervals taking into account the actual stock issue distribution) comes in and optimizes the parameters taking into account the target combination “stock minimization while achieving a specified target delivery readiness level”. This takes place in the program in four steps, which are run through iteratively.
- After transferring the required data from SAP MRP, the average stock levels and delivery readiness levels achieved are calculated simulatively for each item for all alpha-delta combinations.
- Subsequently, the storage areas for stock levels and delivery readiness levels are determined.
- In the third step, a superposition of the spatial surfaces is carried out and the ideal migration curve of the alpha-delta surfaces is determined. This migration curve contains all alpha-delta combinations that represent the minimum stock levels for certain delivery readiness levels.
- Finally, the point on the migration curve at which the required level of readiness for delivery is reached is determined. This point corresponds to the optimum alpha-delta combination for scheduling, which is then transferred back to the R/3 system. The calculation of the basic value and the safety stock then takes place there.
Automatic process selection
Other helpful features of DISKOVER include article structuring and automatic process selection. In practice, the process is as follows: Once the data has been transferred from the SAP system, the entire range of articles is subjected to article structuring. An ABC indicator is automatically determined for each item, which provides information on the sales relevance of the item. In the next step, DISKOVER calculates the XYZ indicators, which provide information on the fluctuations in demand and thus on the predictability of the articles. An outlier analysis is also carried out for certain article groups so that they can subsequently be subjected to an adjusted disposition. The results of this analysis are incorporated into both the XYZ analysis and the subsequent process selection. Depending on the knowledge gained in these first steps, the most suitable forecasting method is automatically selected for each item.
All relevant disposition procedures taken into account
In addition to the standard SAP methods, other methods such as the distribution-free method developed by Abels & Kemmner for forecasting demand are also taken into account. This method is always advantageous when high fluctuations in demand are to be expected. The latter are becoming increasingly frequent, as product cycles are becoming shorter, purchasing behavior is becoming more hybrid and spot demands for smaller delivery quantities are increasing. In a study carried out by RWTH Aachen University, the proportion of items that had to be planned using distribution-free methods was 25%. With the help of these distribution-free processes, a further reduction in stock can also be achieved for this article group, while at the same time increasing delivery readiness.
Implementation procedure
DISKOVER is introduced in two steps. The first step is to investigate and determine how and under what conditions the process and parameter optimization can be carried out. In the second step, the automatic analysis is repeated at intervals to select the optimum forecasting procedure, which is ultimately completed by returning the data to the SAP system.
First, the relevant process data for order processing and the available planning procedures are determined. Data quality must be checked, as experience has shown that there are massive deficits in this area, which can greatly distort the results in the course of an analysis.
Comprehensive discussions on data interpretation are particularly important. For example, what is actually entered in the “Requested delivery date” field? Is this the current date entered by the system or the delivery date actually requested by the customer? How should the “confirmed delivery date” be interpreted? Is it fixed or, as one company found out, is it adjusted and updated in the weekly net change, which of course results in a fantastic actual delivery readiness level, taking confirmed delivery dates into account?
In addition, it is necessary to check how far back the available historical transaction data goes and in what form it can be provided, e.g. at document level or cumulated on a time basis, e.g. months. Finally, the data transfer must be defined. This includes which file and data record formats are used and at what intervals the transfer takes place. Once this preparatory work has been completed, the data exchange between the SAP system and DISKOVER can be started at the specified intervals. Depending on the transaction data, a daily, weekly or at least monthly recalculation of the scheduling parameters is recommended.
1Mr.Josef Bertels is project manager at EMSA-Werke Wulf GmbH & Co. in Emsdetten
2Mr.Martin Jürgens is a senior consultant at Abels & Kemmner