Highly efficient paperwork management
Heijunka boards – another one of those Asian things, some will think. But what’s the point? Montblanc-Simplo GmbH has further developed the Heijunka principle so that it not only serves to level the final assembly of the writing instruments, but also controls the multi-stage and multi-day assembly processes.
At its Hamburg site, Montblanc-Simplo GmbH handcrafts high-quality writing instruments from several different, unlimited product lines such as Meisterstück, Boheme, Starwalker and Etoile in a wide variety of model designs. In addition, special limited-edition devices are produced in the manufactory in quantities ranging from a single unique piece to several thousand.
For the past eight years, the deep-stage production of individual parts and components for the unlimited appliance models has been controlled using a hybrid Kanban system. In this Kanban organization, control takes place on site using Kanban cards and Kanban boards. The production progress is tracked via scanning processes in the SAP system. This Kanban control chain, which in some cases extends over several control loop stages, ends before final assembly in the so-called EMO warehouse, the supermarket for final assembly. This production organization of Montblanc’s individual part and component production has proven itself over the past eight years and has led to significantly lower inventories and work in progress as well as higher delivery reliability of the supermarket for final assembly.
ORDERS FOR FINAL ASSEMBLY
Until the end of 2009, final assembly itself was controlled by traditional SAP production orders, which were triggered by the SAP system based on the monthly calculated target and reorder levels of the finished appliances. In this way, a continuous production process was realized right through to the market. Final assembly was controlled for writing instruments with high sales and more regular market demand by means of target inventory control, which is the result of a differentiated monthly rolling sales planning and production program planning process. Reorder points are automatically calculated each month for writing instruments with lower sales and irregular demand. The result of the rolling monthly sales planning process is not only leveled annual seasonalities, target and reorder levels, but also re-dimensioned Kanban control loops for the production of components and individual parts.
FLUCTUATIONS IN CAPACITY UTILIZATION
However, fluctuations in demand and the resulting varying levels of replenishment requirements in the finished goods warehouse repeatedly led to noticeable fluctuations in capacity utilization in final assembly. In addition, the SAP system triggered production orders with relatively large batch sizes. Both effects together resulted in varying material withdrawal quantities per time unit from the final assembly supermarket, which in turn caused fluctuations in demand in the individual Kanban control loops, both in production and in procurement. In the first years of Kanban control, these could still be absorbed by the Kanban control loops, as capacity reserves were available in almost all production areas. These reserves made it possible to increase production throughput at short notice and replenish the final assembly supermarket in good time. The same applied to suppliers, who responded to fluctuations in demand with great flexibility.
LIMITED ELASTICITY
However, the changing product portfolio of recent years has pushed the utilization of in-house production and suppliers ever closer to capacity limits, thus restricting the elasticity of Kanban control loops. For these reasons, fluctuations in demand from final assembly increasingly led to supply bottlenecks. Due to fluctuating replenishment orders from the finished goods warehouse on the one hand and poorer supply reliability from the Kanban supermarket on the other, the final assembly of writing instruments was facing a production bottleneck.
A Heijunka control system was introduced in final assembly at the beginning of 2010 in order to smooth and stabilize capacity utilization in final assembly and thus reduce fluctuations in demand in the production areas and Kanban control loops. The term Heijunka refers to the process of smoothing out the necessary capacity requirements in conjunction with a higher product mix of the parts to be manufactured in the individual assembly lines in order to bring as much calm as possible to production within given capacity limits without losing the focus on demand.
The specific objectives of the Heijunka control system at Montblanc were:
– increase the product mix in the individual assembly lines,
– reduce the fluctuations in capacity requirements in the individual assembly lines,
– to create transparency for the utilization and capacity requirement situation in the individual assembly lines,
– to reduce the number of missing parts when removing components from the final assembly supermarket,
– to stabilize the removal of parts and components from the final assembly supermarket and thus stabilize the Kanban control loops across the various production stages,
– to reduce the circulating stocks in final assembly,
– to create the conditions for reducing the circulating stocks in the Kanban control loops and
– to develop an instrument for operational self-control of the assembly groups.
SIMPLE PRINCIPLE
The special thing about Heijunka processes, such as final assembly at Montblanc, is that not just a single production step or a short assembly sequence consisting of several small steps is controlled. Instead, a multi-stage assembly process is controlled, in which the production of a final device can take up to a week due to drying times after gluing steps. In order to be able to map the assembly process efficiently in an easy-to-use Heijunka process, a number of conceptual, technical and organizational challenges had to be overcome.
