Increase material efficiency and save an average of 9.6% on material costs
By Dr. Götz-Andreas Kemmner and Armin Klüttgen
In inventory optimization projects, questions of material efficiency often have to be left out of the equation, as they have a much wider impact than the project envisages. Nevertheless, it is important to also focus on material efficiency, as this enables us to do the right thing even better.
Although the potential for material efficiency measures varies greatly depending on the sector, the potential for annual material savings across all sectors averages 9.6%. Depending on the industry, the annual material savings potential can even be up to 20% of the gross production value, as a study from 20051 determined! The sectors with the greatest potential are the chemical industry (20.1%), the construction industry (13.3%), the manufacture of plastic goods (11.9%) and electricity generation equipment (8.6%). However, the manufacture of metal products, the processing of wood, medical technology, measurement and control technology and optics also show potential of between 6.4% and 6.9%. The study is based on 284 potential analyses in SMEs. On average, the potential savings amounted to 220,000 euros per year, 3,300 euros per employee or 2.5% of annual turnover. In the majority of cases, the amortization period for investments to recover this potential was less than 6 months. Consequential effects of the efficiency measures, such as economies of scale in sales due to possible price reductions, have not yet been factored in here.
Although these studies should be well known, it is surprising that around half of all German companies in the manufacturing industry have not yet implemented any measures to improve material efficiency, as a survey from 20082 shows. This is all the more surprising given that material costs represent the largest cost block in the manufacturing industry, accounting for around 46% of total costs. The reasons for this are complex: a lack of personnel capacity and the investment requirements associated with the project are at the top of the list of obstacles.
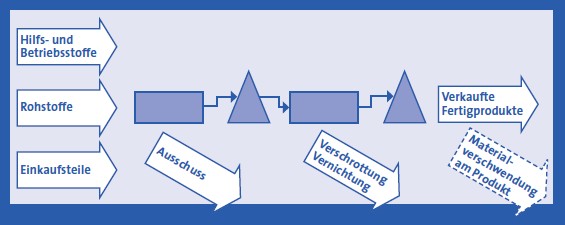
However, personnel bottlenecks can be resolved by using external consultants. However, a project to increase material efficiency is also made even more attractive by the fact that there is currently a funding program from the Federal Ministry of Economics that is open to companies with up to 1000 employees until the end of 2010. Depending on the total volume of funding, such projects are supported with up to 67% non-repayable grants. On average, such projects would pay for themselves in significantly less than six months and then generate an average of EUR 55,000 in additional revenue each quarter. It is also time (not only for SMEs) to take a closer look at this previously neglected potential, as material prices will rise again in the long term. It is also to be expected that climate protection regulations will cause material costs to rise further.
Material efficiency from a macroeconomic perspective
The overall economic potential lying dormant in material efficiency is enormous, as the absolute figures show:
- In 2007, the total costs of the manufacturing industry amounted to 1,723 billion euros.
- 792 billion euros (46%) was accounted for by material consumption.
- In contrast, only EUR 310 billion (18%) was spent on personnel costs.
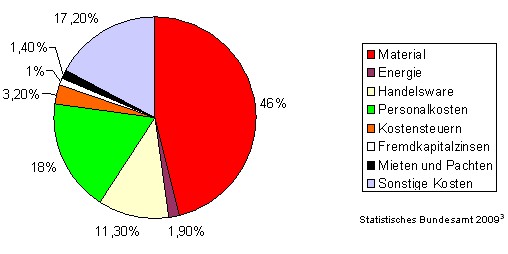
Missing out on innovation potential?
Over the last 50 years, labor productivity has increased by a factor of 3.5, while material productivity has lagged significantly behind at a factor of 2, which to a certain extent also highlights missed innovation potential in products.
This is also evident when comparing the two cost blocks in our companies, personnel and materials. While great efforts have been made in recent years to reduce personnel costs, material costs have risen significantly in the same period as a proportion of the total cost rate. Material costs increased by around 8% between 1995 and 2007, while personnel costs fell by 7%.
It is therefore important to raise awareness of the great opportunity that material efficiency projects offer and to question and remove obstacles to the implementation of measures.
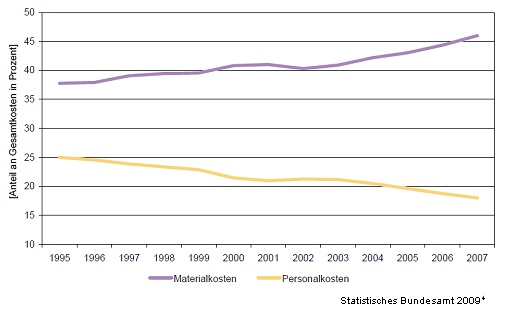
How can material efficiency be increased?
