DISKOVER SCO in use at Mehler Texnologies: Not just a tool, but a sharp weapon against inventories
By Ralf Schechowiz, Lothar Szymkowiak (Mehler Texnologies) and Dr. Bernd Reineke1
Thanks to the high level of transparency provided by DISKOVER SCO, Mehler Texnologies can now influence logistics parameters in a much more targeted manner in order to improve delivery readiness, reduce stocks in the long term and minimize scheduling costs. However, before the new DISKOVER SCO scheduling software, which the schedulers do not regard as a simple tool but as a “sharp weapon against stocks”, could be activated, some preliminary work had to be carried out.
The specialist for coated technical fabrics’ initial aim was to reduce stock levels and improve delivery readiness at the same time. This posed major challenges for everyone involved: In the past, procurement and production across several locations was only planned and managed on the basis of rudimentary sales figures. One reason for this is that the plant-intensive production steps were anything but flexible. The focus of the production sites has also traditionally been on plant capacity utilization and therefore at the highest possible output. As is well known, these are restrictions that drive the company’s existence and are often considered irrevocable.
The specialist for coated fabrics and technical textiles serves eight product areas, including sun protection.
Lack of IT functionalities
To make matters worse, planning and scheduling were only rudimentarily supported by IT systems. Due to the lack of usable sales figures from the sales department, the planning department therefore had to make its own considerations regarding sales expectations. Without appropriate IT support, however, the experience and gut feeling of the dispatchers remain the only sources for estimating sales expectations. It is therefore only understandable that securities are built in at one point or another, which ultimately result in excessively high inventories. An additional inventory driver is the lack of inventory transparency at the individual production stages within the company itself, as here too the gut feeling factor has to be used. The management therefore wanted to make a change and commissioned Abels & Kemmner GmbH to carry out an analysis to assess the potential for reducing inventories.
What is feasible?
In a first preparatory step, a standardized overstock analysis was carried out. The result of this analysis – which is quick and somewhat imprecise due to standardization – showed a clear inventory reduction potential of around 15% to 20%. A short-term additional sensitivity analysis showed even greater potential if production were to succeed in significantly reducing throughput times from three months to one month. Based on these two analyses, the project team decided to first address the potential with the help of planning and methodical improvement measures. In the next step, the production restrictions should then be checked and optimized if necessary. These included, among other things
- Depending on the fabric, the weaving mills retool for several days.
- During finishing, identical colors/coatings are combined and produced rhythmically in campaigns.
- This results in dynamic replenishment times of up to several weeks, depending on whether a color has just been run or is about to go into production.
- The goods produced are assessed after completion, as not every quality can be used for every end product. This means that there may not be enough goods of a certain quality from one batch.
It became clear early on during the first standardized overstock analyses that the predicted results could only be achieved with a great deal of effort in the existing IT environment. The management therefore decided to implement the SCM optimization tool DISKOVER SCO from SCT Supply Chain Technologies GmbH during the project. This decision enabled several synergy effects to be exploited at the same time:
- Rapid implementation of project results with prototypical mapping in DISKOVER SCO
- Optimum learning effect through rapid familiarization with the future tool
- Flexible mapping of logistical parameters, rules and agreements
- Recognize the direct effects of changed parameters
Abels & Kemmner’s proven approach was chosen to achieve the goals set:
- Item classification with the ABC/XYZ analysis
- Definition of stockpiling strategies
- Mapping the production restrictions in the simulation models
- Defining the planning and scheduling framework parameters
- Determination of the optimum, item-specific settings
ABC/XYZ analysis uncovers stock drivers
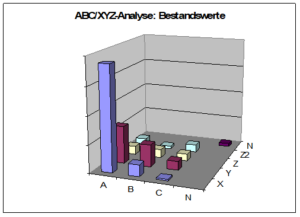
The results of the ABC/XYZ analysis clearly showed where the inventory drivers were: On the one hand, AX and AY articles were highly stocked, which was in line with the objective of the replenishment, namely to have a high level of availability in the top-selling products. Furthermore, the very sporadic items CZ2 appeared to be clearly overstocked, which indicated an unsuitable stocking strategy from a logistical point of view or an unfavorable product range policy.
After the ABC/XYZ analysis, the project team determined the simulation scenarios with the logistical parameters (see table). In the DISKOVER simulation, a period in the past is simulated in terms of planning and scheduling, but with different logistical settings and methods. The simulation result can then be compared with the actual values achieved so that the advantages and disadvantages of changed settings can be assessed. The simulation results are checked and evaluated using an iterative procedure in order to subsequently make modifications to the settings to optimize the results.
Traditionally, the actual settings are first taken from the planning system and simulated with various degrees of readiness to deliver in order to obtain an initial indication of possible potential. In many cases, however, the setting values cannot be adopted one-to-one because either the data quality is not right or the restrictions from production and logistics are not reflected in them. Particularly in the case of complex production processes, this usually has to be worked out by the project team and mapped in parameters. This is also the case here, where the technical fabrics are coated in a specific, color-dependent sequence. Furthermore, the cycle in which individual products are manufactured had to be determined. This has an influence, for example, on the replenishment times and minimum lot sizes to be set.
Stockpiling strategies in the event of production restrictions
At Mehler Texnologies, the production restrictions had a significant impact on the achievable average inventories and delivery readiness levels. An overview of the trends in the parameters is shown in Figure 2. This lists the modes of action, which parameters tend to influence which target values.
