Fine-tuning the production
Montblanc relies on electronic planning boards to cope with changing bottlenecks in the complex production of precious metal spring assemblies, which are manufactured in more than 35 production steps and in a wide range of variants.
Delivering on time is a real challenge for the production management of the writing instrument manufacturer Montblanc from Hamburg. Due to the increased product range in recent years, the complex, multi-stage production process must be monitored and controlled with a sharp pen. For this reason, an electronic production control and order tracking system was programmed for the spring units, which are manufactured exclusively by hand, and installed on 42 large electronic planning boards in the spring production area. The enthusiasm of the employees was palpable from day one. In addition to the transparency gained and the associated opportunity to optimize employee deployment at the many different production stations, the optimized flow production with shorter idle times and lower WIP (work in progress) inventory also contributed to this.
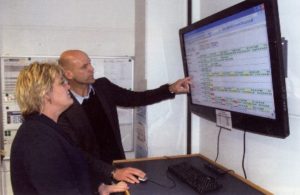
The production process
The 14 and 18 carat gold nibs wait in polystyrene trays to be used at the tip of the fountain pen in the final assembly of the writing instruments. Before they get there, however, they have undergone a time-consuming and labor-intensive production process involving over 35 steps. If you consider this complexity, it quickly becomes clear that optimizing employee deployment in terms of lead time compliance, low WIP inventory and production efficiency is a major challenge for production management at Goldfedermanufaktur. In flow production, not every spring unit passes through the same production stations. Each work step has different processing times, not all production stations are permanently occupied. Despite the high level of employee qualification, not everyone can carry out all operations. And finally, the capacity limits must be taken into account.
Operational planning
Each bottleneck sector limits the overall throughput and at the same time creates a waste of resources for all other parts or orders. The entire operational planning must therefore be constantly realigned to the short-term changes in bottlenecks. The alternating weakest sub-area therefore always determines operational planning in order to align the overall system for maximum efficiency. The actual production situation must be visible at all times, not only for production control but especially for the employees in the production areas who are organized in groups. In this case, transparency means answering the following questions:
- How high is the total production order backlog?
- How high is the order backlog at each individual production station?
- How many different production orders does it consist of?
- Which of these orders are due when?
- Which of these orders are already on ‘yellow’ or ‘red’ in the traffic light circuit?
- Which of these orders have been given ‘additional’ priority?
These questions are answered by the electronic planning board in real time.
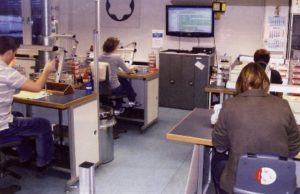
The electronic planning board
The first step at Montblanc was to test a manual planning board in one of the three production areas. Although this brought the desired success, it was too time-consuming to manage in terms of placement, operation and updating due to the high number of production orders and production stations. Based on this experience, the electronic planning board was programmed and implemented in just a few days. Behind the graphical user interface is an SQL database model in which the SAP production orders are updated daily. The user interface of the planning board is structured as comprehensibly as Kanban and concentrates on the essentials: creating transparency by visualizing the production orders waiting in front of the production stations. It also provides information on traffic light status, volume and completion date. Each employee operates the electronic planning board themselves. Once the employee has completed his operation, he goes to the electronic planning board and clocks his production order one operation further. This reduces the quantity of his operation and the subsequent operation is loaded. Employee scheduling of the production groups is carried out daily, several times if necessary. The production orders and production order quantities that precede an operation are decisive for operational planning, in addition to the traffic light system and the additional priority indicators. The time-consuming task of gaining an overview of all production stations in terms of quantities, deadlines and priorities has been completely eliminated thanks to the use of electronic planning boards. At the same time, flow production was optimized, with shorter idle times and lower WIP inventory. This example shows that even the most complex production processes can be controlled in a bottleneck-oriented manner using appropriate planning methods and tools without generating enormous planning effort and IT costs. A clear view at all levels is important for the bottleneck-oriented fine-tuning of production. Data from the store floor in real time and a focus on the essentials in visualization are now an open secret at the Montblanc factory.
Authors:
Frank Derlien is Head of Spring Production and Carsten Hense is Head of Production at Montblanc Simplo GmbH in Hamburg.
Andreas Gillessen is a management consultant at Abels & Kemmner in Herzogenrath.