Clean&Prim KG* optimizes its material efficiency
by Armin Klüttgen
More careful use of resources, with the aim of reducing material losses and leveraging tangible economic potential, are three good reasons why more and more companies have been addressing the topic of “material efficiency” in the last two years. These are also the reasons why Clean&Prim KG*, together with Abels & Kemmner GmbH, has carried out a material efficiency project for part of its product range to investigate which cost reduction potentials can be realized by further increasing material efficiency and how employees’ awareness of the careful and efficient use of the materials used can be further increased. The results of the project confirm the foresight of the management. The task now is to realize the identified potential by implementing the defined measures.
In its final report to the Federal Ministry of Economics and Technology (BMWi) in December 2011, the Fraunhofer Institute for Systems and Innovation Research ISI showed how great the potential in the manufacturing industry often is for increasing material efficiency. The report is based on figures from a 2009 survey on the modernization of production, which the ISI has been conducting regularly since 1993.
The survey revealed that, on average, seven percent of material consumption in production can be saved across all industries if the technical possibilities available today are optimally utilized. This has an impressive impact on the return on sales, as a comparison with the required increase in sales shows. The following table shows the increase in turnover that would be necessary to achieve the same earnings effect in various sectors as would be achieved by improving material efficiency:
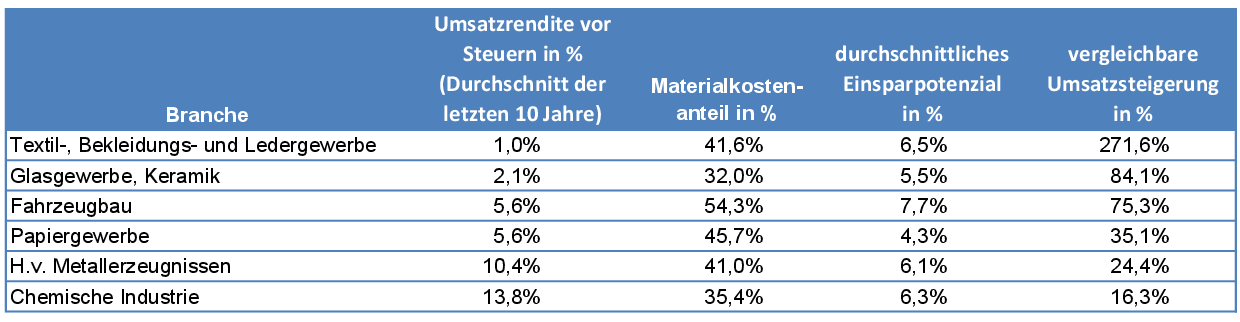
On the one hand, the examples presented impressively demonstrate the great leverage effect of measures to increase material efficiency. Secondly, they give an impression of how high the share of material costs in total costs is in the manufacturing industry: around 43% across all sectors. Given that resource prices are continuing to rise, many materials are becoming scarce on the procurement market and a large number of political measures are aimed at conserving resources, it is essential for many companies to address this issue seriously and sustainably.
Clean&Prim KG sets an example
The Clean&Prim Group has used its employees’ existing awareness of the importance of material efficiency to carry out an analysis of the existing potential for a selected part of the product range with the support of Abels & Kemmner and has willingly made the necessary personnel capacity available. This may not sound like a particularly noteworthy achievement at first, but the unavailability of personnel capacity and the organizational effort required are frequent reasons for the failure or omission of such projects.
Following Abels & Kemmner’s tried-and-tested process model for material efficiency analysis, fields of action and detailed measures were developed to realize the identified potential. These results were based on:
- a comprehensive root cause analysis (constraint analysis),
- a material flow analysis for the complete mapping of all relevant material flows,
- an evaluation of the different types and quantities of scrap and
- a quantification of the potential for improvement in relation to the different types of rejects.
Material losses in production and out of the warehouse
The range examined included products such as household cleaners and cosmetics as well as hair and body care products, which are supplied to many German retail chains, among others. High-quality raw materials are used in the manufacture of the products, which account for a high proportion of the company’s total costs.
The total waste is made up of valuable raw materials such as chemicals, plastics (plastic bottles and caps) and cardboard (paper, cardboard).
The analysis revealed various causes of material efficiency losses: in particular, losses due to cleaning processes for units and pipelines account for a significant proportion of these. Another part of the scrapping is due to planning aspects from the existing stock.
The production process
Clean&Prim uses raw materials such as chemicals, plastics, packaging materials in the form of primary packaging (e.g. cans and bottles) and secondary packaging such as cardboard boxes for the finished products produced in the product range examined. Various other raw materials and supplies are also used.