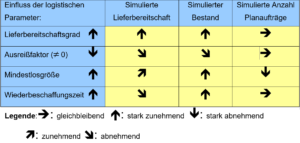
The specific effects for Mehler Texnologies were analyzed in detail as part of the project. As the restrictions on production could not be influenced within the scope of this project, the definition of the stockpiling strategy for the products was a key influencing factor. The project team initially determined which products should be stocked and which should not, i.e. which could be procured for specific customer orders. The latter were in particular articles that were only called up sporadically or rarely by customers. However, exceptions to this are all catalog items that can generally be delivered at short notice and must therefore be stocked. Furthermore, items that can be produced at short notice by cutting from stored basic items should not be kept in stock. This decision has already resulted in an inventory reduction potential of more than 20% of the finished goods inventory.
In the treatment of the remaining items in stock, the main variable that could be influenced was the target delivery readiness with which the products should be available from stock. Two key aspects were taken into account when determining the target delivery readiness:
1. the XYZ feature
The more irregular the demand for an item, the higher the safety stock level must be in order to achieve a high level of availability. The correct safety stock is significantly lower for items that are in regular demand (X and Y items). Therefore, the regular items should achieve a higher readiness for delivery, while compromises were possible here for the irregular items.
2. the product group (market influence)
Depending on the product group, different target markets or customer groups are supplied, which have different requirements in terms of delivery readiness. The automotive industry, for example, has significantly higher requirements than the construction industry. The product groups were therefore categorized into three different delivery readiness categories (high, medium, low).
With these two influencing variables, a set of rules could be mapped that determines the delivery readiness levels to be set (see Figure 3). First, the product group and the target delivery readiness category (high – medium – low) are determined for each material. The XYZ characteristic is then used to determine the target readiness for delivery according to the table below.
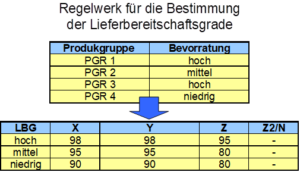
These settings, which were developed in several steps, also resulted in a significant stock reduction potential of almost 10% for the items in stock.
The calculated total potential is shown in Figure 4.
Implementation and experience
As mentioned at the beginning, the results were implemented using the DISKOVER SCO optimization tool from SCT GmbH, which was also used to carry out all the analyses accompanying the project. The initial prototype implementation of the system served to evaluate the software in terms of functionality and usability. During this phase, the users got to know the software. Through further training and subsequent coaching sessions, the users gained confidence in the results and very quickly learned to use the advantages of the system. The actual task of planning and scheduling calculations is now performed by the system. Dispatchers can change and optimize the results by specifically influencing the parameters. A key finding for the dispatchers was the fact that “the right goods are finally in the warehouse. In the past, production capacities were utilized with articles and stocks were built up that are no longer produced from today’s perspective. Incorrect decisions are avoided thanks to the availability of the relevant planning parameters,” says Ralf Schechowiz, CFO at Mehler Texnologies. However, users also point out the need for qualification when using the system: “DISKOVER is like a weapon against stocks, it should be operated by specially trained specialists,” says Lothar Szymkowiak, Head of Scheduling at Mehler Texnologies. DISKOVER regularly monitors whether the key figures remain within the permitted corridor to ensure that problems do not occur even in the event of operating errors. If limit values are exceeded or not reached, an alarm is triggered with automatic notification of the responsible planners and dispatchers.
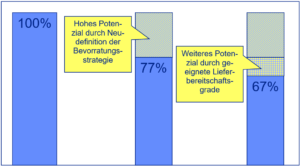
DISKOVER SCO is now a permanent fixture in the planning and procurement process at Mehler Texnologies. Another function of DISKOVER SCO was an additional benefit for planners and dispatchers: The capacity module enables production bottlenecks to be recognized in the future. With the appropriate settings, these bottlenecks can be automatically balanced by DISKOVER shifting production orders to times when free capacity is still available. “We are now finally able to take company vacations at our production sites into account during planning and scheduling. When the operating calendars are changed, changes to the planning are automatically suggested,” says a delighted Lothar Szymkowiak.
About Mehler Texnologies
Mehler Texnologies is one of the leading international companies in the coated fabrics market. Over 50 million square meters of material are produced and sold annually under the VALMEX®, POLYMAR® and AIRTEX® brands. Customers are companies in the processing industry. Over 60 years of development and production experience form the basis for sophisticated products. Ongoing research and development improves existing composite materials and opens up new areas of application. State-of-the-art machinery ensures the high and consistent quality of the products.
The lively dialog with planners, producers and fabricators from a wide range of sectors and industries is evidence of close and trusting cooperation.
The technical textiles are divided into eight product groups:
- Planning
- Textile construction
- Sun protection
- Boat & Pool
- Sport & Camping
- Industry Environment
All technical textiles are based on carrier fabrics that are produced in the company’s own weaving mills. Depending on the application, the coatings are composed of several components. The result is high-quality fabrics and high-tech products that are used in almost all industries worldwide.
Production takes place at two locations in Germany and one in the Czech Republic. Sales companies in Italy, France, the UK, Poland, Latvia, Romania, Turkey and the USA as well as sales partners in other European countries, Asia and Australia serve customers in over 80 countries.
1 Ralf Schechowiz is CFO and Lothar Szymkowiak is Head of Finished Goods Planning at Mehler Texnologies GmbH in Hückelhoven. Dr. Bernd Reineke is Managing Director of A&K.