DISKOVER: Scheduling add-on tool for ERP systems
The optimal disposition of the “necessary evil” inventory is a decisive competitive factor for both series and variant manufacturers as well as wholesalers, because this is where customer satisfaction and profit or loss are mainly decided. If you achieve a high level of delivery readiness, customers are satisfied; however, if delivery readiness is bought with excessively high inventories, you run the risk that financing costs, warehousing costs, scrapping costs and depreciation requirements will eat into profit margins. Unfortunately, in times of faster product life cycles and more hybrid buyer behavior, scheduling has not become any easier despite sophisticated IT systems. The DISKOVER scheduling add-on tool for ERP systems helps.
Empirical facts
A number of mathematical-statistical methods and models exist for determining future requirements and security stocks. This is often based on standard storage situations, which allow mathematically exact calculations, but usually do not represent an adequate model for practical problems: A large proportion of the models assume a normally distributed stock issue without taking the actual stock issue distribution into account. In practice, however, the proportion of normal distributions in outgoing stock is only around 5%. However, a relatively large proportion of the distributions (approx. 25 %) cannot be assigned to any theoretical distribution type at all.
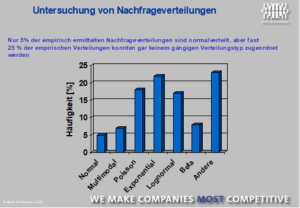
In order to be able to plan precisely, it would actually be necessary to determine the existing distribution type of a demand with the help of statistical test procedures before the actual planning calculation. Until now, this was far too time-consuming for day-to-day operational practice, as no suitable software tools were available. However, ERP providers have not yet taken an interest in this increasingly explosive topic.
The consequence
For this reason, the management consultancy Abels & Kemmner developed the DISKOVER scheduling tool (DISposition with the help of COndifence areas, taking into account the actual stock issue distribution) on its own initiative. DISKOVER is based on specially developed mathematical procedures that enable precise articulation. It is not necessary to identify the distribution types of a demand. Initially, DISKOVER was used as an in-house analysis tool for consulting purposes. Runtime versions have also been available for around two years, currently in version 4.1. Item-specific basic requirements and safety stocks are determined taking into account a specified target delivery readiness level and the demand distributions that actually occur in the companies. DISKOVER is a front end for daily scheduling and integrates seamlessly into the existing ERP, WWS and PPS landscape. As an integrated operational system within an existing materials management or PPS system, DISKOVER receives the data through direct access to the SQL database of the corresponding host computer.
Brand manufacturer Montblanc (SAP)
Montblanc-Simplo GmbH, Hamburg, has been using the DISKOVER 4.1 add-on tool, which is linked to the SAP R/3 SOP function, for more than a year to plan the central sales planning of around 1,000 product groups and 3,000 articles. Since then, demand peaks and supply bottlenecks can be identified earlier despite the wide range of variants and seasonal business, allowing them to be reduced in good time. JIT production and a KANBAN system, which is linked to SAP, were also introduced to streamline the warehouse. This restructuring will reduce the inventory value by 48%, almost halving it. A key factor here is the reduction in finished product inventories, in which the added value must be factored in.
“With DISKOVER, we have found a practical economic tool that supports our SAP world very well” Burkard J. Kiesel, Director of Technology at MONTBLANC-SIMPLO GmbH, Hamburg.
Specialist wholesaler Alfred Rudolph (FAMAC)
The medium-sized specialist wholesaler for kitchen accessories Alfred Rudolph GmbH & Co. KG from Halver works with the FAMAC ERP system from Bäurer. Initially, DISKOVER was used offline to determine the optimization potential in an introductory project. Since the dispatchers themselves have been able to make full use of DISKOVER’s possibilities in their day-to-day business, the inventory situation and turnover have improved significantly. The inventory range as a ratio of inventory to consumption has almost halved from 1.93 to 1.07 months. This corresponds to a virtual doubling of stock turnover.
