Kanban halves the inventory value at Montblanc
by Burkard J. Kiesel, Peter Kluge, Andreas Gillessen, Dr. Götz-Andreas-Kemmner
With the introduction of Kanban control for the production of components and the JIT principle for the assembly of the end devices of the Bohème writing instrument family in March 2003, Montblanc laid the foundation for improved delivery readiness, shortened throughput times and reduced inventories. The total stock reduction potential amounts to 48% of the existing stock value at the start of the project. Due to the successful launch of this project, the Meisterstück writing instrument family will also be converted with immediate effect. From a project management perspective, the “go-live” of Kanban went particularly smoothly. In operation, the solution developed especially for Montblanc impresses with its simplicity and transparency for every employee.
After Montblanc, with the support of Abels & Kemmner, reengineered the sales planning process last year, from budget planning and the forecast process to rolling monthly demand planning (see m+m issue 6/2002, pages 32-35), the project plan included ensuring the delivery readiness of the central warehouse in Hamburg and reducing throughput times and stock levels. Due to the high level of vertical integration, the long replenishment times and the large and constantly growing number of variants, efficient value chains should be established by setting up decentralized organizational control loops that reduce the supply risk at all production levels to a minimum. However, the MRPII logic used (see diagram), with its very high coordination effort, did not deliver satisfactory results. The previous approach lacked flexibility, particularly in the event of short-term fluctuations in demand for individual end products. In order to ensure delivery readiness on the market, excessive stock levels were necessary along the entire value chain up to the finished goods warehouse.
At Montblanc, the main lever for improving delivery readiness while simultaneously reducing inventories was to set up JIT production and thus shift inventories from the variant-rich end device to the variant-forming component level. The analysis of throughput and set-up times had shown that JIT production was possible without major costs. However, setting up JIT production requires a reliable supply of components and purchased parts for final assembly. For this reason, a central Kanban warehouse was set up before final assembly, as well as further Kanban warehouses before various upstream production stages. Suppliers are currently also gradually being integrated into the system.
Thanks to the precise design of the Kanban system and the intensive and thorough preparatory work, it was possible to go live with the Kanban system without any major problems. All preparations for the changeover were completed within just three days. As Kanban systems are self-controlling systems which, in principle, do not require an additional IT system for production control, the Kanban system at Montblanc was designed in such a way that production can also run without the SAP system in use. At the same time, the SAP processes were redesigned so that they do not hinder the processes of the Kanban system with additional administrative work. The employees only open a production order at the start of production of a batch size and report it back again after completion. No further SAP processes are necessary. All stock and stock transfer postings are already automated in the background. Over the next few weeks, the Kanban system will be linked even more closely with the SAP system. SAP’s own Kanban control system is being introduced for this purpose. In future, orders will be opened and closed automatically by scanning the barcodes on the Kanban cards. This all sounds very easy. However, many details had to be considered in order to successfully introduce the Kanban system.
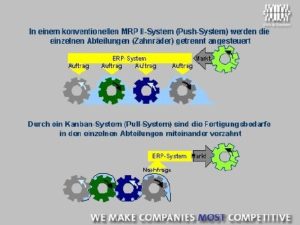
Implementation and introduction
The introduction of Kanban began with a change in the working methods and behavior of the employees involved at Montblanc. This alone necessitated the decentralization of production control back to the individual production areas. One of the main reasons why many companies have problems when introducing Kanban systems is that employees are not prepared to comply with the Kanban rules. They manufacture for stock, stockpile components, do not adhere to batch sizes or throughput times. If the employees are not convinced by the system, they do not adhere to its rules and thus cause the system to fail. A key success factor in the introduction of Kanban at Montblanc was therefore the integration of employees into the system concept. All organizational processes were developed together with the employees in the respective production areas. In this way, the employees’ trust in the concept and their understanding and identification with the overall processes and the detailed processes of the respective production areas could be created.
In practice, however, many companies experience a disaster during the introduction phase because the system has not been adapted to the reality of production processes. At Montblanc, all relevant material, information and order handling processes were therefore recorded before the actual dimensioning of the control loops and tailored to the requirements of the Kanban processes together with the employees in the production areas. The processes were considered under the following aspects:
- Is a flow principle across production area boundaries possible without setting up a Kanban warehouse?
- If a Kanban warehouse is indispensable, can it be set up at a lower value-added stage or before a variant-forming production stage?
- Can production and set-up times and batch sizes be reduced?
- Is the process stability sufficient to guarantee production times and is the process quality controllable?
- Is the capacity situation (employees / machines) sufficient or sufficiently flexible to guarantee security of supply?
- Are the discipline and qualifications of the employees sufficient for managing the Kanban system?
All identified major reorganization potential was deliberately postponed until after the introduction of Kanban control. On the one hand, this made sense because initial experience with the new system in live operation can only be gained after the Kanban introduction and this has a decisive influence on the question of how the processes can and should be changed. This also avoids duplication of work. On the other hand, the changeover to Kanban should not be delayed by other reorganization projects.