The raw materials (chemicals) are mixed and then transported to a buffer via piping systems. From there, they are transferred to different filling areas, depending on the product or application. Again, this is done via appropriate piping systems. During filling, the material is filled into its primary packaging (plastic bottles, tubes, etc.). After primary packaging and subsequent palletizing and repackaging, the finished products are posted to the finished goods warehouse, from where they are delivered.
There are various sources of material waste during this manufacturing process. There are practically no quality-related rejects in the detailed and meticulously monitored process. Damage to the packaging, for example, is only minor in this case. By far the largest share of material losses is accounted for by the so-called planned rejects. These arise during cleaning processes. Cleaning losses occur during product changes at the mixing units, in the affected piping systems and in the filling machines.
The second largest item of material losses is caused by old goods (excess stock to be scrapped in the warehouse), which arises due to effects in the planning and then has to be scrapped for various reasons. There are many reasons why planning creates old goods. Dalli is facing a highly complex planning task here, which can lead to imprecise planning results due to a number of special features. Examples of this are
- Difficult to plan actions in an environment with a large number of variants
- Partly strong seasonal fluctuations
- Partly spot business for packaging materials
- Run-out control with the requirement to synchronize the precise run-out (run all stocks to zero on time) for finished products (content), primary material and packaging
- Product changes that are made due to customer requests, e.g. in the form of recipe changes or packaging changes.
Material losses can be significantly reduced
The potential identified by Abels & Kemmner is considerable in some cases: both planned rejects in production (cleaning losses and overpacking) and rejects from the warehouse (excess stock from planning that needs to be scrapped) have significant reduction potential in purely technical terms.
However, some of the measures that can be used to leverage this potential are characterized by strong company-specific dependencies and interactions and can therefore only be used to a limited extent. The high level of customer orientation in particular must not suffer as a result of the optimization processes. All possible measures identified can be assigned to four main directions in the sense of an action field map:
- Investigation of potential improvements in production,
- Expansion of end-to-end planning to avoid old goods,
- Optimization of individual business processes, e.g. product development process etc.,
- Designing even more efficient system support.
Below we present some examples of selected measures:
Make cleaning losses transparent when changing products
In absolute terms, cleaning losses in production account for the largest proportion of all material losses. Accordingly, reducing these losses leads to lower costs. The first step is to further increase transparency about where and how much cleaning waste occurs. Depending on which product mix is controlled via which line, there may be greater fluctuations here. Technical units involved in production such as mixers, buffers, filters, pumps, pipelines, homogenizers and filling machines have fluctuating loss rates depending on the product mix and production sequences. It is therefore necessary to refine the methods previously used to determine losses and the corresponding controlling.
Overall concept of integrated planning
The transfer of today’s already sophisticated planning processes into a comprehensive overall concept of fully integrated planning and scheduling clearly offers the greatest leverage in absolute terms for avoiding material efficiency losses. The cornerstone of this overall concept is the optimization of demand planning and scheduling and is flanked by even better communication with customers. This takes the supply chain concept of “planning from the customer’s customer to the supplier’s supplier” even more into account than is already the case at Clean&Prim KG.
When optimizing demand planning, the main focus is on the best possible integration of all available planning-relevant information for each individual item, e.g. through an integrated or summarized forecast. This requires sales information, customer information, the current order situation and statistical forecasts, which are combined on an item-specific basis to produce the best possible forecast, also with regard to seasonal business, promotions and other exceptions. Various classifications of the articles must also be used to support this, such as
- an ABC classification (economic importance),
- an XYZ classification (consumption regularity),
- an ELA classification (life cycle) or
- an STU classification (number of customers).
Depending on its classification, an article must be set exactly as required in requirements planning. This requires an appropriate set of rules which, thanks to its automation, enables the material-specific scheduling strategy and all necessary scheduling parameters to be defined on a rolling basis and with little effort, and which allows these to be regularly checked and reset for all items. However, it is important that the already very high level of flexibility towards the customer is maintained and further improved under all circumstances. The specialists at Abels & Kemmner have taken this into account and the automated set of rules ensures optimum scheduling for every finished product and every primary material at all times. Together with improved demand planning, it is therefore the key to avoiding used goods and thus material losses.
Business processes that support end-to-end planning
The product creation process or product control, the product change process and the product discontinuation process have a considerable influence on planning and scheduling. In all of these processes, it is important to work as closely as possible with the customer, who has a considerable influence on the planning processes in Clean&Prim KG’s business model. The business model is characterized by frequent product changes coupled with a large number of variants and customer requests for changes to the product and packaging. Knowledge of the “true demand signal” is very helpful here, i.e. in terms of the supply chain, real market demand information as early as possible. This underpins planning assumptions by adding real market and customer information at an early stage and increases planning reliability. This can significantly reduce planning material losses.
