Market-synchronized production in the watch industry
By Gervaise Voisard, Olaf Rellecke and Dr. Götz-Andreas Kemmner1
Producing and procuring in sync with market requirements makes sense. But how do you build market-synchronized process chains when there are very long delivery times on the procurement side? In a project at Swiss watch manufacturer Montblanc-Montre S.A., Abels & Kemmner reduced stocks by an average of 19% – despite long delivery times.
Montblanc-Montre S.A., based in the watchmaking mecca of Le Locle in the Swiss Jura, is a subsidiary of the Montblanc Group in Hamburg and belongs to the Swiss luxury goods group Richemont in Geneva. Montblanc-Montre manufactures high-quality Montblanc brand watches, which are sold in Montblanc boutiques worldwide and through selected retailers. Founded in 1997, the company has experienced rapid growth in recent years and now produces over 100,000 classic mechanical watches a year.
The watch industry – a special sector
The watch industry has a high proportion of purchased parts that are produced by specialized medium-sized suppliers. Not only movement components, but also dials, cases and hands are highly complex precision mechanical parts that are manufactured in many complex production steps, often from special metal alloys and unusual special materials. Delivery times of three months are already considered fast, and it is not unusual for nine to over twelve months to pass between ordering from the supplier and delivery of the parts.
High quality requirements for the procured components and careful quality checks continue to mean that a significant but fluctuating proportion of the delivery quantities are rejected by quality management and therefore cannot be installed in urgently needed watches. Another characteristic feature of the watch industry is the high annual proportion of new products, which typically accounts for 25% to 35% of a watch collection.
These are all boundary conditions that lead to high stocks of finished goods and still have a negative impact on the ability to deliver finished watches. This is an initial situation in which a market-synchronized value chain is not usually discussed.
Basic principle of two-stage replenishment
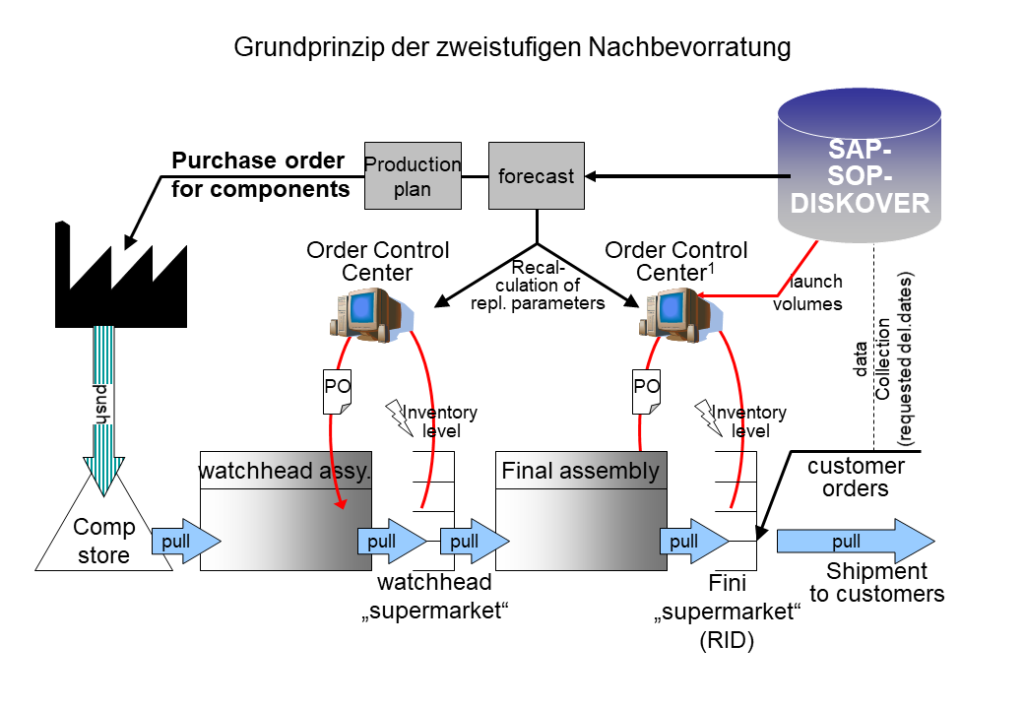
Prerequisite: Demand forecast
If the parts that the company has to install today had to be ordered six months ago, nothing works without a careful sales forecast, regardless of whether you want to produce in line with the market or not.