“Our real figures, some of which can be seen in the balance sheet, prove that the preparations for the introduction of DISKOVER have paid off.” Sabine Plage, Purchasing Manager, Alfred Rudolph GmbH & Co KG, Halver
Medical IT manufacturer Tunstall Group (Baan)
Tunstall Group Ltd, a manufacturer of electronic systems for the care of disabled, sick and elderly people in their home environment, works with BAAN. Using DISKOVER, it was found that finished goods inventories could be reduced by 45%, with significantly improved delivery reliability of 98%.
The sum of successes
By using DISKOVER, Abels & Kemmner has so far achieved considerable inventory reductions: 82% of the companies have been able to save at least 15%, 32% have even been able to save more than 25%. The largest cluster with 43% of companies saved between 20 and 25%. However, reducing the value of inventories is only one aspect that is important, especially in difficult economic situations and Basel II discussions, but in today’s competitive environment, ensuring a high level of delivery readiness is often more important for companies. All DISKOVER users have achieved delivery readiness levels of around 98 percent. This planning security has an impact in many ways:
- The sales department can make reliable delivery promises at any time.
- Production knows at all times which batches are to be produced.
- Purchasing can conclude more targeted framework agreements.
All of this has a positive effect on the company’s performance and is ultimately reflected in higher customer satisfaction and loyalty, so that most companies that work with DISKOVER have still been able to achieve increases in turnover today.
When does DISKOVER pay for itself?
The use of DISKOVER generally pays for itself from an average stock value of around € 2.5 to 5 million, i.e. within six months for most medium-sized series and variant manufacturers and wholesalers.
As Abels & Kemmner does not want to combine software house and management consultancy in the long term, it is currently setting up its own sales channel for DISKOVER. On the one hand, DISKOVER will be offered by ERP providers as an OEM scheduling interface and, on the other hand, DISKOVER and the corresponding training courses will also be offered to potential ERP users by a separate company.
IT facts
DISKOVER is programmed in C++ and runs as a client on all Windows platforms. The central database server (e.g. Oracle, MS-SQL and comparable derivatives) communicates with the leading ERP system via a standardized interface. Client and server must be designed according to data volume.
Required data input
Working with DISKOVER requires data that provides information about stock movements. The exact scope of the required data is agreed with the customer as part of the implementation project. Essential, relevant information for processing is included:
Stock issues: The amount of the issue and the corresponding time must be available for all items (either at individual document level or as cumulative monthly values).
Master data: For all items, the item-specific constant information must be included, such as item description, replenishment times, minimum order quantities, purchase prices, etc.
Working with Diskover
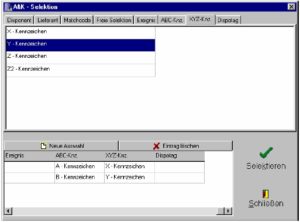
Article selection
Since in practice the articles of certain suppliers are assigned to the dispatcher or in the morning the articles with a current need for action due to falling below the safety stock or the occurrence of a shortage must be processed first, DISKOVER 4 supports the daily workflow with a high degree of freedom in the selection of articles:
Free selection: Item selection criteria in Diskover |
Dispatcher license plate |
Supplier code |
Matchcode |
Free selection |
Events |
ABC indicator (sales significance) |
XYZ indicator (demand behavior) |
Dispotag |
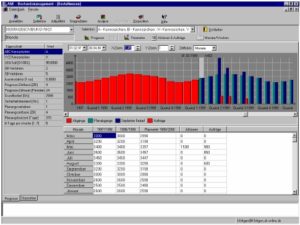
For example, the MRP controller can compile all articles that are assigned to the MRP controller indicator “Müller”, are procured from the supplier “Schmitz” and are also AX or BX articles. The events criterion also allows you to select items that fulfill the “shortage available” or “safety stock not reached” attribute, for example. (see Fig. 3)
Forecast and planning module
Depending on the previously determined demand behavior (ABC/XYZ indicator), the forecasting and planning module offers the appropriate procedures for determining the basic requirement and the safety stock for the planned delivery readiness level. These include classic methods such as the arithmetic mean value, exponential smoothing 1. and 2nd order and also algorithms for determining trend and seasonal factors as part of the determination of basic requirements and, on the other hand, the distribution-free methods already mentioned above for determining basic requirements and safety stock.
