Getting a grip on method chaos during process optimization
by Prof. Dr. Helmut Abels
Many production companies are constantly striving to optimize their production processes. A large number of optimization methods exist for this purpose. However, experience shows that the focus is still predominantly on optimizing individual areas or sub-processes. The optimization successes achieved thus easily “fizzle out” in the overall process or sometimes even have a counterproductive effect if they are not embedded in a consistent overall solution.
In order to better organize the use of methods, an increasing number of companies are establishing so-called “integrated production systems” (GPS). GPS form a regulatory framework for the methods that are to be used in all parts and processes of a company. The pioneer of this development is the automotive industry, above all Toyota with its well-known Toyota Production System (TPS). Today, all other automotive suppliers as well as many suppliers and, increasingly, production companies in other sectors also have such systems. The Daimler Chrysler Production System (DCPS), for example, describes 92 optimization methods, of which around 60 are to be introduced across the board in all plants.
The success of these systems is sometimes called into question. Critics question whether there can be a standardized system for all plants if the framework conditions (product structure, target markets, production organization, etc.) differ significantly (cf. e.g. Weber/Wegge 2003). The transferability of this approach to individual and small series manufacturers can also be discussed. Nevertheless, two aspects of the production systems that are already established always stand out:
- The development of synchronous (consistently optimized) production processes is a matter for the boss. This requires corresponding visions and guidelines from the company or plant management, the development of which cannot be delegated.
- The variety of methods offered in production systems is still considerable. This also leaves open the question of which methods are necessary for the implementation of synchronous production processes and in which order these methods must then be introduced.
Value stream management can provide important assistance in answering this question. Value stream management is a management tool which, from the outset, does not focus on partial process steps, but on the manufacturing process as a whole, i.e. at least “from ramp to ramp”, but cross-plant or cross-company considerations are also possible. It offers the manager support in three ways:
- Using simple tools, a transparent basis for discussion is initially and quite quickly created by recording the current situation.
- This is followed by the development of the future value stream vision for the synchronous process flow.
- Due to the simplicity of the illustrations, value stream management is also ideal for communicating the vision to employees and for deriving the necessary individual measures, which are then implemented in project teams in line with the overall design.
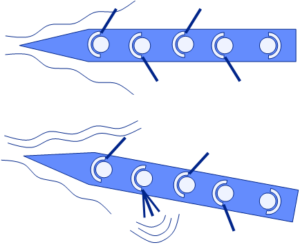