As a subsidiary of Montblanc in Hamburg, Montblanc-Montre also uses SAP and is integrated into the global sales planning process of the Montblanc Group, which was designed and implemented together with A&K several years ago. This was a necessary, if not sufficient, condition for thinking about market-synchronous production at all. However, even the best sales planning cannot completely prevent actual market demand from deviating from the forecast, deliveries arriving late or partial deliveries not meeting the required quality. Ultimately, not all components that are needed for a particular production requirement are regularly available, or they have been installed in the wrong finished watches that are not currently in demand, thus increasing stock levels and reducing the ability to deliver.
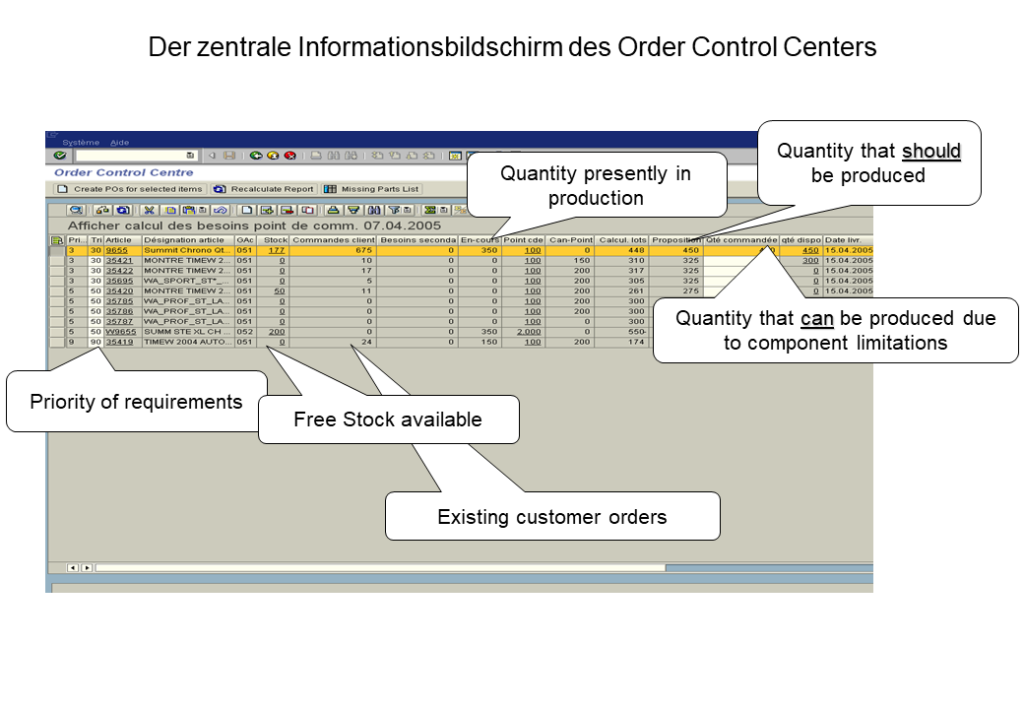
Basic principle: Two-stage control loops
In order to fundamentally and sustainably improve this situation, A&K, together with a project team from Montblanc-Montre and Montblanc-Simplo in Hamburg, developed a so-called “Postponed Manufacturing Concept” with a two-stage control loop, the internal stages of which have now been implemented. Supplier integration follows in further stages. Internal restructuring alone reduced inventories by an average of 19% despite the existing problems.
The entire manufacturing process was divided into two replenishment control loops: The finished goods warehouse is now supplied with the finished watches via just-in-time final assembly. This final assembly uses pre-assembled watches to which only the bracelets need to be attached. As a large number of finished watches differ only in the different leather, textile and metal bracelets, it was possible in this way to move the creation of variants downstream towards the customer delta, which means that significantly lower stocks of finished watches have to be held in the finished goods warehouse. The ideal situation would even be to move assembly directly to the point of sale. However, a number of quality restrictions currently prevent this assembly step from being dispensed with.
Based on the positioning of the finished watches in an ABC-XYZ portfolio2 , criteria were defined as to which watches should be kept in the finished goods warehouse and which watches should be produced at short notice via JIT final assembly if required.
Instead of classic Kanban: Order Control Center
It was clear from the outset that a classic Kanban system for controlling the two replenishment loops was out of the question. A classic Kanban system presupposes that the components from which a control loop draws are available in the supermarkets – at least for the most part. Before carrying out an upcoming kanban, it would have to be checked whether the required components are available in sufficient quantities in the supermarket. If a component is missing completely, the order cannot be started. If a subset of one or more components is missing, only a subset of the collective kanban can be fulfilled. If the undercovered components are included in several pending collective kanbans, a decision must be made on the priority of the component allocation. A classic Kanban system is completely overwhelmed by such a situation.
