Avoid unproductive whip effects with market-synchronized production
by Oswald Kuschel1, Peter Bröcker2, Andreas Gillessen, Dr. Götz-Andreas Kemmner
In the current market situation, today’s supply chain management has only one undisputed benchmark: the wishes and requirements of customers and the market. In order to meet this standard with the continuing explosion of product variants, companies in almost all sectors must establish lean and flexible value chains that can be operated with the lowest possible inventories and minimal waste of resources. Uncertainty in market expectations and increasingly stochastic customer demand are further increasing the demands on supply chain management and, in particular, on companies’ flexibility. The example of Orthomol GmbH in Langenfeld shows how productivity can still be increased and market demands satisfied in such a situation despite the lack of economies of scale.
Orthomol has developed into the leading specialist for supplementary balanced diets. More than 100 products and over 50 trial and sample articles are currently being produced. As a delivery service, Orthomol guarantees its customers that orders received by 13:00 noon will be dispatched the same day at 17:00. Orders received later on the following day. In order to be able to guarantee this fast service with increasing individualization of the products and an increasingly stochastic demand, the entire value chain from shipping to packaging to production at Orthomol must have a very high degree of flexibility (see Figure 1). This means that product changes can be made relatively frequently thanks to optimized set-up times. Production delivers directly to the finished goods warehouse via packing, which is controlled via ranges of coverage based on sales planning. Stocks and therefore ranges were kept very low due to the high flexibility of production. However, withdrawals from the warehouse led almost immediately to the start of post-production. In order to enable short-term reactions and a high degree of flexibility, personnel capacities had to be “kept available” in all areas to ensure short throughput times and low inventories. At the level of the packaged but still unpackaged mixture, there is no further storage stage. As a result, the capacity utilization situation in the packaging area depends directly on the production output of the production lines running in parallel. Production therefore also sets the pace for the utilization of the more personnel-intensive assembly. For this reason, production peaks in packaging have long been balanced out by highly flexible external suppliers. Nevertheless, the changes in market demand also caused increasingly greater losses in the area of productivity in packaging.
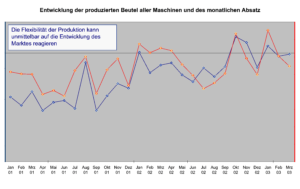
Harmonious production despite stochastic demand
The analysis and structuring of the range of articles (ABC-XYZ analysis) offered good starting points for improvement. By restructuring inventories, i.e. increasing the ranges of fast-moving items with relatively regular consumption patterns while at the same time realizing reduction potential in other item classes, major improvements in the production planning process were achieved without major inventory changes. By changing the stock ranges per item class, market fluctuations can now be dampened for production. This allows production planning to work with greater certainty. Orthomol is now able to plan production for 2 weeks in advance and even fix a production program for one week. However, only around 80% of all capacities in production and packaging are ever planned and around 20% is left open for so-called exotics and unexpected requirements. If these extraordinary requirements do not occur, the capacity is filled with “normal” orders. By reducing the hectic pace of operations and improving planning reliability in the planning horizon, the strong fluctuations in capacity can be reduced and capacity utilization significantly improved. This leads to significant improvements in productivity, whereby the market can still be served without compromises and without higher stocks of finished goods.
In order to be able to correctly assess the current situation of the supply chain, the following studies were carried out, among others:
- Analysis of market demand and the sales planning based on it, its forecasting methods and forecast quality
- Structuring of the entire range of articles from raw materials to finished goods (ABC / XYZ analyses), analysis of the development of inventories, ranges of coverage and their consumption behavior over time
- Analysis of productivity in the areas of shipping, packing and production over time
- Determining the employment risk of the individual production areas
- Analysis of production planning, its planning parameters, influencing variables and planning quality
- Checking the delivery reliability and flexibility of suppliers
Define employment risk and develop potential
The first point of contact for growing market stochastics is, of course, sales planning. The analysis of the market and the assessment of sales planning quality therefore form the starting point for all further considerations.
Without suitable countermeasures, the constant increase in the number of variants demanded by the market leads directly to an increase in inventories, because sales forecasts in the longer term cannot always be accurate and, in addition, the many product variants mean that sales fluctuations in the product mix are inevitable.
