Incorrect inventory planning not only leads to high warehousing costs, but also to shortages in delivery readiness due to stock shortages. The fittings manufacturer Hansa has successfully reorganized its processes and achieved sustainable improvement effects.
An initial scan of the planning and scheduling processes at Hansa Metallwerke AG showed that there was significant potential for optimization in the areas of demand forecasting, material planning, shading and production/order processing. The scan was based on intensive work with checklists from Abels & Kemmner GmbH, Herzogenrath, which can be modularly adapted to the respective company to be examined. The less than optimal state of development of the supply chain processes, measured against current best practice, was an initial indicator that significant logistical improvements could be expected through suitable measures in the areas of system support, planning and scheduling processes and the procedures used
In addition, an initial overstock analysis for finished goods, merchandise and purchased parts was carried out as part of a potential study. The inventory reduction potential was between 18 and 40 percent and could be realized in the first six months. The total inventory reduction potential for finished goods and semi-finished products was over 50% in some cases.
The first main project phase
In the first main project phase, the planning and scheduling processes for the various material types were recorded in detail, the existing IT support was examined and plant and warehouse structures were recorded in the existing system. At the same time, portfolio driver workshops were held with the various specialist departments, which led to further findings.
Purchasing tended towards price optimization via quantity. New products are subject to a long design process. However, milestones for the handover to the production phase were not set, which often resulted in time-critical decision-making at the end with a fixed end date. One of the consequences of this was that the initial stock levels for new products were set too high because there was no time to carry out suitable analyses.
The innovative spirit of the developers led to frequent technical changes, which unnecessarily increased the number of variants and led to high stock levels, especially for the spare parts business.
During the discontinuation process, residual quantities from framework agreements were found that were keeping inventories unnecessarily high due to a lack of communication of residual purchase obligations. Due to the lack of active control, stock levels sometimes fell below minimum levels, resulting in new orders. The comparatively poor delivery reliability of suppliers was not actively addressed due to a lack of resources. Alternatively, it was easier to increase the safety stocks.
Assortment constraints for accessories were generally supported and stocked ready for delivery as a finished assembly kit, but without examining alternative supply chain models at previous stages of the value chain in order to avoid expensive inventories including in-house value creation.
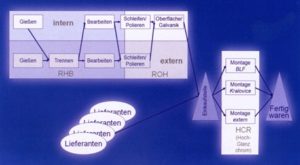
The second phase
In the second main project phase, a concept for the sustainable reduction of finished goods and purchasing inventories was developed. In addition to article structuring according to ABC and XYZ codes, various sensitivity analyses were carried out in the form of simulations.
These analyses showed which logistical variables, such as target delivery readiness, replenishment times or batch sizes, influence the inventory situation and to what extent. Based on this, all parameters for optimizing the value streams were determined using dynamic simulation. The detailed analysis of the existing IT support as well as the planning methods and processes revealed weaknesses in some areas that could be sustainably resolved by the concept to be implemented.
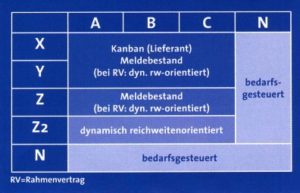
Processes optimized
The inadequate system support made it necessary to investigate the need for external forecasting and scheduling optimization. In future, Hansa will now be using the “Diskover SCO” software from SCT (Supply Chain Technologies). Diskover receives all planning-relevant data from the ERP system via a transfer table, which is then processed by the solution using simulation to optimize the processes and parameters as well as for planning and scheduling, right through to the order proposal or production order proposal. The optimized procurement elements generated in this way are then returned to the ERP system for operational implementation.
In addition, a standardized planning model and a clear demarcation of the planning levels and their tasks (sales, production planning/disposition, production control) were introduced. Sales planning incl. The planning process, which takes into account trend and seasonal effects, is system-supported using the latest planning methods, and the treatment of new and discontinued products is also clearly regulated. The calculation of optimal reorder points and safety stocks is now carried out throughout the system.
Disposition becomes active when there is a need for action, i.e. when replenishment is required. Manual planning activities are replaced by optimized automatic processes. Each item is automatically adjusted on a rolling monthly basis according to its consumption characteristics and its current life cycle position in terms of planning and scheduling. How this is to be done is stored in the software in the scheduling rules. The stock and supply situation is transparent at all times and planning deviations are immediately displayed to the dispatcher via alerts and reports. The entire planning process is less time-consuming and significantly less prone to errors.
There are clear business rules on how to work in planning and scheduling/production control. The variety of order and priority lists has come to an end. Unnecessary production advances no longer take place, as they build up superfluous stocks, consume input material for parts that are used several times and may be needed elsewhere, and use up production capacity at the bottleneck. The stocks are transparent, so that multiple allocations can no longer occur, as the available quantity is reduced when the planner schedules a production order.
Conclusion
As part of this project, Hansa Metallwerke AG has consistently pursued and achieved the implementation of integrated planning. After around a year, it can be stated that the significantly increased transparency of the planning and inventory situation improves the ability to act and the quality of planning decisions. The use of Diskover SCO makes it possible to optimize the planning and scheduling of each individual item with system support. Since the start of the project, the inventory required for this has been reduced by around 30 percent and delivery readiness has already improved. The project has also set in motion a development that promises high performance at minimum cost for the requirements of the future. As a result, the company is well positioned not only to overcome the current economic crisis, but also to be able to operate in line with requirements and, above all, without any inventory problems when the economy picks up again.
Hansa Metallwerke
Founded in 1911 by a predecessor company in Stuttgart, Hansa Metallwerke AG has been producing sanitary fittings since 1950. Hansa offers a varied portfolio of innovative bathroom and kitchen fittings as well as shower and shower systems. The company manufactures products from the entire range at its Burglengenfeld site. Sales are split roughly equally between the domestic and foreign markets, with 50 percent each. In 2008, the globally represented Hansa Group achieved a turnover of just under 220 million euros. The number of employees is 1,150.
Authors: Steffen Trautwein, Head of Supply Chain Management, Hansa Metallwerke AG, Stuttgart and Armin Klüttgen, Senior Consultant, Abels & Kemmner GmbH, Herzogenrath.