In order to solve this problem elegantly and efficiently, ABAP programming (Advanced Business Application Programming; programming language for SAP) was carried out on the existing SAP system. The new SAP module “Order Control Center (OCC)” now helps to control replenishment loops. The control loops themselves are re-dimensioned monthly by a second SAP ABAP, the “Replenishment Parameter Calculation (RPC) module”.
What is to be produced in the two replenishment loops is controlled via reorder points in the supermarkets that are supplied by the two loops.
All pending production requirements for watch heads and finished watches are listed on the OCC’s central control screen and sorted according to various defined priority criteria. However, this order sequence can be overridden by the dispatcher.
For each pending order, the OCC shows what quantity would have to be produced and what quantity can be produced. When determining the quantity of a part to be produced, the OCC not only takes into account the shortfall of a reorder point, but also takes into account pending customer orders that exceed the replenishment quantity of the reorder point control. For new products, the OCC specifies exactly the initial production quantity defined by marketing as the system filling. The actual production batch size that can be manufactured depends on the lowest available component. The OCC assigns the available component stocks to the pending replenishment orders in the order of order priority. This ensures that the “most important” orders are supplied with the required components first. This quantity allocation can also be overridden by the operator, who can thus incorporate further information not known to the system into the component allocation. The consequences of a changed allocation of component quantities are displayed to the operator directly in the dialog.
From the central screen of the OCC, the MRP controller can jump directly to the conversion of the requirement request (BANF) into a production order or an external order. The two alternatives are necessary because some of the watches (excluding bracelets) are produced by an external contract manufacturer. In this way, production capacity is adapted to the strong seasonality and there is no need for extensive pre-production during the low seasonal periods.
Only when the operator triggers the automatic generation of a BANF and its subsequent conversion are component stocks definitively assigned to the production orders. The OCC does not make any material reservations for the future. This ensures that the OCC compares the current demand situation with the current supply situation for components at every start.
The replenishment parameter calculation module dimensions the control loops on a monthly basis
The strong seasonal fluctuations in market demand make it necessary to re-dimension the reorder points of the replenishment loops on a monthly, item-specific basis. This task is performed by a second ABAP called RPC module (replenishment parameter calculation). The RPC module accesses the demand forecasts for the individual finished watches determined as part of sales planning and calculates four control parameters for each finished watch: a target production lot size, as well as a must, can and max point. The max point indicates the maximum stock level up to which the stock may be replenished. Required stock is the stock that must be replenished at the latest. This mandatory stock practically corresponds to the red area of a classic traffic light kanban control system. Just as in the traffic light Kanban there is a yellow area which, when reached, may be reworked but does not have to be reworked, the RPC module calculates an optional stock with the same meaning.
Once the OCC has mathematically supplied all production requirements that have been triggered by falling below the mandatory point with components, it allocates the remaining available component stocks to the optional production requirements.
One fifth less finished goods inventories – and we’ve only just begun
The two-stage replenishment concept, controlled by the Order Control Center (OCC) and the Replenishment Parameter Calculation (RPC), has significantly reduced the management effort in the company. In order to recognize the development of stocks, it is necessary to compare the former stocks of finished goods with the current stocks of finished watches and watches (excluding bracelets). Due to the strong seasonality, it is also necessary to compare 12-month moving averages. After one year in operation, this results in a 19% reduction in inventories.
At present, components are still ordered from suppliers by deriving requirements from medium and, in some cases, long-term sales planning, with suitable, specially calculated safety stocks that statistically evaluate and absorb forecast uncertainty and delivery uncertainties.
Concepts on how delivery times can be shortened in future and how suppliers can be integrated into the pulling system are available and are now to be implemented in the next stage of the project.
1 Ms. Gervaise Voisard is Logistics Manager at Montblanc-Montre, Le Locle, Switzerland. Olaf Rellecke is now Manager Finance and Services in the same company and was Supply Chain Manager for Montblanc’s watch division at the time the project was carried out. Dr. Götz-Andreas Kemmner is Managing Director of Abels & Kemmner GmbH, Herzogenrath/Aachen
2 The ABC classification classifies products according to their importance for sales, while the XYZ classification assesses the predictability of products based on statistical parameters.