There are many ways to increase material efficiency in the production of goods. Resources can be saved by designing products accordingly and optimizing industrial processes. In addition, raw materials that are classified as critical or problematic can be replaced by less problematic ones. All measures that reduce the use of materials (including auxiliary and operating materials) in the production process are therefore suitable for increasing material efficiency. This can be achieved, for example, by improving the design of products, reducing waste (quality scrap) or optimizing offcuts (flat scrap). The main starting points for increasing material efficiency can be broken down into the following areas:
- Product design and dimensioning
- Material selection (selection or substitution of materials used as well as cleaning agents and auxiliary materials)
- Determination of geometries
- Variant management (reduction of internal complexity while maintaining external complexity)
- …
- Production process
- Processing techniques in machining
- Process parameters
- Waste optimization
- Reuse of scrap / use of waste
- Time and type of cleaning of intermediate products
- Work instructions Time and method of error identification in the processes
- …
- Production environment
- Disposition and warehousing
- Packaging and transportation
- Cleaning agents and water consumption and treatment
- …
- Planning
- entire process in the supply chain
- Sales, demand and inventory planning
- Production planning
- Procurement planning
- …
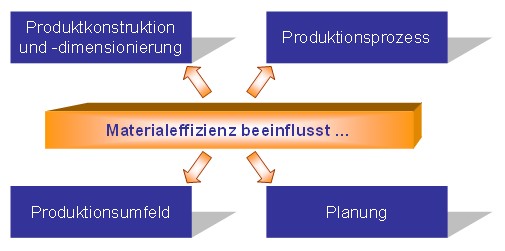
The potential for improving material efficiency is particularly high when developing new products. As the automotive industry has long practiced, it is of course necessary to make fundamental material savings (e.g. lightweight construction) without restricting the requirements of the overall product. In addition, products should be easy to repair and ultimately easy to recycle.
Not to be neglected in this early phase of the product life cycle is the reduction of internal complexity while maintaining external complexity. Customers should be able to choose from a wide variety of products. However, the aim must be to minimize diversity internally through a high proportion of multiple-use parts, as a high number of variants affects the number and quantity of raw materials, production and assembly parts and assemblies required and also has an impact on the efficiency of the production machines used. Reducing the number of variants within the company also improves the ability to plan products and minimizes the risk of rejects and scrapping due to missing requirements or planning errors. At the same time, the effort required for master data creation, scheduling, transportation and handling is also reduced.
While these aspects are reflected in the design-to-cost method or in later standardization projects, for example, the zero-loss management method is particularly effective in the life cycle phases of growth, maturity and saturation. In addition to considering the entire supply chain, particular attention is paid to production processes and the design of material flows. In zero-loss management, all cost elements that are not used by the customer in the form of end products and are therefore not paid for by the customer as a product are referred to as loss. The aim of optimization is to avoid as many losses as possible. The focus of a material efficiency project therefore includes losses such as raw material waste or rejections, losses in intermediate products, finished products and packaging materials as well as consumables such as water. Practical examples of this are
- In the pharmaceutical industry, increasing the target product yield by optimizing the process parameters, in particular the deviation from the stoichiometric input ratio of the starting materials, in order to achieve a higher overall yield. A cost reduction of up to 12% is certainly possible.
- Savings of 3.5% in total production costs by avoiding product and packaging losses at a frozen food manufacturer
- Adaptation of measurement and control technology so that production parameters can be set more closely and quality losses reduced -> Reduction in material loss costs by 14%
- Reduction of annual scrapping at a medium-sized trading company by €450,000 per year
In addition to the often existing problem of waste optimization, the increased recycling of materials also offers great potential for increasing material efficiency. In the lubricants sector, for example, a large proportion of the waste oil produced can be recycled more and more effectively thanks to advanced recycling methods.
Conception of material efficiency projects
Wherever you see the main starting points: It is important that all the areas mentioned above are embedded in a comprehensive and holistic design approach in material efficiency projects. Individual actions are of little use here because they are not sustainable.
As part of a potential analysis, the first step is therefore to draw up a complete material balance sheet for the company and its processes. In a productive system, the material balance compares the quantities of material input with the quantities of material output. The entire material flow is identified by type and quantity, and losses are disclosed. The central question is: Where are material efficiencies being eaten up or potential for increasing material efficiency not being utilized in the design of products, production processes, the production environment and the end-to-end planning of the supply chain? The identified material efficiency deficits are then not only attacked in the next step with the design of an overall concept, but are to be resolved in the long term.
This requires the effective linking of all measures, from the procurement of materials to the distribution of the manufactured products. End-to-end planning of the supply chain in terms of demand and inventory and the definition of optimal stockpiling strategies form the essential basis for increasing competitiveness with a low level of scrapping and thus in a resource-saving and cost-effective manner. Errors in these planning domains inevitably lead to unnecessary consumption of raw materials, incorrect use of materials (and energy, which is not counted as material efficiency) in production and the manufacture of unnecessary intermediate products and end products. This, in turn, often leads to scrapping or discounted sales campaigns, which place an undue burden on the material balance and thus on material efficiency. The strategic lever of increasing material efficiency can therefore only be implemented efficiently if the scheduling processes are optimized at the same time.
1 Study by Arthur D. Little GmbH, the Wuppertal Institute for Climate, Environment and Energy and the Fraunhofer Institute for Systems and Innovation Research.
2 BDI survey from fall 2008
3 Federal Statistical Office (2009), Produzierendes Gewerbe – Kostenstruktur der Unternehmen des Verarbeitenden Gewerbes sowie des Bergbaus und der Gewinnung von Erden und Steinen, Fachserie 4 – Reihe 4.3, Wiesbaden.
4 Federal Statistical Office (2009), Sector/Statistics Code 42251