New methods for optimizing the procurement and inventory of spare parts
Withdrawals from spare parts warehouses rarely follow the known probability distributions. The new scheduling system now implemented at an automotive supplier takes this into account.
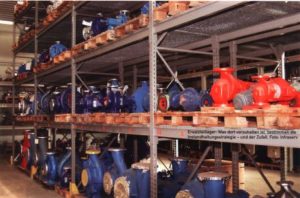
Strategies for stocking spare parts and maintenance materials depend on two important factors: the chosen maintenance strategy – and chance.
At first glance, chance does not seem to be a factor that is particularly easy to plan with. But random distributions determine the removal sequences of materials and spare parts – and when experts use mathematical methods to analyze these sequences, the “fleeting journeyman of chance” becomes a reliable helper. And it was precisely this task that the logistics experts at Stabilus GmbH in Koblenz solved together with the developers of special planning software.
For the logistics experts at Stabilus, this work began with a certain amount of rethinking. Stabilus is a manufacturer of systems for hydraulic damping and adjustment of flaps, doors and seats in numerous industrial products, but especially in the automotive industry. And the usual handling processes in the area of procurement and production of series materials have had a significant influence on the company’s thinking.
However, the area of non-series materials such as spare parts and repair materials is structured completely differently and subject to different rules than the management of series materials. And these conditions must be taken into account when planning maintenance requirements.
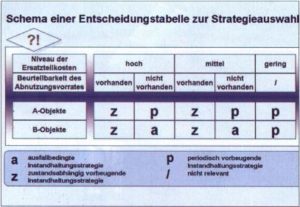
The objects are categorized according to their importance
In order to plan these materials correctly, it must first be made clear for which maintenance objects they are required. It is common practice to classify maintenance objects according to A, B and C objects:
“A” objects are particularly important for the realization of production targets. It is typical for A systems that their failure leads directly to a reduction in the output of end products. Spare parts belonging to these systems must therefore be given the utmost attention when planning.
“B” objects are also very important for the implementation of production targets. However, they are either designed redundantly or exist several times in the process chain, and their degree of utilization allows some of the maintenance objects to be taken out of operation for a certain period of time.
“C” objects are maintenance objects of minor importance that either cannot fail in the narrower sense or whose failure has no influence on the realization of the production targets.
If a basic scheduling strategy is now to be defined for A and B objects, then two criteria in particular are of paramount importance:
- the amount of the spare parts costs and
- the assessability of the wear stock.
The higher the spare parts costs for a maintenance object, the more advantageous a condition-based maintenance strategy proves to be, which largely utilizes the useful life of a part.
However, condition-based preventive maintenance is only possible if the wear stock of a maintenance object can be assessed.
However, this usually requires the use of complex inspection technologies, so that a trade-off between spare parts costs and inspection costs is necessary.
Based on these considerations, basic maintenance strategies can then be assigned to the individual assets, which can be represented in a decision table.
This decision table forms the basis of the scheduling strategy for the various maintenance materials. A series of criteria relevant for scheduling, such as delivery readiness levels and safety stocks, can then be derived from these specifications.
As many maintenance materials are required in A, B and C objects and sometimes have longer delivery times, effective scheduling of maintenance materials also requires a demand forecast based on historical data. And this is where “tamed coincidence” comes into play.
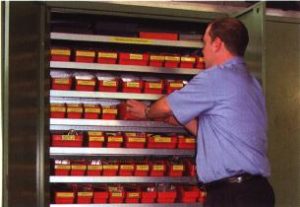
Normal distribution is not the normal case in warehousing
This is because the distribution of demand volumes plays a decisive role in deriving the right forecasts for future demand structures from historical data. The standard MRP procedures used in ERP or IPS systems generally assume a normally distributed stock issue.
In practice, however, this is only very rarely the case – in reality, the proportion of normal distributions in stock issues is only around 5%. A relatively large proportion of the distributions, around 25%, cannot even be assigned to any of the theoretical distribution types.
Stabilus was now looking for a solution in SAP for the planning of non-serial articles that cannot be assigned to any of the theoretical distribution types, which would also make it as easy as possible to plan this scope of requirements.
The “Diskover” program offered such a solution – because this software takes into account the actual distribution of outgoing stock. In conjunction with the leading SAP system, this software now determines the optimum scheduling procedures and parameters in two successive stages.
First, the parts are sorted in an article structure according to demand and consumption patterns.
The program then determines the optimum scheduling procedures and parameters for each article class with regard to stock levels and required delivery readiness. These parameters are then transferred to the leading host system, in this case SAP, or to DISKOVER itself in order to generate the order proposals for parts procurement.
The determination of item-specific basic requirements and safety stocks is carried out in such a way that a specified target delivery readiness level is taken into account, as well as the actual distribution of both stock issues and replenishment fluctuations within the company.
Uwe Mollenhauer, Head of International Logistics, Production Control and Material Planning (SILS) at Stabilus, is certainly satisfied with this “taming of chance”. “DISKOVER enables us to optimize our stocks quite elegantly at the level of agreed delivery readiness for the large number of our non-series materials,” he says.
Diskover 4.1: Areas of application, structure and features
The Diskover 4.1 scheduling system is an operational management system for optimizing the supply chain from purchasing to delivery.
It offers extensive selection mechanisms for daily scheduling as well as portfolio analysis and simulation functions and distribution-free scheduling procedures.
DISKOVER (DISposition with the aid of confidence ranges taking into account the actual stock issue distribution). can be run as an add-on tool under SAP and all common ERP, PP and WW systems.
The software is programmed in C++ and runs as a client on all Windows platforms.
The central database server, for example Qraclde or MS-SQL, communicates with the leading ERP system via a standardized interface. Client and server must be designed according to data volume.