The historical movement time series and the planned requirements of an item are displayed both in tabular and graphical form. To assess the planning quality, existing orders for the future are also transferred from the host system and displayed as a cumulative requirement quantity. It is also possible to supplement the forecast planned requirements by manually entering promotions (major projects, sales promotions). (see Fig. 4).
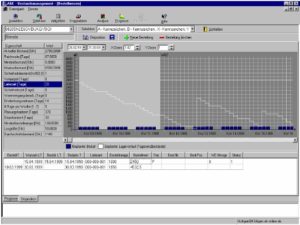
Disposition
In MRP, order proposals are generated for each individual item, taking into account the set MRP procedures and the future requirements determined in the forecast. The functionality for determining the correct order time and the correct order quantity is provided by a dynamic, range-oriented order calculation, which automatically takes into account minimum order quantities and order quantity increments (e.g. packaging unit), and alternative suppliers can also be provided for selection.
The time at which a new order proposal is triggered and the order quantity for the subsequent observation period are recalculated dynamically on a daily basis or with each calculation run. This functionality allows the MRP controller to follow the fluctuations in demand for an item much more precisely and adjust the order quantity accordingly.
The order proposals are then transferred to the host system and converted into purchase orders after being checked and approved by the dispatcher. In addition, various stock and range developments can be simulated by varying the parameters to be specified.
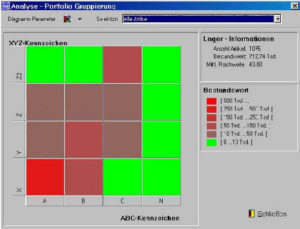
The requirements and the development of stock levels are displayed in a graph on a daily basis (see Fig. 5). The open orders and the newly determined order proposals are entered in a table. As long as they have not yet been converted into orders, order proposals can also be edited, deleted or supplemented with manually entered proposals by the dispatcher at any time.
Portfolio analysis/controlling
The portfolio analysis is a controlling function that enables the MRP controller to regularly examine his range of articles, e.g. with regard to stock levels and stock distribution. It is also possible to analyze sub-spectra by combining portfolio analysis with the item selection described above.
In the portfolio analysis, the selected items are displayed in a three-dimensional matrix structure. Two dimensions are displayed in the screen level, the third dimension is realized by color gradations of the fields. The three axes of this display can be optionally filled with the parameters stock value, range, replacement time, ABC and XYZ indicators. The following graphic (see Fig. 6) shows an example of an ABC/XYZ analysis with output of the stock values on the Z-axis (color coding).
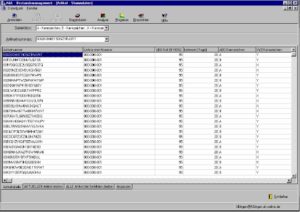
By clicking on one of the matrix fields in the graphic, the affected articles can be displayed and sub-selected for further root cause analysis.
Master data maintenance
DISKOVER offers extensive display and editing options for item master data and item-specific parameters in addition to the scope of services described (see Fig. 7 and 8). Which information is displayed in which order in an article table can be set individually. Other screens offer the option of editing master data fields and parameters for an individual item or for all items in the active item selection.
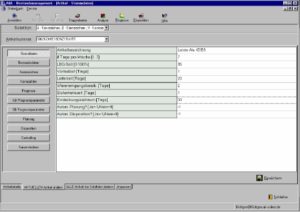
About Abels & Kemmner
Abels & Kemmner GmbH was founded in 1993 by the engineers and economists Dr. Helmut Abels and Dr. Götz-Andreas Kemmner. The company focuses on streamlining value chains (supply chain optimization) for series and variant manufacturers as well as wholesalers. Abels & Kemmner deals with the design and optimization of order processing and logistics from suppliers to customers and from article assortment to IT support. Supply chain concepts that we have developed with our customers have already won two best practice awards. A&K caused a sensation in 1997 when it founded the first virtual company made up of six medium-sized companies from the automotive supply industry.
The second focus is on restructuring and earnings enhancement projects. Here, the consultants develop going concern forecasts as well as restructuring and downsizing concepts and implement these in the companies. Abels & Kemmner has made a name for itself in crisis and turnaround management through the successful restructuring of medium-sized companies. In recent years, the consultants have been involved in the restructuring of the majority of major corporate insolvencies in Saarland.