Medion introduced a new demand forecasting tool to reduce spare parts inventories by a double-digit percentage. The investment should pay for itself in the current year.
Short product life cycles, high-priced parts and unpredictable demand characterize the supply of spare parts in the consumer electronics industry. This area has a particularly high priority at Medion AG. The company manufactures PCs and multimedia devices, entertainment and household appliances as well as communication technology according to the “build-to-order” principle. The manufacturers in China, Taiwan, the Philippines or Europe only produce the required quantities of appliances – from electric toothbrushes to televisions – when the retail partners place orders for their sales campaigns. The advantage of this strategy is that Medion does not incur any storage costs. The company manages import, distribution and aftersales at its headquarters in Essen. In contrast, the retailer has completely outsourced the actual logistics activities to several external service providers and set up a single-stage logistics system.
“We design and schedule our products on a customer-specific basis. This allows us to manage a wide range of spare parts,” explains Mathias Schwenck, who has been with Medion for seven and a half years and is responsible for international aftersales service. The individual products also have different warranty periods and failure rates depending on the partner. As part of the overall service for its retail customers, Medion offers a hotline for end consumers in its own call center. In warranty cases, the trading company carries out repairs, sometimes on site at the customer’s premises within Germany. This requires a high availability of spare parts.
However, these components cannot be procured over the entire warranty period. This is because manufacturers cancel them well before the end product’s warranty expires. For example, motherboards for PCs are often only available for a few months, while plastic housings for notebooks are often only available during production itself. The appropriate hinge, should it be defective during the warranty period, must therefore be ordered in good time.
However, it is a very fine line to ensure the stocking of spare parts for the remainder of the warranty period. If stocks are too low, spare parts run out and customer appliances can no longer be repaired. Medion must then replace the defective devices with an equivalent product. However, if too much stock is held, the company is left with high stocks at the end of the warranty period, which also drives up costs.
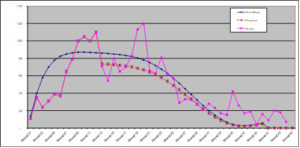
In the prototype of the analysis software tool, users can assign a failure pattern to each spare part. The dispatcher can change the demand forecast by reweighting the consumption periods.
Five failure patterns
All spare parts are stored centrally in Mülheim an der Ruhr. Essen-based van Eupen Logistik GmbH & Co KG is responsible for warehousing and transportation between the warehouse and workshop as well as refurbishment (general overhaul). From here, consolidated repair workshops throughout Europe are supplied with material. “At the end of a warranty period, we decide whether we need more materials in Mülheim and, if so, in what quantity or order of magnitude,” explains Schwenck. The requirements are calculated on the basis of previous consumption or warranty losses. In the past, the 15 material planners at Medion used several individual solutions for this purpose.
In order to systematize these processes, document them and make them verifiable, Medion commissioned Abels & Kemmner GmbH from “Herzogenrath near Aachen at the beginning of 2010. The consultants were tasked with optimizing the demand forecasts in the rink purchase with an improved calculation method. “The aim was to calculate the failure rates more effectively and accurately so as not to tie up capital unnecessarily or drive up the warranty payments,” recalls Schwenck. Due to the very short consumption periods of less than six to twelve months and the fluctuating requirements, the experts first analyzed the consumption series of projects from the past. Five different types of failure patterns were identified.
In the second step, they developed a prototype of the graphical analysis software tool “DISKOVER SCO”. By assessing the first phase of a consumption period, users can assign the appropriate failure pattern to each spare part and determine the requirement for a warranty period (see diagram). The dispatcher can change this forecast by reweighting the consumption periods with a mouse click.
After a test phase in the last quarter of 2010, the new tool went into full operation at the beginning of this year. In total, less than 100,000 euros were invested in the project, which, according to Schwenck, will pay for itself this year. Medion has already improved residual demand coverage in the double-digit percentage range with the new forecasting method. This results in higher delivery readiness and material availability with lower inventories. “What we charge now for expiring projects will only have an impact in two years’ time. However, I can already see a trend towards avoiding unnecessary or late acquisitions,” summarizes Schwenck. The long-term goal is to reduce inventories in the double-digit range.
About Medion AG:
Medion AG, based in Essen, Germany, currently employs 1,026 people.
In 2010, the consumer electronics provider generated sales of more than 1.6 billion euros. The company’s customers are retail and wholesale companies throughout Europe, including Scandinavia and the UK, but also in Australia and the USA.
Customers include Aldi, Mediamarkt, Metro, Real, Tchibo, Sainsbury’s (UK), Dixons (UK) and Carrefours (F).