by Dr. Bernd Reineke
Globalization, globally distributed branches and the growing cross-company electronic data exchange are increasingly overtaxing existing ERP systems. In the near future, many companies will therefore have to decide on a new ERP system. However, finding the best system means checking more than a thousand criteria for over a hundred systems. We recently identified the right ERP system for a fast-growing IT company within three months, without significantly disrupting the employees’ normal daily routine.
The medium-sized IT company with around 650 employees and an annual turnover of €365 million develops and produces components for PC systems for both professional users and the SOHO sector (Small Office Home Office) and sells them from Germany and via its seven branches in Europe, Asia and the USA. Procurement is primarily from leading electronics companies in Taiwan and China. Due to the company’s strong growth and increasing globalization, the old ERP system was increasingly becoming a burden:
- The system offered no possibility of external connection via the Internet for the seven foreign branches in Europe, Japan, Taiwan and the USA, which was becoming increasingly uneconomical.
- Significant functional deficiencies in scheduling, warehouse management, service and inventory management could only have been supplemented by additional products with correspondingly high interface costs.
- In addition, the heavily modified legacy system was based on a file system that was becoming increasingly unstable due to the large increase in data volume, meaning that the necessary system availability could no longer be guaranteed or could only be guaranteed with very intensive maintenance.
- Even minor adjustments would therefore only have been possible with a great deal of effort.
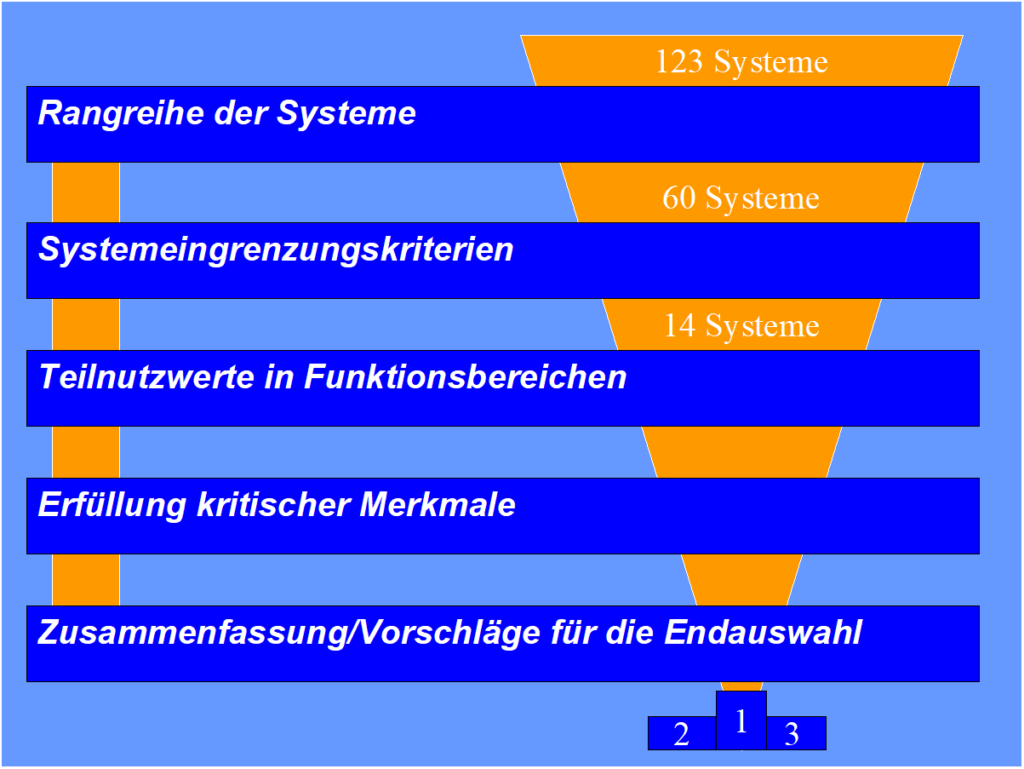
For these reasons, a system change was imperative, and a decision had to be made within three months in order to eliminate these growth- and performance-inhibiting factors as quickly as possible. However, the team, which had previously managed the old applications and had a very good overview of the requirements of the specialist departments, felt unable to manage a new system selection within the set time frame, especially as the old system was very demanding. It was therefore decided to bring in external consultants. When selecting the right consultant, comprehensive references were particularly important, as was the use of a tried-and-tested methodology, such as that offered by Trovarit AG’s IT Matchmaker for vendor-neutral software selection. This constantly updated database provides the most up-to-date overview of the relevant ERP and PPS systems currently available on the market and provides comprehensive catalogs of criteria for system selection.