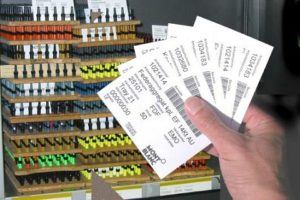
Don’t lump everything together
At Montblanc, the characteristics of the range of articles place very different demands on the dimensioning of the Kanban control loops. There are production areas that work with large batch sizes due to the process and other areas that are characterized by minimal to no set-up times. The only way to do justice to these different areas was to differentiate the Kanban dimensions accordingly. The actual dimensioning of the individual Kanban control loops and thus the determination of the number of Kanban types in circulation was therefore placed on a broader, mathematical-analytical foundation. When dimensioning Kanban control loops, often only the replenishment time per Kanban, the average consumption of the article (historical), the quantity per Kanban container and a so-called safety factor are taken into account. With this approach, the number of Kanban cards in circulation and thus the stock level essentially depends on a factor that is not determined mathematically and analytically, but on the basis of a “gut feeling”. Important determinants such as
- Lot size of the supplier (collective kanban)
- Batch size / consumption of the customer
- Consumption behavior of the article (XYZ behavior) and thus the correct safety stock
- Reject factors and
- the future consumers
are usually not even taken into account. However, it is not possible to optimize inventories, throughput times and the delivery service. This is the second main reason why many companies struggle with the introduction of Kanban and do not achieve the desired success.
One of the major weaknesses in the dimensioning of a Kanban control cycle is the calculation using consumption from previous periods. In the dimensioning for Montblanc, on the other hand, the “future” in the form of rolling sales planning was used for the underlying consumption values. As a result, Kanban at Montblanc has become an acting rather than a reacting control system.
Another weak point of existing Kanban systems is often the lack of regular resizing of the system. However, re-dimensioning must be carried out quickly and easily at regular intervals or as required, whether due to changes in sales forecasts or production parameters. At Montblanc, the scheduling department is responsible for this. It will carry out the resizing of each individual item as required or at regular intervals. The result of the redimensioning is a change in the number of Kanban cards in circulation. If the number of cards is increased, the additional cards must be fed into the system or withdrawn from it if the number of Kanban cards is reduced.
The calculation of the yellow and red areas of the Kanban boards and a simulation of the capacity situation of the individual production areas were carried out at the same time as the dimensioning of the control loops. The simulation calculates the maximum and minimum number of set-up operations required per time unit and compares these with the existing capacity situation. In addition, the storage space required for the Kanban items was dimensioned by calculating the minimum, average and maximum storage space required per item and Kanban warehouse over time. This data ultimately formed the basis for the procurement of sufficiently large Kanban boards and shelving systems.
PPS systems and Kanban
Since Kanban is a self-controlling system, it does not require an additional PPS system in principle. Therefore, when implementing Kanban, the aim should not be to forcibly integrate existing PPS systems into the Kanban system. Rather, it is necessary for the PPS system to have a logical interface to the Kanban system. The Kanban system at Montblanc was therefore designed in such a way that production can also run without the SAP system in use. Nevertheless, an image of the production processes in a PPS or ERP system is required for order accounting, procurement and inventory planning.
Why not make direct use of the Kanban functionality of many ERP systems? A key feature of a Kanban system is the visualization of all processes for all employees. This is not possible by mapping a Kanban board purely in the ERP system. At Montblanc, for example, SAP Kanban will run in parallel to the manual Kanban system in the future, but normal users will not notice this. You simply set different statuses in the system by scanning the barcodes on the Kanban cards. This synchronizes the material balance in the SAP system with the physical stock changes. Another argument against pure Kanban control via the SAP system is that the SAP system currently still has major weaknesses in Kanban dimensioning and has no solution for processing collective Kanbans.
Summary
The success of Kanban lies in the self-control of the production areas within the framework of the defined Kanban rules and the exclusive focus on customer requirements. The self-regulating control loops reduce the complexity of the entire logistics planning process. This makes the permanent intervention of the central control system in the processes superfluous. However, it remains a permanent task for all employees involved in the system to further optimize the value chains in terms of throughput times, delivery service and inventories by further improving the framework parameters such as batch size, set-up and production times, reject rates, etc.
About Abels & Kemmner
Abels & Kemmner GmbH, which is celebrating its 10th anniversary this year, was founded in 1993 by the engineering and economics experts Dr. Helmut Abels and Dr. Götz-Andreas Kemmner. The company focuses on streamlining value chains (supply chain optimization) for series and variant manufacturers as well as wholesalers. Abels & Kemmner deals with the design and optimization of order processing and logistics from suppliers to customers and from article assortment to IT support. Supply chain concepts that we have developed with our customers have already won two best practice awards. A&K caused a sensation in 1997 when it founded the first virtual company made up of six medium-sized companies from the automotive supply industry.
The second focus is on restructuring and earnings enhancement projects. Here, the consultants develop going concern forecasts as well as restructuring and downsizing concepts and implement these in the companies. Abels & Kemmner has made a name for itself in crisis and turnaround management through the successful restructuring of medium-sized companies. In recent years, the consultants have been involved in the restructuring of the majority of major corporate insolvencies in Saarland.