Originally from the automotive industry, cumulative quantities are mainly used in large-scale production as a control method between suppliers and customers: they represent the cumulative quantity of a production part at a specific point in time at a specific control point. Changes to deadlines and quantities can be clearly displayed using cumulative quantities and the resulting requirements can be transferred to internal and external suppliers.
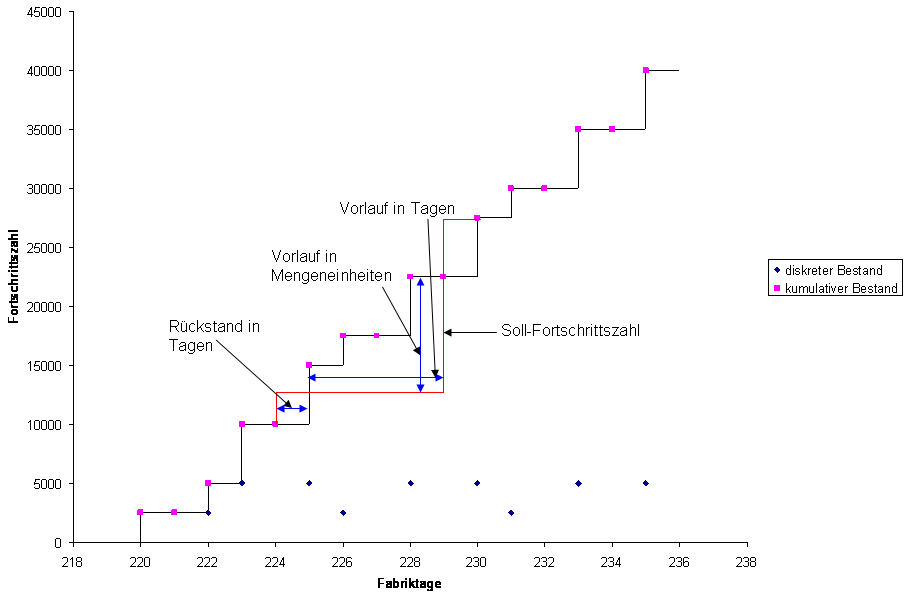
For this purpose, the quantities to be delivered of each individual part are determined for the same fixed periods (e.g. working week) in order to obtain the target cumulative quantities. The actual stock or actual quantity, on the other hand, is recorded on a daily basis. This allows you to quickly identify emerging lead times or backlogs and react accordingly. As part of[intlink id=”1620″ type=”post”] just-in-time planning (see Potentials 3/2007)[/intlink], cumulative quantities are also suitable as an alternative to Kanban for fine-tuning requirements as they are an integral part of delivery call-offs. As cumulative quantities are based on the FIFO principle (First In First Out), the oldest stocks are automatically taken into account first.
Our tip:
Cumulative quantities can offer advantages over Kanban for production control if there are output disruptions in one of several production areas working in parallel. While the Kanban mechanism automatically slows down the areas working in parallel and thus keeps circulating and warehouse stocks low, the cumulative quantity mechanism ensures that the areas capable of working continue to follow the market specifications, even if the components produced have to wait for the components of the disrupted area for further use. This temporarily increases circulation and stock levels, but avoids expensive overtime in all production areas once the fault has been rectified.