THE FOUR PHASES OF THE PROCESS
The Heijunka process at Montblanc is based on the rolling planning process described above and consists of four phases: In the first phase, the replenishment requirements for the finished goods warehouse are broken down into smaller assembly lots in the SAP system and printed out as Heijunka orders for the individual assembly groups. In the second phase, a Heijunka board is provided with the printed orders by the production logistician or the group spokesperson of an assembly group, the required personnel capacities in the various assembly groups are compared and the so-called assembly order box is filled. In the third Heijunka phase, the multi-stage assembly of the devices takes place according to the specifications in the assembly order box. Once assembly has been completed, the Heijunka cycle is concluded in the fourth phase by scanning the Heijunka production order card, the so-called “final scan”.
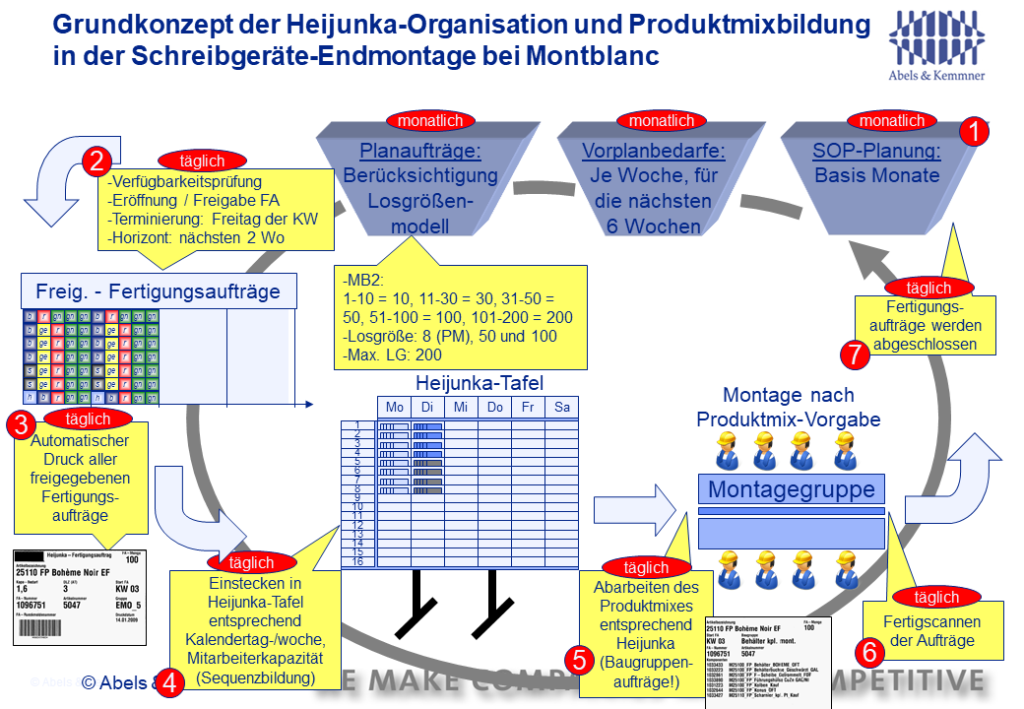
THE RESULT
The Heijunka organization in final assembly has proven itself at Montblanc for over two years now and has developed into a key design element of Montblanc’s lean strategy. Originally developed with a pilot group, the organizational principle has since been successfully extended to all assembly teams. The result: the assembly teams now work in a more relaxed and yet more efficient manner; there are no longer any frictional losses or hectic situations caused by missing components and/or order backlogs Even if parts are missing for a short time despite availability checks, this does not disrupt the assembly teams’ workflow: they can intervene independently and bring forward other assembly orders as part of the weekly planning – even an order from the following week if necessary. The planning of personnel requirements has also been significantly simplified and safety stocks in the Kanban control loops in production have been reduced thanks to the more consistent removal of components. In final assembly, too, work in progress has decreased as orders can now flow through assembly more quickly.
On the purchasing side, the more even demand has meant that Montblanc can work with significantly lower safety stocks. Suppliers receive more reliable demand forecasts, which allow them to plan their own production more evenly and further reduce their own safety stocks. Discussions with suppliers showed that not only could processes be simplified, but that suppliers were also able to produce more cost-effectively, so that the increase in purchase prices was kept to a minimum despite rising raw material costs. The result shows that demand orientation does not necessarily mean hectic and inefficiency, because with Heijunka it is possible to produce very efficiently in line with the market even with given capacity limits.
The authors
Peter Hartwig, Carsten W. Hense, Andreas Gillessen, Dr. Andreas Kemmner