Detailed analyses of sales planning at Orthomol showed a similar trend. Although sales planning was fairly accurate across the entire product range, it was not possible to achieve the optimum possible at the individual product level. By adopting and initiating a wide range of measures, the sales planning process aims to achieve the optimum forecast for each individual item in an increasingly difficult market environment. The following measures, among others, were agreed for this purpose:
- Classification of the range of items and review/reassignment of the most suitable forecasting methods for each item class
- Setting tighter tracking signals of the sales planning system
- Introduction of a planning meeting with production and purchasing before implementation of the planning
- Optimization of the planning process for marketing campaigns with regard to necessary lead times
- Fixing the planning period of each individual product with regard to the period of its “precise” and binding planning
- Introduction and development of checklists for product managers to support planning
Changes in shipping
The shipping department was able to meet any market demand with its existing capacities. However, the flexibility achieved was not sufficient to be able to react to daily market fluctuations in customer demand by making short-term adjustments to the employment situation (Fig. 2). As a result, too many employees tended to be needed to guarantee practically “100%” delivery readiness. For this reason, it was discussed whether the worklist in dispatch could be increased. This could be done by extending the delivery of the goods to the working day after next at the latest. The increased volume of work could lead to improved deployment planning and thus higher basic employment. However, these changes would have a direct impact on delivery times. True to the maxim “The market makes the demands, we follow!”, it was therefore rejected. A so-called “after-work shift on call” in combination with basic employment is now intended to cover any peaks that occur more flexibly.
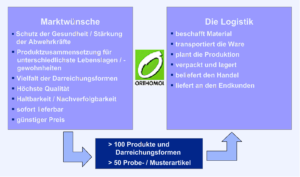
Changes in packaging
In the packaging department, we are also currently examining whether it would be economically viable to intensify cooperation with external suppliers while reducing the number of basic internal employees. The key decision criterion here is the upper price limit, which is determined by the (additional) costs of in-house production and compared with the supplier’s purchase price.
The cost consequences of outsourcing the service are determined by recording the costs that are incurred or can be saved by outsourcing and then comparing them with the new upper price limit for in-house production. However, the costs of in-house production are strongly influenced by the employment situation and the ability to adapt capacities to changing employment situations. However, the new production planning situation has already significantly improved the cost situation for internal packaging.
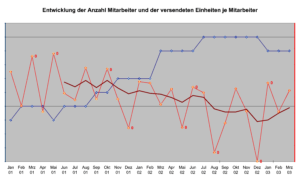
Summary
The example of Orthomol shows that the general trend towards greater flexibility in an increasingly difficult economic environment must be considered in a differentiated manner for each company and for each division. It is crucial to meet the wishes and requirements of customers and the market with a value chain that minimizes costs as much as possible. Everything must be subordinate to these requirements. On the way there, the company’s profitability and innovative strength must be the yardstick for all decisions as a decisive factor for survival. It is therefore not the productivity of the individual area that matters, but the long-term overall productivity of the value chain. It is often necessary to find the “optimum operating range” in the trade-off between inventory costs and flexibility costs.
About Orthomol
Orthomol was founded in 1991 by Dr. Kristian Glagau and his partner Dr. Hans Dietl. Contrary to the generally changeable economic situation, the young GmbH grew within a few years to become one of the market leaders in the micronutrients sector and currently employs more than 250 people. Product development is carried out by our own research and development department. Doctors, pharmacists, ecotrophologists and biologists at Orthomol are constantly monitoring current developments and research results in the field of micronutrients.
Orthomol products are supplementary balanced diets and are developed on the basis of the orthomolecular principle, which was founded in 1968 by the American Nobel Prize winner in chemistry Linus Pauling. Micronutrients are used as part of nutritional medical treatment to contribute to the success of medical therapy and delay the progression of diseases. Orthomol’s micronutrient combinations contain vitamins, minerals, trace elements, secondary plant substances (e.g. phytoestrogens, bioflavonoids), amino acids, omega-3 fatty acids and probiotics, depending on the indication. The special feature of the products is their complex composition and balanced dosage. Orthomol products are micronutrient combinations put together for specific indications, which are generally taken on the recommendation of a doctor or pharmacist. They are only available from pharmacies.
1 Oswald Kuschel is Operations Manager at Orthomol GmbH and managed the project from the customer’s perspective
2 Peter Bröcker is Head of Corporate Controlling at Orthomol GmbH