by Dr. Götz-Andreas Kemmner
Competition in consumer electronics is tough. Manufacturers of computer “peripherals” such as Cherry are therefore dependent not only on excellent products but also on outstanding supply chains. The company, which is one of Europe’s leading manufacturers of computer input devices, snap-action switches, automotive switching and control systems, therefore decided to subject its existing supply chain to a critical review in a two-day workshop accompanied by Abels & Kemmner in order to reveal further optimization potential.
Three areas of action should be addressed: The improved integration of customers, the optimization of delivery readiness and inventories and the better integration of the company’s own suppliers. At the beginning of the workshop, Jürgen Feihl, Head of Materials Management and Purchasing, got his team in the mood with a presentation on Cherry’s future product strategy and the resulting requirements for the supply chain. In a further presentation, Abels & Kemmner explained what supply chain management means and what objectives it pursues.
Following this plenary event, the current situation in the three fields of action was analyzed in three parallel workshops, common objectives were developed and initial concepts were drawn up as to how the desired objectives can be achieved in the individual areas. The workshops were moderated by Jürgen Feihl, Thomas Kilchert, Head of Controlling Materials Management at Cherry, and the consultants from Abels & Kemmner. The consultants moved from team to team, contributing food for thought to the discussion and thus ensuring the necessary synchronization between the teams.
As the individual fields of action cannot be considered independently of each other, it was important to coordinate the findings and considerations of the individual workshop teams with each other. For this reason, all three teams met in the late afternoon of the first day to present their interim results to each other.
Regina Späth, Jürgen Feihl’s assistant, had organized a dinner and cabaret performance for the evening. Although the evening was long, the entire team met at 8:30 sharp the next morning to continue the workshop work. Beforehand, Jürgen Feihl, Thomas Kilchert and the team of consultants had already agreed on the work program for the second day.
On Saturday, after lunch, the three teams met again in plenary to present the results of the individual working groups. The results of the three fields of action were defined in a strategic master plan, which also set out all the necessary work steps and sub-projects with their interrelationships, sequences and key dates. With this roadmap, Cherry and Abels & Kemmner are now working on the result-oriented optimization of the value chain.
For the initiator of this workshop, Jürgen Feihl, Head of Materials Management and Purchasing, the decision to hold such a workshop was absolutely right because, on the one hand, all employees involved in the supply chain were involved in the change measures from the outset and were thus able to develop common objectives. On the other hand, they were able to quickly overcome their fear of the external consultants, agree on the joint chemistry for potential follow-up projects and create a spirit of optimism. A supply chain workshop is therefore a highly efficient way of working, the results of which could hardly have been achieved in normal meetings.
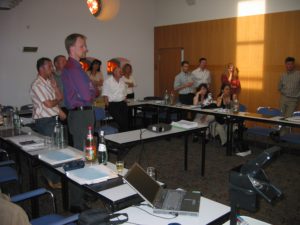
Observe objectives
The top priority when planning workshops is to define the objectives of such a workshop. Here, the mistake is often made that a global goal is formulated, such as “How do we increase customer satisfaction”. But what is usually forgotten is that the workshops themselves should have their own goal. Without a workshop objective, such as in the case of Cherry “definition of a master plan”, there is a risk that everyone will have racked their brains as to how customer satisfaction could be increased, but the transfer from this workshop will not take place. Therefore, always make sure that a workshop also has a clear objective, which must be developed during the meeting and documented at the end and agreed as clear tasks with fixed deadlines.
Create framework conditions
A key condition for the success of such a workshop is also that it is held outside the company, e.g. in a hotel, so that the workshop is removed from the daily routine and so that the participants – in Cherry’s case for two days – can concentrate on the topic without being distracted by day-to-day business. In order to gain the necessary distance from everyday life and strengthen the team spirit, it is advisable for the participants to spend the night together at the conference venue and not drive home. This strengthens the shared experience and the perception of colleagues not only as functionaries, but also as people.
Letting everyone have their say
In addition to the goal orientation, it is particularly important in a workshop that all those involved have an appropriate say so that the target agreements can also be supported by all employees. The moderator of a workshop therefore has a special role to play: in day-to-day operations, problems often only come to light slowly. This usually happens much faster in workshops. In such situations, the moderator is called upon. It must be able to lead participants back into the group and deal with dominant participants who need to make a name for themselves. This requires a good dose of empathy and the ability to overcome conflict situations by motivating the participants.
The moderator must also have a reliable command of the overarching topic of the workshop and, in Cherry’s case, be a proven expert in the areas of production organization and logistics. His ability to pass on knowledge and expertise is crucial for the success of the workshop and for the start of successful project management of operational restructuring measures.
Don’t let everyday life catch up with you
Once such an initial workshop has been completed, it is then important to gradually implement the goals that have been set. First and foremost, this requires that appropriate time is made available for the company’s own employees and a budget for the necessary external support to implement the measures. Even if you don’t like to believe the consultant: without external support, major change processes in companies are no longer feasible. The lean personnel structures on the one hand and the necessary specialist knowledge on the other require external support in order to successfully implement the change process. It is also advisable to divide the catalog of measures into milestones in order to set small interim goals that can be achieved within a reasonable period of time.
This is the only way to ensure that the solutions adopted do not come to nothing or are delayed by months or years because day-to-day operations catch up with you and slow you down. Last but not least, the achievement of milestones should also be communicated so that all workshop participants perceive the success of the project and perceive the results as a consequence of their own performance in a motivating way.
About Cherry
The company headquarters of Cherry GmbH in Auerbach, Upper Palatinate, controls the fortunes of Cherry Europe with around 2,100 employees. With production facilities in Auerbach, Bayreuth in Upper Franconia and Klasterec in the Czech Republic, Cherry manufactures its products and supplies them to its international customers via regional companies.
Cherry’s range of computer keyboards comprises several product lines, which will be supplemented in the fall of 2003 by the new Cymotion series with its pioneering design and functionality. Cherry extends the range of functions of computer keyboards either integrated in the keyboard or by means of complementary products with a variety of additional functions such as chip/magnetic card readers, biometric identification systems, etc.
In the automotive segment, Cherry is a leading supplier of mechatronic products, particularly in the area of locking systems and convenience functions.