The risk of obsolete material being created is particularly high in the case of product changes, as some planning processes that have already been initiated are affected, such as the printing, delivery and storage of packaging material. The product change process must therefore be clearly defined:
- the type of possible change types (customer requirements, product improvement, …),
- the roles and responsibilities for each type of change,
- Clear business rules for each change type,
- a workflow for controlling and monitoring the execution of the change process,
- clear documentation and communication of the process and embedding it in the end-to-end planning.
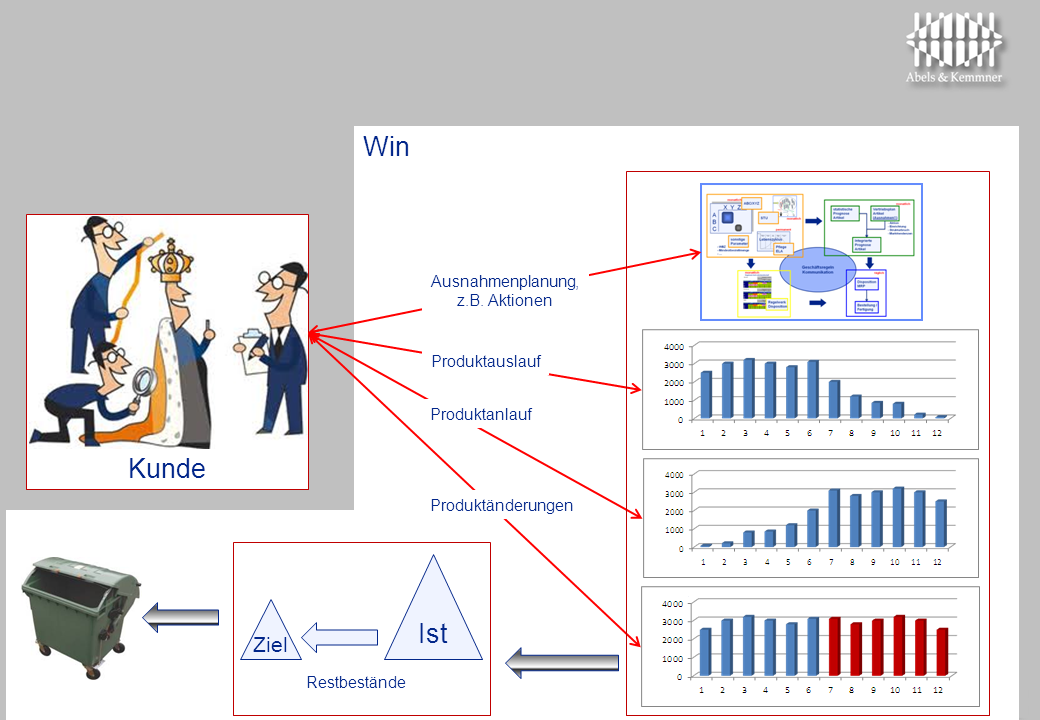
Product discontinuation also often leads to material losses, as a certain product must be reduced to zero stock by a fixed date while maintaining maximum delivery readiness. This alone is certainly a difficult planning task. To make matters worse, it is necessary to closely synchronize the discharge of the product and the primary packaging material, which proves to be very difficult, e.g. due to the specified minimum order quantities for the packaging materials.
In addition, an announced expiry date may be postponed by the customer. In this case, too, planning must act to maintain the required delivery readiness and stock up on both primary materials and finished products. This always leads to residual stocks.
Here, it is particularly helpful to further expand the already existing close partnership with customers and, on the other hand, to realize the closest possible integration of packaging material suppliers in particular as part of supplier integration – because this prevents the creation of old goods and thus further increases material efficiency.
Forcing system support
The project has shown that the possibilities of system support must also be better utilized to achieve greater material efficiency. In future, the existing systems will therefore continue to be highly integrated with a view to a consistent overall planning process and ensure maximum transparency. The manual effort involved in planning and scheduling will be significantly reduced. This creates the freedom to deal intensively with the real “problem cases”, particularly in scheduling.
Conclusion
Clean&Prim KG not only has a very material-intensive production process, but is also extremely conscious of the high-quality raw materials it uses. The efficient use of increasingly scarce raw materials is part of our corporate philosophy and also offers economic advantages. As part of the material efficiency project with Abels & Kemmner GmbH, Clean&Prim KG was able to improve its already good material efficiency and will continue to pursue this strategy based on the project results.