While the industrial sector is searching hard for ways to save energy, far too little attention is still being paid to a much larger cost factor: material efficiency. Huge sums are still being sunk here.
Energy efficiency – within two to three years, what was once a marketing buzzword has become a topic that almost all serious companies, from SMEs to large corporations, are devoting themselves to. Rising energy costs were one reason to take a close look at the “energy” cost component and to make the right adjustments to improve energy efficiency. Clever control technology, completely reorganized production processes and optimized machines and systems have led to significant cost reductions in many companies. But one thing must be said: Energy accounts for a total of 1.90 percent of costs in the manufacturing industry. These figures, which were collected in Germany in 2008, can also be used for Austria.
It is therefore all the more surprising that a much larger chunk of costs tends to be neglected. In an analysis, Götz-Andreas Kemmner and Armin Klüttgen from the German consulting firm Abels & Kemmner found that a good half of all German companies in the manufacturing industry have not yet implemented or planned any measures to improve material efficiency. “This is all the more surprising as material costs in the manufacturing industry represent the largest cost block of all, accounting for around 46 percent of total costs,” Kemmner and Klüttgen criticize in a study on the subject.
Austria is in default.
“Material efficiency describes the relationship between the quantities of materials in manufactured products and the quantities used to make the products,” explains Götz-Andreas Kemmner. “At a time when raw materials are becoming scarcer and more expensive, the efficiency of material utilization is an important lever for strengthening competitiveness; a lever whose importance will continue to grow.”
While Germany has responded with a nationwide “Material Efficiency Impulse Program”, Austria has done next to nothing in this regard. According to a study by the German Material Efficiency Agency (demea), companies could save an average of 20 percent of their material costs through more efficient production processes. The impulse programs “VerMat” (for advising SMEs on improving material efficiency) and NeMat (a program for forming networks to improve material efficiency) are intended to ensure that the idea of saving is implemented in as many companies as possible.
Personnel instead of material?
“Regardless of the fall in raw material costs due to the current economic situation, all experts are assuming that demand will continue to grow in the medium term and that supply on the global markets will only be able to keep pace to a limited extent,” says Armin Klüttgen. “The fact that, in addition to competitiveness, sustainability also benefits immensely, especially with regard to climate protection requirements, should only be mentioned in passing here.”
What do 20 percent savings mean? In 2007, the total costs of the manufacturing industry in Germany amounted to 1,723 billion euros. 792 billion of this was attributable to material consumption.
“In contrast, only 310 billion euros (18%) was spent on personnel costs,” says Klüttgen. A comparison of the two cost blocks clearly shows which issues were in the foreground in the years before the crisis, adds Kemmner: “While great efforts were made to reduce personnel costs, material costs rose significantly as a proportion of the total cost rate during the same period. Material costs increased by around 8% between 1995 and 2007, while personnel costs fell by 7% at the same time.”
Labor productivity and material productivity have also not grown at the same rate over the last 50 years, by a factor of 3.5 and 2 respectively.
Why nothing happens.
This raises the question, not only for consultants, as to why so many companies do not implement measures to improve material efficiency. “The most important obstacles cited are a lack of personnel capacity, supposedly long amortization times and high investments,” explains Armin Klüttgen. “In addition, there are sometimes conflicts of objectives within the company that hinder the implementation of corresponding projects, as well as a lack of awareness among decision-makers of the hidden potential here.”
In many cases, it would be possible to get a grip on the issues mentioned – if information deficits were eliminated and programs available today to promote material efficiency projects were used. Götz-Andreas Kemmner and Armin Klüttgen are convinced that although external consultants cannot fully compensate for aspects relating to investments or staff shortages, they can make them much more attractive.
Increasing material efficiency – but how?
There are a number of starting points for more economical procedures. “By designing products accordingly and optimizing industrial processes, resources can be saved and raw materials that are classified as critical or problematic can be replaced with less problematic ones,” says Kemmner. The main areas to be considered are product design and dimensioning, the production process itself, the production environment and planning.
Lightweight construction, but above all the reduction of internal complexity while maintaining external complexity, should not be neglected. Kemmner: “However, the aim must be to keep internal diversity as low as possible through a high proportion of multiple-use parts, as a high number of variants affects the number and quantity of raw materials, production and assembly parts and assemblies required.”
What’s the point?
A study in 2005 identified the potential that can be realized in various industries through increased material efficiency. The knock-on effects of the efficiency measures were not even taken into account. Accordingly, the chemical industry (20.1%), the construction industry (13.3%), the manufacture of plastic goods (11.9%) and electricity generation equipment (8.6%) are areas with the greatest potential. However, the manufacture of metal products, the processing of wood as well as medical, measurement and control technology and optics also show potential of between 6.4% and 6.9%. On average, 284 potential analyses at SMEs revealed 220,000 euros or 3,300 euros per employee. This corresponds to a potential of 2.5% in terms of annual sales. The amortization period for investments was less than 6 months in the majority of cases.
demea also underlines the statements of the experts from Abels & Kemmner and addresses a multiple misconception: Getting started with material efficiency is not time-consuming. Secondly, companies generally do not have to make huge investments. This is shown by the evaluation of the potential analyses carried out to date: almost half of the savings measures proposed by the consultants can be realized without investment.
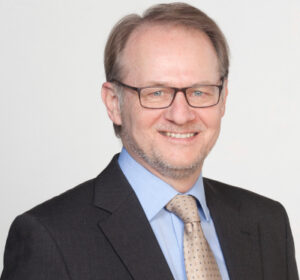
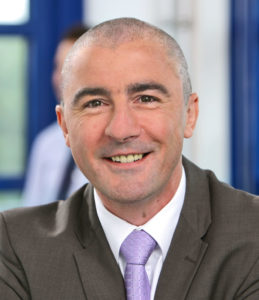