However, before this database could be consulted, a target concept had to be drawn up, as this is the only way to compare it with the potential solutions. A suitable team was formed for this purpose at the start of the project. In addition to those responsible for the old system, employees from the sales, order processing, purchasing, scheduling, production and service departments were also selected. Based on a previous project aimed at optimizing the process organization, the target concept for the organizational processes had already been agreed with the specialist departments. The documentation of the processes with regard to the ERP selection was carried out using rough task descriptions and flow charts. Special features of specific customer processes or sub-processes were also recorded in the process documentation.
Based on this information, the requirements catalog with over 1,000 criteria was filled out together with the ERP specialists. This catalog was then used for the pre-selection phase of the suitable ERP system, whereby three basic database queries were to be run:
- Sum of all requirements to select the best all-round systems
- Exclusion of warehouse management requirements with regard to the possibility of supplementing an otherwise strong ERP system with extra warehouse management software.
- In addition, exclusion of the requirements for production planning and control, as production in particular should be supported by specific solutions in the context of documentation and serial number management, which can hardly be fulfilled by a standard system and will probably have to be supplemented by a special solution.
Preselection with the ERP database
We evaluated the catalog of requirements with the help of the ERP database, which Trovarit AG now offers with IT Matchmaker. The first result was a list of 123 ERP systems, sorted in descending order according to the percentage utility value of the all-round ERP variant including warehouse management and production planning and control. It was particularly noteworthy that a dozen of the systems met 80% or more of the requirements. The results of variants 1 and 2 allowed initial conclusions to be drawn about strengths and weaknesses in the areas of warehouse management and production planning and control. However, the analysis of the degree of fulfillment of certain functional areas, such as production requirements planning or external procurement planning and control, also clearly showed the strengths and weaknesses of the systems.
In order to further limit the number of eligible systems, additional criteria were evaluated that did not directly affect the system properties but were of considerable importance for the selection:
- The system provider should have at least 40 employees in the area of system development and system maintenance.
- The system should be used by at least 150 companies in order to prove the implementation know-how and to ensure the possibility of exchanging experiences with other companies.
- The sector-specific orientation of the system should correspond to the sector to which the company in question belongs.
- The system should be at a stage in its life cycle that ensures long-term investment security.
This information could also be queried and evaluated via the ERP database. This reduced the number of potential systems to 60. This number was further reduced by specifically considering the utility values of the functional areas already mentioned, so that the number of remaining systems was reduced to 14. Figure 2 shows the utility values of the 14 systems in relation to the three variants.
