Key figure system helps to monitor material planning
Dr. Bernd Reineke
The project to optimize material planning has been completed. Methods, master data and parameters are set. The target stocks are defined. However, it is not uncommon for optimization targets not to be achieved. Why is that? With a suitably tailored system of key figures, companies can quickly identify the causes.
Typical supply chain (SC) projects, such as those carried out or supported by the management consultancy Abels & Kemmner, usually result in fundamental changes to the planning and scheduling processes and their parameters. Sustainable solutions are characterized in particular by the fact that the scheduling procedures and parameters used are constantly updated to take account of changes in demand for products and materials. But this measure alone is not enough, as the stocks do not “automatically” reach the target values, ranges or stock turnover. Without consistent application of the new parameters, no sustainable reduction in stocks can be achieved.
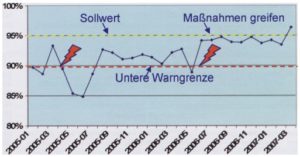
In practice, however, this application fails time and again for the following reasons: The dispatcher often does not adapt his working methods to the new requirements, which leads to deviations from the calculated targets. And even if training measures have been carried out, the dispatchers are often overwhelmed by the multitude of new procedures on a day-to-day basis. There is also often still a certain mistrust of the new procedure, which can lead to orders being placed earlier and/or more. As a result, unnecessary inventories are built up and the identified potential remains unused.
However, the failure to achieve the targets is not only due to the dispatchers, but also to the fact that the corresponding software support is not available. Recognizing and exploiting all the potential of hundreds or several thousand articles per MRP controller for each individual item is not possible without the appropriate tools. It is therefore advisable to develop and implement a key performance indicator system tailored to the area to be optimized at the same time as an SC project.
However, this does not involve regular evaluations such as monthly inventory reports from Controlling. Instead, a monitoring system should be set up that recognizes any short-term deviations and reacts to them independently as required. For this purpose, actual values must be compared with target values for each scheduling-relevant process. Permissible deviations must be specified in advance as a corridor – with upper and lower limits (Fig.). When leaving this corridor, a message is generated that is ideally delivered directly to a predefined group of recipients.
With the possibilities offered by today’s information technologies, messages with case-based predefined texts can be forwarded online in “real time” according to urgency or relevance, e.g. by e-mail, SMS or workflow datasheet.
One of the most common scheduling errors is ordering goods too early: the MRP controller has all order proposals displayed within the opening horizon, which is usually freely selected by him. If this period is set too long, he receives a long list of order proposals or planned orders. Several suggestions for an article are then often quickly summarized and ordered. Further items are ordered, although this would not be necessary until later. The result is that the range of stocks increases around this time, which is ordered too early.
In this case, a monitoring system must be set up that ideally limits the order proposals to an agreed, minimum required opening horizon on a daily basis and compares them with the new orders or production orders. If there are discrepancies between the order proposals and actual orders or production orders in terms of date or quantity, an alarm is triggered and a previously defined distribution group is notified.
Another mistake lies in the “love of smooth numbers” that many dispatchers have developed over time. This is expressed by the fact that the amount is often rounded up. In this way, seven pieces quickly become ten, or 83 become 100. Quantities are often rounded up to packaging units or transport units and 26 pallets suddenly become 32 pallets because they just fit on the truck. If it is actually necessary to round up order quantities, e.g. to packaging or transport units, this must be stored in the master data of the ordering system. However, if the master data is correct and rounding up is nevertheless carried out without authorization, this has unintended consequences that increase the inventory.
In this case, the monitoring system compares the demand with the order quantities and issues an alarm if the required quantities in the orders or production orders are exceeded.
Another important key figure is readiness to deliver. It can also be monitored using a suitable monitoring system, with deviations from the target delivery readiness corridor directly triggering an alarm. In this way, it is possible to check immediately how the deviation occurred and what measures need to be taken in response.
To set up the monitoring, the key figures to be collected must be determined based on the project objectives – e.g. inventory reduction and delivery capability.
The second step is for the project team to determine target figures for the KPIs and define the target corridor (as with a process control chart). It is important to present these targets to those involved and the management and have them approved accordingly so that there is consensus on the target values.
The next step is to collect these key figures, which can be automated by using a suitable software tool. It is important to collect the key figures regularly right from the start of the project in order to be able to prove the project’s success with reliable figures later on. The definition of the survey rhythms is also part of this.
The fourth step involves the implementation and application of monitoring, i.e. the systems generally determine the key figures on a daily basis and sound the alarm in the event of deviations. To avoid receiving too many exception reports at the start of monitoring, it is advisable to limit the reports to A articles or a specific article group (pilot articles), for example. Once the processes and settings for these articles have been consolidated, further articles can be added until the entire range of articles is subjected to monitoring.
As it would generally be too time-consuming and costly to implement the KPI system in the customer’s ERP system or data warehouse at the start of the project, Abels & Kemmner uses the project-supporting software tool “AK-Toolbox”, which can be adapted to specific customer requirements with just a few parameterizations and delivers the reports directly to the screens of those responsible by e-mail.
The use of the KPI system serves as a preventative measure to ensure that the forecast reduction in inventories and increase in delivery readiness is achieved in the long term. However, if the pre-defined tolerance corridor is deliberately exceeded and this is documented accordingly, reliable reasons for not achieving the forecast potential can also be determined, which can be reflected on a cyclical basis. This often results in new starting points for exploiting new potential.
Procedure for setting up a monitoring system
- Definition of key figures
- Align with the project goals
- Consider opposing goals (e.g. inventory and delivery readiness) equally
- Check availability of the necessary data and supplement if necessary
- Determining the value limits and collection rhythms
- Analysis of key figures and calculation of permissible tolerances
- Derive value limits
- Determine sensible survey rhythms
- Coordinate key figures and value limits with those involved
- Realize and automate the collection of key figures
- Setting up the monitoring system in the ERP system, data warehouse or with additional software
- Time or event-driven collection of key figures
- Realize the delivery of messages from the monitoring (e.g. e-mail, workflow, SMS, …)
- Implementation and commissioning of the monitoring system
- Implementing macros, reports and, if necessary, software
- Setting up the group of addressees for each deviation
- Initially restrict to a pilot area to test functionality and gain experience