Bernd Reineke
Disposition is a highly complex task. Mastering the large number of parameters and their dependencies is a major challenge in order to avoid inconsistent stocks and poor delivery performance. A good concept is therefore needed to support scheduling and master data maintenance.
What do we actually expect of our dispatchers? For example, if we only look at the usual master data views for MRP, there are around 60 master data fields to maintain for each item. Added to this is the master data for work preparation, forecasts, info records, order books and, and, and… Depending on the number of articles and selected functionalities, the classic dispatcher has to keep between 100,000 and one million master data items up to date.
A dispatcher has more data to maintain than he has working minutes available per year! And that’s just the quantitative view. At the same time, we demand that they also make the right quality entries and thus make the right choice every day. Anyone who has taken a closer look at scheduling knows that this is a highly complex task: many parameters are interdependent and mutually dependent. This inevitably leads to excessive demands due to the mass of data. What do people do in such situations? It simplifies the task. It is therefore not surprising that most companies only use a few planning and scheduling alternatives.
In order not to attract unpleasant attention – for example through annoying stock-out situations – he creates mechanisms that lead to a perceived better result: He builds up certainties. For example, safety stocks are set or target figures are increased, which should guarantee delivery readiness even during peak demand. Minimum batch sizes are increased and longer delivery times are introduced with the same aim. Not immediately obvious to everyone, lead times are also very popular, which ultimately have the same effect as premature stockpiling.
We like to blame the dispatchers for inconsistent stocks and poor delivery performance. But that’s too easy! Rather, it is a lack of concepts and a lack of support in scheduling and master data maintenance that lead to the misery. But that doesn’t have to be the case! If you follow our 8-point program, you will get your parameters under control and save valuable resources.
1. classify your articles
The classification serves to reduce complexity in planning and scheduling. Form classes and make decisions on how to set up the individual classes sensibly. The following classification criteria can be used: the life cycle indicator, the ABC/XYZ characteristics or the procurement indicator. As a rule, further company-specific characteristics are added to take account of the respective restrictions in logistics and production (e.g. storage volume, multiple use, contractual agreements with suppliers and customers).
2. set up rules for the individual classes
You define the rules by answering the following questions: Is an item kept in stock or only procured when needed? Are pull mechanisms used or are push methods more suitable? What delivery readiness or availability is specifically targeted? Should sales planning figures or statistical forecasts form the basis for planning? How should seasonality or fluctuating demand figures be dealt with?
3. talk to your internal and external suppliers to optimize the supply chain
First check which suppliers are worth changing the logistical parameters, e.g. delivery time, batch size, minimum quantity, etc. Work with them to define the future processes for how you want to work together. Determine which parameters influence this and how they should be set. Define exact, comprehensible rules for these variables as well.
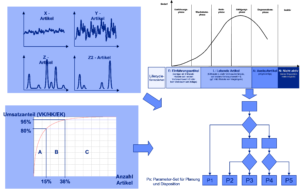
4. check the effects of the regulations
The decisive factor is what effects the regulations achieve. In order to avoid having to adjust these with a lengthy and costly “trial and error”, the simulation of the procurement processes with changed parameters is a good option. It is therefore first necessary to simulate how the relevant logistics key figures change. Will the targeted delivery readiness be achieved? What does it cost to increase delivery readiness? Is there potential for reducing inventories and thus liquidity reserves? What (additional) costs do the changes mean for production, logistics and suppliers?
5. convert the rules into setting values for the master data
Now get specific: define the exact characteristics of the master data. On the one hand, this means specifying precise settings such as the scheduling method, batch size rule or planning strategy. Secondly, you will implement the rules you have developed in algorithms, e.g. for calculating the minimum lot size, reorder points or cover periods.
6. realize the set of rules to support the dispatchers as a sustainable solution
As already described at the beginning, the volume of data to be handled is often a problem, which is why the master data is hardly or only rudimentarily maintained. With the defined set of rules, it is now possible to map and automate data maintenance using software. The programming effort is comparatively low – but the benefits are enormous. The task of keeping master data up to date and checking it regularly is now performed by the machine. The planners and schedulers are now more responsible for checking the quality of results and maintaining the rules and regulations. This means that the effort involved in data maintenance is drastically reduced while data quality and planning and scheduling results are improved.
7. conduct carefully prepared training courses and coach your employees after the go-live
Even if this point is almost at the end, it is the decisive factor in implementation. Only a trained and convinced dispatcher will be able to let go of old procedures and use the new set of rules. Appropriate training measures must therefore be prepared and implemented in order to explain the rules and make them transparent. It may be necessary to provide additional training on scheduling principles that have not yet been applied but are now being used. It is sometimes astonishing what gaps in knowledge can still be found even among long-serving employees. After the training phase and the operational changeover to the new regulations, it must be ensured that the planners and dispatchers have contact persons who can answer questions or solve problems at short notice and, if necessary, help to rectify errors. Ideally, the colleagues who were involved in the development of the rules and regulations provide coaching.
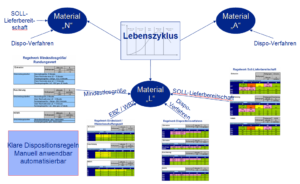
8. trust your employees, but don’t do without controlling
In order to achieve a sustainable solution, it is essential to regularly monitor and check the results of the project. On the one hand, this serves to check the effectiveness of the new regulations. If necessary, make fine adjustments to the set of rules. On the other hand, of course, this also serves to recognize deviations from the rules. Because there are a thousand reasons why an item cannot be planned according to the standard right now. These items must be tracked down and agreed with the dispatcher. Either the dispatcher is right and there may be a gap in the regulations that needs to be closed quickly. Or you can clear up any ambiguities by explaining how the regulations work again. Constant dripping wears away the stone here too.
Conclusion:
The development and introduction of a set of rules as described above has the following advantages:
They take some of the responsibility away from the dispatcher, which is often perceived as a burden. He can refer to the rules when asked by his colleagues if, for example, a stockout situation should arise. Because this is to be expected: 95% readiness to deliver also means not wanting to deliver 5% on time.
The regulations lead to a standardization of planning and scheduling processes. This has the advantage that vacation replacements or a different distribution among the participants are not a problem. Furthermore, training courses can be geared more specifically to the task. Ultimately, new planners and dispatchers can be trained more quickly.
The effort required for parameter maintenance is reduced to a minimum, so that those involved can concentrate on problem situations or carry out other tasks, such as price negotiations in purchasing, with more care.
Dr.-Ing. Bernd Reineke is managing partner of Abels & Kemmner Gesellschaft für Unternehmensberatung mbH.