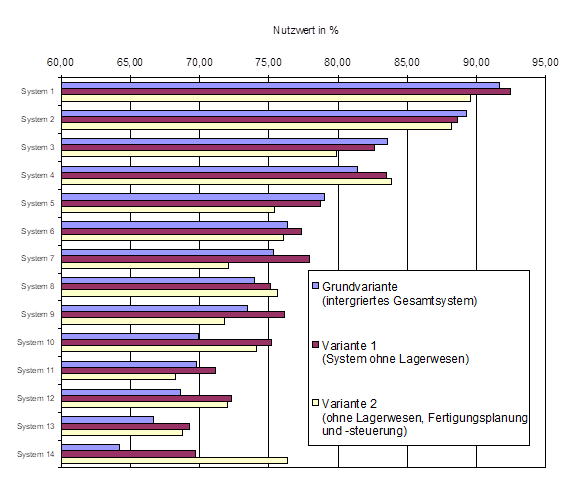
The further procedure concentrated on checking the 14 systems with regard to special functions that resulted from the target processes but were not queried in the specific form via the requirements catalog. Of the total of 27 criteria, the following should be mentioned here, for example:
- Aggregation of sales planning by region, customer and period
- Management of customer-related material data
- EDI interfaces to customers, suppliers and external warehouses
- Continuous serial number tracking from the end product to the component supplier
- Parts list history with the specification ‘replaced by’ and ‘replacement for’
On the basis of this additional information, the picture of the 14 remaining systems was clarified and it was quickly possible to agree on four systems for closer consideration. Of great interest was a system provider that had taken over the manufacturer of the legacy system in use and had already replaced the legacy system with its own system in several cases. With this system, it could therefore be assumed that tried-and-tested interfaces for transferring master and transaction data and the necessary consulting expertise were already available
Final selection phase
The system tests in the final selection phase were prepared with the help of so-called test schedules. This outlined the business processes that were to be run through and evaluated on the system as examples during one-day workshops with the system providers. All project team members took part in the workshops. There was also plenty of opportunity to ask specific questions about the system and the required features. This was also the time when the future users saw the system interfaces for the first time and got to know the system providers. For the system providers, this was the time to demonstrate their expertise and show their flexibility with regard to requirements.
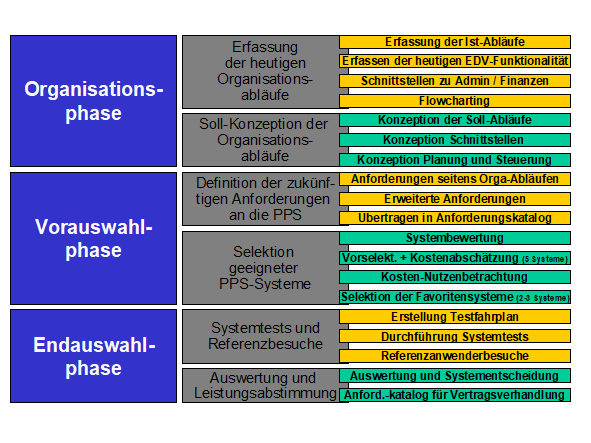
In order to save time in the selection process, it was decided to contact reference users of the systems under consideration in parallel to the system tests and in three cases to visit them. The reference users were suggested by the system providers in terms of similarities in industry and business model. The visits themselves took place without a representative of the system provider, so that an open exchange of information and opinions could take place between users and the project team members. In addition to information on the system features, background information on the system providers was of particular interest:
- What experiences were made during the introduction?
- How does the provider respond to customer wishes?
- What is your experience of the release policy?
- What response times should I expect in the event of problems?
The workshop results were evaluated by team members using school grades for the individual sub-processes and system features (e.g. user interfaces). These results were also compiled and compared in tabular form. Two systems received good marks, while the other two candidates received consistently poor ratings and were therefore excluded from further consideration. Unfortunately, this also included the successor to the old system. This was an excellent position for the future user to enter into negotiations with the two remaining providers and achieve good conditions. But in the end, it wasn’t just the price of these systems that made the difference. It was strategic considerations that ultimately tipped the scales in favor of one of the two systems:
- Availability of competent consultants for system implementation
- Availability of already trained system users on the labor market
- Strategic system orientation for future development
- Market position of the provider
The decision
In the end, the decision-making process was so far advanced that we were able to make a clear decision that everyone (including the Management Board!) could understand. The winner of the selection process not only fulfilled the criteria described above very well, but also offered an integrated solution for warehouse management. Only in the area of production planning and control were the expected additions necessary. In the implementation project, we pursued the strategy of introducing the system as standard and putting it into operation. Adjustments to add or optimize functions were only tackled afterwards. But more on that soon here.
Conclusion
Thanks to the standardized procedure and the experience of the external consultants, the selection process was completed within the set timeframe despite the extensive content. By defining the target processes and the resulting requirements, there was a very concrete idea of the possibilities of the selected system and its subsequent practical application right from the start. This had a very positive effect on the subsequent introduction and implementation process. In this respect, a structured approach is always recommended, which is shown again in brief in the diagram below.