Project for lean materials management at the market leader for mass spectrometers
By Kurt Künnemann and Bernd Reineke
Thermo Electron GmbH is a high-tech company in Bremen that manufactures mass spectrometers for a wide range of applications. Since the 1990s, the company has concentrated on its core competencies of technology, product development and marketing and has gradually reduced its in-house production depth. However, this measure does not automatically lead to lean internal materials management. The company therefore commissioned supply chain specialist Abels & Kemmner to design new logistics processes and support their implementation.
Short delivery times for customers from research, public institutions and industry also play a key role for highly specialized analysis devices. For this reason, Thermo Electron procured standard components and devices mostly on a customer- and order-neutral basis in order to ensure a high level of delivery readiness at all times. A large number of mechanical and electronic assemblies and countless individual parts were always kept in stock.
Stock reduction of 40 % as a target
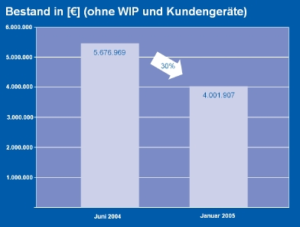
Following the outsourcing of the special workshop and vacuum technology in the 1990s, however, inventories of purchased parts, some of which were high-value and large-volume, did not fall appropriately. For this reason, the management defined the goal of reducing the portfolio values of approx. 5 million by at least 40% to around EUR 3 million. The fact that the new building, which was to be occupied at the beginning of 2005, also required this target from a purely physical point of view, as the storage areas were correspondingly tightly dimensioned during the construction planning phase, created a corresponding pressure to move. The challenge in this project was therefore, on the one hand, to maintain or ideally even increase delivery readiness and, at the same time, to drastically reduce stocks.
Right at the start of the project, it became clear that supplier integration would play a key role in the design of future logistics processes. In particular, they should support and help shape the changeover from the previous push system to the future pull system by taking over the stockpiling of large-volume and high-quality assemblies in particular. However, before the suppliers could be familiarized with the new structure, important preliminary work had to be done. These included:
- Analysis of procurement parts using the ABC and XYZ methods,
- Volume analysis of purchased parts to estimate the required storage volume,
- Analysis of the device structure with regard to multiple part use and the possibility of combining into “delivery kits”,
- Review of purchasing-relevant logistics parameters such as replenishment times, minimum order quantities and price scales.
Simulation tool determines target stock level
At the beginning of the project, the product structures had to be analyzed in detail using the parts lists up to the purchasing component level. The parts lists reflected the structure according to functional assemblies from a design perspective; aspects of assembly and parts usage were given less consideration. All connecting elements such as screws, clamps, washers or nuts were included as individual items and were also procured and stocked individually. The first starting point here was to create “assembly kits”. In terms of the parts list structure, these are therefore assemblies that are procured externally. This significantly reduces the number of individual parts that need to be procured, as well as the work involved in goods receipt and order picking. Other examples of assembly kits are “pump kits” (vacuum pumps, hoses, connections, etc.) or tools for assembling devices at the customer’s premises (e.g. tool bag, screwdrivers, open-end and ring wrenches, ratchets, etc.).
Furthermore, the range of hand bearing parts was reviewed and adapted to current assembly requirements. These are low-value DIN and standard parts that are required for practically every appliance. They are stocked at the assembly workstations and procured purely on the basis of consumption. Compared to other parts, the procurement and provision of hand bearing parts therefore involves very little effort.
Stockpiling strategy
Once the product and parts list structures had been clarified, the stocking strategies for assemblies, assembly kits and individual parts could be decided. This was based on the ABC/XYZ analysis and the results of the volume analysis. The ABC analysis was carried out classically according to purchasing sales or according to production costs in the case of in-house production parts at 80%. (A), 15% (B) and 5% (C) Share of sales. The XYZ analysis is an evaluation of consumption based on the coefficient of variation and provides information on the uniformity of parts consumption. While X and Y parts flow out of the warehouse relatively regularly, Z parts mainly show irregularities in consumption. The more uniform the consumption, the more reliably the components can be planned. This was taken into account accordingly in the tabular analysis (Figure 1).
Class | Planning/disposition | In stock | Delivery |
ABXYZZ2 | Reversal of requirements acc. rolling production plan | no | JIT scheduling agreements with JIT delivery schedules |
C-parts from AB parts suppliers | Reversal of requirements acc. rolling production plan | no | JIT scheduling agreements with JIT delivery schedules |
CXY WBZ<30 days low storage volume | Consumption-controlled with reorder level | yes | Automated ordering |
CXY WBZ>30 days low storage volume | stochastic disposition | yes | Automated ordering |
CXY large-volume | Reversal of requirements acc. rolling production plan | no | JIT scheduling agreements with JIT delivery schedules |
CZZ2 | Needs-based | no | Order |
Figure 1: Stocking by class
As can be seen from the table, it was decided that all A and 13 parts, irrespective of consumption patterns and volumes, will in future be procured on demand and delivered just-in-time (JIT) by the supplier. If a supplier is already a JIT supplier because it delivers A or B parts, all other items from this supplier must also be delivered just in time. Large-volume C-parts are also JIT candidates if they exhibit X or Y consumption behavior. All other low-volume CXY parts must be stockpiled and procured based on consumption.
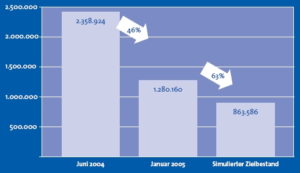
Suppliers included in pull principle
The necessary conversions of the SAP R/3 system were prepared by the SAP specialists at Abels & Kemmner GmbH and carried out in close coordination with the central IT department, which is based at Thermo Electron in the USA¹. The focus was on high transparency of the procurement situation, including traceability down to the individual appliance, as well as the most efficient handling of order and booking processes. For this purpose, the possibilities for simplification and automation contained in the SAP standard were used.
The new processes and interrelationships, in particular the new JIT delivery, were documented and coordinated and trained with internal staff. This means that JIT parts can now be identified in the incoming goods department and transferred directly to the production area, which reserves separate staging areas specifically for upcoming assembly orders, without having to store them. However, coordinating the new processes with the suppliers was also an important step in successfully implementing the project results. To this end, the JIT suppliers were familiarized with the changes in individual meetings and, in particular, the flow of information between the companies was coordinated.
The first fruits of success were already evident at the end of the initial project: the value of the portfolio fell by 46% within seven months. The target stock level determined with the “Diskover” simulation tool from Abels & Kemmner, i.e. the stock of the remaining BOM items, is even more than 60% below the initial value (Fig. 2). The number of active assemblies and components used in parts lists was reduced by 15 % for basic appliances and by 11 % for options, which are modules that can be used according to customer requirements.
The move at the turn of the year and the associated changes were completed within a very short space of time. The new processes are currently being fine-tuned and consolidated.
The integration of suppliers into the pull principle proved to be unproblematic due to the focus on A and B parts with XY behavior. In addition, the assembled kits provide Thermo Electron with a simplified procedure for the internal provisioning processes, which was readily accepted (Fig. 3). For suppliers, the changes mean higher sales potential and stronger customer loyalty, which has a positive effect on planning and investment security. Thermo Elektron ultimately benefits from increasing liquidity, as significantly less capital is tied up in portfolio assets. In this respect, everyone involved can benefit from the new JIT concept. The next steps are to further reduce inventories and at the same time increase delivery readiness by using forecast-based scheduling processes. The optimum forecasting methods and process parameters are determined using Abels & Kemmner’s simulation tools and transferred to the SAP system.